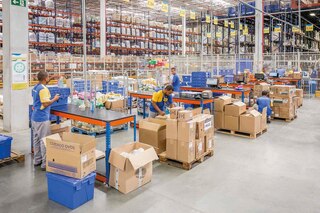
How do you plan logistics operations for Black Friday?
Although each warehouse or distribution center is unique, with its own rules and ways of operating, one common challenge is the organization of logistics operations during peak season, e.g., Black Friday. The ecommerce boom has made logistics operations more complex, introducing variables like last-mile delivery and reverse logistics. And these become especially hard to manage during peak season.
Black Friday is an important date on consumers' calendars. But the current environment could have a direct impact on companies' sales forecasts. According to a survey of 2,000 people in the UK by Censuswide and Finder, British consumers will invest £850 million ($1 billion) on Black Friday in 2022, down 18% from the previous year. Despite the overall reduction in spending, 6% more Brits expect to shop during Black Friday compared to 2021. So, why is this? Faced with an ever-increasing cost of living, when making their purchases, consumers want to take advantage of bargains.
Below are some good practices to apply in the warehouse so that logistics operations work smoothly — even under the pressure of Black Friday or any other peak season.
1. Analyze in-warehouse logistics operations
Detecting points to improve is the first step towards process optimization. In this sense, picking and order preparation are the most time- and resource-consuming logistics operations in a warehouse. Therefore, it's essential to analyze every detail to detect inefficiencies and adapt the facility to a peak activity period.
Even the smallest changes can have an enormous impact on the final outcome. For example, having enough packaging in stock and having it conveniently located can save unnecessary operator trips. This is especially important during busy periods such as Christmas, seasonal sales, and Black Friday.
Do an in depth analysis of all processes that are carried out in your center along with your team of operators: goods receipt, shipping, and even other activities such as cross-docking.
2. Check your layout and adapt if needed
A warehouse’s design is crucial in responding to peak season logistics operations. How stock and picking areas are arranged directly affect the time spent on picking.
During peak activity, efforts are concentrated on picking the right goods and getting them out the door as quickly as possible. To speed up the process, we recommend optimizing your in-warehouse material flows. Another measure to consider is to set up additional areas dedicated to order conditioning or to try to simplify the packaging process.
To determine whether the requirements involve a temporary change in your layout, you need information on demand forecasts. In the end, the warehouse doesn't function as a separate node within the supply chain — it must be in direct communication with all the cogs and wheels.
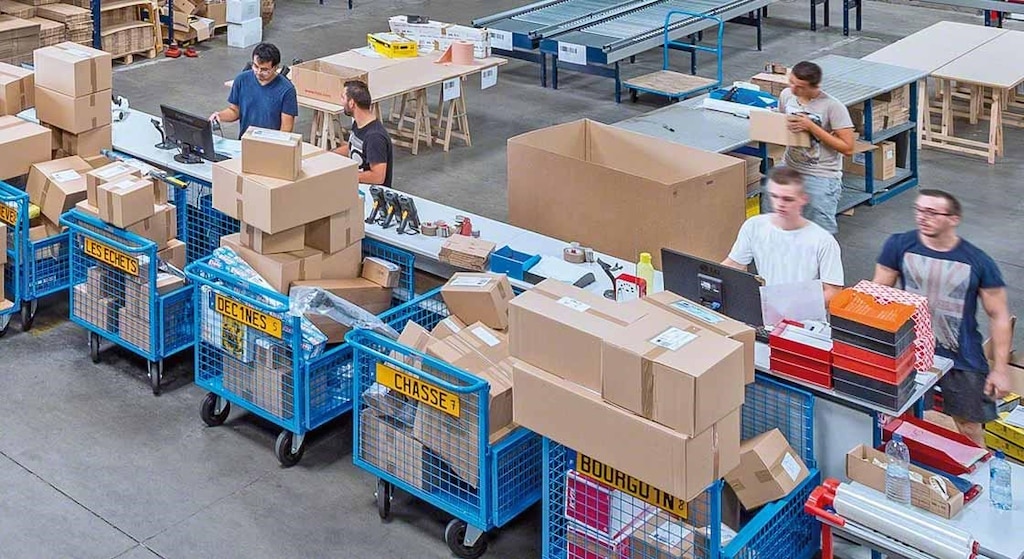
3. Don't neglect operator training
Operator versatility is one of the key assets when we talk about peak season logistic operations. However, working under pressure without the right tools can be counterproductive. Training is the core element that equips operators with the skills they need to perform effectively during peak activity. Two types fit all:
- Continuous training for staff: job rotation helps all workers to have the capacity to perform tasks in different areas. In addition, if automated storage and retrieval systems (AS/RS) and/or warehouse management software are used, all workers must have the knowledge required to operate with them.
- Effective initial training: in peak season, it's common to shore up your workforce with temporary workers. To integrate them quickly and fruitfully, design an express training plan specifically with them in mind.
4. Make the most of WMS functionalities
Using a WMS is a great help in managing a warehouse during peak seasons. Operations are automated and optimized thanks to the program, which tells your team which tasks to execute step by step and in what order. This way, there's no confusion — even in peaks in activity.
Taking Interlake Mecalux's Easy WMS warehouse management system as an example, its Labor Management System module is especially useful for coordinating operators during busy periods like Black Friday.
As we've seen, there are many areas in the warehouse that need to be fine-tuned. For many sectors, this period of peak logistics activity is concentrated at Black Friday and Christmastime, but there are warehouses that go through them at other times of the year. Take our advice: squeeze more potential out of your facility and WMS to successfully deal with operational risks in times of increased logistics activity.