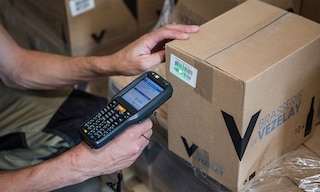
Case picking to speed up order fulfillment
When it comes to fulfilling orders in warehouses and distribution centers (DCs), there are several ways you can store and retrieve goods. The standard method for this is picking, and depending on your needs, one type you can employ is case picking.
What is case picking in the warehouse?
Case picking is a picking method whereby operators remove an entire case or carton instead of a single product unit. These boxes can be retrieved from picking shelves, mini-load automated storage and retrieval systems (AS/RSs), pallets, and conveyors. In the context of picking operations, a case contains a large number of items of the same SKU. Manufacturers pack them so that each product takes up minimal space, keeping down transportation and storage costs.
Case picking is used extensively in DCs that serve retailers. It’s perfect for moving large volumes of SKUs at a moderate-to-rapid pace. You can put full case picking into practice in several ways. Operators often retrieve cartons of high-turnover products directly from pallets. Meanwhile, they pick low-turnover products directly from cases on picking shelves.
Where is case picking used?
This technique is generally applied in DCs catering to retail or ecommerce businesses. 3PL (third-party logistics) providers and suppliers of department stores typically devote a section of their warehouses to case picking. These are some industries that use this method:
- Automotive
- Food & beverage
- Consumer goods
- Ecommerce
- Electronics
- Pharma & healthcare
- Large-scale retail
- Logistics & 3PL
- Wholesale
- Retail
- Fashion
Sometimes, cases are sent to retail stores or shopping centers, where workers place individual items on shelves. Businesses that function as wholesalers, on the other hand, sell boxes directly to end consumers.
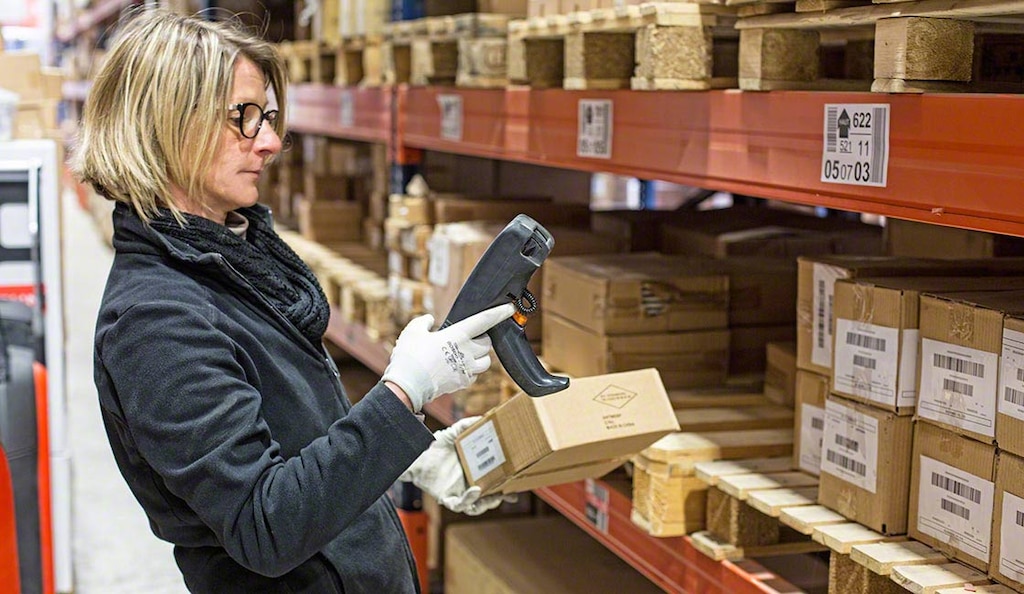
Advantages of case picking in warehousing
Although case picking forces you to reserve a certain amount of space for this task, this method has several benefits compared to conventional picking, particularly in these situations:
- Using the entire box as a single item prevents picking errors and improves fulfillment accuracy. This will have a positive impact on the customer experience.
- Case picking maintains better control over inventory and reduces material handling compared to piece picking. The result is less travel through the facility and greater productivity.
- This picking method moves products more quickly and efficiently from receipt to shipment, especially in the case of best-selling SKUs.
- Box picking simplifies packing since cartons are easily organized and loaded onto pallets or in containers.
- This technique decreases the use of packaging and generates less waste.
How can case picking optimize operations?
One way to boost logistics operations with case picking is to implement the most suitable storage solution for each item:
- Carton flow racks. Also known as carton live storage, these racks comprise slightly inclined roller platforms that support the goods. When a product is picked, the ones behind it slide by gravity towards the pick face. This option is very helpful for offloading high-demand merchandise.
- Multi-tier shelving. These structures are formed by tall shelves and one or more walkways. They’re an excellent choice for high-intensity order picking, as you can assign warehouse pickers to a particular floor. Multi-tier shelving is used in ecommerce, warehouses for hanging garments, parcel services, industrial supply storage, and archival facilities.
- Warehouse management system (WMS). Employing a software program to oversee automated and/or manual operations can significantly enhance case picking. Interlake Mecalux’s Easy WMS, for example, provides full inventory traceability, optimizes pick paths, and streamlines processes.
- Flow channels for picking. It’s possible to install flow channels on the lower levels of pallet racks. This way, your WMS can instruct the channels to be replenished with pallets, and operators can pick cases directly from them.
- AS/RSs for boxes. Mini-load systems and box conveyors can transport cases to picking operators in line with the goods-to-person method.
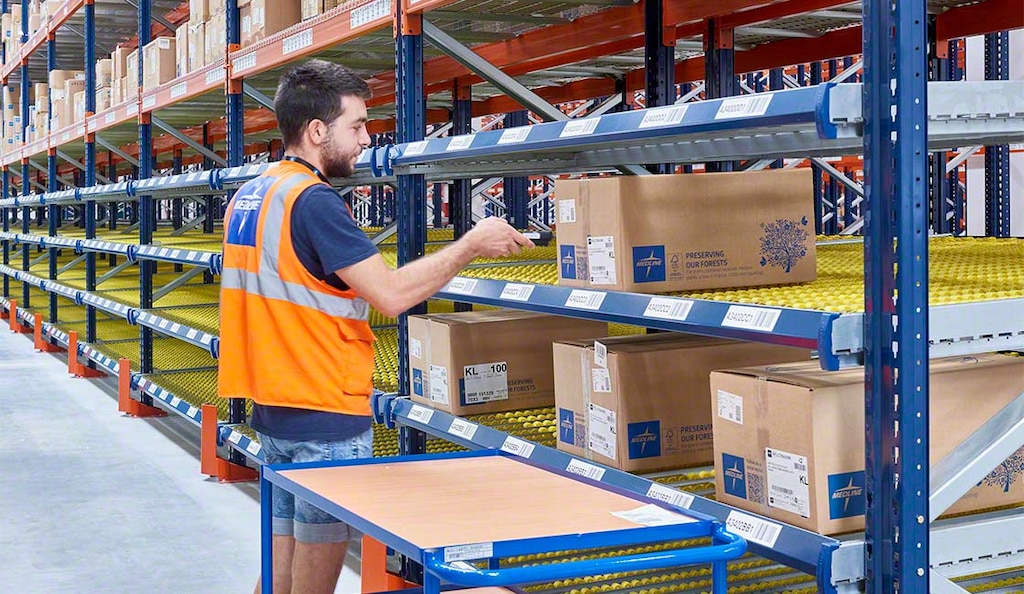
Another option would be to redesign your layout to have pick paths coincide with case picking areas. When implementing these solutions, it’s important to ensure that workstations are ergonomic. This will directly impact operators’ well-being in addition to the number of picks per hour. To pick products from very low positions, it’s a good idea to use hydraulic tables or autonomous mobile robots (AMRs), which lift boxes and facilitate their movement. For instance, AMRs can act as case picking robots, transporting cartons, trays, and packages. In contrast, to reach considerable heights, it’s best to rely on stacker cranes and AS/RSs for automated case picking.
Get your warehouse ready for case picking
Before opting for individual or case picking, you should have an expert assess key factors such as SKU demand, order lines to fill per hour, distribution channel, shipping and pickup times, and return on investment.
If you’re thinking about implementing case picking in your warehouse or optimizing your current operations, we’re here to help. The Mecalux Group develops warehouse automation and management solutions that drive efficiency in all types of logistics centers. We also manufacture our own robots and racking systems. Thanks to the experience we’ve gained since 1966 in projects around the world, we’re specialists in streamlining processes and facilities. Get in touch for your personalized advice.