One of the primary issues when constructing a warehouse is where to build it. The warehouse's location is an influencing factor in its construction and, even more importantly, on the strategy of the company. Therefore, it can be crucial to the success or failure of the business.
The process of deciding on the location of a warehouse will be longer and more complicated the larger the company and, therefore, the larger its distribution system. In any event, this process must always consider four basic factors: production, demand, costs, and competition.
For each of these elements two different aspects must be considered – financial and commercial – to create as realistic an analysis as possible. Bearing this in mind, the analysis must include a range of variables.
- First, in regards the product, an assessment must be carried out on the type and total quantity of the product to be stored.
- In terms of costs, these relate to infrastructure (land, buildings, and equipment), direct and indirect labor, transport and handling costs, and parallel costs of the activity, as well as services and insurance policies that must be bought.
- In terms of demand, one must estimate the quantity and location of consumers, the number and size of orders, the demand curve, the relative importance of proximity, and the speed of delivery.
- Lastly, with regards to competition, one must examine the location of their warehouses, and the efficiency and services provided by them.
The analysis to determine the location of the warehouses must be carried out by examining these variables and the four parameters discussed in the following paragraphs. For example, the characteristics of the product, the manufacturing capacity of the industry and the specific features of the distribution network required.
Location according to product characteristics
Three factors must be taken into account when analyzing the characteristics of the product that may influence the location of the warehouse: durability, intrinsic stability, and manageability.
Durability
This characteristic determines how close distribution warehouses should be to points of consumption.
Thus, products with a low durability (such as fresh fruit and vegetables) require installations that are very close to final purchase points, since the time between their production or picking and their consumption must be very short. Therefore, transit warehouses cannot be used with these items because even the short period of time the product spends there could prove disastrous in terms of its conservation.

Close up of a loaded pallet
For very long-lasting products, such as almost all industrial items, there is no need for warehouses to be very close to points of consumption, at least from the perspective of how time impacts quality, since time has little or no impact on their condition. Therefore, this type of item can be stored in different types of warehouses (central, regional, or transit).
Intrinsic stability
Intrinsic stability refers to the stability of the product itself, which can affect its transport and safety. If the product is intrinsically very unstable it will need special warehousing installations, since its storage could affect the physical safety of the location and even the health of nearby residents. A typical example would be chemical products, whose intrinsic instability means it is advisable for warehouses that handle them to be located in one of two locations: the point of production or the point of consumption, with no intermediate warehouses.
The size of the warehouse will be very different for each of these two options, since at the point of production it is possible to have a large storage facility (an actual warehouse). Meanwhile, at the point of consumption there will only be storage room of a size which reflects the demand and the average transport time between the two locations.
This is not a determining factor when storing goods of great intrinsic stability, where any of the options discussed earlier can be used.
Manageability
The options for handling a product and the ease with which it may be handled can be restrictive characteristics in terms of the number of movements that may be carried out with the item.
Very hard-to-handle products, such as liquids and bulk aggregates, must be stored in as few locations as possible, since their characteristics mean that costs increase exponentially as transfers and movements take place. In addition, in most cases such movements can also lead to a reduction in quality and a loss of volume. The best solution is to have just two types of warehouses: a central warehouse, located at the production plant, and a warehouse for raw material, which must be located at the product packaging plant.
Once packaged, these items are reclassified as very manageable. At this point, where they are stored is totally independent of their manageability.
Manufacturing capacity
The manufacturing capacity of the industry served by the warehouse determines the quantity of goods that need to be stored. This is a relative factor, which must also be assessed based on the demand for that particular product.
Its influence on the location of the different types of warehouses depends on the degree of processing that takes place in an industry.

Degree of product processing
Not all industries have the same degree of product processing, as this depends on their specialization, their preparation, and, above all, on their capacity. To study possible locations for warehouses, this factor can be split into three levels: low, medium, and high.
- Low levels of processing are present in industries which, due either to the nature of the product or their capacity, are limited to merely sorting and packaging raw material. This is the case, say, for food companies in the primary sector. In this sector, only a central warehouse, located at the production plant itself, is required. The installation must have two sections: one for raw materials, another for products used in processing for the packaged product. In any event, its location does not depend on the quantity of goods that must be stored.
- A medium level of processing is where raw materials are received, sorted, and transformed into various different products. In this type of industry, the quantity of goods that must be stored starts to be a factor in the location of the warehouses. As a general rule, given that it is normally a question of mass production, whether for a single product or for several in parallel, these industries need three independent warehouses: one for raw materials, one for products used in processing, and one for finished units.
If a small quantity of items is being stored, the three warehouses can probably be located in the same place as the manufacturing plant. When production volumes are very large, local or regional warehouses must be installed, and even intermediate warehouses at times for semi-finished products, or transit warehouses for the finished products.
- Finally, industries with a high degree of processing are also highly influenced by the quantity of product obtained. Thus, their case is almost the same as for the medium level, the difference being that it will almost certainly be necessary to use intermediate warehouses to control the various stages of production.
The necessary distribution network
The composition and availability of the network required to sell an item will influence the location, number, and types of warehouses needed.
This point involves the analysis of two separate factors:
- Influence of the composition: The distribution network can be composed of independent concession holders (such as independent companies) or the company’s own agencies. In the case of the former, the amount of product that must be stored will be determined exclusively by demand and the number of orders received from this network. Under no circumstances should a staple warehouse be created, because the network itself takes care of this. For self-supplying agencies, in addition to having the classic central, regional, and transit warehouses, there must be a center for staple items in each distribution point. These must be as close to the demand areas as possible.
- Influence of the sales network's distribution: The geographic spread of the network influences the location, number, and types of warehouses required. As with the previous factor, there are two possibilities: a network of independent concession holders or self-owned agencies.
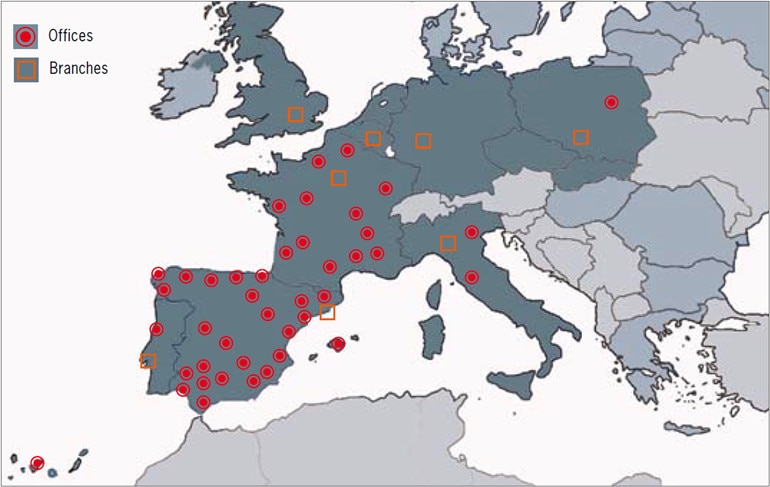
The distribution of a sales network is a deciding factor when designing a warehouse or warehouses
- If agents are positioned in the correct locations, the agent's locations should each be considered as a storage area. A distribution center is placed in each of the strategic positions and, if demand in a specific area so requires, the corresponding transit facility is created. The purpose of this strategy is to minimize the time required to supply the agents, who must be considered points of consumption.
- When concession holders are located in positions that are not the most suited to selling that particular product, the first step is to rectify this problem. Once this limitation has been resolved, proceed as set out in the previous paragraph. An incorrectly positioned sales network within a territory will inevitably lead to an increase in the use of transit warehouses and can even lead to delays in supplying consumption points, two factors that increase the cost of distributing the product and, therefore, result in a loss of market competitiveness.
If the sales network consists of company agents, it is also necessary to ensure that they are correctly positioned within the territory. This avoids, as far as is possible, the need to create more transit warehouses than is strictly essential, and to ensure that the time required to supply points of consumption perfectly reflects demand.
In any event, for both physical and commercial distribution it is possible to operate without intermediate or regional centers, working with just a central warehouse, if you have a good transport and distribution service.
Services can also be outsourced to a logistics operator, who will manage the transport and distribution, and even the storage and picking of the orders if so required.