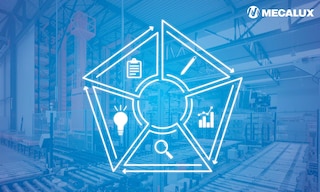
Six Sigma and its application in logistics
Various techniques and tools can improve production systems and ensure service quality while minimizing errors. One of the most well-known is Six Sigma (aka 6σ or 6 Sigma).
What is Six Sigma?
Six Sigma is a methodology used by companies seeking to implement continuous improvement in their processes and achieve operational excellence. This lean approach focuses on quality control, and its name refers to the statistical concept of standard deviation. The goal of Six Sigma is to operate so efficiently that defects are reduced to a maximum of 3.4 per million units produced or handled. This ensures a six-standard-deviation gap between the process mean and specification limits.
First developed by Motorola in the 1980s, Six Sigma is now widely adopted across manufacturing, healthcare, finance, and industrial services to improve customer satisfaction, reduce costs, and maximize profits. Six Sigma certification programs classify expertise levels using a belt system, ranging from white to black, similar to martial arts rankings.
What is Lean Six Sigma?
The Six Sigma continuous improvement methodology and the lean logistics philosophy share common goals. While Six Sigma aims to minimize errors, the lean concept — focused on achieving more with less — strives for efficiency by simplifying manufacturing processes.
Their similarities have led to the development of a hybrid methodology known as Lean Six Sigma. In this framework, the lean approach optimizes processes by improving workflows, and Six Sigma uses data analysis as a tool to identify and eliminate the root causes of potential issues. The Six Sigma method also shares similarities with other techniques, such as the PDCA (the Deming cycle).
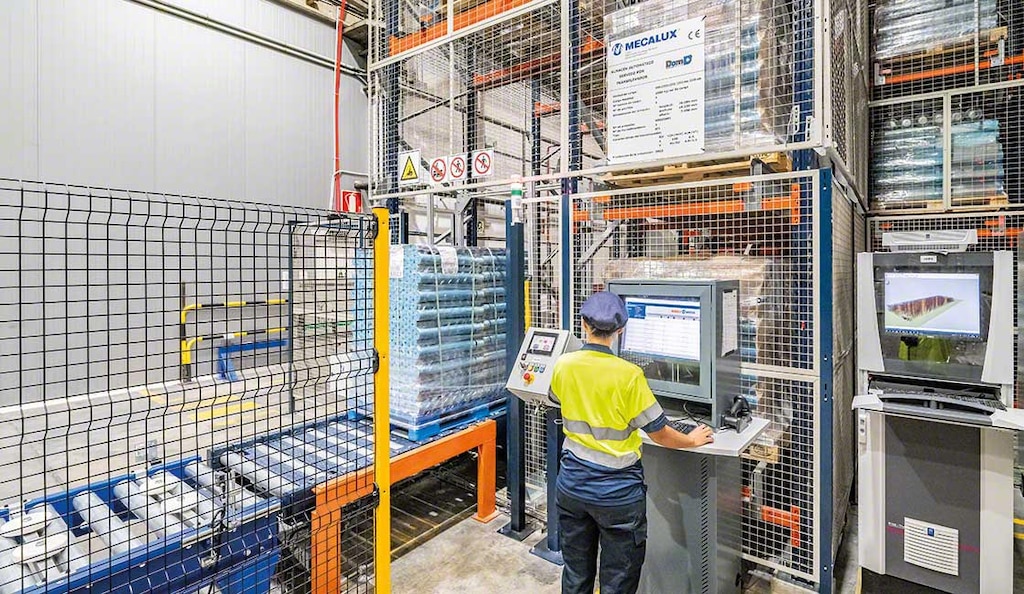
DMAIC: The five phases of Six Sigma in manufacturing
To successfully implement this program, companies follow the DMAIC methodology, which consists of five key phases: define, measure, analyze, improve, and control.
- Define. Clarify the client’s needs, quality requirements, project scope, and the team responsible for execution.
- Measure. Identify and assess all variables related to the issue to understand its current state.
- Analyze. Interpret the collected data to determine the root causes of the problem.
- Improve. Implement solutions to correct defects, prevent recurrence, and optimize processes.
- Control. Monitor results to verify whether objectives have been achieved.
Six Sigma methodology types: DMAIC and DMADV
Besides DMAIC, another Six Sigma sub-methodology also consists of five phases: DMADV, which stands for define, measure, analyze, design, and verify. While DMAIC applies to existing processes or products, DMADV is useful for those yet to be developed. The first three phases — define, measure, and analyze — are shared, but the last two, design and verify, serve different objectives:
- Define. Establish the client’s needs, quality standards, project scope, and team members.
- Measure. Identify and quantify all factors affecting the issue to understand it fully.
- Analyze. Examine the collected data to determine the problem’s root causes.
- Design. Use the parameters identified in previous phases to achieve the set objectives.
- Verify. Ensure the process is progressing as planned.
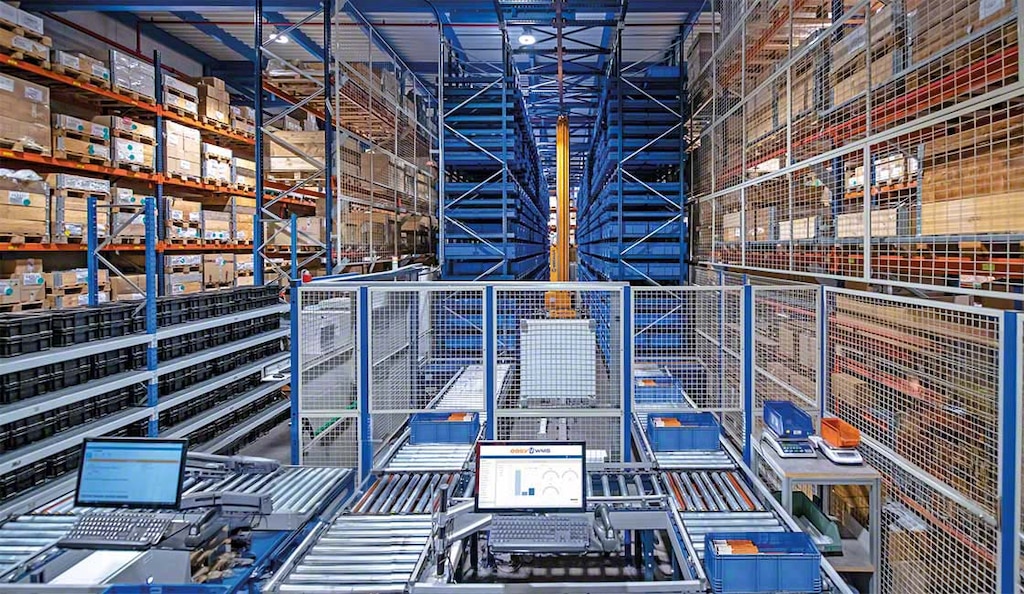
Six Sigma applications and benefits
The Six Sigma concept and its five-step approach to organizing work offer numerous advantages to businesses that adopt it:
- Greater efficiency. Six Sigma aims to achieve a 99.99966% effectiveness rate, meaning only 3.4 defects per million products reach customers.
- Process control. By defining measurable variables, this methodology monitors company processes in pursuit of operational excellence.
- Increased productivity. Engaging all business areas in continuous improvement can enhance performance across multiple departments.
- Resolution of structural issues. Identifying areas for improvement and implementing solutions help eliminate potential failures.
Six Sigma examples
Logistics companies can apply Six Sigma in several ways to improve operations. One approach is to reduce response times for user requests or complaints.
For instance, businesses can log customer complaints, analyze them, and measure resolution times. Categorizing these grievances in a table, along with their root causes, helps identify key defects and areas for improvement.
Retail and distribution companies can also optimize warehouse processes and resource management using specialized software. Interlake Mecalux’s Easy WMS warehouse management system, for instance, provides complete real-time product traceability, minimizing errors and raising productivity.
Improve your warehouse efficiency with Interlake Mecalux
At Interlake Mecalux, our storage, automation, and software solutions streamline operations and boost efficiency for all kinds of facilities. We work closely with our clients, tailoring our WMS to their particular needs. If you’re looking to enhance your supply chain, be sure to contact us — we’ll guide you in optimizing your logistics operations.