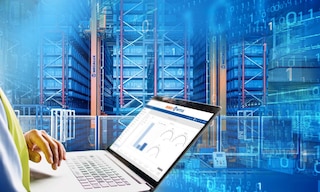
Make to stock: the advantages of anticipating orders
Knowing what the immediate demand for a product will be makes it easier to establish manufacturing strategies such as make to stock.
What is make to stock?
Make to stock (MTS) or build to stock is a production method based on manufacturing according to demand forecasts. It involves initiating production in advance and independently of customer orders. To be successful, it requires accurate forecasting. With this approach, items are made based on expected demand and stored until customers purchase them. The main advantage of this strategy is that products are available even before they are requested.
This manufacturing system is extremely efficient when demand can be accurately estimated. Therefore, before putting it into practice, it’s best to rely on historical data and real-time information sources. Executing it correctly and having inventory available as early as possible will give you a competitive edge. But implementing make to stock incorrectly can lead to overstock, stockouts, and business losses.
How can companies benefit from make to stock?
Adopting the make-to-stock production method — also known as the push system, has multiple advantages:
- Economies of scale. By manufacturing in large batches, fixed costs are spread across more units. This reduces the production cost per unit, allowing companies to benefit from economies of scale.
- Faster deliveries. Since make to stock is designed to produce for storage, products can be available in stores from day one. By not having to wait for manufacturing, you can leverage sales opportunities.
- Greater flexibility. Running longer series with similar items maximizes equipment usage, limits changeovers, and boosts overall efficiency.
- Improved forecasting. While good forecasting and inventory visibility are essential before implementing make to stock, this strategy can also enhance future forecasts. Demand becomes more predictable when products are readily available to customers.
- Minimized inventory. Aligning production with anticipated demand enables efficient resource management and prevents excess stock.
- Optimized production. Anticipating needs before receiving orders allows for better adjustment of capacity, labor, and raw materials, resulting in a more accurate production plan.
- Reduced costs. Acquiring resources in advance, in bulk, and through efficient planning minimizes excess inventory and associated costs.
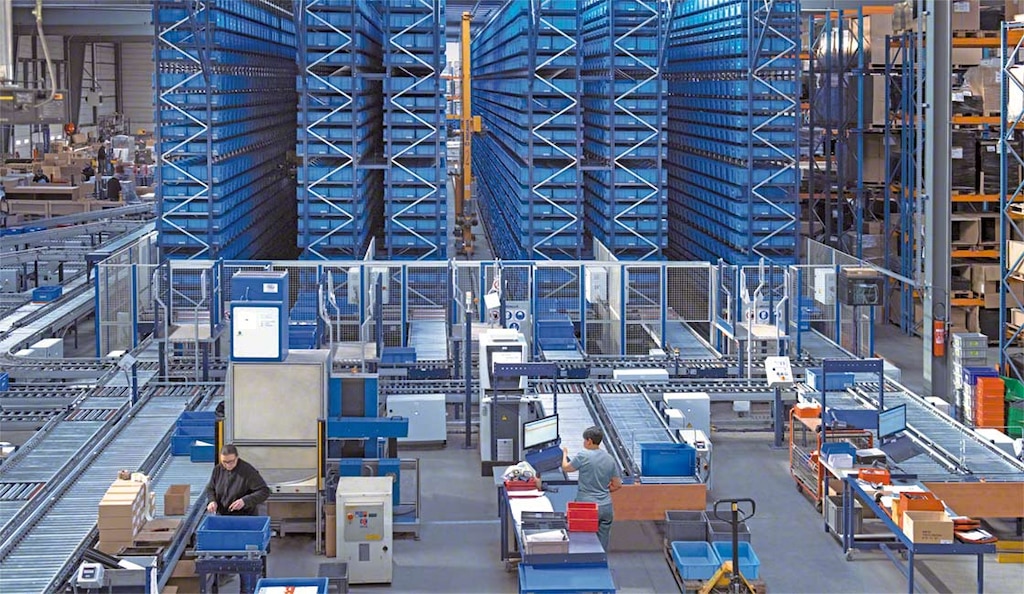
Who uses make to stock?
The make-to-stock production method can be especially advantageous for companies that supply major retail chains. This is because these clients typically do not require product customization and often place large orders.
However, to leverage the full benefits of make to stock, you need access to the best possible information sources. For this, it’s crucial to have excellent inventory visibility across all distribution nodes and points of sale. This can be achieved with a distributed order management system such as Easy DOM. It’s also vital to thoroughly analyze all processes in your facility with a warehouse management system like Interlake Mecalux’s Easy WMS.
Examples of warehouses using make to stock
Businesses across various industries can benefit from make to stock. Here are some prime examples of facilities where this strategy is effective:
- Toy companies produce year-round to be ready for the fourth quarter, when most sales occur due to holidays like Christmas and Black Friday.
- Manufacturers of other seasonal products such as swimsuits anticipate their production for each hemisphere’s summer, ensuring these items reach department stores before the warmer months.
- Similarly, outdoor furniture sales decline during winter. Nonetheless, companies can continue manufacturing during the colder months to have enough stock ready by spring.
- Another scenario involves businesses that produce goods for distributors. These organizations manufacture items that are later purchased by third parties, who then sell them in the market.

What is make to stock vs. make to order?
Make to stock contrasts with the make-to-order philosophy. Make to stock consists of producing goods to be stored before receiving orders. Make to order, on the other hand, focuses on producing based on customer demand, i.e., only after an order has been placed.
Although make to order may seem more flexible at first glance, it can be less efficient than make to stock. It allows for more changes and customizations, but this also makes the process more complex. Generally, make to stock is suited for companies with more predictable demand, while make to order is appropriate for products with unstable demand.
Prepare your strategy with Interlake Mecalux
Whether you choose make to stock or make to order, implementing the latest advancements in intralogistics is a must. Interlake Mecalux can help you effectively manage inventory before customer orders are placed, while also collecting critical data about your warehouse and stock levels. This information will enable you to make accurate predictions and prepare for future scenarios.
Our expertise in automation and management software like Easy WMS supports your operations. Additionally, we enhance visibility for large distribution networks through Easy DOM. Contact us to benefit from our extensive intralogistics experience, built over decades since 1966.