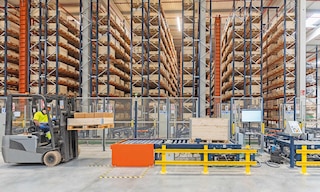
Putaway in warehousing: Types and best practices
To achieve successful logistics operations, managing inventory and determining its placement in the warehouse are just as critical — if not more so — as packaging or final transportation.
What is putaway in a warehouse?
Putaway refers to the operations involved in receiving goods from suppliers or production and storing them on racks for future picking and shipment. This process is essential for maintaining a well-stocked, easily accessible inventory. Effective putaway can mean the difference between optimized product retrieval times and inefficiency that could pose safety risks for operators.
Putaway applications in logistics
Putaway is closely linked to spaces such as warehouses and distribution centers (DCs). While each facility follows a different workflow, all rely on systems that determine how goods should be stored before shipment, even if they spend minimal time on-site due to cross-docking operations. Putaway also comes into play when previously delivered items return as part of reverse logistics processes.
When organizing inventory management, locations can be assigned according to different criteria such as demand level, size, weight, or available storage space. Tracking all of these positions manually can be challenging. However, a warehouse management system like Easy WMS enables intelligent slotting, task sequencing, and automation of information flows, minimizing the risk of errors.
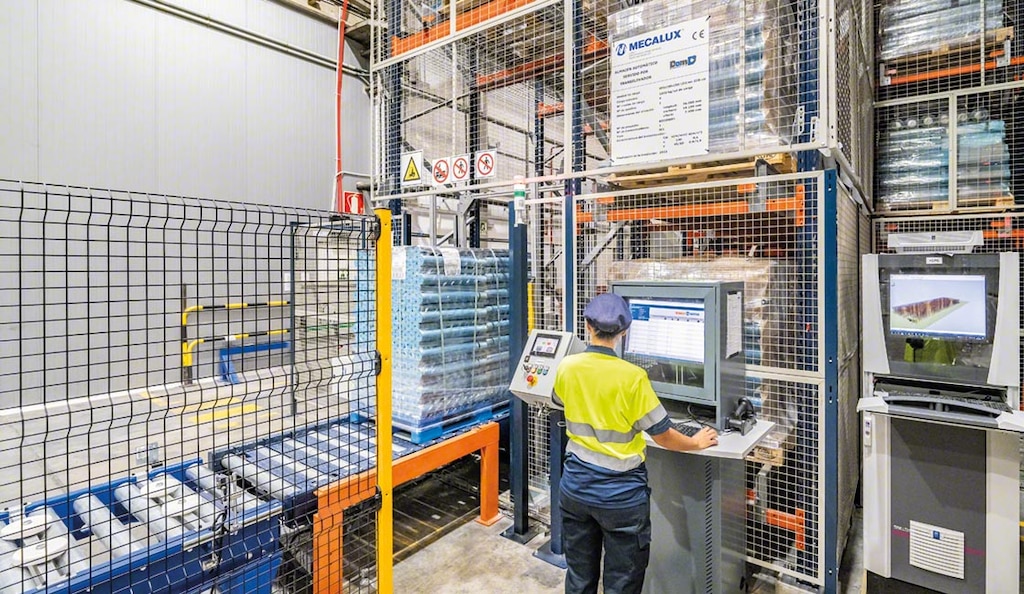
Benefits of effective putaway
Implementing a structured warehouse putaway process instead of placing goods in the first available space without a clear strategy provides multiple advantages:
- Easy SKU tracking and improved distribution of products stored in the warehouse.
- Less inventory shrinkage by preventing unnoticed losses or theft.
- Control and traceability of any discrepancies when every SKU is accounted for.
- More efficient picking by placing best-selling items closer to pickers.
- Faster deliveries due to optimized warehouse processes, which positively impact the rest of the supply chain.
- Reduced space usage and inventory maintenance costs, making it possible to accommodate more valuable products or raw materials. Better organization also contributes to a tidy workplace.
- More accurate putaway and easier item location through the use of a WMS.
Types of putaway in a warehouse
An effective putaway strategy helps avoid stockouts and, conversely, overstock, while boosting warehouse efficiency. It can focus on the characteristics of the materials or products handled, such as their weight, quantities, size, and other specific factors relevant to each industry. These are the four most common types of putaway:
Based on available space | Based on putaway rules |
Direct putaway. Instead of storing goods temporarily upon arrival, they’re immediately transported to their final location within the warehouse or processed for shipment. Direct putaway is typically performed in small-to-medium-sized facilities with an average number of locations and products. |
Fixed-location putaway. Warehouses following this method assign permanent spaces to each product. A key advantage of this system is its ability to minimize the chance of error. It’s especially useful for items like frozen foods, which require controlled temperatures, or heavy items that need to be stored on lower shelves. |
Indirect putaway (staging). Before being placed in their long-term locations, products are temporarily stored in a designated staging area. In this space, they may undergo additional processes (e.g., labeling) before being assigned a final location. | Random putaway (chaotic storage). According to this method, items don’t have predetermined locations — they’re placed in any available space as they arrive. This makes locating items more challenging, so deploying a WMS is highly recommended when adopting this strategy. |
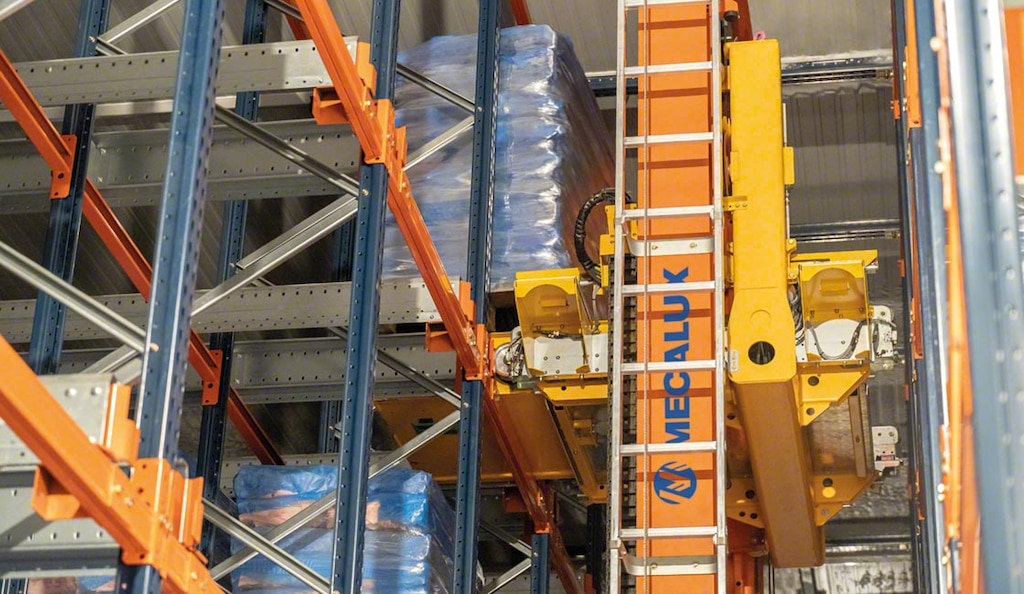
Best practices to optimize warehouse putaway
In addition to understanding the different types of putaway, it’s advisable to consider these tips before deciding on a method for putting away inventory:
- Implement barcode and RFID technology to track products, shortening search times and making the facility more efficient.
- Automate repetitive tasks to eliminate the chance of error and allow associates to focus on higher-value activities.
- Leverage dedicated warehouse management software like Easy WMS to significantly enhance product control and traceability.
- Establish clear protocols to ensure that goods receipt and return processes are carried out optimally without missing any steps.
- Regularly review processes and apply principles like genchi genbutsu to identify areas for improvement.
Optimize putaway with Interlake Mecalux
Are you looking to streamline your operations with the support of an innovative team, a cutting-edge WMS, and the latest automation technologies? Interlake Mecalux is here to help. With over 55 years of experience designing intralogistics systems, we know how to optimize our clients’ capabilities. Contact us today, and we’ll offer you the most effective storage solutions to take your company’s logistics operations to the next level.