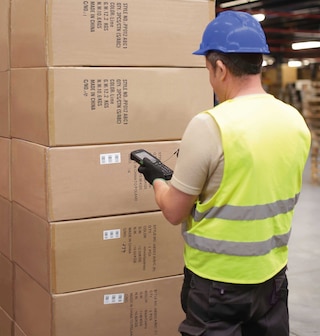
Errors to avoid during order processing
Are you completely happy with the order fulfillment at your company? If not, can these results improve? Is creating a better customer experience important to you? The many mistakes made during picking or packaging are what can lead to customer complaints and claims. Although total perfection is hard to achieve, it is possible to make corrections along the process so orders are dealt with and shipped out in the best possible condition. To do so, here are a list of errors to be avoided during order fulfillment.
1. Pick the wrong item = picking error
If an article was slotted in a specific warehouse location where it didn’t belong in, most likely the person tasked with collecting a SKU from this location would pick the wrong item. The consequences of such an error should not be taken lightly, since the order picker ends up putting together the wrong items for the same order, which without a doubt will mean a claim from the customer.
2. Not enough product was picked
Sometimes, how many items were picked is the issue and the person picking the order might have taken either more or less than what is needed for the order.
When a company is quite large and using barcode readers, these devices can keep operators informed of how many items must be collected. However, it is crucial to register the number of items picked on the barcode scanners to avoid repeating this type of error.
3. Collecting SKUS with very similar IDs
Slot signaling is of vital importance to many logistics professionals. This system makes it possible to locate an item quickly. However, this can just as easily case mistakes: instead of scanning the intended item’s barcode number, the operator internalizes a very similar reference number and picks a different item.
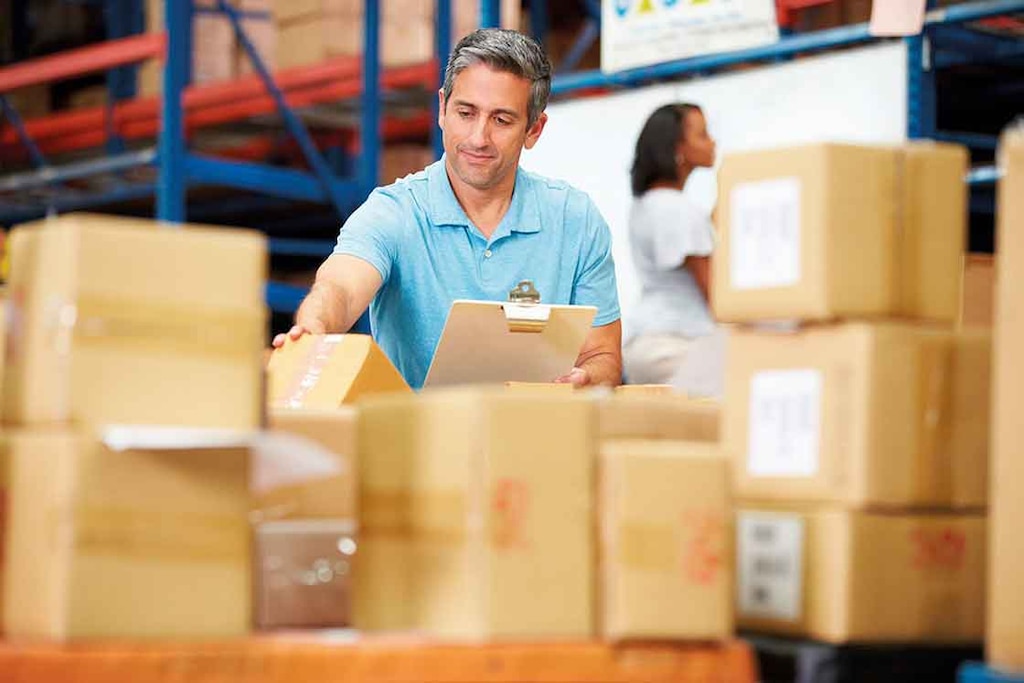
4. Items are spread all over the warehouse
As a time-waster in picking, being unorganized means: the operator must go to different warehouse zones to pick different units of the same product. This situation is fairly common and, despite which, should not be happening if your business shows dedication to being organized and managing stock right.
5. Missing items
You receive barcode labeled products and goods with codes that let you ID and locate these items in the warehouse. Despite this fail-safe, it is not uncommon to find unlabeled items on the racks. In this event, these items must go through the labeling phase again before being added to an order.
6. Mixing two or more orders
Many times, a single operator is tasked with collecting various items from different orders at once. A matter of fact, this practice streamlines order processing.
However, this technique is quite risky because a single lapse in attention can cause an error when packing an order.
Since you want to avoid making this mistake, get in the habit of scanning each item before packing. Likewise, the barcode scanner comes in handy to keep the person preparing the order up to speed on what must be packed for each one of the orders.
7. Unauthorized item replacement
When dealing with stock breakage, if an item must be replaced by another, it is vital to properly register this replacement in the system. Otherwise, this action can adversely affect stock management. Your replacements policy must be clear, and all your employees must follow it to the letter.
8. Wrong-sized item picked
Often, a warehouse carries identical items but in different sizes. So, if you want picking to be done under suitable conditions, each package must have its own barcode reference, and the person preparing the order must scan the item before picking.
Many factors can lead to errors being made during order processing. Identifying these errors is the first step towards fixing the problem successfully. Once you pinpoint money-losers and other processes that stand in the way of 100% customer satisfaction, we recommend you apply solutions to optimize the order fulfilment process.