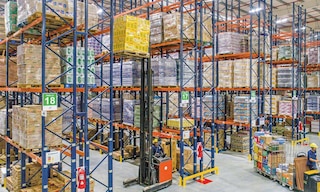
Inventory shrinkage: the silent menace of warehousing
Although it may sometimes seem insignificant, inventory shrinkage has a substantial effect on balance sheets and warehouse operations. Fortunately, the latest intralogistics technologies offer ways to monitor and prevent it.
What is shrinkage in warehousing?
Inventory shrinkage is the loss of stock value in the warehouse. It’s due to various factors and can occur at different points along the supply chain. Shrinkage represents the difference between recorded (theoretical) stock and actual (real) stock.
Types of inventory shrinkage
Stock shrinkage can be divided into two major groups. Normal shrinkage occurs when raw materials are employed in production processes. Abnormal shrinkage, meanwhile, is the most common variety found in warehouses. Below are some examples of shrinkage in businesses.
What causes inventory shrinkage?
These are some of the most typical reasons for abnormal inventory shrinkage:
- Administrative or accounting errors. Checking stock manually can lead to imbalances. These arise from mistakes in record-keeping, causing a mismatch between your inventory and your actual stock. Using tools such as Interlake Mecalux’s Easy WMS warehouse management system prevents information transfer delays, ensuring that these crucial data are updated.
- Expiration dates. These indicate when products are no longer safe for consumption or do not meet quality standards. These dates are a key factor depending on the goods stored; otherwise, you may have to discard them. Additionally, keep an eye on the expiration dates of your raw materials. To make sure they’re used in advance, it’s best not to receive more than what you need for production.
- Inefficient receiving process. This happens when products leave the factory and arrive at the warehouse but are not properly checked. Inspections can guarantee merchandise isn’t damaged, poorly packed, expired, missing components, or incorrectly labeled.
- Theft. The unauthorized removal of goods will result in shrinkage for your company. If you suspect theft might be the reason, be sure to take deterrent measures.
- Stockouts. These are often caused by deficient material handling or by slotting products in the wrong locations. When a stockout occurs, identify where the problem lies, and make sure your racking systems are the most suitable for your goods.
- Deficient transportation. Poor management during this stage could cause the merchandise to spoil. It’s important to verify that transportation is carried out within agreed-upon times and deadlines while maintaining excellent quality and safety levels.
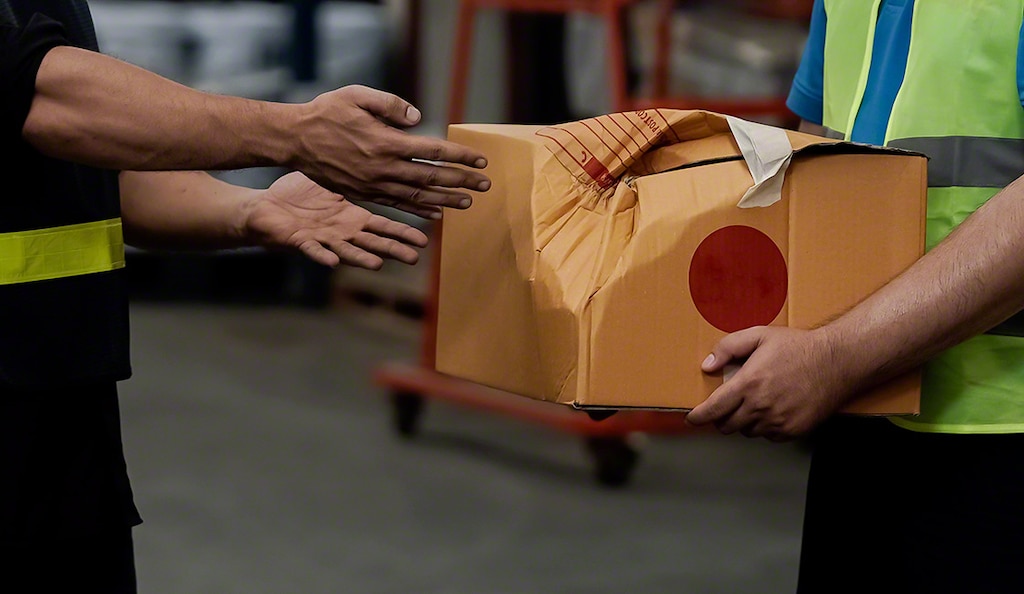
What are the consequences of shrinkage?
Controlling shrinkage in the warehouse is a must, as it involves merchandise with no market value. These goods can no longer be sold, entailing losses for the business. On the other hand, improving inventory to prevent shrinkage boosts productivity, reduces costs, and increases profits.
Another possible consequence of shrinkage is overstock, which can cause space issues and make timely turnover challenging. Although excess stock is more prevalent in companies that store products with short sell-by dates, any retailer can be affected by shrinkage.
How is shrinkage calculated?
Calculating the shrinkage KPI is fundamental — even more so in sectors such as the manufacturing and food industries. To determine the difference between the initial quantity of a product and the final quantity following the production or picking process, we have to consider the concepts of gross weight and net weight.
Gross weight is the total weight of a product before processing. It includes packaging and waste. Net weight refers to the product after processing, ready for sale. One way to measure shrinkage is to subtract the net weight from the gross weight and apply the following formula:
Shrinkage = (Initial product quantity - Final product quantity) / Initial product quantity × 100 |
The result is the shrinkage rate, a critical KPI in any warehouse or distribution center. This percentage enables you to detect problems in logistics and production processes and take measures to correct them.
What’s the average shrinkage rate for a warehouse?
Although it may seem drastic, the target average inventory shrinkage rate is zero. According to the Warehouse Education and Research Council (WERC), the average warehouse experiences an inventory shrinkage rate of 0.2%. This division of the Material Handling Institute also indicates that if the rate exceeds 0.46%, alarm bells should ring. A rate of up to 2% might not seem very high, but all costs add up: inventory shrink is a silent killer of successful ecommerce businesses.

How to avoid shrinkage
Now that we’ve established that shrinkage affects stock value, what steps can you take to minimize it? The answer lies in making changes to your warehouse or production plant operations:
- Adopt inventory control procedures. Labeling products with RFID tags and employing inventory management software such as Easy WMS is the best way to obtain an accurate, real time view of your company’s stock, including in several facilities.
- Reorganize the warehouse. Assigning all products an ideal slot cuts down on inventory errors, promotes turnover, and facilitates material handling. It’s best to plan your new warehouse layout design with assistance from intralogistics professionals.
- Improve receiving and shipping processes. This will avoid potential damage during transportation and ensure that issues are detected earlier, during the storage phase.
- Establish a policy for handling damaged goods. Providing guidelines for detecting, labeling, and managing these items makes inventory control easier.
- Train staff. Employees should be familiar with these protocols and best practices, which often involve using WMS software and automated solutions.
- Increase security. Installing surveillance cameras and systems such as automatic doors can deter theft, one of the causes of shrinkage in warehousing.
Reduce inventory shrinkage with Interlake Mecalux
Managing goods quickly and effectively is the best way to combat losses caused by shrinkage in the supply chain. Looking to automate your operations or digitize them with software? Interlake Mecalux can help. We have extensive experience designing and installing automated warehouses and can create the solution you need. Contact us to enhance your logistics operations and make inventory shrinkage a thing of the past.