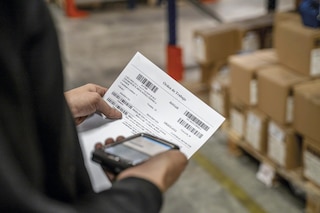
Internal traceability = quality and safety in the warehouse
Relying on an internal traceability system is essential in every installation nowadays. The safety and quality of the goods are factors increasingly valued by suppliers and consumers that want to know what phases each product has completed.
In this post, we analyze the concept of internal traceability, showing how it differs from product traceability and, above all, emphasizing what to take into account to ensure the quality of a product when it leaves the warehouse.
What’s internal traceability?
Also known as process traceability, internal traceability stems from the concept of product traceability. This, of course, is the set of actions, measures, and procedures that make it possible to record and identify a product and the steps it’s gone through within the supply chain.
In this sense, internal traceability concerns the monitoring of the goods in the installation or production plant. This encompasses everything from measures relating to the handling and manufacturing of the product to its bill of materials (BOM) and the equipment used to process it. On the other hand, the concept of external traceability refers to the exchange of information and products between the various links in the supply chain.
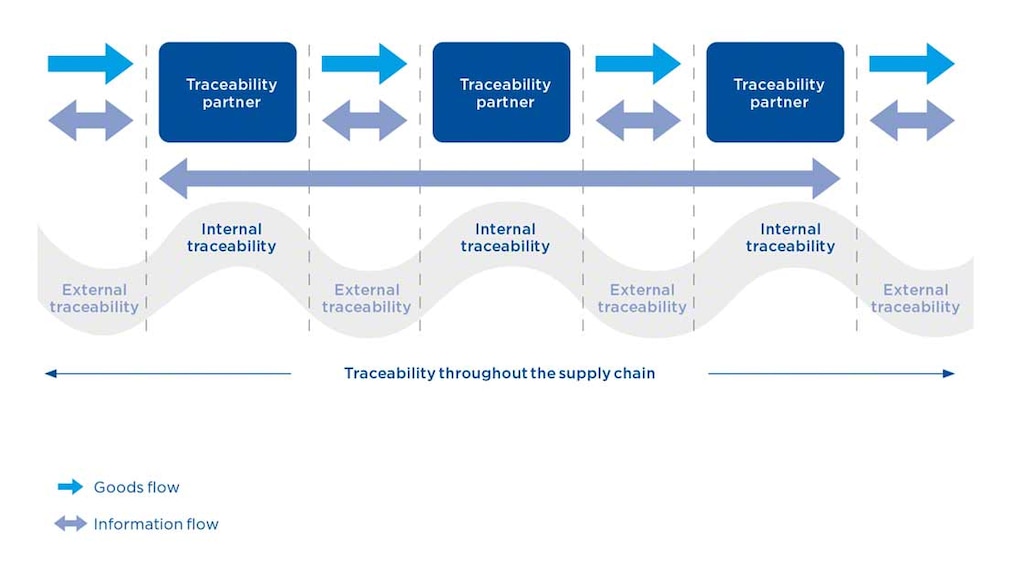
Internal traceability has become a basic logistics requirement, especially in sectors sensitive to stock quality and safety, such as the food and pharmaceutical industries. For this reason, more and more customers and suppliers are demanding manufacturing-history and order-preparation control.
Internal traceability: applying it in the warehouse
To maintain a continuous, useful record of the path that goods follow in an installation, it’s necessary to deploy an internal traceability system that monitors this.
To implement an internal traceability plan that verifies that a product can be located despite the multiple operations it undergoes, be sure to bear in mind the following:
- Registration in internal communication systems: the logistics manager has to sync all the devices and areas in the warehouse to guarantee the effective communication of data on a product in its various phases. The progressive automation of logistics centers — incorporating barcodes on the labels of each container — simplifies this work.
- Procedures in place for finding errors: the internal traceability plan must include mechanisms for detecting errors in the different operations, locating the products involved in these processes, and removing them as quickly as possible.
- Knowledge of current standards: the organization should base its plan on existing legislation in terms of traceability (ISO 9001:2015 or ISO 22005) and standards pertaining to any elements that make up the warehouse, for example, the ANSI-MH16.1 standard (Specification for the Design, Testing and Utilization of Industrial Steel Storage Rack).
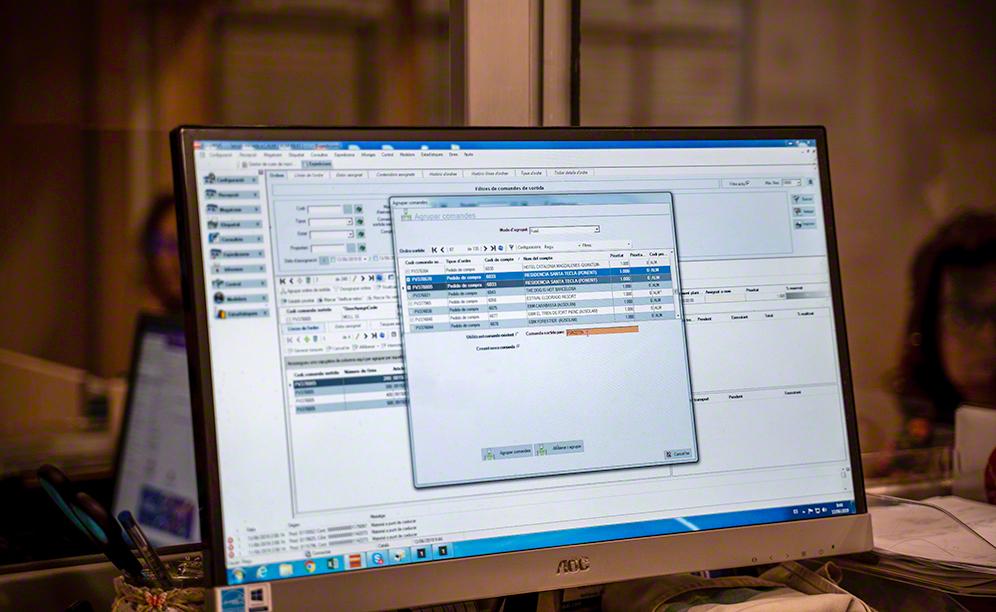
The role of software in process traceability
A warehouse management system plays a key part in ensuring the internal traceability of SKUs. The software is charged with recording goods movements, providing a complete picture of each container: contents, product makeup, exit order, and the processes through which the products have gone.
The WMS acts as an information consolidator for all the nodes in the supply chain. In each entry order, the ERP system communicates to the WMS the products held by each container, the materials they’re made from, their origin, and even the license plate of the truck slated to make the delivery, among many other data.
Thus, digitizing warehouse management through applications such as ERP, WMSs, and MESs guarantees not only comprehensive control over inventory, but also real-time knowledge of which operation a product is undergoing, how each order was prepared, and which batch was managed with each raw material. All this allows end customers as well as any supplier to break down all the processes through which the product has gone and see who took part in each one.
Additionally, internal traceability is fundamental — perhaps even more so — for organizations with manufacturing processes in their installations. This is why several software applications include modules to sync the supply buffer with production, seeing to it that operations are nonstop. That’s the case with, for instance, our advanced Easy WMS feature WMS for Manufacturing.
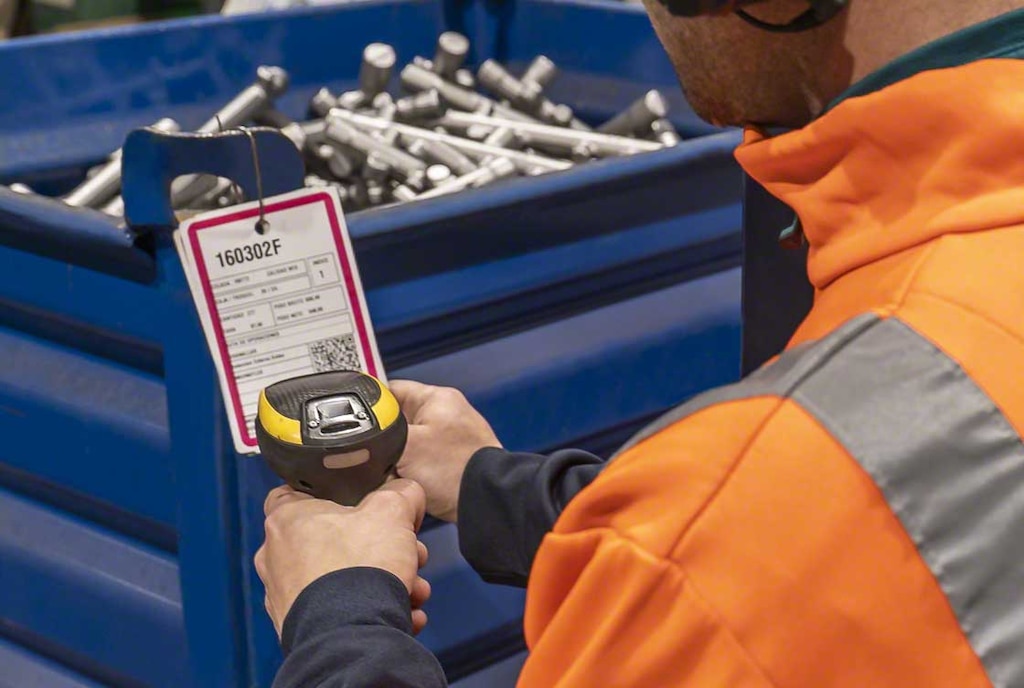
An actual process traceability system
Let’s take a look at an example of the implementation of an internal traceability system, namely, the case of Nicopan. This baked goods and pastry producer controls over 9,000 perishable SKUs in its installation.
Nicopan installed our company’s Easy WMS warehouse management system to administer all workflows in its logistics facilities. This has provided the Nicopan with real-time information on all products in all its centers.
With this software, operators can identify the location and characteristics of each SKU. Through radiofrequency terminals connected to the WMS, workers can access all a product’s details by simply scanning its barcode. Meanwhile, the logistics manager can now accurately monitor inflows and outflows. This is especially important, as this firm receives goods from both external suppliers and in-house production.
In short, the deployment of a warehouse management system has enabled this company to sync the installation with the production center, achieving efficient logistics and full traceability of its centers.
Internal traceability, vital in logistics today
A WMS ensures the implementation of an effective process traceability system. That is, it makes sure that a reliable record is made of all the characteristics of each container entering and leaving the warehouse, in addition to monitoring in real time the operations it’s undergone, its location, and the handling equipment or employee that processed it.
If you’re looking to install a system that strengthens internal traceability in your facilities, don’t hesitate to get in touch with an Interlake Mecalux expert. Many businesses have improved their information flows and operational efficiency thanks to our software.