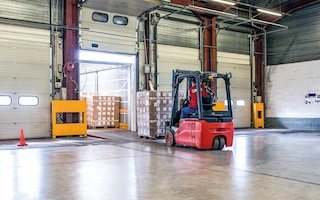
Optimize truck loading with software
Properly loading goods onto a truck is a complex process, especially when faced with increasingly varied packaging, unit loads, and transportation modes. Software and digitalization are the solution to this issue, as they help to automate a large part of this process, making it quicker and more effective.
In this post, we’ll explore how new technologies can achieve maximum efficiency and productivity in goods dispatch.
Loading trucks in the age of e-commerce
Truck loading constitutes the process by which products are placed on a vehicle in order to be transported to their destination (a distribution center, another warehouse, or directly to the end customer). It’s vital to make sure that the weight distribution in the truck is correct and, particularly, that there are no mistakes in the goods dispatched or assigned.
The difficulty is further complicated by tight delivery times dictated by e-commerce retail and multimodal logistics, where a parcel is moved by various modes of transportation before finally reaching its destination. One sector that exemplifies this complexity is the 3PL industry, since the variety of SKUs and customers make dispatch a particularly tricky operation.
These growing challenges, meanwhile, are exacerbated by increasingly complicated error management. In the event of a mistake, as a minimum, the company has to manage the return and shipment of the new product — and cover that additional expenditure.
Consequently, the dispatch phase is key to controlling costs and brand image. Once the goods are in the truck, it’s hard to correct any mistakes that may have been made. Therefore, incorporating software in this phase is crucial for ensuring that the process goes smoothly.
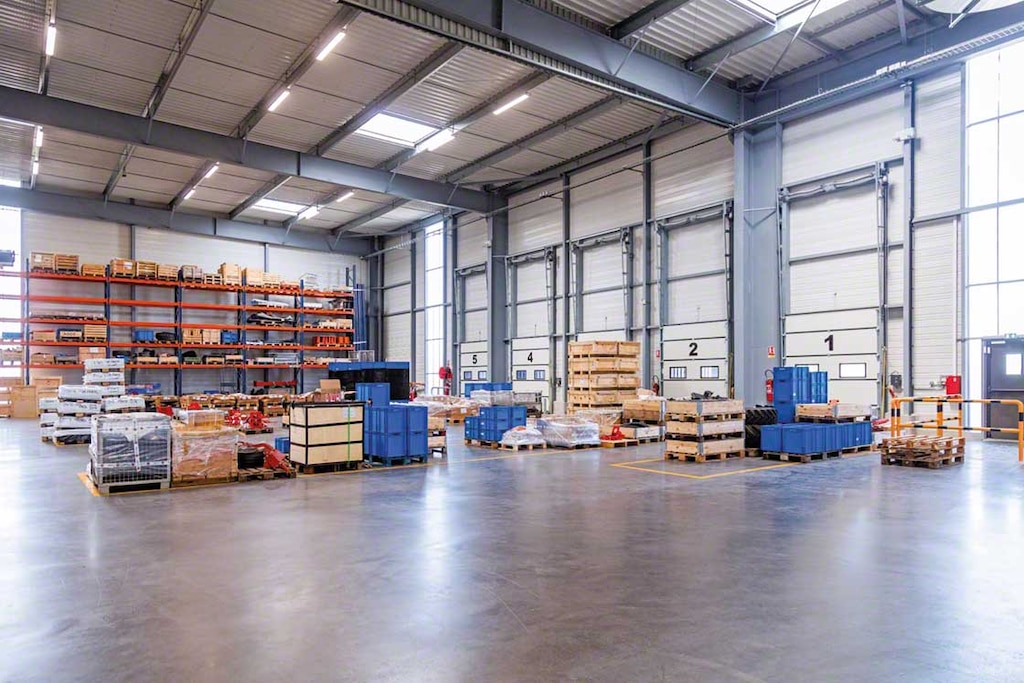
Advantages of implementing software in the truck loading phase
A warehouse management system (WMS) is the software charged with managing truck loading in an installation. In fact, Easy WMS, the WMS by Interlake Mecalux, makes it possible to assign a loading dock or exit buffer to each item to be dispatched.
The implementation of a software program in this process has the following benefits:
- Goods placement by truck route. The application establishes location criteria and rules adapted to the requirements of the product or company. Easy WMS, for instance, tells the operator to move the goods to a designated buffer or loading dock. From there, they will be loaded onto the corresponding truck. The aim of this is to personalize this operation as much as possible, planning the placement of the merchandise in line with the vehicle’s transportation route.
- Better weight and volume distribution in the truck. The optimal combination of boxes, pallets and/or other unit loads lets you maximize the vehicle’s capacity. The software also considers weight distribution to prevent imbalances and ensure that the vehicle doesn’t exceed the gross vehicle weight rating (GVWR).
- Anticipation of unloading needs. On occasion, a truck has to be unloaded in a specific order. The goods might not all be dropped off in the same place, or some might have to be offloaded before others so they can be dispatched first. These requirements must be taken into account much earlier, at the time the products are loaded. Here is where the software comes in, indicating which parcels to load first to ensure that those to be removed sooner are more accessible.
- Overcost reduction. A WMS guarantees full product traceability, preventing loading errors. The software assigns loads automatically based on preset criteria (route, license plate, or exit order, etc.) so that the parcel arrives at its final destination error-free. Eliminating these mistakes cuts reverse logistics costs.
In short, software streamlines dispatch tasks in the warehouse, doing away with delivery blunders and optimizing loading times for every truck.
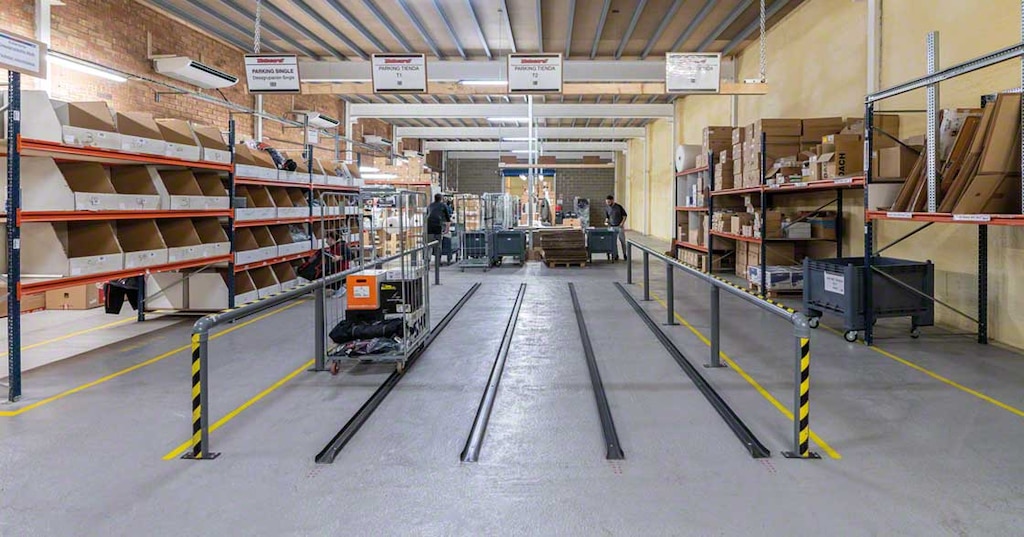
Automatic assignment of loading docks
One of the features of software such as Easy WMS is the management of truck loads by transportation route.
Let’s examine how this works. When products are slated to be dispatched, Easy WMS designates them to be sent to a buffer (a space where they are held beforehand) or directly to the loading dock. This decision can be made manually, by an operator, or the WMS can determine this automatically (based on predefined criteria).
During the order prep process, Easy WMS can assign each package to a certain buffer, in line with the exit order or preset route. Thus, the warehouse management system by Interlake Mecalux facilitates goods dispatch, distributing the cargo by designated carrier.
This operation can be performed via a small terminal or a workstation. To do so, users merely have to enter the pertinent data in the screen. Following a series of steps, they can create as many loads as required. Easy WMS will indicate to operators the dock where the loading will take place and, optionally, the license plate of the transportation vehicle.
Hence, software lets you configure loads automatically according to data previously entered into the WMS. On the basis of the exit order, the predesignated route, or the assigned transportation agency, Easy WMS creates a task directing the operator to bring the goods to the designated buffer. This guarantees that no package will be sent via the wrong carrier.
Swift, error-free dispatch
The implementation of software — particularly, a WMS — not only lightens the load of the workforce in goods dispatch, but also prevents errors, streamlines the operation, and ensures product traceability throughout the supply chain.
If you want to stand out from your competitors — eliminating delivery mistakes in your warehouse — don’t hesitate to contact Interlake Mecalux. An Easy WMS expert consultant will offer you the best solution for your particular needs. We can ensure you fast, error-free transportation to both customers and suppliers.