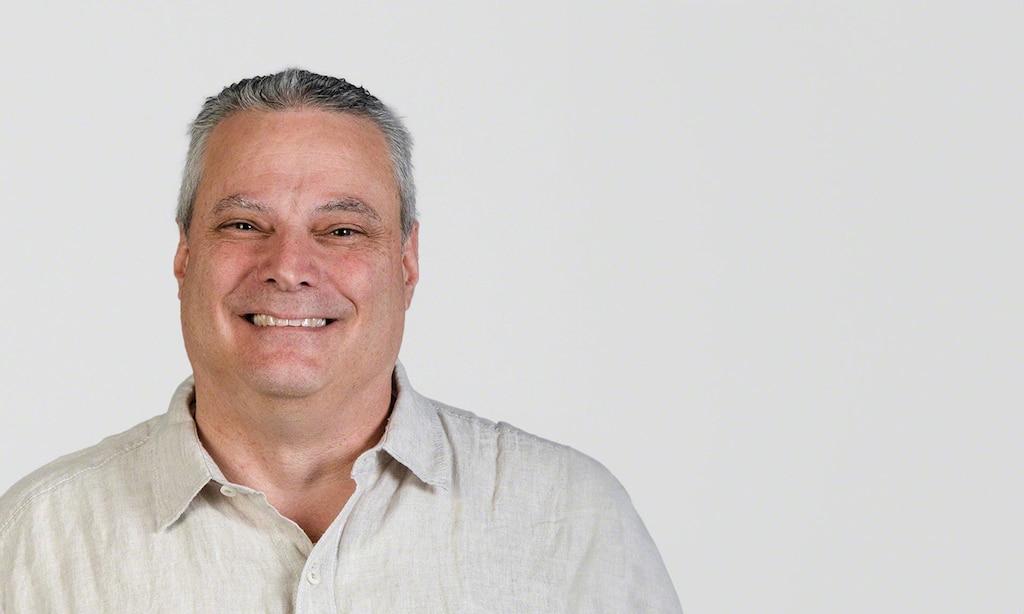
“With the Interlake Mecalux solution, we’ve simplified our warehouse operations”
About College of DuPage
With more than 28,000 students, College of DuPage is the second-largest higher education institution in the state of Illinois. Its 272-acre Glen Ellyn campus is home to 11 buildings and a warehouse equipped with Interlake Mecalux push-back racking. This storage system accommodates a significant amount of paper and supplies for the college’s students, faculty, and staff.
Mecalux interviews Angelo Conti, Warehouse Manager at College of DuPage (Illinois), to discuss how the Interlake Mecalux solution enhances safety and efficiency in storage processes.
-
What role does your warehouse play in the scope of the entire college?
We’re kind of behind the scenes. We’re not a student-facing department, but we provide part of campus services. So, our role is to offer services to all departments throughout the college. We handle all of the school’s inbound shipments. Everything and anything that the college orders comes through us. We take care of all of the asset management. We touch everything because it has to get received through us in our system.
-
What made the college upgrade its facility with Interlake Mecalux storage solutions?
What we had prior were just free-standing racks that weren’t push-back, so we needed to use our reach truck to reach into the structure and pull the pallets forward every time we needed them. From my previous job, I was well aware of push-back racks because they’ve been around for years. Installing the push-back racking simplified things a lot, so that’s what drove us to do it.
We never have to use a reach truck to retrieve pallets — they move forward automatically, allowing us direct access to any product
-
What benefits have the push-back racks brought to your logistics operations?
Keep in mind, it’s a college. We’re not producing anything, and we don’t have timelines like a manufacturing facility would. For us, this was more of a safety feature and a matter of convenience because we don’t need to get on the reach truck now to pull a pallet forward. We can use a sit-down forklift. We don’t need to climb underneath a rack to remove boxes from a pallet. The pallet is going to push forward to the front of the rack. We deal with a lot of paper here. The paper comes to the front, and we can now take the cases of paper off the pallet.
-
”The choice of this system was a matter of safety, convenience, and efficiency in storage operations” What were your logistics processes like before putting this new storage system into operation?
We had to get on the reach truck to pull pallets forward all the time because everything was in the back, and nothing would come to the front. People weren’t willing to wait, and they would climb into the racking to get cases of paper, which was a major safety concern. That’s kind of what motivated this whole project. It’s just so much better now. It’s second nature. We don’t even think about having to carry out risk-prone actions anymore. The process of how we pull paper out of the racks has totally changed.
-
How did Interlake Mecalux work with you to devise the best solution for your facility?
We looked at a couple of different types of racking. We wanted to stick with something heavier duty because of the weight that we’d be putting on them. These push-back racks are pretty sturdy structures. We store all the college’s paper, which is very heavy. That more or less determined the type of racking we’d get because we were replacing heavy-duty racks.
-
Why was this particular storage system selected for the facility?
We chose it mainly for safety reasons. When we receive orders for paper, we have to pull the cases. We don’t want to be forced to climb under the rack to get that pallet and remove the cases from it. So, if the pallet that we’re done with rolls forward and the one behind it rolls forward, we don’t need to climb under the racking; there’s always a pallet in the front. We never have to use a reach truck to get that pallet because it moves forward automatically, allowing us to retrieve anything we need from the front of the racking, even on the top level. For us, it was more of a convenient safety feature because before, the process was quite a hassle.