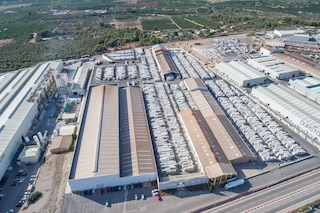
Supply chain benchmarking: a key strategy for continuous process improvement
Supply chain benchmarking is defined as the process of collecting information on good practices in the sector and from industry leaders to study and adapt them to the reality of your company.
Why benchmark your supply chain processes?
If your goal is to achieve the world record for running a marathon, the first thing you need to know is what record you need to beat, who you’re up against and, above all, what their strengths are.
Something similar occurs when we talk about benchmarking in supply chain management: the pursuit of efficiency is inherent in your business, but aspiring to logistics excellence means adapting your activity to trends in the sector.
At this point, we should note the differences between and the benefits of combining the following concepts:
- Benchmarking or comparative analysis: this procedure is used to compare processes, products and operations with other areas of the business, with other firms, and with leading companies in the sector. In the end, supply chain benchmarking is a comparative assessment used to put into perspective your performance and methods compared to those of others.
- KPI (key performance indicator): it’s advisable to break down each operational area into specific subprocesses and assign to each one a metric or KPI that evaluates their evolution over time. With these indicators, you’ll be able to detect deviations and situations that need to be addressed.
Key steps in supply chain benchmarking
To perform this, it’s necessary to go through a series of stages:
1. Identify the supply chain processes to benchmark
The first step in a competitive analysis is pinpointing the processes that are critical to your business. In general, the spotlight will be on those that are registering ineffective results and whose improvement would have a major impact on performance. In this case, it’s extremely useful to consult your key performance indicators, as seen in our article on measuring warehouse KPIs.
Tools such as warehouse management software and, in particular, the Supply Chain Analytics Software module enable you not only to record but also to process and analyze large amounts of data.
These systems assign KPIs and measure operation throughput, which will prove very useful in determining which supply chain processes you should benchmark.
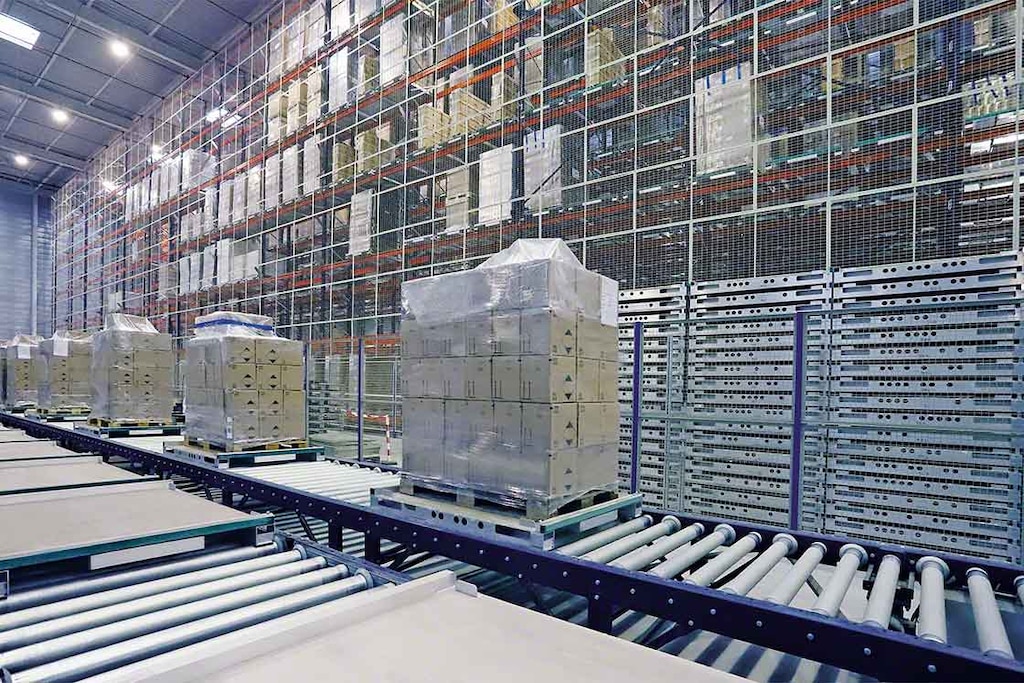
2. Identify sector leaders and gather information
Once you’ve identified the critical processes you want to analyze, the next step is to look for those firms that stand out for their efficient management. You can take into account:
- Direct competitors: they’re the ones you’ll be drawn to first. But they’re also the most difficult to analyze, since accessing their information is more complicated.
- Indirect competitors: due to their size, they’re not on the same level within the industry. However, they do compete for the same customers and can halt your growth.
- Businesses in other sectors: although they operate in another sphere and aren’t competitors, you can learn from their efficiency and methods.
Where can I find information?
- Technical publications and media specializing in the logistics sector highlight developments in terms of procedures, strategies, product launches, etc.
- Industry trade fairs usually bring together the sector’s best and brightest, featuring them in discussion panels that facilitate idea-sharing and presentations of success stories.
- Suppliers, who are in contact with numerous firms in the logistics sector, have an overall view of the standards and of the problems that many logistics companies face.
- Business associations form a network of companies with the aim of defending their interests and looking for synergies.
3. Adapt good practices to the reality of your company
Supply chain benchmarking isn’t about merely copying your competition without taking into account the context. The purpose of a comparative assessment is to improve your own processes while drawing inspiration from formulas that are working in a specific industry or organization. To adapt good practices to your business, you need to:
1. Define the implementation plan and establish objectives: specify which best practices will be carried out and how this will be done.
2. Assign resources: designate, for example, the work team and tools to be used.
3. Set your KPIs: these will measure the evolution of your project.
4. Prepare a pilot project as a trial test: this could consist of, for example, applying a different picking method to certain SKUs in the installation. You would perform this in a restricted way to then compare it with the previous technique.
5. Analyze the pilot project: check the results to decide whether or not it’s scalable.
Supply chain benchmarking is an excellent strategy for looking beyond the confines of your warehouse and learning from the experts. If you’d like our help in finding the solutions most suitable for the realities of your installation, we encourage you get in touch. One of our technical specialists will advise you.