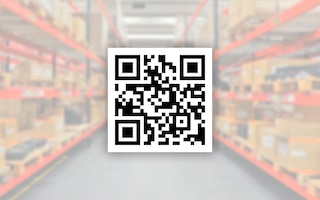
QR codes in logistics: speed and flexibility
QR codes have been a part of logistics since their creation in 1994. Like barcodes, they mainly fulfill two functions in warehouses: to help operators take inventory more quickly and to provide full traceability, that is, monitoring of all the products across the various processes they go through along the supply chain.
According to consulting firm Future Marketing Insights, the global QR code market was valued at $996.8 million in 2018 and is expected to increase annually by 8.7% between 2019 and 2027. So, what about the logistics sector? What impact have QR codes had on the supply chain? In this post, we’ll explore how they’re used as well as their characteristics and advantages.
What are QR codes?
Before getting down to the nitty gritty, let’s begin by defining QR codes. QR (Quick Response) codes refer to an item coding system created to be read extremely quickly. QR codes store different types of information: numeric codes, text, webpage links, and even small binary files (with a 3 KB limit).
Engineers at Denso Wave, a Japanese subsidiary of the Toyota Group, developed QR codes with the aim of overcoming the limitations of barcodes. But what were these shortcomings? At this company’s production plant, operators had to scan a large number of barcodes and identify many SKUs, which required time and effort. What’s more, with products of varying sizes and characteristics, they needed smaller codes that adapted to the different sizes of the goods.
Ultimately, Denso Wave’s objective was to make inventory management with barcodes more flexible. The high-speed reading was achieved through the design of the QR codes themselves. In terms of size, the tiniest QR codes can be as small as 0.6 x 0.6".
How do QR codes work?
They consist of quadrangular codes containing small black and white squares (called “modules”). Let’s take a look at their configuration.
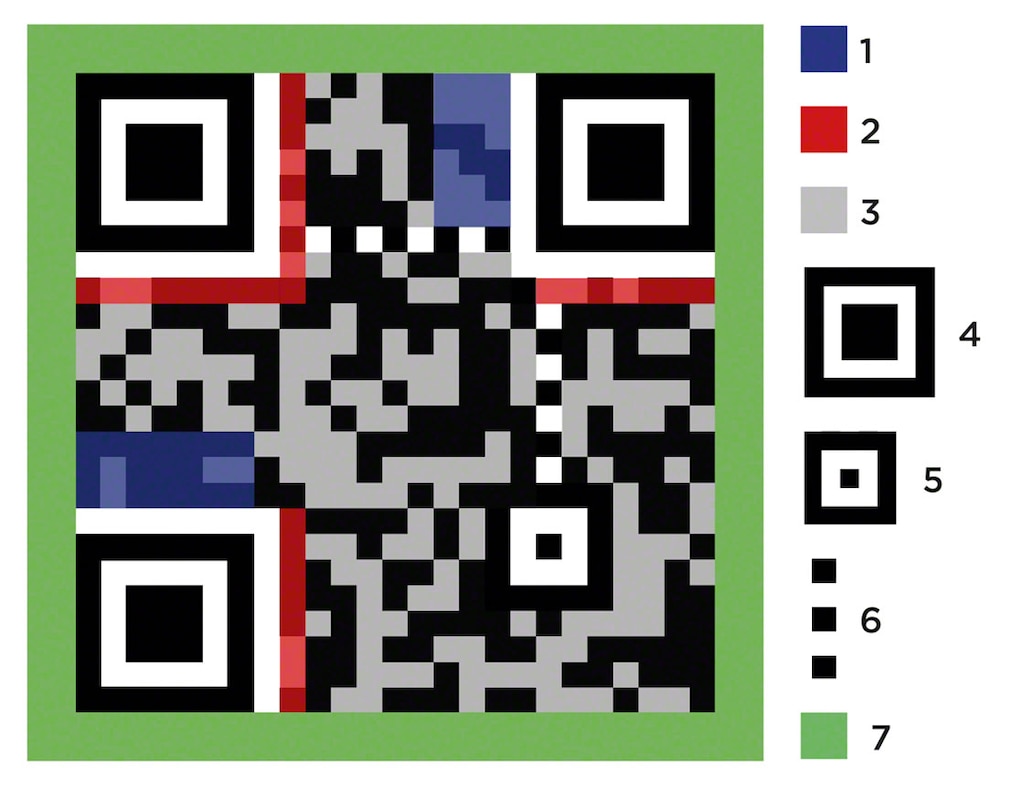
1) Version information. This identifies the QR code version.
2) Format information. This stores data on the error correction level and is what the system first reads when decoding the code. It shows the size of the symbols inside the body (the number of available bytes).
3) QR code data. The alternating black-and-white modules serve to store information.
4) Finder (position detection) pattern. These are the squares at the four corners that facilitate high-speed reading. They identify the rotational orientation of the symbol.
5) Alignment pattern. These smaller squares serve to detect the QR code coordinates and can be read on curved surfaces.
6) Timing pattern. This resyncs the coordinates in the event of a slight distortion.
7) Quiet zone. This helps to isolate a QR code from its environment.
QR code types
There are several kinds of QR codes on the market. The most common is the Model 2, an improved version of the first model designed by Denso Wave. Likewise, other codes, such as Micro QR, SQRC, and FrameQR have begun to take off in the market. These are some of their features and uses:

- Models 1 and 2. Model 1 is the initial version of the QR code devised by Denso Wave. Model 2 is the improved version that can store more information.
- Micro QR. This is the smaller variant of the QR code. Depending on the content and error correction level, it can come in up to four different sizes.
- SQRC. This QR code contains a data-reading restriction, so it serves to administer a company’s private and internal information.
- FrameQR. Illustrations and photos can be added to this code without damaging its contents. Therefore, certain companies use it to add their logo and strengthen their corporate image.
Businesses employ the most appropriate coding for their needs and particular characteristics. For example, the Model 2 has a greater information capacity, so it’s the most suitable for controlling products in the warehouse.
QR codes in logistics
Although QR codes were designed to be implemented in manufacturing, they were soon adopted by the logistics sector. By managing more information and being read faster, they’re ideal for controlling products throughout the various supply chain processes.
Nevertheless, you might ask yourself, “Why should I switch to QR codes when I already use barcodes?” Let’s examine the differences between and advantages of both types of coding:
- Information. Companies manage a multitude of product data (manufacture and expiration dates, owner, demand level, special characteristics to bear in mind when storing the goods, etc.). QR codes contain a large number of characters — up to 7,089 numeric characters, 4,296 alphanumeric characters, or 2,953 bytes — in other words, up to 10 times the information stored by barcodes.
- Sizes. Companies work with all sorts of products, from large (refrigerators) to small (microchips), and they must all be correctly labeled at all times. QR codes are equally effective, regardless of size.
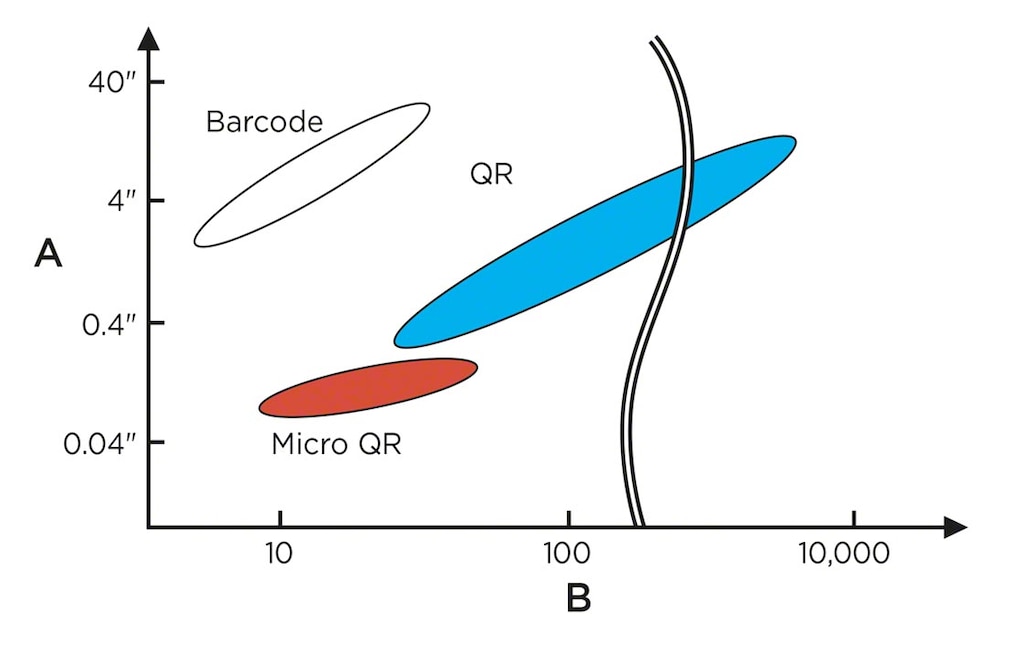
A) Code size (in)
B) Numeric characters
- Resistance. If the barcodes are damaged or dirty, they can’t be read. This doesn’t happen with QR codes. Thanks to the timing pattern, the data can be collected without any problems.
- User-friendliness. QR codes can be scanned by most devices typically used in installations. They are easily read, irrespective of the positioning of the terminal, as opposed to barcodes, which can only be identified horizontally.
The major drawback with QR codes is that, nowadays, barcodes are much more widespread in the market. Companies are used to working with barcodes to identify their merchandise, and implementing QR codes in their businesses would take effort.
Plus, certain products are hard to label with QR codes because of their shape. An example of this is cables, where a conventional barcode would be a better fit.
QR code solutions for warehouses
Coding, whether barcodes or QR codes, is highly practical for ensuring that each product is identified. Although first employed in manufacturing, QR codes were introduced in logistics in order to optimize operations and identify goods more quickly.
To work with QR codes in a warehouse, all you need are laser scanners specifically designed for this purpose. The device should be able to read 2D codes (in addition to the usual 1D) and, particularly, the desired QR code format.
In an installation, all products and processes must, of course, be controlled by a warehouse management system (WMS), such as Easy WMS by Interlake Mecalux. By scanning the barcode or QR code, this WMS accesses the most relevant product data (primarily SKU and turnover) and, thus, can then assign the item a location.
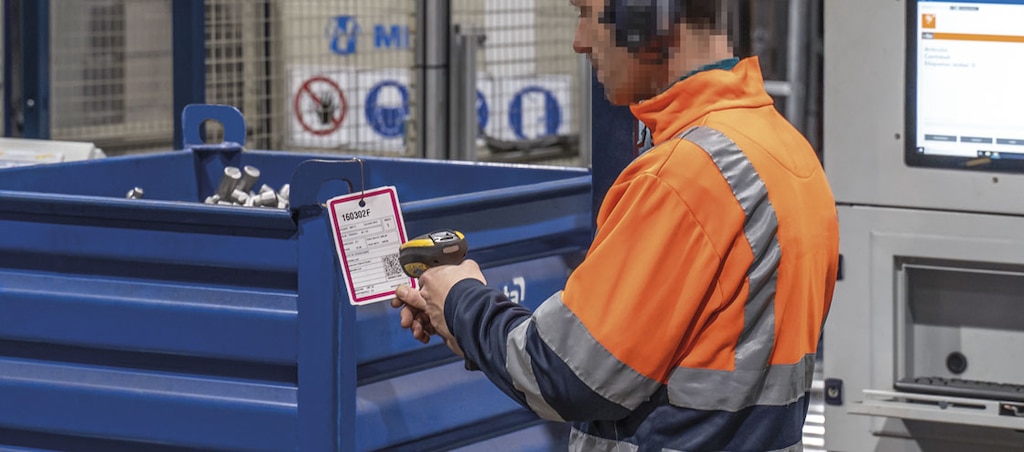
Coded logistics
Businesses accustomed to using barcodes in their installations can consider implementing QR codes to improve agility in storage and stock management tasks.
In an installation that works with QR codes, effective management is essential. Interlake Mecalux offers Easy WMS, a software system capable of operating with coding generally used in warehouses, including QR codes. By reading them with any kind of radiofrequency terminal, the WMS assigns a location to each product, taking into account company particulars. Feel free to get in touch with Interlake Mecalux. We’ll show you how Easy WMS can adapt to and optimize your warehouse.