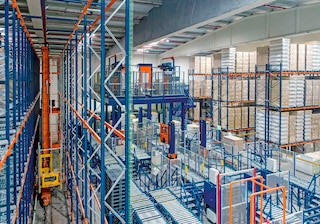
Warehouse robotics in the Logistics 4.0 era
A robotized warehouse is one that has automatic systems and specialized software to control and handle the goods. There is nothing new about machinery and robotics being used in logistics. However, digitalization and the advent of Industry 4.0 (and Logistics 4.0) have led to major progress in the field of robotics and the automatization of every inch of the supply chain.
Besides the revolutionary warehouse robot prototypes grabbing the spotlight lately, our article focuses on the main systems established in the sector because of their efficiency and proven results. But, first of all, let's look at some key concepts.
Industrial robots vs. cobots
Two important ideas co-exist in the field of industrial warehouse robotics:
- Industrial robots
Machines programmed to execute industrial processes in a specific way. To a large extent, they replace manual labor in heavy, repetitive tasks and operate automatically. Moreover, they are equipped with sensors that detect and collect information from the surroundings in real time.
Industrial robots have a wide variety of applications, meaning they can take many different forms, as we will see later on. In this class of warehouse, for example, you’d find automatic conveyors and stacker cranes.
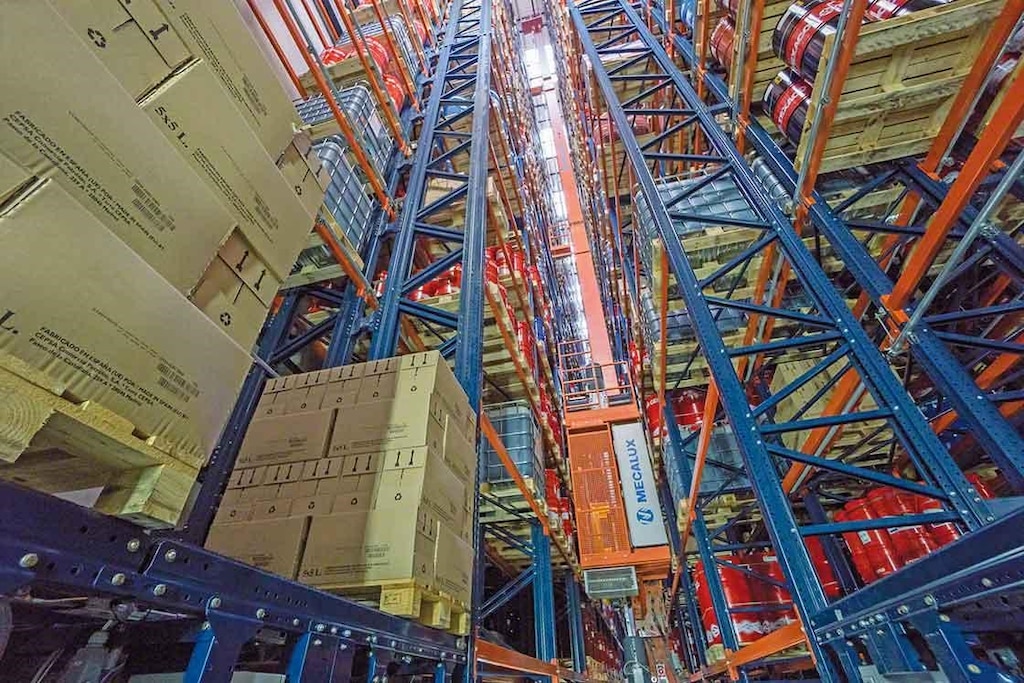
- Collaborative robots or cobots:
Collaborative robots or what are known as “cobots” tend to be more compact, with a more manageable structure. The difference with standard industrial bots is that they are designed to support humans to carry out diverse tasks in their working environment (hence the name). Versatility is one of their major advantages, since they can be programmed to operate autonomously or guided by the worker. You’ll definitely come across mechanical arms for handling loads or packaging machines in storage contexts.
What operations should I robotize in my warehouse?
Who knows if the warehouses of the future may eventually be completely people-free. But, in reality, even the most modern centers these days still require a certain degree of human intervention. Despite advances in automation, the warehouse still needs operators to be present to perform the most complex and variable tasks…
Cause not everything can be automated. Rather than looking for a perfect solution, the things we envision when we propose a warehouse automation project are any conditioning factors that might restrict potential. Of course, we find the most efficient, productivity-oriented systems and scenarios.
In any case, the road towards warehouse robotization is clear and comprises the following premises:
- Unit loads must be standardized, be it a pallet, drawer, box or any other type of container.
- Each in-warehouse movement must be examined, as the biggest potential in automation lies in robotizing repetitive movements. These can be carried out manually or be assisted.
- Don’t let yourself be swept away by unrealistic expectations and remember that, normally, a company automates a specific part, zone or operation of its warehouse.
What tasks should I set my sights on? The best results in robotization happen when these three factors flow together at the same time:
- Repetitive movements.
- Huge volumes of operations.
- Big loads to be handled.
Robotization can be readily applied in a building adjacent to manufacturing plants, since the company can regulate and coordinate production flows with those linked to storage. Although, in general, any kind of warehouse can be robotized where the three points above are present.
Main warehouse robotics systems
So, we trace a route through the main systems, organizing them according to the processes they execute:
1. Extraction and storage of goods
- Stacker cranes
This is an automated system able to pick up and place pallets or crates or totes on the shelves. An AS/RS stacker crane comprises a sturdy upright mast that runs along the racks, as well as a cradle with forks where the pallet or crate is placed. These machines replace forklifts.
- Pallet Shuttle
The Pallet Shuttle moves along the high-density racking channel and brings the rear pallet forwards and vice versa. In its semi-automatic version, the Pallet Shuttle works side by side with the operator, as they can program and operate it directly from the forklift with a tablet.
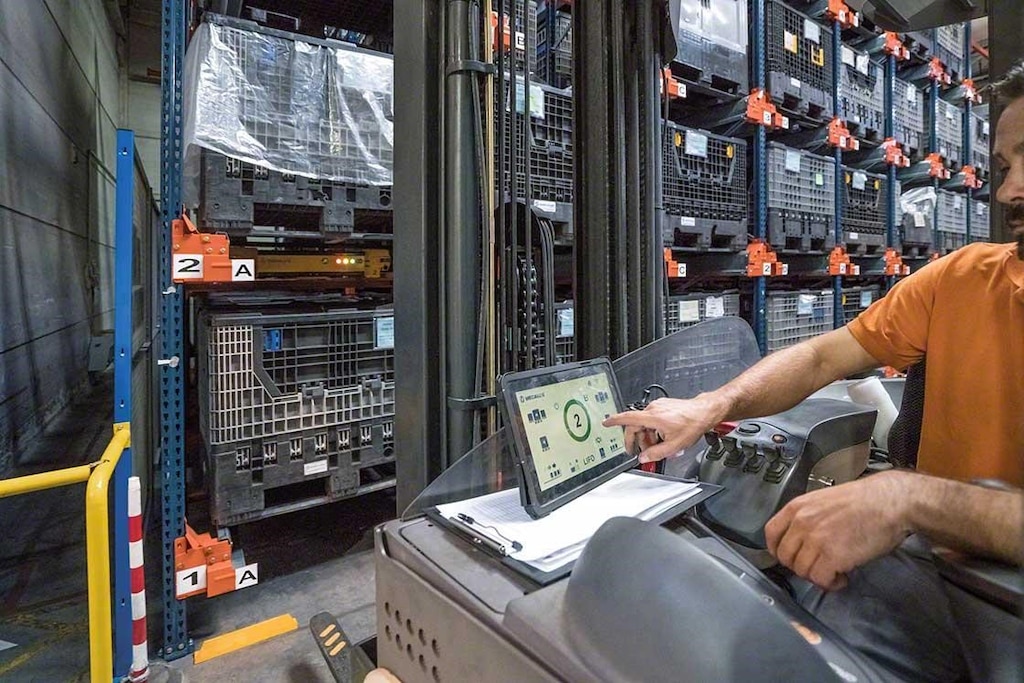
2. Transport of goods between different zones
- Conveyors
Whether with rollers, belts or chains, conveyors are a fixed system for moving loads in a warehouse. They cut back on the movements of goods with manual handling equipment. Usually, they are devised as a vital addition to stacker cranes in automated warehouses, although conveyors are used for a wide variety of purposes in different warehouse zones.
- Electrified monorail systems
Overhead conveyors or what are called electrified monorail systems run the same operation as conveyors, except they feature an overhead rail system (i.e. not anchored to the warehouse floor). Their main advantage is the high speed they reach. So, they are used for medium distances, as seen in the warehouse that Mecalux designed for the Polish company Sokpol.
- AGV or LGV Vehicles
Automated Guided Vehicles (AGVs)—or what some also call Laser Guided Vehicles (LGVs)—can follow a mapped-out itinerary with no human involvement whatsoever. They are similar to forklifts: fitted with a loading platform with forks. Their sensors let them pick up and follow the radiofrequency waves emitted by a transmitter located in a buried cable. One such system can be found in the goods reception area of the Dafsa automated warehouse.
3. Auxiliary picking systems
- Anthropomorphic robots for automated picking
In some warehouses with predictable, stable operations, it is possible to install robotic arms that execute the entire order preparation phase automatically. These are fixed industrial robots that normally help place and palletize goods.
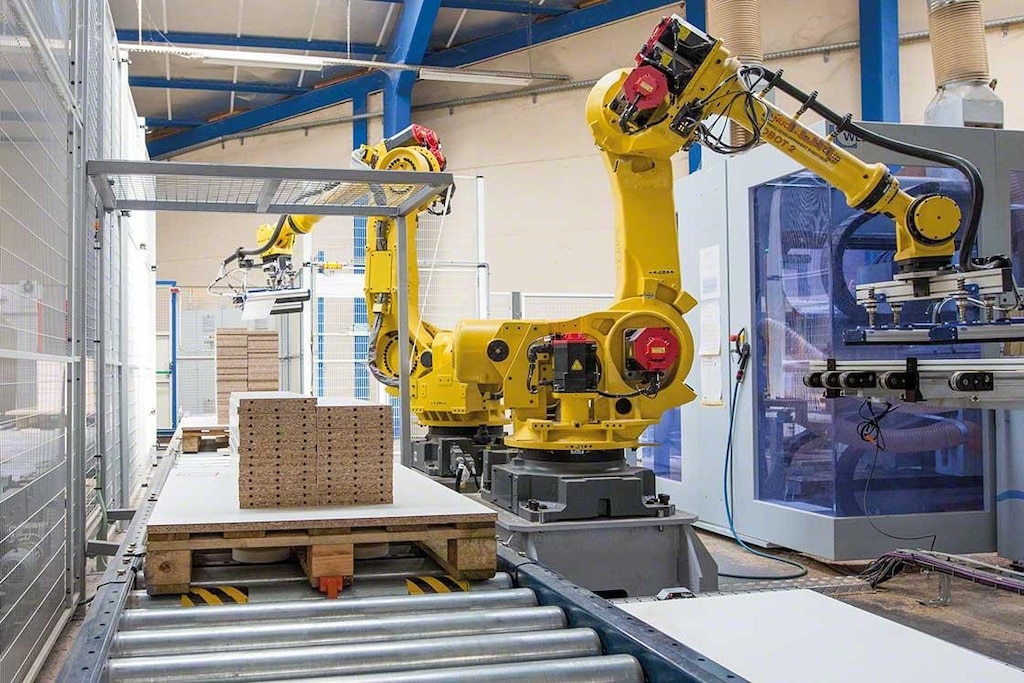
- Auxiliary robots that assist the operator in picking operations
In this field, several cobots are spread out to help the worker perform tasks:
- Heavy-duty mechanical arms: used to transport weighty goods to be palletized. A good example is in Cepsa's automated warehouse in Spain.
- Packing machines: they come in very different formats depending on the kind of packing required. For example, packaging systems prepare and calculate the filling for each box, making it easier for the operator.
- Mechanical exoskeletons: also known as Personal Protective Equipment (PPE); these robotic mobile suits adjust to the person who wears them, improving their physical capacities and limiting fatigue from performing movements.
Key needs linked to automated warehouses
A robotic warehouse does not only rely on its installed systems, but also on elements such as:
- Software’s indispensable role in warehouse robotics: despite how imposing some industrial robots seem, they would be useless without the various software layers to which they are connected. Different types of software mean they can program, communicate and execute movement orders and make decisions in warehouse management to optimize your entire operation.
- Preventive maintenance program: apart from putting an action plan in place if a breakdown occurs (which usually includes contacting the supplier’s technical service right away), you need to develop a preventive maintenance program that can avert unexpected disruptions that can hamper warehouse activity.
- Operator training: programs need to be implemented to help update workers’ skills by focusing on digitizing tasks, running software and automated systems that, in turn, have intuitive interfaces to accelerate your team’s learning curve.
Robotic warehouses are part of today’s modern business. Automation and robotization forge one of the most profitable avenues towards gaining efficiency and improving the quality of warehouse logistics processes. If you are thinking of getting the upper hand in your warehouse and want some advice from one of our robotics and automation experts at Interlake Mecalux, please get in touch.