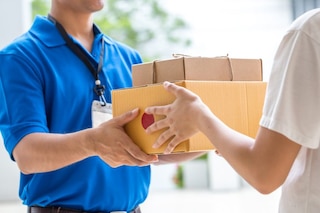
Logistics planning: how to implement it with flying colors
Properly structured logistics planning is fundamental for optimizing all operations involved in the warehouse. And the incorporation of strategies specially devised for each particular case actually reduces inefficiencies and multiplies productivity.
But how is this successfully implemented in an organization? In this article, we analyze which aspects to take into account when designing logistics planning and what the deployment process should look like.
What’s logistics planning? Definition and purpose
Logistics planning consists of an action plan agreed upon by all stakeholders that establishes a company’s logistics objectives. It ranges from the procurement of the raw materials necessary for manufacturing the product to the management of shipments to customers. For example, the players involved arrange the terms of delivery to the end customer, the loading docks to be assigned to a shipment, etc.
This plan also sets out the key performance indicators (KPIs) to be measured, as well as their parameters, in order to assess the company’s logistics performance. These data also serve to identify inefficiencies and errors to be remedied throughout the product’s supply chain.
Lastly, logistics planning determines the methods and regularity with which operations are evaluated. The aim is to prepare a continuous improvement plan that multiplies productivity in the installation.
When developing the planning, it’s important not to lose sight of your main objectives, namely:
- Reduction in errors and inefficiencies: planning facilitates control over information in all logistics phases, drastically minimizing mistakes in the warehouse.
- Optimization of resources and investment: monitoring the company’s logistics systems in real time allows managers to make decisions related to movement flows in the warehouse. As a result, it’s easier to leverage the resources available to the logistics manager.
- Increased productivity and efficiency: the end goal of all logistics planning is to ramp up throughput in the installation, boosting the productivity and efficiency of each operation.
Planning all the stages of logistics activities
It’s essential for planning to include the four key stages of any logistics operation:
- Procurement of raw materials
- Production
- Inventory control
- Goods distribution
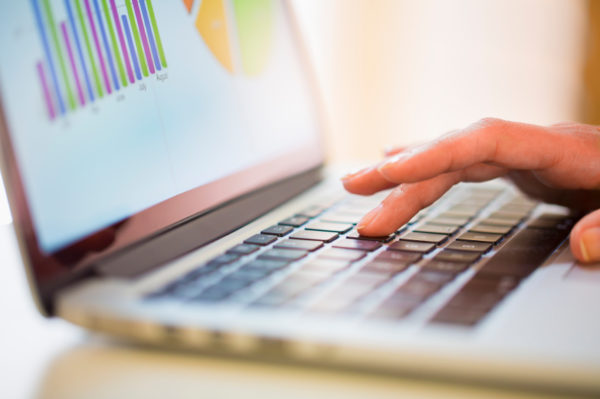
Nevertheless, planning also includes aspects taking place prior to the logistics process, such as warehouse design and management of warehouse slotting, taking into account operator workflows and goods inflows and outflows.
Likewise, planning covers elements subsequent to the delivery to the end customer. An example of this is reverse logistics: the business needs to have a strategy for minimizing the impact of this consumer trend, which already accounts for over $50 billion a year in the US, according to a study from the Reverse Logistics Association.
Good logistics planning: how to do it
The secret to good logistics planning is to analyze your supply chain down to the last detail to identify all obstacles in each logistics phase and devise the best way to overcome them.
Consequently, the strategy should take into account, for example, your end customers (and their delivery demands), your suppliers and their lead time, and even the intrinsic characteristics of the product.
Additionally, all logistics planning should:
- Be designed for growth: the company’s strategy should consider the possible expansion of the storage installations and production lines and the potential increase in demand. One criterion that can facilitate this next step is flexibility in warehouse design.
- Employ appropriate metrics: the supply chain generates an endless stream of information that, when properly analyzed, is extremely useful. However, it can also lead to inefficiencies in the installation. Thus, understanding the product and defining the right KPIs is vital for logistics planning to be successful.
- Innovate constantly: although the business should have clear targets in place, it must continuously seek out new methods that enhance the efficiency of its logistics operations. From this perspective, the incorporation of new technologies in storage facilities has become an invaluable asset for responding to the challenges of omnichannel retail and same-day deliveries.
Staff and goods flows and warehouse organization are other elements that should be integrated in a good logistics planning strategy. But the list of aspects to be included doesn’t end here. Handling equipment such as stacker cranes, storage systems such as the Pallet Shuttle, and automatic elements that ensure efficiency in picking such as pick-to-light systems will make the difference between good planning and no planning.
On the other hand, in recent years, the incorporation of warehouse management systems (WMSs) has become especially relevant, as they collect the information generated in the installation and automate such complex phases as stock control, warehouse shipping and receiving, and order picking.
Logistics planning for warehouse efficiency
All businesses, regardless of their sector, perform a role in the supply chain. Underestimating the importance of this stage in the business can lead to cost overruns, mistakes, and inefficiencies in service provided to the end customer.
An excellent example of logistics planning is seen in Belgian textbook rental company Rent a Book: Due to inefficient order prep ― reverse logistics accounted for up to 3% of its final shipments ― this firm designed a plan based on digitizing its processes and automating picking with RFID technology. Another case illustrating logistics planning is KH Lloreda. Faced with increased demand, it came up with a logistics strategy that consisted of automating its warehouse to improve its customer service.
In the end, in any organization, all departments have to work in sync and focus on the overall goal of logistics: to ensure that the goods arrive at right time, in the agreed-upon conditions, and at the lowest possible cost.