Warehouse flooring must be able to support very heavy loads. First, there is a series of static loads under the pillars of the racking units. Then there are some dynamic loads produced by the handling equipment, for example, stacker cranes for pallets.
Loads generated below the pillars of the racking units are point loads of great intensity, concentrated on a very small surface area and distributed evenly across the entire grated surface of the warehouse floor. These are disconcerting to most construction companies, causing them a great deal of alarm, since they are concentrated on a reduced surface area of just 12.4 to 15.5 in2 (of the section of the pillar), and can reach 7.71 or 8.82 US tons, or even more.
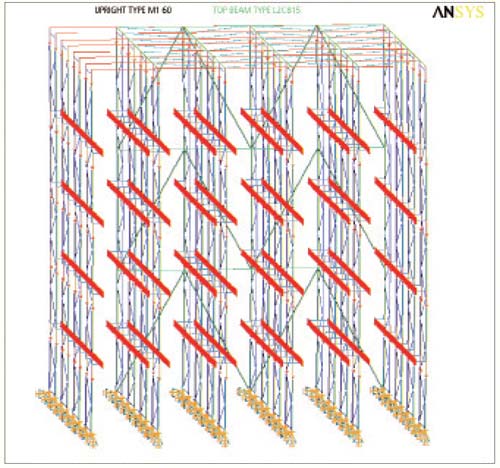
Study of the nominal load that must be withstood by the racks.
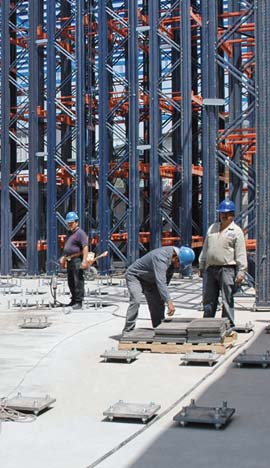
Pavement analysis during the construction of a warehouse.
Dynamic loads, which are produced by handling devices moving along very narrow aisles, are also very large and vary according to the type of machine used. In the most extreme case, like a stacker crane, this load can reach 19.84 US tons and be concentrated on a small surface area, i.e. the track of the load wheel. Yet this effect can easily be minimized, since it is distributed across the entire guide rail along which the machine moves.
With other types of handling devices, the heaviest loads are produced when they are at rest. One very significant example is VNA trucks, whose greatest impact on the floor is when they are depositing or taking a weight at the maximum height and with the forks extended to the side. At that moment in time, the pressure on the load wheels is so high that the resistance limits of the floor may be exceeded, as may those of the wheels and their bearings. This force is transmitted directly to the sides of the aisles.
Other machines, such as counterbalanced forklifts, produce their maximum pressure on the floor when they are unloaded. This pressure is produced through the rear wheels, since this is the part where the counterbalance rests. When this forklift is loaded, there is a leveling of the load in the front (through the lever principle). Although the total weight increases, this is distributed throughout the entire surface area of the machine. In this case, the load is also supported by a small surface area, namely of the tires's track.
What do we mean by “suitable flooring”?
The purpose of flooring (and its foundations) is to withstand and transfer the loads just described from the surface of the floor downwards, until they reach the subsoil level. This applies both to dynamic loads (produced by devices in movement) and static loads (loads generated by the racking unit pillars). Therefore, suitable flooring is that which has the strength and stability required to meet these requirements.
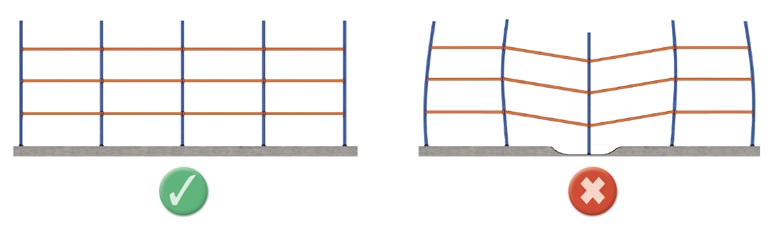
It is essential to observe floor leveling specifications to guarantee that a warehouse functions properly.
The finish of the surface must be correctly leveled within the margins and tolerances required for a certain type of installation, with its specific devices and storage system. Achieving these objectives and qualities is the responsibility of the designers and construction companies.
The importance of the substrate
Before starting to install a good floor for a warehouse, it is essential to examine the substrate or firm layer on which the flooring must be soundly supported. The substrate is quite variable and there can be enormous differences between two points, even if they are very close to each other and even within the same plot. For this reason, variations between points within a facility can be substantial.
The most important parameters that must be taken into account in relation to the substrate are its compressive strength, its tendency toward slippage, and its water-absorbing capacity. To determine the extent to which these factors are present in a specific location and to discover how these vary in depth, an analysis must be conducted on-site.
It is essential to ensure that the warehouse’s substrate will behave appropriately given the load that will be borne by the flooring laid over that substrate. The exact location and area in which the facility will be built will be determined by the results of the necessary examinations.
The characteristics of this very important part of the floor are a decisive factor influencing the foundations. The foundations can be laid using anything from simple support pads or strips of varying width to, in extreme cases, a complete grating system. At times, the characteristics of the substrate require a change in the position of the racking unit pillars, so that these coincide with the points that offer the necessary guarantees.
Composition of the flooring
The flooring is constructed on the substrate, which normally consists of a sub-base of agglomerated material, firmly compacted to withstand the load. This layer consists of any type of material, either natural or filler. A concrete slab designed to support the pressure is placed onto the sub-base.
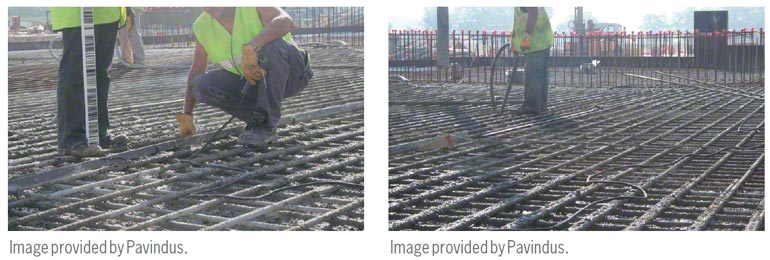
Reinforcement can also be provided using steel bars, which increase the resistance of the cured layer despite the inevitable contractions and slippage suffered by the concrete during the process.
Whether or not this reinforcement is included, it is inevitable that cracks will appear in the cured slabs, even if the greatest possible care has been taken in their construction. If these cracks are incidental and random, the impossibility of carrying out the appropriate filling due to their irregular shape invariably causes problems in terms of load fluctuations.
Cracking is often induced so that these openings appear in specific places that can be observed and controlled. This is done by sawing the slab along a given strip, cutting to a depth of between one-quarter and one-third of the layer's thickness. In this way, the breakage takes place in these positions as opposed to others, and can be easily filled following a simple and clean process.
Joints in the flooring
Joints that can be found in the floors of facilities can be caused by various factors: they may be produced by individual strips in the flooring resulting from construction (produced by the end of one working day and the start of the next), created to avoid or surround columns or walls, or produced through cutting with saws. Irrespective of their origins they can be a source of problems, creating ruts caused by the continuous passing of forklifts.
Joints must be bonded or bolted to the structure of the sub-base to prevent transfers of movement beneath the adjacent slabs. In expansion joints, the bolts must be properly built in and in complete alignment. These bolts must have a free sliding end with a plastic sleeve embedded into one of the slabs.
On the other hand, the width of the expansion joints must be proportional to the thickness of the slab, although never more than .39 inches. While they can be positioned at any point, it is always preferable to avoid places with very large point loads, i.e. far from the uprights of the racking units.
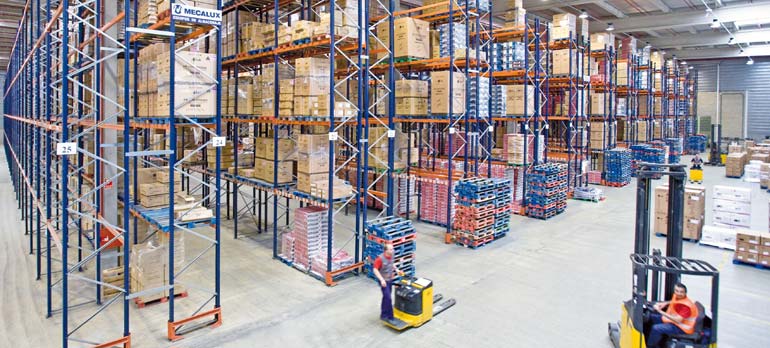
Warehouse for a consumer electronics company.
The finishing layer
A third, finishing layer is applied to the sub-base and slab. It is monolithic, and constitutes the actual working surface. Normally, the finishing layer consists of a granulite concrete mixture around 2 inches thick. The smoothness, hardness, and properties of this material are the most suitable to ensure that the flooring can withstand the conditions that exist when devices are in use in the warehouse.
The granulite concrete is applied over the wet slab of industrial concrete, forming a block on it and, thus, inherits its joints. At this point, a decision must be made in relation to a specific issue: should the finishing layer be done together with the slab and, thus, also be subject to its problems and treatments, especially with regard to the joints? Or should it be applied completely separately?
This layer can be applied independently and separately on a dry slab, but this requires the minimum thickness of the latter to be around 5 inches. In this case, a new layer of concrete is laid, with the same fragility and warping problems as the main slab, since the surface of the finish will act and contract independently. To avoid this, a new separation film or membrane, which forms a very fine layer with no appreciable joints, must be added. Extremely fine concrete mixtures can be obtained by adding bitumen or a wide range of copolymers.
If using synthetic resins, a layer of only 1/8 inch thick can be used, providing flooring with an excellent finish. If, however, a more comfortable surface is sought, one option is to use resins with greater resilience or, in other words, those with a greater elastic capacity to absorb deformation and return to its original shape when the pressure is removed.
One must bear in mind, however, that some layers created using special mixtures can be unstable or have insufficient complete granulite features, as occurs when using inappropriate resins to correct defects in the upper layer. These mixtures can end up being not only unstable, but also very expensive.
Warehouse floorings therefore need to be very carefully laid and require preventative maintenance while in use. In this way, imperfections and ruts that may be produced by the wheels of the forklifts when they move and cross the joints can be avoided and corrected. The use of such high specification finishing layers is not necessary in automated warehouses, since there is no movement over the floors.
Laying the flooring
Once the basic concepts and the elements that make up the flooring have been explained, the next step is to analyze how it must be laid. After preparing the foundation and leveling the sub-base, the next step is to decide what type of frame to use and the method for laying the flooring. This will vary depending on whether the flooring needs to be low- or high-tolerance.
The method for laying the floor is based on the use of a compaction rod, handled by two operators, which ensures that the concrete is perfectly embedded in the frame. Meanwhile, other operators, equipped with a steam roller, move over the surface. This is a typical construction method, but although the roller can help to smooth the surface it does not achieve the flattening required, as explained below.
To prevent heavy granulates and additives from falling to the bottom of the flooring or the layer, the concrete must not be handled excessively. To achieve good tolerances in the finished surface without the need for an extraordinary amount of work, the concrete must not be laid where there are significant height differences or holes in the sub-base.
Great care should be taken to ensure that the flooring is laid with a high degree of leveling; otherwise, it becomes progressively more difficult to obtain the required tolerances at each stage of construction. The frame used also has an influence here. For a relatively low-tolerance floor a wooden frame can be used, but if high tolerances are required at least the sides must be metal. The reason for this is that the accuracy of the linearity and leveling depends on the frame used. The more reliable this is, the better the results will be.
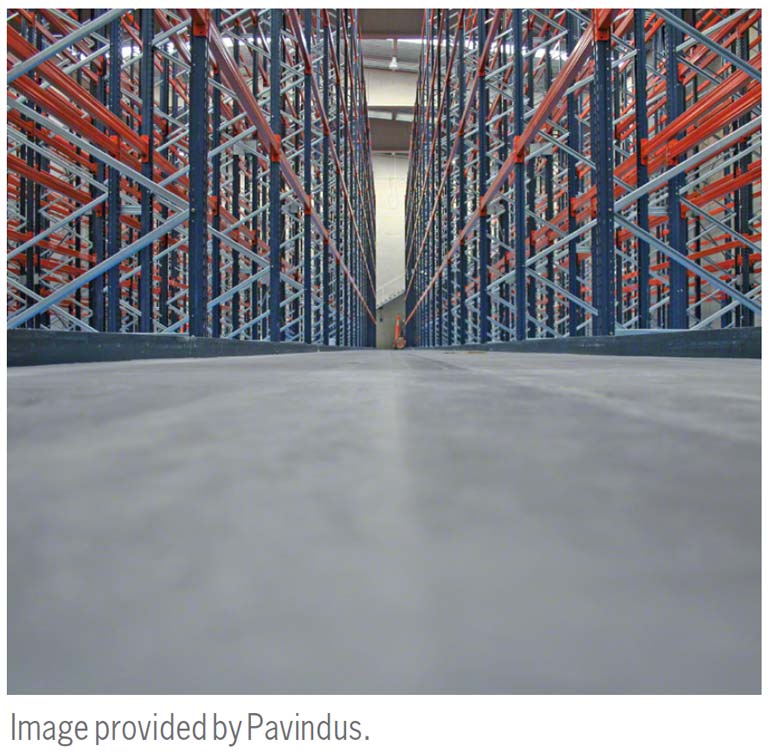
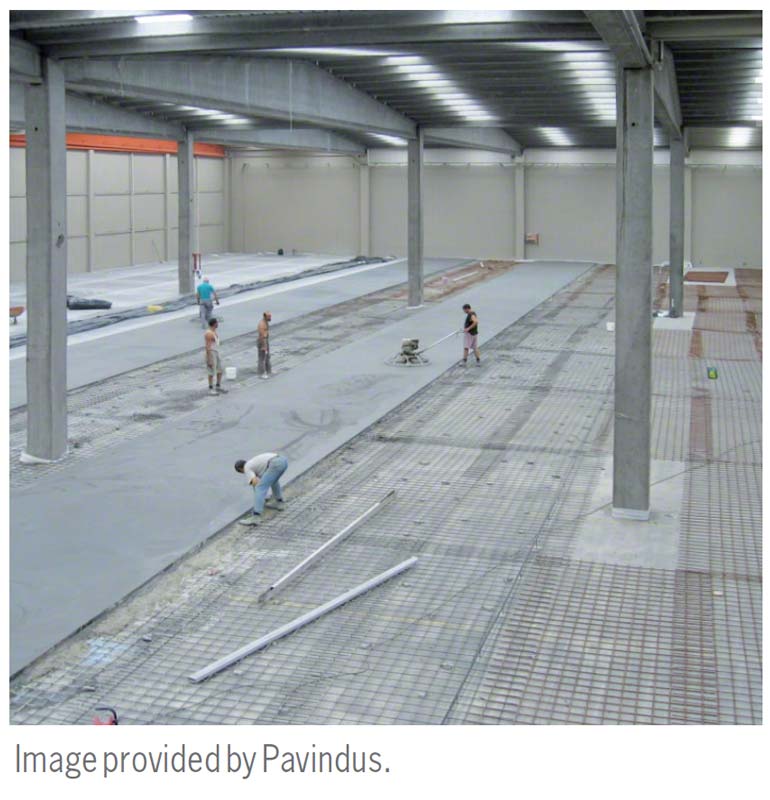
Success in creating the flooring depends not just on the use of the right frame, but also on another basic factor: the personnel who build it and their skills in using mechanical compacting and finishing devices.
A typical system for creating conventional flooring is to lay concrete strips that are finished as they are poured (this technique is illustrated in the top right-hand image). This system can raise two problems when laying high-tolerance floorings. The first is disorganized access to the filling areas during the verification process. The second is the physical difficulty of laying broad strips. Therefore, long, narrow strips may be needed.
Strips 29.5 ft to 49.2 ft long are currently achieved in premises with very high-tolerance floors. This requires highly specialized personnel and the use of compaction rods specially designed for this purpose. In any case, the most common method consists of creating wide or narrow alternative strips, which are poured and finished. After a short curing period, the rest is completed later.
Strength, porosity, bonding and durability of floorings
In addition to the construction characteristics mentioned earlier, warehouse floors must also have other features that make them particularly suitable for their intended use.
Thus, they must be resistant to abrasion, an issue addressed in the UNE 41008 standard, which establishes a scale known as the MOHS that goes from 0 to 10.
They must also withstand compression, and be able to support over 7,112 psi in general areas. Depending on the devices used, they may be required to support up to 11,378 psi on the routes used for the movement of the devices. In terms of requirements for flexural resistance, these tend to be around 2,133 psi to 3,556 psi.
The floor must also be resistant to the effects of elements such as oil, grease, and hydrocarbons. While these materials are not stored in the installation, they are used for the forklifts and there will inevitably be stains on the floor. Allowable porosity must be very low (below 3%).
The flooring must form a monolith together with the support base to prevent slippage and downward movements that cause bumps on the surface.
Finally, the floor must be durable and resistant to wear and tear, although it is inevitable that over time ruts will form from the constant repetitive movements of the wheels of devices along the same routes and given their tremendous weight. These ruts can become very deep and cause misalignments in the facility, with the resulting implicit risks.
Using a company that specializes in flooring for narrow aisle forklifts is, undoubtedly, the best way to ensure a perfect and longest-lasting surface. Skimping in this respect can seriously compromise the entire facility. A very expensive project can be ruined due to savings in one area that appears less important, but which in practice is crucial.