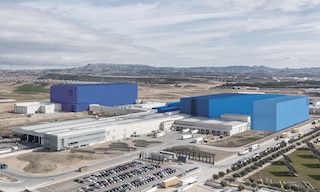
Industrial warehouses and their management
The storage of products and raw materials is a fundamental stage within the supply chain. As such, industries require specific buildings and facilities to carry out their activities. In addition to these spaces, companies should take into account certain aspects and tools to enhance their overall efficiency.
What are industrial warehouses?
Industrial warehouses are buildings or facilities where various processes take place, from manufacturing to the putaway of finished goods. Thus, industrial warehouses can accommodate nearly an entire production chain. Although these spaces house products and raw materials, they shouldn’t be confused with logistics centers, which are dedicated solely to order distribution.
There are several models of industrial warehouses, but generally, they can consist of manufacturing, storage, inbound, and outbound zones; yards; and even exhibition and sales areas. They can be conventional or automated, with machinery, goods, and operators inside them.
What are the uses of industrial warehouses?
These facilities are the backbone of companies’ activities. They house logistics processes such as goods receipt, management, internal transport, handling, conditioning, and storage. Optimizing space utilization and the internal organization of these warehouses will significantly impact business performance.
- Storage. This deals primarily with accommodating raw materials, semi-finished products, and finished goods in a controlled, systematic, and safe manner. Storage can be short-, medium-, or long-term.
- Material handling. This involves everything related to loading, unloading, order picking, and transfer operations, among others. Being equipped with a warehouse management system (WMS) facilitates stock control and ensures real-time traceability.
- Order consolidation. This consists of organizing and classifying items prior to shipment. The aim is to reduce transportation costs, achieve full vehicle loads, and expedite product delivery.
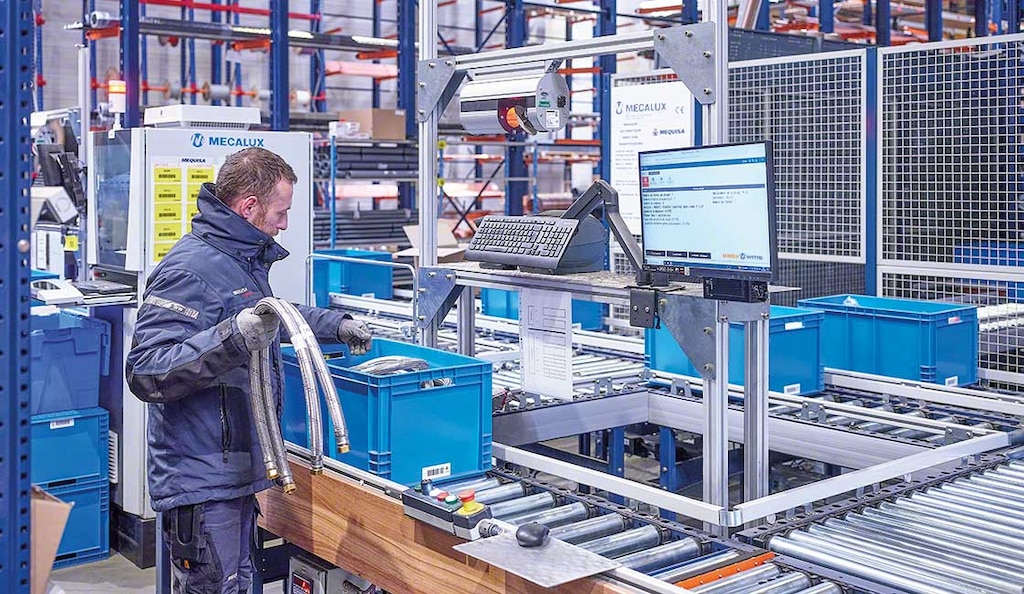
Types of industrial warehouses
These buildings — essential for any industry — can be divided into different categories:
According to characteristics
- Outdoor industrial warehouses. These are contracted by third parties, often by multiple enterprises simultaneously. They can be geared towards national or international transportation depending on the nature of their clients’ businesses and typically contain a wide array of industrial items. They are usually equipped with security measures and management systems to optimize operations, speed up process times, and control product turnover.
- Indoor industrial warehouses. These form part of the company’s own distribution channels. They can be modernized to reach their maximum potential.
- Industrial depots. These structures, often larger than other industrial spaces, house manufacturing machinery, transportation vehicles, merchandise, and large items.
By good type
- For raw materials. Industrial warehouses can be used to store all the inputs required to manufacture goods.
- For semi-finished products. These buildings can also accommodate materials that have been manipulated previously but are still in an intermediate stage of the manufacturing process.
- For finished goods. Following the completion of production, industrial warehouses store finished products ready for distribution and sale. These items remain in the facility until they’re requested as part of an order or for placement at a point of sale.
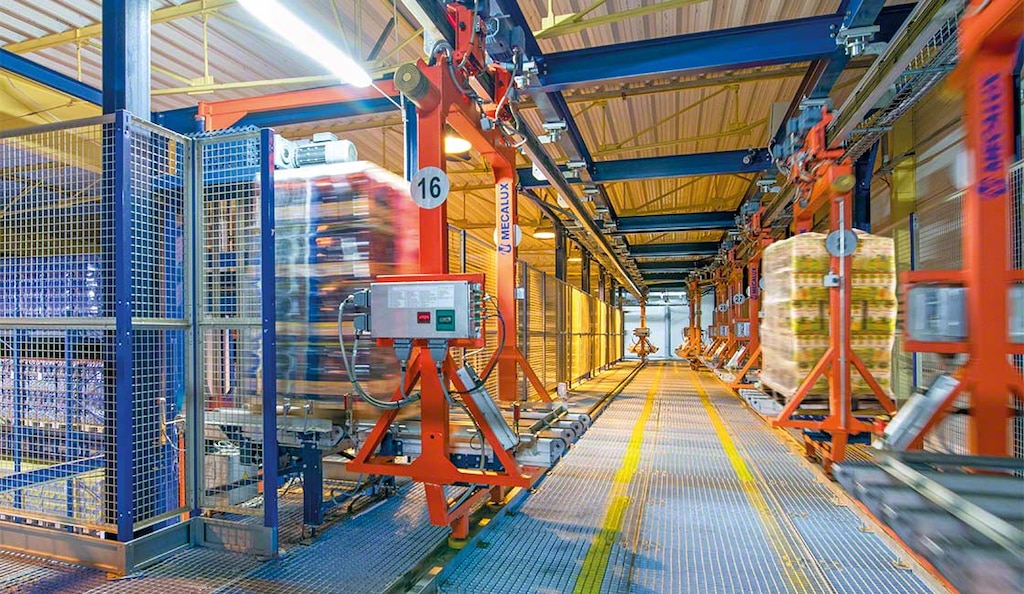
Tips
Here are four tips to keep in mind for the effective operation of industrial warehouses:
- Analyze your needs in advance. Depending on the characteristics of your goods, one storage system may be more suitable than another. You need to know your product details beforehand: their state (solid, liquid, or gaseous); how they’re packaged (drums, barrels, or pallets); their dimensions, volume, and weight; and if they’re sensitive to external factors such as light, humidity, or vibrations. Knowing this information will enable you to design your warehouse layout accordingly.
- Label your racking and shelving. This can range from simple numerical identifiers or tags to automated systems with barcodes read by RF scanners or robots. These rack accessories are sometimes overlooked, but they’re crucial for making operations more agile.
- Invest in routine maintenance services. Even if you seek advice and end up purchasing one of the top storage solutions on the market, all systems must be inspected periodically to prevent malfunctions. It’s advisable to consult with companies that offer racking inspection services.
- Review your processes regularly. Storage management that delivers excellent results during one season may not be suitable for another period or campaign. Be sure to monitor the operation of your industrial warehouse from time to time to identify areas for improvement.
Management system for industrial warehouses
Industrial warehouses are a core element in the supply chain. Therefore, to maintain a competitive edge, it’s critical to make sure they run like clockwork. To this end, it could be in your best interests to automate the areas most frequently used in these facilities and manage inventory, inflows, and outflows with a software program like Easy WMS.
Are you in need of logistics consulting for your warehouse? Or are you considering building one from scratch? Be sure to contact us. We provide guidance from the start, accompanying you throughout the project. We’ll tailor our services to match your needs. And once the project is completed, we’ll offer ongoing support to ensure the success of your operations, as we do every day with other satisfied clients.