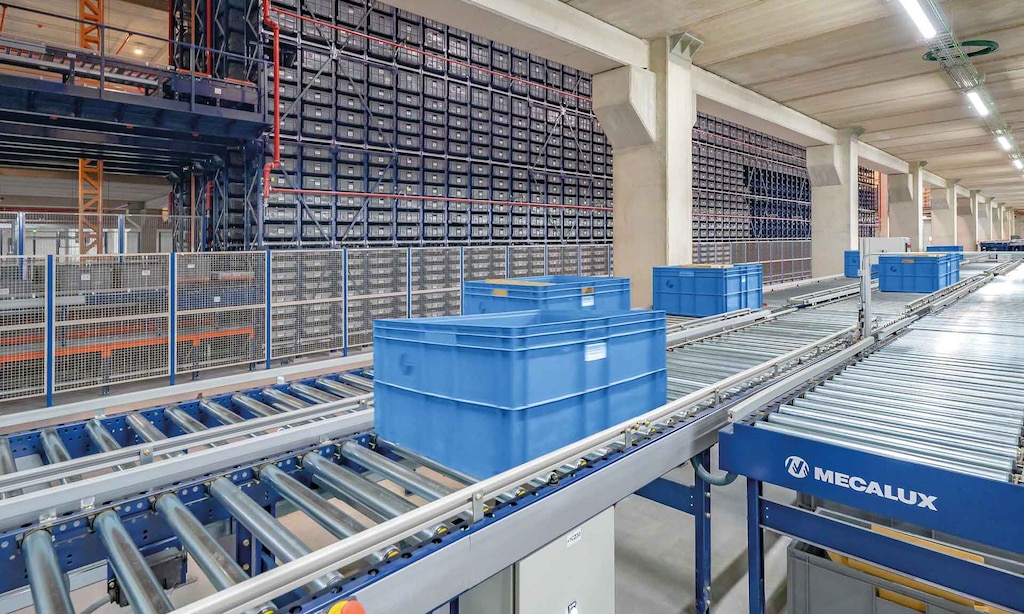
IN-DEPTH ANALYSIS
By Beatriz Royo
Covid-19 demonstrated that the European manufacturing sector is very vulnerable when facing unprecedented events for which it is not prepared. Reports from the European Union show that this sector was more heavily impacted and is experiencing slower growth than other areas of the economy.
While the support of governments cannot be underestimated, the resilience of manufacturers is what made the difference that enabled certain companies to thrive during these challenging times. Covid-19 shone a light on the ability of many businesses to leverage flexibility or reconfigurability to adapt and grow. Since then, continuous, significant disruptions are becoming the new normal (e.g., climate change and the wars in Ukraine and Gaza). Organizations need to be able to operate in volatile, uncertain, complex, and ambiguous (VUCA) environments, and the answer to tackling these challenges is to increase the resilience of manufacturing firms.
Resilience can only be achieved through rapid reconfigurability and digitalization
In the case of medium- or high-volume manufacturing industries, resilience can only be achieved through rapid reconfigurability and digitalization. This swift transformation must be implemented at all production levels, including the factory, machinery, individual processes, and interactions with the supply chain as a whole.
R3GROUP is a four-year European project created to support the resilience of manufacturing firms by providing digital tools. The objective is to enable rapid reconfigurability and respond to the VUCA manufacturing environment. The project focuses on four scenarios of changes that heavily impact the manufacturing industry.
VUCA scenarios affecting the manufacturing industry
Companies across Europe are participating as pilots in R3GROUP to demonstrate whether Industry 4.0 technologies will lead to a more resilient, rapid, and reconfigurable manufacturing sector. Within the framework of the project, they will test different digital technologies and demonstrate whether it is possible to respond to external events more agilely and prevent risks more proactively. The technologies and use cases explained below are being developed following the human-centered principle.
IoT connectivity
One element of a manufacturing system’s reconfigurability is integrability. Managing production is a multi-level challenge, encompassing everything from the shop floor to the engineering and management offices, including internal interactions and downstream and upstream supply chain flows. The Asset Administration Shell (AAS) serves as the reference architecture where all the data will be encapsulated.
An AAS is an implementation of a digital twin for industrial applications. This tool equips any component with the ability to share information within the digital IoT world. It is deployed in the cloud with a cyber-physical production system (CPPS) approach, where the information and communication technologies in the offices and the operational technologies on the shop floor have evolved to converge into a unique integrated platform.
The resulting interoperable digital platform is the technological foundation for the project and the smart factories of the future.
Evolution of IT-OT convergence into an integrated system. Source: Conrad Leiva
Multi-level digital twins
To successfully navigate VUCA conditions, manufacturing supply chains need to be able to calculate the effects of anticipated reconfiguration alternatives. This will allow professionals to identify the optimal path through informed decisions. Thus, R3GROUP is considering multi-level digital twins as a key enabler for evaluating the impact of reconfigurability.
Unit-level digital twins
These replicas comprise the machine, manufacturing process, and workpiece. They are deployed by combining surrogate modeling approaches, data-driven models, and artificial intelligence (AI) techniques to explore non-linear relationships.
Line-level digital twins
A line-level digital twin, such as the one developed by Greek copper tube manufacturer Halcor, integrates data coming from every production and quality assurance step. These twins will make it possible to develop advanced (re)routing and (re)scheduling algorithms to optimize material flow within production and reduce lead times and costs.
Factory-level digital twins
These digital counterparts will use as inputs the outcomes of reconfiguration awareness tools to provide support for strategic decision-making. Gorenje, a Slovenian toolmaking company for the household and automotive industries, will use the information from the shop floor and legacy information systems to dynamically support production scheduling/planning and layout planning.
Supply chain digital twins
Supply chain digital twins (SCDTs) will enable the evaluation of the impact of supply chain decisions by leveraging the data integrated into the platform, external data, and employing various analytical, optimization, and simulation techniques. Katty-fashion, a first-tier Romanian womenswear manufacturer, is transitioning from physical to digital prototyping in the product design phase. On the one hand, this shift is poised to bring many benefits by avoiding the processes of sourcing, manufacturing, and transporting samples. On the other hand, this transformative change might have a significant impact on final product availability and quality. Thus, the company is leveraging the valuable data, tactics, and production-generated knowledge of its factory and supply chain operations to develop product and supply chain digital twins. These models will help the manufacturer understand the impact of this change and create more accurate cost, operational, and environmental models to support decision-making at both the factory and supply-chain levels.
Real-time decisions
Beyond the manufacturing industry and R3GROUP use cases, supply chain officers in other industries are expected to make quicker, more informed, and accurate real-time decisions. This requires two things: knowing exactly what is happening in the supply chain at any given moment and seeing into a variety of future scenarios. A stress testing tool represents an additional capability of SCDTs. Subjecting the chain to different disruptions and examining how it would react may detect weaknesses in the supply chain and determine the most effective path of action to make it more robust.
An illustrative real example of the potential of SCDTs is JD.com. This retailer achieved the highest revenue by reconfiguring its supply network during Covid-19. Back then, JD.com operated 41 mega “Asia No. 1” logistics parks in China, with almost 1,300 warehouses and more than 9 million self-operated stock keeping units (SKUs).
Digital twin technology can help companies boost revenue
JD.com addresses upstream and downstream supply chain planning and operations. In a two-level supply chain network, upstream distribution centers (DCs) might have been unable to distribute goods to warehouses due to Covid outbreaks resulting in travel restrictions. In those cases, JD.com needed to reconfigure its supply chain network to respond to the disruptions. The company managed to replenish orders through other alternative DCs or using the backorder strategy. Nevertheless, adopting alternative DCs decreased the order fulfillment rate and led to significant additional transportation costs. The SCDT platform was used to examine conflicting objectives. This innovative tool for human–AI collaboration in decision-making combined historical and real-time data with knowledge of business processes (such as corporate policies) and cutting-edge AI approaches and algorithms.
Framework of JD.com’s SCDT platform
Digital twin technology can help companies boost revenue by up to 10%, improve time to market by as much as 50%, and upgrade product quality by up to 25%. However, implementing this technology usually requires the involvement of nearly all teams, as it should cover all essential supply chain management processes. This may make it a bit overwhelming and lead to certain mistakes. Consequently, businesses must analyze their supply chains and devise a roadmap by prioritizing the critical areas that, when improved, will yield the most returns.
Technology-driven smart supply chain
Given the innovative approach of the SCDT concept, the opportunities to build and improve the smart supply chain are considerable. Practitioners should embrace innovative digital twin technology to build an SCDT from the ground up and stay ahead of the competition. Realizing the smart supply chain vision takes time, but the transformation is worthwhile. By combining internal data with external disruptions, organizations can anticipate the need for reconfiguration. As a result, digital technologies will enable more resilient, rapid, and reconfigurable supply chains across Europe.
References:
- De Vet, Jan Maarten, Daniel Nigohosyan, Jorge Núñez Ferrer, Ann-Kristin Gross, Silvia Kuehl, and Michael Flickenschild. 2021. Review of Impacts of the COVID-19 Pandemic on EU Industries. European Parliament. Policy Department for Economic, Scientific and Quality of Life Policies, Directorate-General for Internal Policies.
- EUROPEAN COMMISSION the SECTORAL IMPACT of the COVID-19 CRISIS.
- Factories of the Future - European Commission. Single-Market-Economy.ec.europa.eu.
- Industrial Platforms | Shaping Europe’s Digital Future. Digital-Strategy.ec.europa.eu.
- Latif, Hasan, Guodong Shao, and B. Starly. 2020. A Case Study of Digital Twin for a Manufacturing Process Involving Human Interactions. Online World Conference on Soft Computing in Industrial Applications.
- Siemens and NVIDIA to Enable Industrial Metaverse. NVIDIA Newsroom.
- Digital Twin Factory: Hoja de Ruta - ASM Soft.
- Katty Fashion Website. Katty-Fashion.com.
- Sahilbhutada. 2023. Digital Twin Technology and Supply Chain Management. Medium. May 6, 2023.
- Oil Prices Remain Volatile amid Uncertainty Arising from Geopolitical Conflict. World Bank Blogs.
- Reinventing Supply Chain for the Future. 2022. Gartner.
- Simchi-Levi, David, and Edith Simchi-Levi. 2020. We Need a Stress Test for Critical Supply Chains. Harvard Business Review. April 28, 2020.
- Wang, Lu, Tianhu Deng, Zuo-Jun Max Shen, Hao Hu, and Yongzhi Qi. 2022. Digital Twin-Driven Smart Supply Chain. Frontiers of Engineering Management 9 (1): 56–70.
- Koshulko, Alex. Council Post: How Digital Twins Can Help Supply Chains Survive Disruption. Forbes.