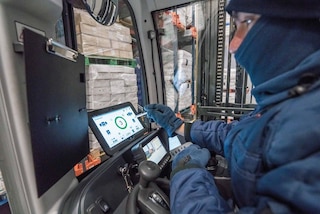
Protect your cold chain with these in-warehouse systems
Cold-chain breakage in a refrigerated or frozen goods warehouse is an inexcusable mistake that a logistics manager should never make. However, preventing this hazard is not an easy task. Ensuring that goods are kept within a very strict temperature range at all times presents a real challenge.
You can preserve the cold chain inside your warehouse with the help of a series of automatic and manual systems that aid in the appropriate conservation of food, pharmaceutical or chemical products. Discover these systems and what challenges you can overcome thanks to them.
Challenges in protecting an in-warehouse cold chain
Good cold chain management requires that you keep an eye on the following points:
1. Make the most of the available space in your freezers
The idea is to maximize the storage capacity of your cold room because this will lead to greater power efficiency and consequently higher profit margins.
High-density racking and Movirack mobile pallet racking systems are a perfect duet for storing large volumes of goods in just a few square feet.
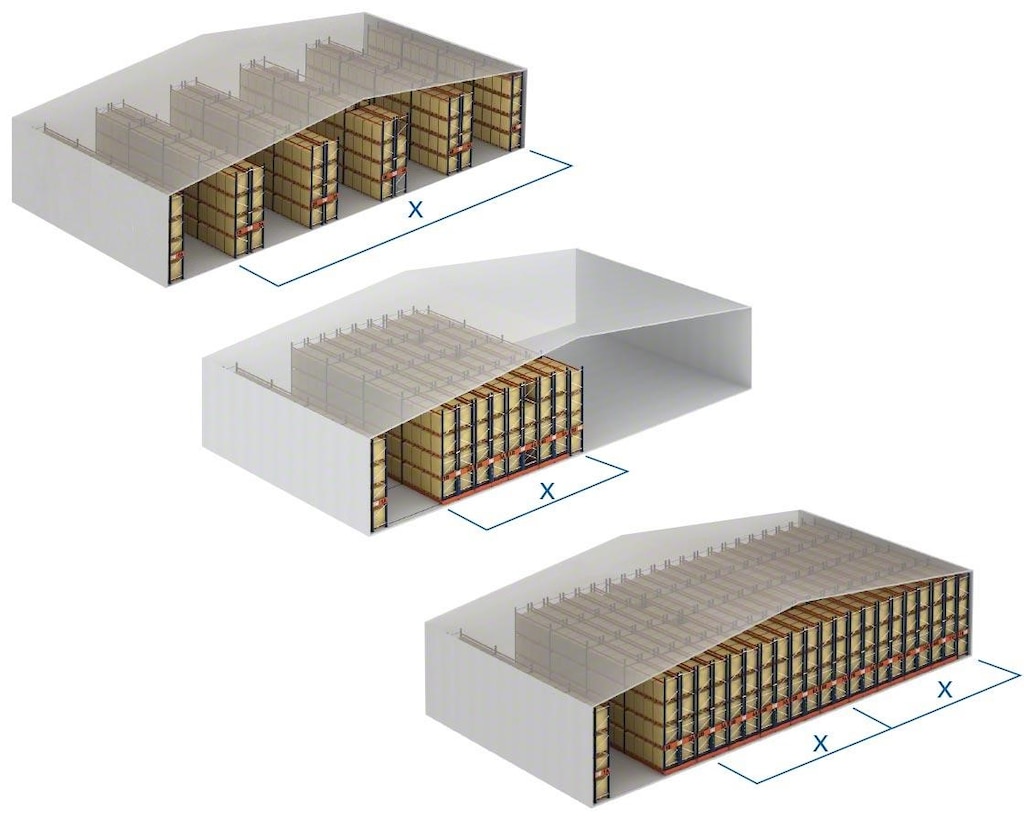
The illustration above shows the advantages of the Movirack mobile pallet rack system over a standard pallet rack system. The installation of this compact-type racking allows more than double the storage capacity thanks to the savings in space previously used for aisleways.
2. Minimize manual operations needed inside your freezer
Limit the presence of operators inside the cold stores. Access should occur only when it is essential. This is the best approach to deal with cold air leaks and preventing occupational hazards and human slip-ups.
3. Controlling product traceability
Constant control over stored products and perpetual inventory must be enforced across the board to certify that goods are dispatched in their optimum state of preservation. Guaranteeing the traceability of SKUs in the eyes of the consumer is possible thanks to a warehouse management system such as Mecalux's WMS, which automates information flows in real-time.
Systems to protect your in-warehouse cold chain
If your warehouse specializes in chilled or frozen products, you should definitely include technologies to preserve the cold chain, such as:
1. Automated installations
In low-temperature environments, the quality and productivity of your workforce is affected. For this reason, it is best to automate most of your refrigerated warehouse's processes. In this way, fewer errors or lapses will occur, which could cause breaks in the cold chain.
Depending on the number of SKUs handled, you can choose between different modalities: single or double-depth racking, or by adding a Pallet Shuttle to run in tandem with stacker cranes or transfer cars.
2. SAS (Security Airlock System)
A SAS (Security Airlock System) is an anteroom with two doors located at the access point to a frozen-storage installation. These doors should never be opened simultaneously.
A SAS prevents goods from being exposed to abrupt temperature changes and keeps condensation at bay while minimizing cold leakage from your installation.
3. Preload staging areas in freezer stores
Preloading products in temperature-controlled settings is another core cold chain protective solution, which goes hand in hand with a SAS.
With this system, the goods leave the freezers via automatic roller or chain conveyors that move the items to the preloading area (after they cross through the SAS), where they are available to the operators.
4. Automatic picking
Automating picking in freezer installations is a fundamental good practice for preserving the cold chain. Picking via robots controlled by a WMS frees up your staff, so they only have to strip plastic from the pallets and, then, the machines can get down to work.
If you must choose a manual picking system, it is a good idea to equip workers with a voice-picking system that gives them “hands-free” pick capacity to concentrate on just handling product.
Thanks to cold-chain protection systems such as these, warehouse managers achieve optimum space usage, a very high operational safety level and a considerable increase in productivity and return on investment. Do you want to see how others pulled it off? Check out our cold-storage success stories.