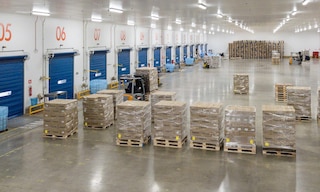
Consolidation and deconsolidation cross-docking: what are they?
Consolidation and deconsolidation cross-docking are order fulfillment processes that fall under the cross-docking goods distribution strategy, whereby products are dispatched directly without being stored beforehand.
In cross-docking, operations aren’t usually performed on the products received. However, in consolidation and deconsolidation cross-docking, shipments either need to be set aside temporarily or broken down and then merged into new unit loads before being sent to customers.
What are consolidation and deconsolidation cross-docking?
In the literal sense, the term cross-docking refers to moving shipments from one warehouse dock to another. This logistics procedure consists of dispatching goods that arrive at the facility without having to handle or store them previously.
Nevertheless, with consolidation and deconsolidation cross-docking, products are handled in the warehouse to a certain extent. Let’s take a closer look at these two order fulfillment strategies:
- Consolidation cross-docking: with this method, the logistics facility receives several smaller unit loads separately from one or more suppliers or production centers. They are set aside temporarily and then consolidated into a single, larger shipment to optimize costs.
- Deconsolidation cross-docking: this is just the opposite of consolidation cross-docking. The warehouse receives full shipments from one or more suppliers or production centers. They are then broken down and relabeled. Following this process, the products are deposited in new unit loads and moved to the loading docks to be consolidated on the various transportation vehicles.
With these cross-docking modalities, distribution centers (DCs) often serve as hubs for order processing: the company’s suppliers or production centers send the goods to the DC, which receives them, fragments them (or groups them together with other orders), and puts them into new unit loads. DCs are designed for this function: they have a large number of loading docks and an open space that acts as a buffer, facilitating continuous goods flows and optimizing time and logistics costs.
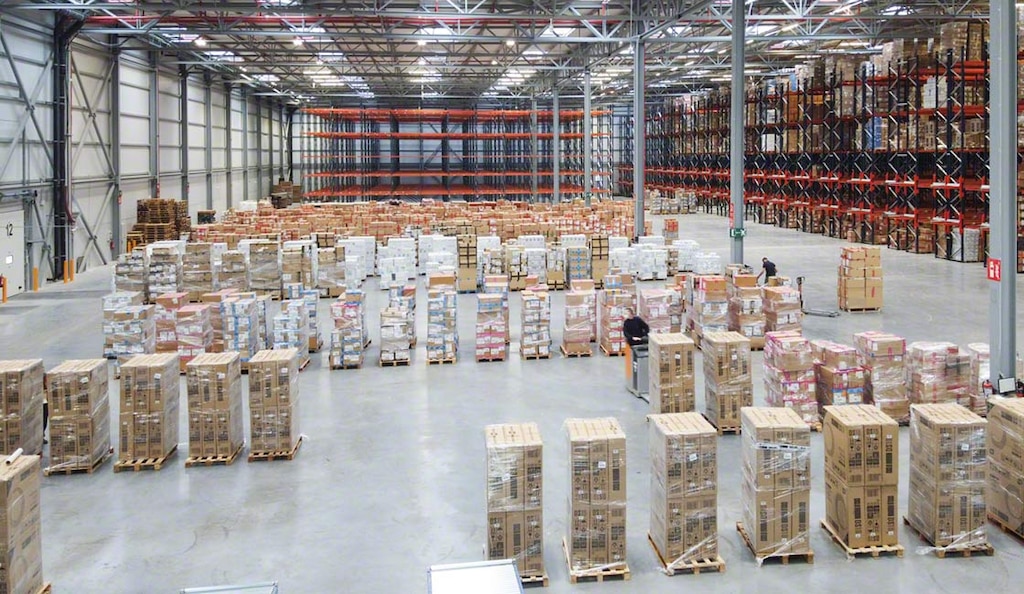
Benefits of consolidation and deconsolidation cross-docking
Cross-docking is becoming increasingly popular in logistics because of the advantages it has for warehouses and DCs:
- Reduced delivery times to customers.
- Elimination of goods handling costs.
- Optimization of storage overhead.
- Speedy product dispatch.
- Better compliance with deadlines agreed upon with customers.
Differences between consolidation, deconsolidation, and continuous cross-docking
Cross-docking can be differentiated according to the level of product handling involved. In continuous cross-docking, goods handling is minimal: loads are merely moved from an inbound dock to an outbound one. With consolidation and deconsolidation cross-docking, on the other hand, the products are handled prior to being dispatched to customers.
Meanwhile, there are other cases where cross-docking is combined with another order fulfillment strategy: in hybrid cross-docking, products are received at the docks — without being stored — and are put together with other goods from the storage systems.
The choice between one type of cross-docking or another will depend on factors such as:
- Quantity of SKUs in the warehouse.
- Number of suppliers and customers.
- Order distribution strategy.
- Type of goods, sizes, and volume managed.
- Product delivery windows to customers.
Deconsolidation cross-docking, which is widely used in the food industry to supply large shopping centers, calls for the goods to be separated and then picked before being dispatched to their final destination.
Software for consolidation and deconsolidation cross-docking
Cross-docking is an ideal solution for shortening product storage and delivery times. However, managing this strategy manually could lead to errors, especially in e-commerce, retail, and food warehouses, where multiple SKUs are processed.
The solution for achieving effective consolidation and deconsolidation cross-docking processes lies in swapping manual warehouse management for digital logistics. Implementing a warehouse management system (WMS) lets you coordinate all operations taking place in your facility, from goods receipt to dispatch and including complex phases such as order picking.
An advanced software program like the one from Interlake Mecalux has functionalities for employing cross-docking. The WMS coordinates all the equipment and workstations to optimize movements of products from the inbound loading docks to the outbound ones without the need to store the goods on the racks.
In addition, this software coordinates the different RF scanners and organizes the actions of the operators to make cross-docking a productive, agile, and error-free process. In the particular case of consolidation and deconsolidation cross-docking, the software plans operations, optimizing the movements of the operators, the loads, and the handling equipment to make consolidation and deconsolidation as efficient as possible.
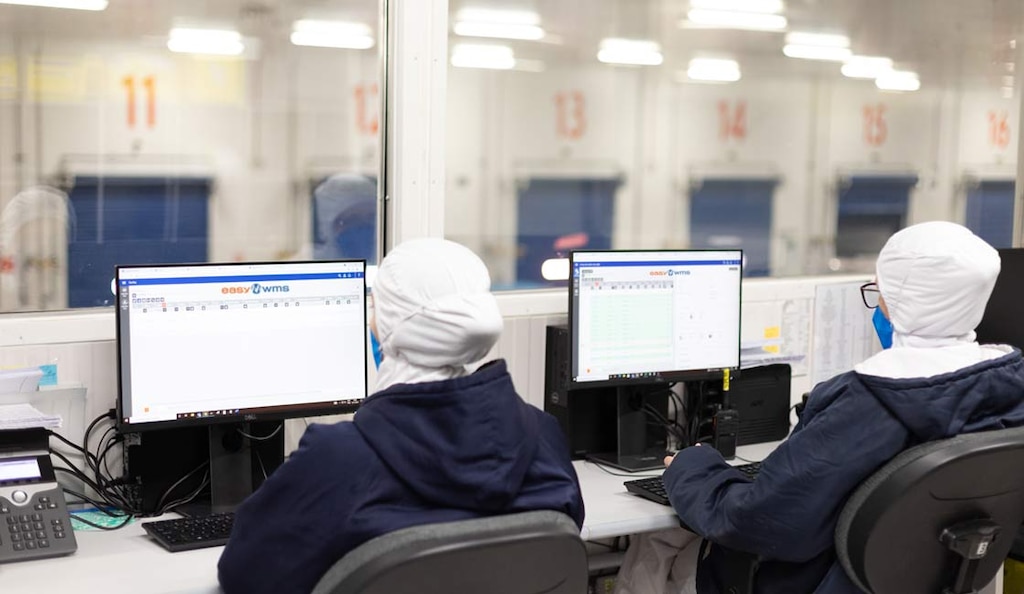
(De)consolidation cross-docking: skip the storage phase
Consolidation and deconsolidation cross-docking increase the complexity of inventory control and goods dispatch: logistics managers not only have to know the availability of the products but also place them in different unit loads without previously storing them.
Therefore, implementing a WMS is key for ensuring agile, effective, and error-free cross-docking. Want to find out more about how our software can benefit you? Be sure to contact us. One of our expert consultants will advise you on the best digital solution for your company.