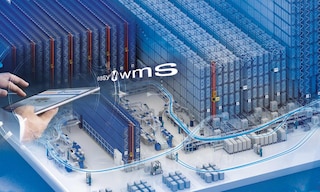
The road to an autonomous supply chain
Is it possible to have an autonomous supply chain in which all links are governed by digitization and automation? The answer is still unknown. But little by little, technological advances — e.g., 5G connectivity, cloud computing, artificial intelligence (AI), and the Industrial IoT (Internet of Things) — are paving the way towards a fully autonomous supply chain. In this scenario, human intervention in stages like process planning, execution, and supervision wouldn’t be necessary.
Autonomous supply chain: present and future
An autonomous supply chain is one capable of automating, digitizing, and robotizing all processes, including product design, operation planning, and shipping and delivery of goods to end customers. Implementing a completely autonomous supply chain calls for processes such as product procurement, performance monitoring, and goods distribution to be performed automatically, with minimal human intervention.
The path to a fully autonomous supply chain is still a futuristic concept, but more and more solutions are becoming available to automate a wide range of processes and enable higher degrees of autonomy in specific supply chain links.
For example, robotic process automation (RPA) automates supply chain management processes: it makes it possible to replicate and fulfill repetitive tasks previously carried out by humans, such as extracting data, filling out forms, performing advanced calculations, and executing multiple procedures without errors. Although RPA offers companies multiple benefits, the autonomy of these software robots is still limited, as they carry out actions based on predefined rules.
One supply chain operation that can be completely automated is logistics planning. According to McKinsey analysts in the publication Launching the journey to autonomous supply chain planning, “practically, autonomous planning enables ongoing, machine-supported decision making in every part of the planning value chain, with planners intervening only to manage exceptions. In other words, the machines do what they do best — crunching data and applying advanced analytics — thus freeing up planners’ time for higher-value activities.”
One of the engines of the autonomous supply chain of the future will be hyperautomation — a term coined by consulting firm Gartner — which combines advanced automation technologies. Hyperautomation consists of integrating technologies such as RPA, AI, machine learning, and big data to implement specific actions in a fully autonomous way with the least possible human intervention.
Applied to the supply chain, hyperautomation fosters the integration of the latest technologies to achieve increasingly higher levels of autonomy. According to Gartner, in the next 10 years, supply chains will be more autonomous: “Hyperautomation will eventually augment humans’ decision-making capabilities and support the creation of an autonomous supply chain. Such a supply chain of the future will be able to automatically plan in real time and run automated operational actions in a frequent, granular, and cost-effective way.”
Characteristics of an autonomous supply chain
Beyond the lack of human involvement, the autonomous supply chain will be:
- Predictive: advanced monitoring of data and of cross-cutting key performance indicators will help predict errors and inefficiencies in work and goods flows. This will also stave off potential bottlenecks along all the stages of the supply chain.
- Intelligent: the autonomous supply chain will rely on the use of new technologies to process data, identify trends, and detect opportunities that will increase the efficiency of the logistics operations taking place inside and outside the facility.
- Scalable: it will be versatile and flexible in response to the changing demands of Supply Chain 4.0. It will be capable of automatically scaling operations up or down to guarantee efficiency in demand peaks and reduce resources in times of lower outbound order volumes.
- Integrated: the autonomous supply chain will drive full digitization of processes to sync all logistics operations between companies involved in the design, manufacture, and marketing of a product. An integrated supply chain promotes complete product traceability, i.e., the monitoring of the life cycle of a good, including design, production, processing, and distribution to end customers.
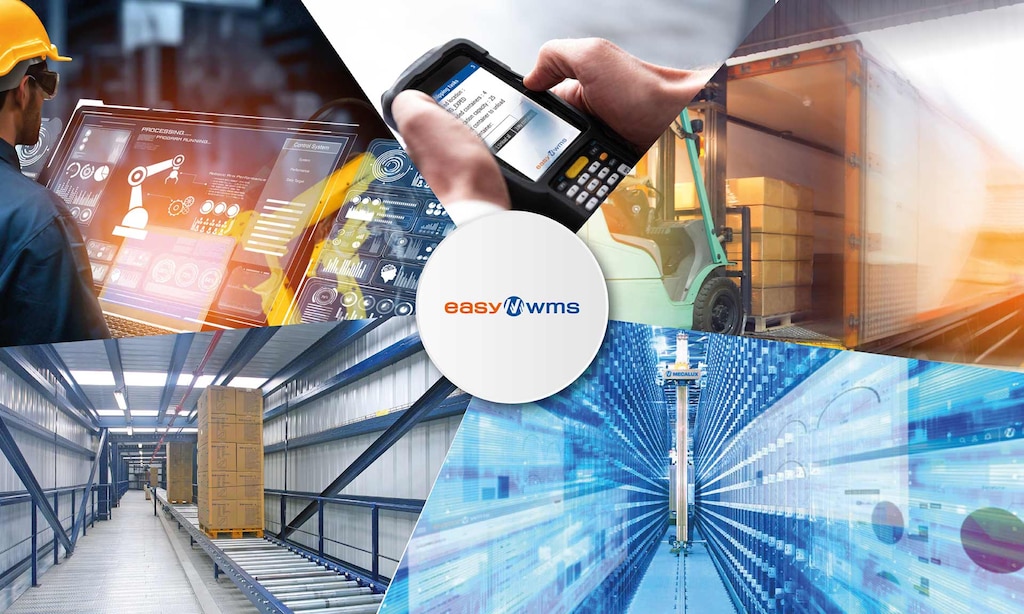
Benefits of an autonomous supply chain
According to a study from the University of Cambridge’s Institute for Manufacturing, “New technologies such as the Internet of Things (IoT) and artificial intelligence (AI) offer the opportunity for companies to transform linear supply chains into autonomous supply chain ecosystems, resulting in more seamless and coordinated operations.” The advantages of having an autonomous supply chain are multiple. Namely, they “can help reduce labour costs and enhance operating efficiency by automating routine tasks of supply chain monitoring,” say the researchers.
Automation and cross-cutting communication among the various links in the supply chain could bring these benefits, to name a few:
- Increased productivity: implementing automated solutions in a warehouse or production center ensures the continuous supply of goods to the production lines or storage area with uninterrupted flows. Extending automation throughout the supply chain would make it possible to automate routine tasks and improve operational efficiency in the different links.
- Error reduction: installing automated solutions based on technologies such as AI and RPA across the entire supply chain would minimize the probability of mistakes in process management and goods handling.
- Enhanced product traceability: controlling a supply chain’s different communication flows in a combined way will ensure end-to-end traceability of stock, because each player will have access to the information stored in the cloud.
- Holistic, customer-focused view: full digitization of supply chain operations will enable all companies involved in the different links to be integrated and have direct, two-way communication, acquiring a holistic view of the process.
The McKinsey report Autonomous supply chain planning for consumer goods companies indicates that “autonomous supply chain planning can lead to an increase in revenue of up to 4 percent, a reduction in inventory of up to 20 percent, and a decrease in supply chain costs of up to 10 percent.”
Software for an autonomous supply chain
Digital process transformation must be the cornerstone of a fully autonomous supply chain. Today, there are already multiple digital solutions that ramp up warehouse throughput and enable automated process management, such as warehouse management and distributed order management software. Digitizing operations makes it possible to establish a real-time, accurate data connection between the different links in the supply chain.
Autonomous decision-making will be one of the pillars of the supply chain of the future. In this regard, advanced software will enable companies to predict scenarios, anticipate changes in demand, and vary the logistics strategies in their warehouses in line with their needs. Collaboration between digital programs enables a holistic view of the supply chain, as McKinsey points out in its study: “Advanced analytics throughout the supply chain, moving beyond standard software functionality for individual processes, [makes it possible] to create an explicit link from demand forecasts and orders back through to the production schedule and plan.”
Digital management is increasingly common in warehouses that need to boost throughput, eliminate errors, and reduce logistics costs. In this vein, the implementation of a warehouse management system (WMS) will be a key part of an autonomous supply chain, characterized by the integration of all players involved in logistics processes.
Digitization allows the warehouse management software to connect with the other programs run in the different stages of the supply chain, whether belonging to the company or to another organization. The objective is to improve the exchange of information and automate tasks, fostering advanced levels of product traceability and more efficient operations.
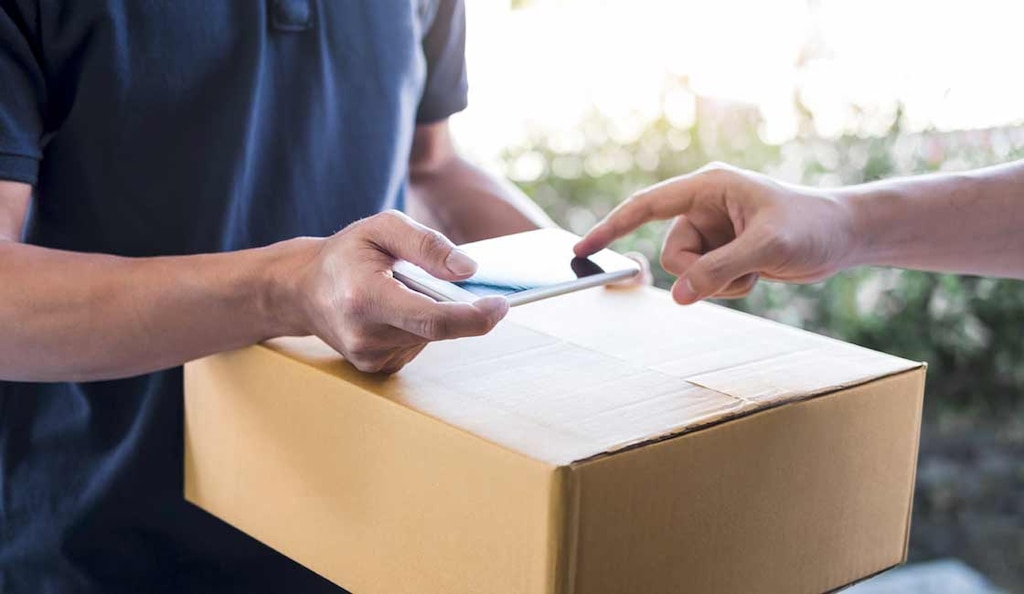
Autonomous supply chain: a new paradigm
Nowadays, there are already a large number of digital and automated solutions transforming the industrial world and limiting human intervention in logistics and production processes. But we still have a long way to go before achieving a fully autonomous supply chain.
In this new industrial paradigm, technologies such as the IoT, machine learning, and cloud computing will play a key role. Digital programs such as warehouse management software will help to transform the supply chain, eliminating the risk of error linked to manual management.
The future of the supply chain will depend on technology advances and companies’ capacity to integrate the latest technologies in their processes to drive autonomy in operations and decision-making.