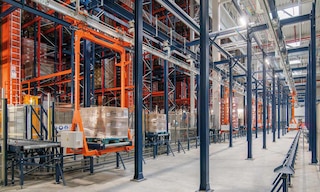
Warehouse optimization and its advantages
Warehouse optimization is essential for companies that want to provide top-notch customer service and continue expanding their operations as orders and product SKUs increase.
What is warehouse optimization?
Warehouse optimization is the process of improving operations, material flows, and productivity in logistics facilities such as distribution centers (DCs). Warehouse optimization tactics aim to reduce costs, maximize performance, and, ultimately, provide a first-rate customer experience.
Companies can achieve this transformation by designing and automating their facilities in collaboration with experts, overhauling processes, and training employees. Focus should be placed on aspects such as receiving, location management, packaging, shipping, and returns, i.e. reverse logistics.
Why optimize your warehouse?
Although often out of the public eye, the warehouse is the central hub for many businesses, especially those in sectors like ecommerce. Prioritizing warehouse efficiency helps ensure timely deliveries, creates a productive work environment, and maximizes profits. These are the three major benefits of warehouse optimization:
- Increased productivity. Reviewing each step of the goods flow (from receipt to shipment) boosts efficiency while shortening lead times. This allows businesses to handle higher volumes.
- Improved customer satisfaction. A warehouse in tip-top shape tells consumers that they can trust the company, as deliveries are made on time and as expected. In contrast, shipping errors and delivery issues will tarnish the organization’s reputation.
- Cost-effectiveness. The faster goods can be moved without sacrificing operational excellence, the greater the facility’s revenue potential. Similarly, investing in warehouse optimization techniques like automation can further enhance results.
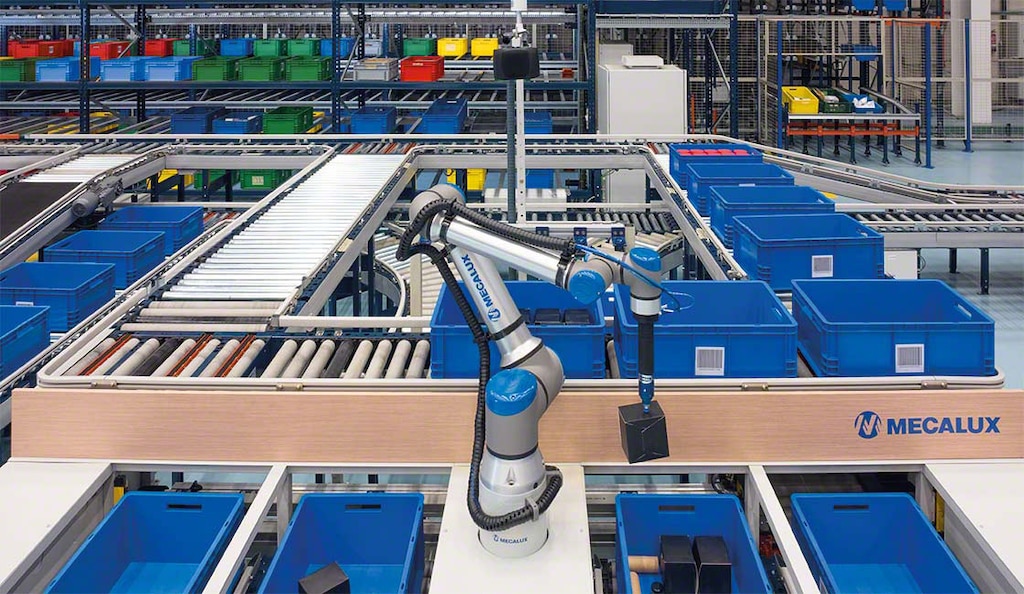
Benefits of warehouse optimization
In optimizing a facility, the first steps typically involve physically revamping the workspace and modifying operations by implementing a warehouse management system (WMS). Following these processes, the advantages of warehouse optimization become clear:
- Better inventory management. Although tracking SKUs manually is feasible in small spaces, it increases the chance of error. Moreover, this task becomes much more complex when dealing with hundreds, thousands, or tens of thousands of SKUs. WMSs track inventory levels in real time, preventing overstocking and stockouts. They also facilitate more accurate demand forecasting.
- Greater picking accuracy. RFID devices and RF scanners help associates fulfill orders correctly, resulting in fewer returns.
- Effective kitting and assembly. Warehouse optimization makes it easier to partially assemble products before shipment and combine several SKUs in one package for bundle sales. When executed correctly, these services can increase average order values. However, without properly established workflows, error rates will rise.
- Fast shipping and receiving. Delays in unloading, inspecting, and storing items can cause bottlenecks and lead to missed sales opportunities. Being expeditious, on the other hand, gives companies a competitive edge.
- Agile returns. Effective reverse logistics management can help retain customers. Analyzing and studying information related to these operations provides valuable insights into product quality and consumer preferences.
How to implement a warehouse optimization plan
When changing your facility’s workflow, it’s important to take a good look at areas for improvement and the zones most likely to experience delays. Be sure to gather feedback from the associates who perform tasks daily and apply genchi genbutsu (“go and see for yourself”) to observe processes on-site. You’ll also want to seek the advice of storage experts specializing in inventory and warehouse optimization strategies.
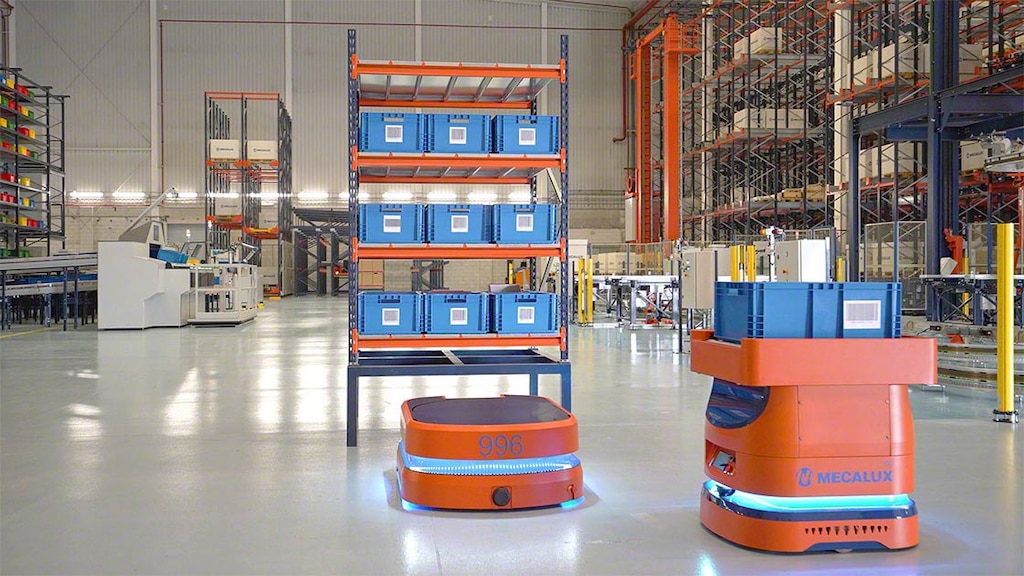
Warehouse optimization trends to follow
Businesses looking to stay ahead of the curve on agility and customer service are implementing the latest inventory management technologies. These are some of the trends transforming warehouses and distribution centers:
- Automation. Elements like picking robots help move products through DCs more efficiently, whether independently or in collaboration with humans.
- Industrial Internet of Things (IIoT). Intelligent devices are becoming increasingly prevalent in these workplaces. They make it possible to collect data on SKUs and track the location of robotic elements like autonomous mobile robots (AMRs).
- Visibility. Digital twins simulate warehouses and supply chains, providing valuable information for planning operations.
Warehouse optimization case studies
Numerous real-world examples of warehouse optimization illustrate how companies can improve their operations by tweaking certain aspects of their facilities. Here are some examples:
- DHL. The logistics and express mail service provider operates a center in Madrid that leverages every square inch. The space houses over 90,000 pallets and features more than 98,000 feet of hanging garment profiles. This setup enables fast service to the stores of DHL’s main client in the Iberian Peninsula.
- Spartoo. Europe’s leading online shoe retailer operates a 5.68-acre warehouse in Saint Quentin Fallavier (France). Thanks to warehouse optimization, this example of ecommerce logistics can manage 2.2 million units and ship over three million pairs of shoes annually.
Optimize your warehouse with Interlake Mecalux
At Interlake Mecalux, we specialize in warehouse automation and management with our Easy WMS software. This successful solution runs the logistics operations of over 1,100 facilities in 36 countries, maximizing companies’ supply chain efficiency. Similarly, our Easy DOM system provides visibility into large distribution networks. Contact us to benefit from our extensive intralogistics experience, built over decades since 1966.