Some products are not subject to physical limitations for handling purposes (such as items supplied in bulk), and can therefore be grouped into a wide variety of load units of all sizes. As a result, their handling costs are lower.
Given that one of the main objectives when it comes to managing goods is to limit the number of movements to an absolute minimum, it is convenient and desirable to generate the largest load unit possible.
The problem that can arise is that while these products are often produced on a mass scale or in large batches and are supplied in the largest load units that can be handled, their distribution may be subject to different needs when it comes to the most appropriate size of the loads.
There is no doubt that in the vast majority of cases, handling large loads makes storage easier. However, it is common for products that entered a warehouse in a specific load size to leave it in much smaller units.
One way of combining both criteria is to generate a small load unit, one that can be handled individually but which is also suitable for being handled once grouped, thereby reducing costs.
In view of these issues, all elements in a materials handling system must be considered as a whole. Therefore, the first step is to analyze the strength and stability of the loads in more detail.
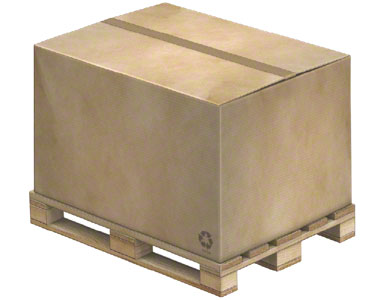
Pallet
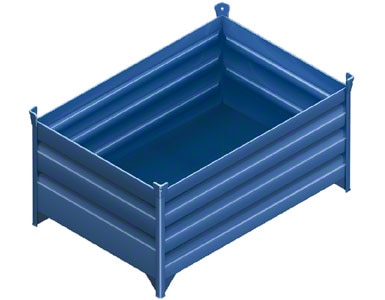
Container
Pallets and containers: general issues
When it comes to load units, one of the fundamental issues is what in many cases constitutes the support structure where items to be stored are grouped.
Support structures consisting of a platform onto which the goods are deposited are called pallets, while recipients or packages into which the load is placed are called containers. Both are auxiliary equipment used to create, move, and store load units and products.
It is essential to pay particular attention to these elements, since their shapes, dimensions, and strengths and the materials used to manufacture them are not always suitable for all different storage systems, or may require complementary tools or accessories to help position them on racking units. Furthermore, their characteristics also affect the handling equipment and methods used.
This article reviews the most common types of pallets and containers. However, when planning the facility, there are specific models the details of which it is necessary to know in advance, such as their shape, dimensions, materials, etc.
The building, quality and size of the pallets and containers, as well as the load dimensions, its stackability, etc. are factors that directly influence what is proposed in a warehouse solution project.
Correctly assessing the data corresponding to the load unit, in this case pallets and containers, is essential to put together the best warehouse fulfillment solution that meets the concrete needs of the customer on any level and that makes it run smoothly.