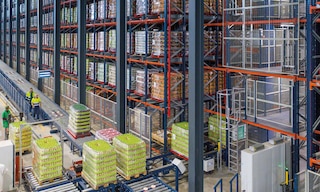
Tugger train: precursor to automated transportation systems?
A tugger train is a transportation system used to move large volumes of goods between different areas in the warehouse.
In logistics facilities and distribution centers with a high density of product inflows and outflows, however, this solution might not be the best choice. In this case, it’s advisable to replace manual handling equipment with automated transportation solutions such as pallet conveyor systems or electrified monorails.
What’s a tugger train?
A tugger train is a type of handling equipment made up of an operator-driven tow tractor (tugger) attached to a set of trailers or carts, each with an individual load capacity of up to 4,400 lb. Tugger train systems are used to accelerate the movement of stock along distances exceeding 330', speeding up the flow of goods between two different workstations.
These logistics transportation solutions stand out for their versatility, as tugger train carts are available in different configurations, adapting to any need. As a result, they can ferry all different types of loads across the warehouse, including pallets, boxes, large containers, parts, and tires.
These machines are also available as wire-guided AGVs (automated guided vehicles); with this configuration, the tow tractor design is the same, but the steering of the machine is automated by installing a magnetic field-emitting wire on the warehouse floor. The wire marks the path to be traveled, and the tow tractor follows it.
Tugger trains: benefits (and drawbacks)
A tugger train is a type of handling equipment similar to a forklift, the difference being that a tugger train can move a larger number of pallets on a single run. This is because the tractor can haul multiple carts simultaneously. This represents a huge advantage compared to other varieties of handling equipment, generally limited to handling one unit load at a time.
Compared to moving goods with pallet jacks or forklifts, this solution enables:
- Transportation of large amounts of product: a tugger train makes it possible to move a high number of loads between workstations or different areas in the warehouse under the supervision of a single operator or by means of a wire-guided machine.
- Flexibility in product handling: tugger trains consist of a tow tractor and a combination of several carts, which vary based on the demands of each customer. Cart configurations range from modules that carry standardized GMA or Euro pallets to others with a bridge frame for moving goods stored vertically.
- Safety and ergonomics: these machines are equipped with immobilizers, which are safety devices that prevent the train from moving when the trailers aren’t properly positioned or raised. Additionally, drivers can operate the lifting mechanisms with a foot sensor, making their work more ergonomic.
However, this solution could prove inefficient by increasing the density of incoming and outgoing stock in the warehouse. Although a tugger train’s load capacity isn’t low, it is limited. Moreover, the flow of goods it allows is always one-way, which is inconvenient when high levels of productivity are required.
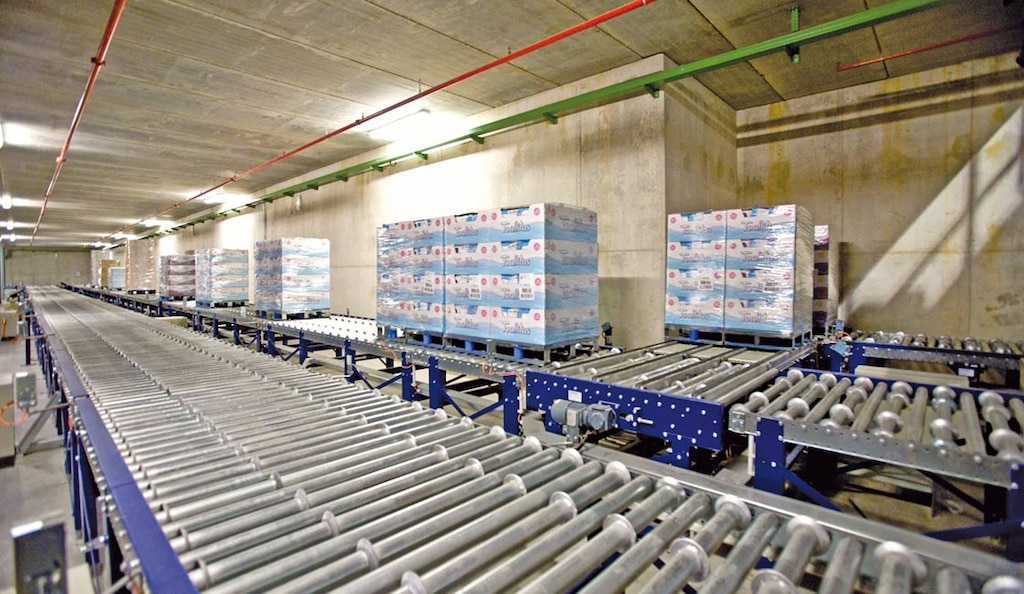
Tugger trains vs. automated conveyors
The main difference between tugger trains and industrial conveyors is the volume of products they can move simultaneously. While the load capacity of a tugger train is limited to the set of carts that make it up, systems such as pallet conveyors and roller conveyors for boxes, totes, and bins are designed to move larger quantities of goods nonstop.
Conveyors ensure a safer working environment: mesh enclosures prevent interaction between the operators and the machinery, preserving the integrity of the system, of the load, and, most importantly, of the employees. Nevertheless, in warehouses that work with tugger trains — whether operator- or wire-guided — the routes should be marked clearly so as to avoid impacts and accidents. This is crucial, since the area in which the vehicle travels is operator-accessible.
Both conveyors and tugger trains are known for their flexibility, as both feature a wide variety of elements that allow for configuring complex circuits, adaptable to the warehouse layout and to any type of customer demand. Wire-guided tugger trains, though, can sometimes force companies to redesign their warehouses in order to establish the routes to be followed by the machines inside and outside the facility. Pallet conveyors are a more productive and cost-effective solution to the need to set up routes: they can move greater volumes of goods along the same path with minimal maintenance.
In fact, conveyor lines can be built by means of modules with rollers, with chains, or a mix of both, depending on the pallet movements required. Plus, they run the gamut from simple configurations — such as plug & play, which is easy to assemble and requires no programming — to setups with more complex accessories, such as hydraulic tables, pallet lifts, and pallet retainers, to name just a few.
Moreover, while tugger trains only transport merchandise between two workstations located on the same level, conveyors make it possible to accumulate loads or move them between different heights in the facility.
For these reasons, conveyors for pallets are the ideal solution for a warehouse close to the production lines. This can be seen in the new Cistér facility in Portugal, where this automated transportation solution ensures that finished product is moved between the production lines and the warehouse continuously, without the need to assign an operator to this task. The software that coordinates the conveyor moves the goods that leave production and assigns them a location in the automated warehouse. These automated movements eliminate the possibility of bottlenecks on the production lines.
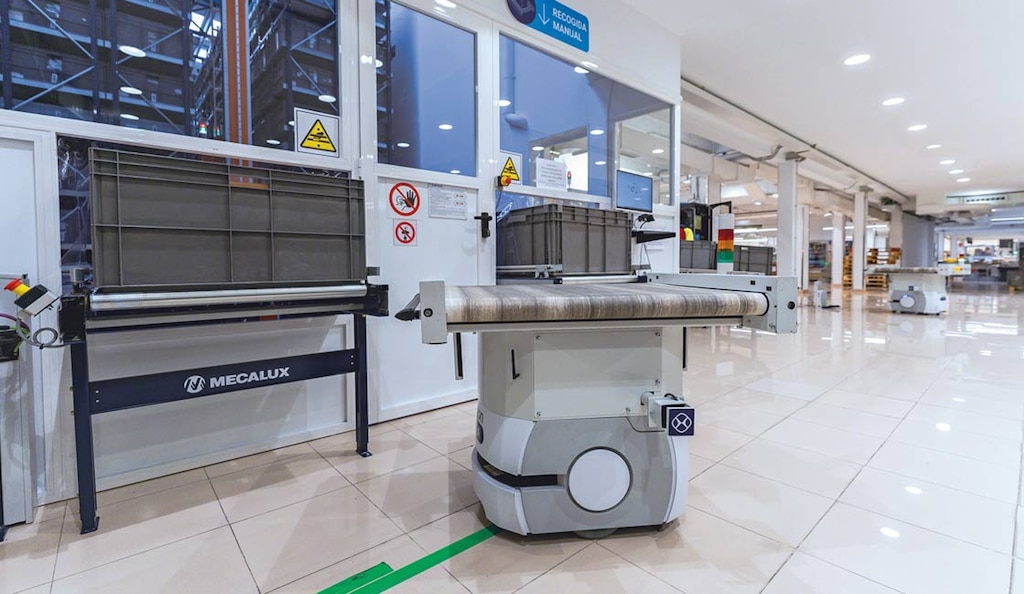
Tugger trains vs. AMRs
Tugger trains can be compared to another type of transportation system: autonomous mobile robots (AMRs). These machines can move through a facility on their own, transporting product without the need to establish a closed route. A control system, integrated in the warehouse management system (WMS), orchestrates the robot’s movements.
Unlike tugger trains, these robots generally move lighter loads, although there are models designed to transport palletized goods. They are used in ecommerce warehouses, for example, or in sectors such as pharma logistics, which works with small SKUs.
But despite their constant evolution, AMRs are not as technologically established as automated transportation systems. This means that their implementation in a warehouse still entails a hefty investment, whether for the purchase of the machinery or for periodic user licenses.
Tugger train: simple solution for a complex problem
Tugger trains are a means of transportation that can be effective for speeding up product movements, but only in certain contexts. In the end, they’re a natural evolution of the movement of goods via pallet jack, a type of manual handling equipment commonly used for loading and unloading trucks.
However, there are more efficient automatic transportation solutions on the market that, above all, guarantee maximum productivity in supplying workstations and/or production lines. Systems such as automatic conveyors are a flexible solution that can be adapted to the demands of any warehouse, greatly speeding up the movement of goods through the facility.
Interested in maximizing productivity in your warehouse? Don’t hesitate to contact us. Our team of experts will analyze your logistics performance and offer you a personalized solution.