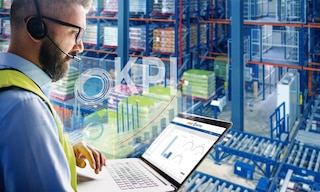
9 warehouse KPIs to measure logistics management
Warehouse KPIs are metrics used to calculate and control the efficiency of the logistics operations performed in a facility. These KPIs (key performance indicators) make it possible to identify strengths and weaknesses relating to stock management.
With these warehouse KPIs, logistics managers can monitor process throughput, find opportunities for improvement, and make decisions based on the real productivity of each area in the facility.
Warehouse KPIs to monitor logistics performance
There are multiple warehouse KPIs for managing logistics management. When choosing the metrics that will be decisive for knowing how storage, order fulfillment, and dispatch operations are being performed, several factors should be taken into account. These include the characteristics of the facility, the location of the goods, the type of product or unit load to be stored, among others.
These are some of the best warehouse KPIs for monitoring logistics performance:
1. Efficiency in goods receipt
This measures the productivity of the work done in the facility’s receiving area. This metric is useful for evaluating the performance of the transportation and storage systems, as well as operator training and the efficiency of the devices employed in the goods receipt process, for instance. A sensible receiving procedure reduces the risk of stock loss and simplifies operations such as storage and order picking.
The formula for measuring efficiency in goods receipt is:
Efficiency in receiving = amount of stock received / total number of hours worked
For example, if a company receives 480 unit loads a day and the warehouse operates in three shifts, the receiving efficiency would be:
480 / 24 h = 20 unit loads an hour
2. Loading dock occupancy
This KPI calculates the percentage of occupancy of the warehouse docking area during goods receipt, order dispatch, or both operations. Full occupancy of the loading docks could indicate to the logistics manager the need to expand the warehouse yard. The formula for this KPI is:
Loading dock occupancy = (loading docks used / available loading docks) x 100
Continuing with the case above, if only 5 out of the 7 available loading docks are used to receive the 480 pallets a day, the loading dock occupancy is:
(5 / 7) x 100 = a 71% loading dock occupancy while receiving tasks are being carried out
3. Stock turnover rate
This measures the quantity of times that procured goods become finished orders during a specific period of time (typically a year). In other words, this indicator calculates the number of times the products stored complete the entire business cycle (sale, dispatch from the warehouse, and payment collection). Generally, a high stock turnover rate is beneficial for the company, as a fast-moving inventory brings down storage costs.
Stock turnover rate = cost of products sold / average inventory value
For example, if the cost of the merchandise sold is $720,000 and the average inventory value is $120,000, the company’s stock turnover rate would be:
720,000 / 120,000 = 6. In other words, the business turns over its entire inventory once every two months on average, since the resulting stock turnover rate is 6.
4. Stockout rate
This KPI shows the percentage of orders that are not fulfilled due to a lack of sufficient stock to meet demand. Logistics managers have to keep this value down to a minimum to guarantee deliveries to customers.
Stockout rate = (number of unfulfilled orders due to lack of stock / total number of orders) x 100
If the average number of unfulfilled orders due to lack of stock is 60 a month out of a total of 450 monthly orders, the stockout rate would be:
(60 / 450) x 100 = a 13.33% stockout rate in the warehouse
5. Picking accuracy
This warehouse KPI calculates efficiency in order processing. A productive picking operation should have a numeric value as close to 100% as possible, meaning that orders are dispatched without errors and in the shortest possible time.
Picking accuracy = [(total number of orders - returns of incorrect items) / total number of orders] x 100
Thus, if a company shipped 5,400 orders last year and customers returned 350, the picking accuracy would be:
[(5,400 - 350) / 5,400] x 100 = a 93.5% picking accuracy rate
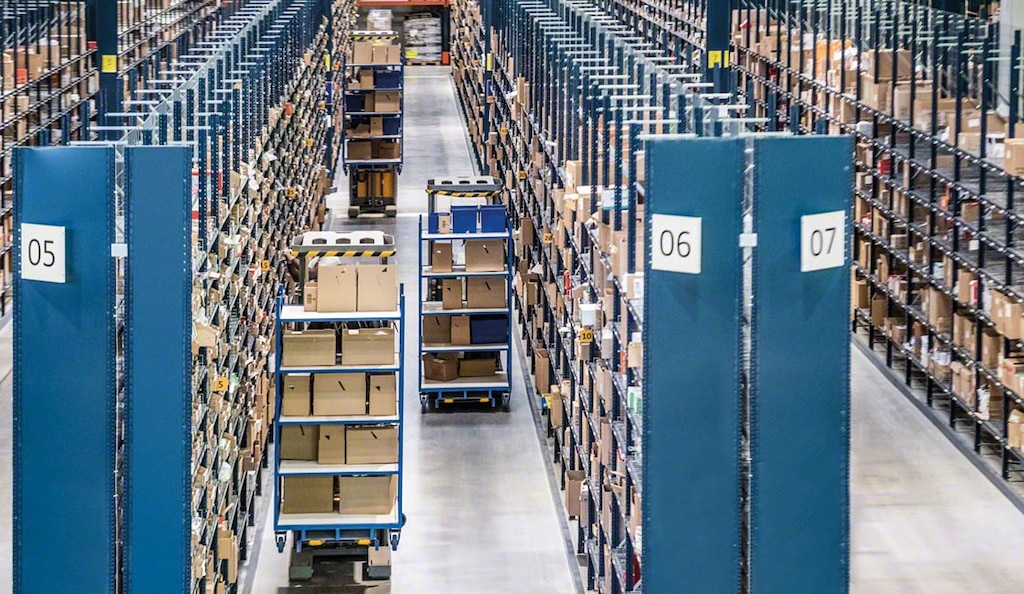
6. Backorder rate
This indicates the number of unfulfilled orders ― normally due to lack of stock ― out of the total orders the facility receives. In an efficient warehouse, this KPI will be as close to 0 as possible.
Backorder rate = (number of unfulfilled orders / total orders) x 100
If a facility can’t prepare 30 out of the 450 orders it receives every day because it doesn’t have enough stock on hand to fulfill them, the daily backorder rate would be:
(30 / 450) x 100 = a 6.6% backorder rate
7. Days sales of inventory
This KPI calculates the amount of time goods remain stored in the facility. Days sales of inventory (DSI) reflects the number of days a company takes to sell its warehouse stock. There is no target value for this KPI, since the optimal number of days will depend on the type of business, product, or facility in question. For instance, in a warehouse that stores perishable products, inventory that takes too long to turn over could become a problem.
Days sales of inventory = average daily inventory value / (value of goods sold annually / 365 days)
To work out this formula, you first need to obtain the average daily inventory value, which is calculated as follows: (beginning inventory value + ending inventory value) / 2.
Let’s take the following example: a company starts the year with an inventory worth $100,000 and ends the year with $140,000 worth of stock stored. If all the goods sold during the year amount to $720,000, the days sales of inventory are:
[(100,000 + 140,000) / 2] / [(720,000 / 365)] = 60.8 days sales of inventory, i.e., the average amount of time the inventory spends in the warehouse.
8. Cost per order
This calculates the monetary cost of each order for the company, from the minute the customer purchases the product until it’s delivered. This value takes into account the storage, order processing, and energy costs in the warehouse, among many others.
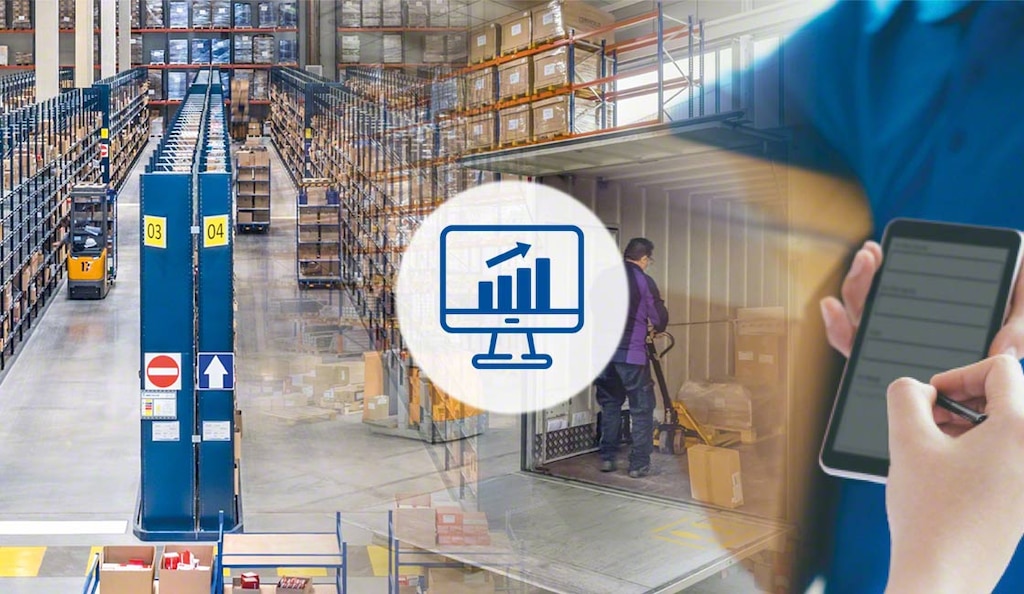
Cost per order = total warehouse costs / total number of orders shipped
Let’s take the case of a company with different costs relating to storage, product handling, and order fulfillment totaling $150,000 a year. If the company has dispatched 5,400 orders during that period, the cost per order is:
150,000 / 5,400 = a cost per order of $27.70
9. Delivery in full, on time (DIFOT)
This KPI denotes the percentage of complete orders that are shipped by the deadline agreed upon with the customer. The manager should plan the logistics strategy so that this value is as high as possible to ensure good logistics service.
Delivery in full, on time = (number of orders sent on time / number of total orders sent) x 100
If, out of the 5,400 orders a company fulfilled last year, 4,674 were delivered satisfactorily ― in terms of both the expected product and deadline ― the DIFOT percentage would be:
(4,674 / 5,400) x 100 = an 86% DIFOT rate
Software to measure warehouse KPIs
Warehouse management KPIs are becoming more and more complicated to measure and analyze manually. Nevertheless, supply chain digitization represents an opportunity for logistics managers: programs such as warehouse management software coordinate and monitor logistics operations, collecting all information produced in the facility.
To illustrate this with a real program, Easy WMS from Interlake Mecalux automates processes such as goods receipt, order picking, and product returns, telling operators via RF scanners which tasks they need to carry out at every turn. The software assigns product locations and operator pick paths based on efficiency criteria and rules predetermined by the warehouse manager.
Warehouse management software also incorporates advanced functionalities to adapt to the particular requirements of each customer. In this vein, the Supply Chain Analytics Software module from Interlake Mecalux segments and structures all the information generated in a facility. It then transforms this data into KPIs, enabling logistics managers to make better decisions.
Warehouse KPIs: essential for measuring performance
Warehouse KPIs are a key tool for measuring logistics throughput. They offer a real-time snapshot of how efficient your logistics operations are and how to detect improvement opportunities.
Digitization has equipped logistics managers with tools to monitor warehouse performance, measure process efficiency, and make decisions based on the throughput of each operation. Want to boost your facility’s efficiency? Get in touch, and one of our expert consultants will advise you on the right solution for your company.