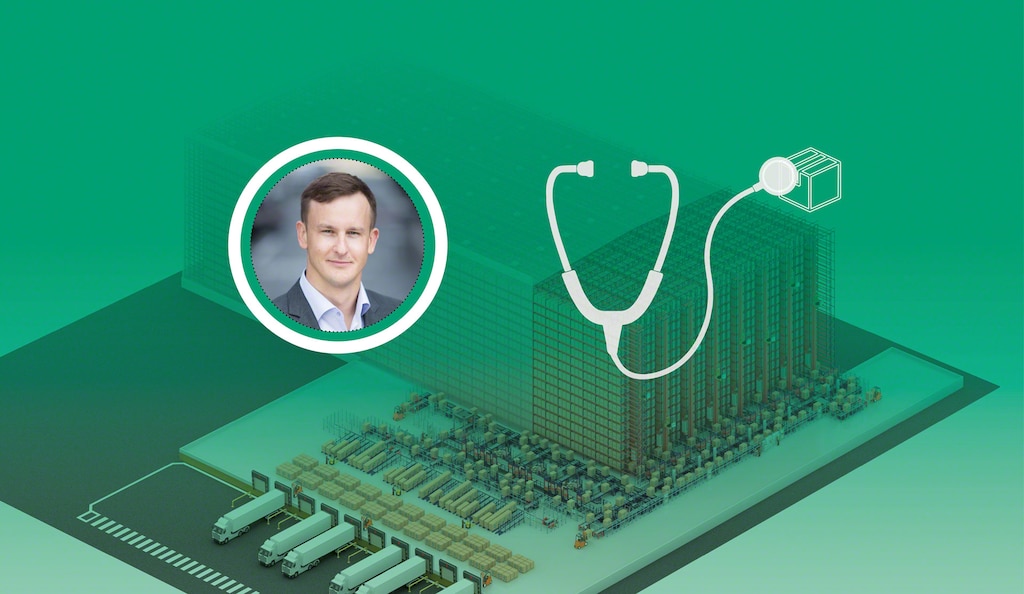
Health logistics challenges during the Covid-19 pandemic
An interview with Martynas Tamosiunas, Intersurgical
During the coronavirus outbreak, Intersurgical, a global supplier of medical devices for respiratory support, experienced a dramatic increase in movement flows in its automated warehouse. The company’s main logistics hub, an impressive 98.4-foot-tall clad-rack warehouse built by Mecalux in Lithuania, was crucial for handling the 50% rise in inflows and outflows during the pandemic.
Mecalux talked with Martynas Tamosiunas, Group Supply Chain Manager at Intersurgical, about how the company adapted all its logistics processes and benefited from automation to handle the unprecedented demand during the pandemic.
-
How did Intersurgical manage its logistics operations to face the sudden surge in demand for ventilators and other medical devices used with ventilators?
Among other projects during the pandemic, we were involved in a project for the Lithuanian Government that required us to develop, manufacture and distribute one million respirators for emergency rooms, hospitals, and homes in record time. This was a critical pandemic project where time was of the essence. All teams involved at Intersurgical worked hard to make sure we had enough materials and production resources to deliver the respirators on time. This time-sensitive project proved that we were capable of reorienting our efforts in difficult times to overcome a critical health challenge.
-
Your efforts saved many lives.
The project contributed a great deal to our country’s fight against Covid-19. In our internal discussions, it was easy to motivate the teams because we were aware of the negative consequences of not having enough products for respiratory care. We did our best to help hospitals and healthcare workers. Even our suppliers were fully on board — we didn’t need to spend much time convincing them to prioritize our materials over other industries — they always worked against the clock to make sure we received all the materials we needed.
We were involved in a project for the Lithuanian Government that required us to develop and manufacture one million respirators for emergency rooms, hospitals, and homes in record time
-
How important was your automated warehouse in this scenario?
The automated warehouse is located in the town of Pabradė, Lithuania, which is also home to our group’s biggest manufacturing plant. We manufacture solutions for airway management, anesthesia, critical care, and oxygen and aerosol therapy. In total, 99% of these items are exported to other countries around the world. The automated warehouse centralizes our logistics operations and plays a strategic role for Intersurgical to distribute our products across the world. The warehouse was built right before the pandemic. The onset of Covid-19 accelerated everything, and automation became crucial for Intersurgical to handle the swift increase in demand. With our new automated warehouse, space and related logistics processes were no longer a problem for us, so we were able to focus on production; this turned out to be the key to coping with the huge demand. Having the automated warehouse fully operational in time for the pandemic also helped us to ensure that we had enough flexibility in our supply chain to handle unexpected demand peaks.
-
“The automated warehouse centralizes our logistics operations and plays a strategic role for Intersurgical to distribute our products across the world” How has Covid-19 affected your activity at Intersurgical?
At the onset of Covid-19, our business experienced two major changes. First of all, the demand for our products increased dramatically, over ten times more than we could manufacture. We had never seen anything like that. Then, the products that we were selling prior to Covid-19 were temporarily no longer in demand.
-
How did you manage that change?
In the initial stages of the pandemic, we had to reorient our full portfolio and boost our capacity as much as possible. This change created many challenges for our organization. From one day to the next, we had to readapt our supply chain, production, and capacity plans from scratch. It was a huge challenge because most of our previous strategies and plans were no longer appropriate, and everything had to be redone and implemented very fast. There’s no perfect plan for an unexpected event such as a pandemic. We had to forget about everything we knew, adapt to the new reality, and start operating in a different way. It has been a big challenge for all of us, but also a very interesting period from a business perspective.
-
What role do automation and technologies such as warehouse management systems play in your logistics processes?
Technology and automation are at the core of our strategy. We constantly automate our production processes, so it was only a matter of time to also start automating our logistics operations. Technology helps to ensure that our processes are more integrated and managed more efficiently. Automation allows us to have much better control of all our processes and better predictability. It helps us to manage our supply chain in a reliable and efficient way.
-
Has Covid-19 brought opportunities for improving your logistics performance?
I believe so. When the pandemic started, we had just put our new automated warehouse into operation. Suddenly, the demand for our products increased dramatically, and we had to adapt our logistics processes to make sure that the automated warehouse was working at full speed, that we were properly trained and that we got used to the processes very quickly. To summarize, the pandemic accelerated some logistic aspects that we had planned on addressing in the future.
-
“Logistics and supply chain management are at the core of many businesses and industries” Beyond Covid-19, what are some of the challenges companies in the medical device sector are facing today?
First of all, the demand for some of our products hasn't come back to pre-Covid levels yet, and it remains to be seen when things will go back to business as usual. We’re in the process of getting back to normal, which makes our supply chain and production planning extremely challenging. Another recent challenge this year was the chaos in the container shipping industry. This situation is causing additional headaches for many companies because it means more uncertainty on top of Covid-19. We’re coping well at the moment and finding solutions for these unexpected events, but we don’t know what else the future will hold.
-
In your opinion, which way is logistics heading in the medical equipment sector?
We can observe general trends across all industries that also apply to the medical equipment sector. Many sectors are moving towards having more control over their processes, more predictability, and better coordination of supply chain operations. For global supply chains to work effectively, every element in the chain needs to be connected — all the partners have to know about each other’s processes. This requires robust information systems, more automation, and better integration of all processes. I believe our industry is also moving in this direction, perhaps even faster than other industries in some areas.
-
What skill sets will be useful for supply chain managers in the post-Covid era?
Logistics and supply chain management are at the core of many businesses and industries. I believe that today and even more in the future supply chain managers should be able to adapt quickly and react, replan, and reshape strategies in record time to obtain optimal results in the shortest time possible. Another skill that I believe will be necessary is the ability to lead global teams and global processes — and to see beyond and across a company’s country and manufacturing site.
-
What do you think Intersurgical’s logistics operations will look like once the pandemic is over?
Nobody knows yet. There are many things that are difficult to predict from today’s perspective. We don’t even know when the pandemic will be over. But one thing we know for sure is that the pandemic will have long-term consequences. The need to manage global processes will likely grow, and businesses will have to be more adaptable to unpredictable events such as pandemics or natural disasters.