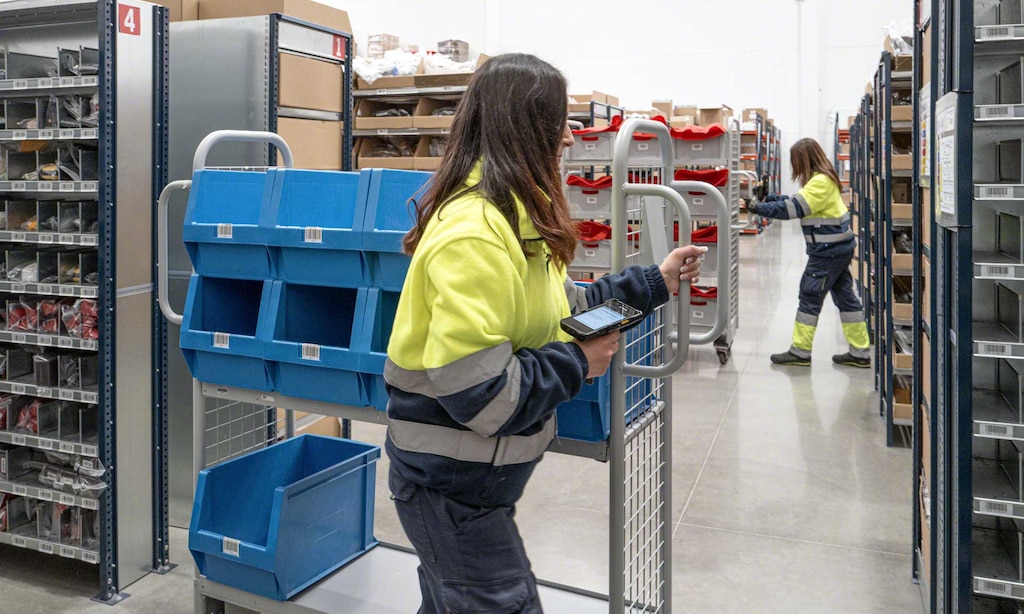
LOGISTICS RESEARCH
By Shuya Zhong, Vaggelis Giannikas, Jorge Merino, Duncan McFarlane, Cheng Jun, and Shao Wei
Order picking and packing are two key processes warehouses use to fulfill customer orders. Order picking deals with the collection of required goods from their storage locations. It is followed by packing, where goods are placed in different types of containers (e.g., boxes, parcels, and bags). Both operations are critical in defining the flow time an order spends in a warehouse, from the point it is placed by a customer until it is ready for shipment.
In this study, we analyze the results of integrating picking and packing planning in e-commerce warehouses. Determining its usefulness requires consideration of both components: improving just one of these operations will not have a major impact because they affect each other significantly.
However, although picking and packing are closely linked, they are often successive but separate processes performed by two differentiated employee teams. We propose that managing order picking and packing in an integrated way leads to improved warehouse performance compared to organizing each operation separately.
Three key questions
Taking an integrated picking and packing approach focuses on not only improving the performance of each standalone process but also reducing the waiting time between them. To this end, we used two main metrics: the order processing time (the time needed for a single order to be prepared and ready for shipment) and the makespan (the time required by the warehouse to process a certain number of orders until they are ready for shipment).
Generally, an e-commerce order can be classified into one of four categories depending on the number of SKUs it contains and the quantity requested for each SKU. These are 1-SKU-1-item, 1-SKU-multiple-items, multiple-SKUs-1-item, and multiple-SKUs-multiple items. This classification affects the number of storage locations that need to be visited and the retrieval, sorting, and packing time.
Our study also takes into account the different levels of workforce assigned to picking and packing. To assess the potential benefits of operating in an integrated way, we designed an experimental study based on empirical data from a warehouse company. Using a mathematical model, we compared integrated and non-integrated planning of picking and packing.
Integrated picking and packing management can enhance warehouse performance
The mathematical model aimed to answer three key questions: How should orders be grouped into pick lists? How and in what sequence should the pick lists be assigned to pickers? How and in what sequence should the pick lists be assigned to packers after picking is completed?
To address our research questions, we considered the following warehousing characteristics, inspired by relevant literature and the operations of our case company. The facility runs a low-level order picking system with picker-to-part, sort-while-pick operations. The picking area includes a multiple-block layout of wide pick aisles and a depot, with each SKU stored in a single location. Pickers use trolleys, which are always available, and follow an S-shaped route. Packers, meanwhile, remain at their workstations.
Four different scenarios
The manual warehouse studied is an order fulfillment center for an online retailer. We analyzed several scenarios with diverse order volumes. Each one required varying quantities and SKUs, and orders were distributed among different numbers of pick lists.
Picking and packing waiting and execution time of integrated and non-integrated methods
When there are more packers than pickers, time savings occurs before picking
- With 300 orders and a maximum of 24 pick lists, integrating the organization of picking and packing reduced the order processing time and the makespan. To achieve this, the integrated method “sacrificed” some efficiency in picking to gain significant time savings in the packing phase. Hence, overall performance was improved.
- In scenarios with 100-600 orders structured between 8 and 48 pick lists, our findings show that as the number of orders increased, the benefits of integrated management of picking and packing typically decreased.
- In examining 300 orders of varying types and proportions (1-SKU-1-item, 1-SKU-multiple-items, multiple-SKUs-1-item, and multiple-SKUs-multiple-items), we observed that the integrated method enhanced performance. The most considerable advantages were seen in cases with order pools of medium complexity.
- Twelve workers were assigned in various combinations to vary the number of pickers and packers filling 300 orders with 24 pick lists. When there were more pickers than packers, the greatest benefit of integration was the considerably reduced waiting time before packing. With more packers than pickers, time savings occurred before picking began. This demonstrates that for certain scenarios where there are no opportunities to accelerate the packing process, the integrated method would not be advantageous.
Results: smaller picking waves
Our results indicate that integrated picking and packing planning can enhance performance under various conditions. They show that focusing solely on improving picking does not guarantee gains in overall system performance, as the packing process that follows can act as a bottleneck. In particular, small sacrifices in picking management can lead to greater time savings during the packing phase, increasing efficiency overall.
Likewise, there appears to be an inverse relationship between the number of orders one has to plan for and the advantages integration can offer. This highlights the importance of deciding how many orders should be grouped together before a planning process begins, (i.e., wave release). As the results of this study indicate, in practice, it might be preferable to opt for multiple, smaller waves to capitalize fully on integrated planning.
AUTHORS OF THE RESEARCH:
- SHUYA ZHONG. Associate Professor in Logistics and Supply Chain Management, University of Bath (UK).
- VAGGELIS GIANNIKAS. Professor of Technology and Operations Management, Director of the Centre for Smart Warehousing and Logistics Systems, University of Bath (UK).
- JORGE MERINO. Research Associate at the Institute for Manufacturing, University of Cambridge (UK).
- DUNCAN McFARLANE. Professor of Industrial Information Engineering, Cambridge University Engineering Department; and Head of the Distributed Information & Automation Laboratory within the Institute for Manufacturing (UK).
- JUN CHENG. Shenzhen YH Global Supply Chain Co., Ltd (China).
- WEI SHAO. Shenzhen YH Global Supply Chain Co., Ltd (China).
Original publication:
Zhong, Shuya, Giannikas, Vaggelis, Merino, Jorge, McFarlane, Duncan, Cheng Jun, Shao Wei. 2022. “Evaluating the benefits of picking and packing planning integration in e-commerce warehouses.” European Journal of Operational Research, 301 (Elsevier).
An open-access version of the manuscript can be found here.