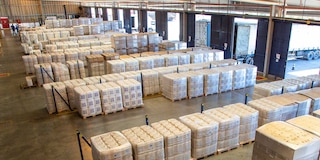
Optimal stock level: how to calculate it
Maintaining an optimal stock level in the warehouse is essential for having efficient logistics systems and avoiding extra storage costs. But what’s the exact number of SKUs you need for to effectively meet product demand without suffering from stockouts?
In this post, we take an in-depth look at optimal stock levels in logistics as well as the differences between this concept and minimum and safety stock levels. Plus, we break down the formula for making sure your inventory is in line with demand, the warehouse, and the steady growth of your company.
Optimal stock: what is it and how do you put it in practice?
In logistics, optimal stock designates the exact amount of inventory a business requires to fulfill routine demand without the occurrence of a stockout. In other words, it involves obtaining maximum profitability and bringing storage costs down to a minimum.
This concept shouldn’t be confused with average stock (or average inventory), which is the average number of SKUs in the warehouse. This number oscillates between the maximum stock level — which refers to the total items able to be stored in the facility taking into account the square footage and storage systems employed — and the reorder point or minimum inventory level, which defines the limit at which the company needs to procure more product.
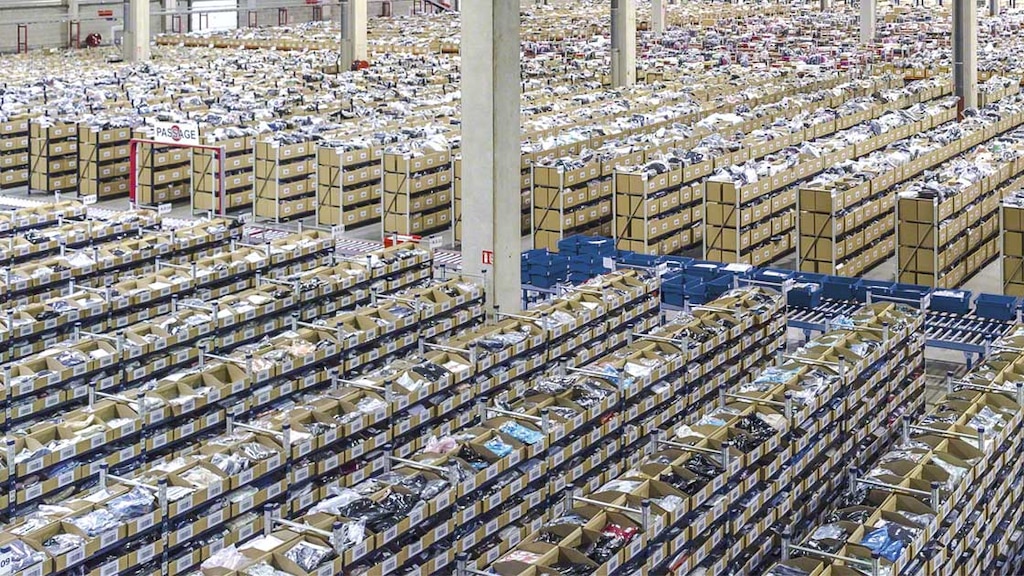
Ignoring the optimal stock level could lead to serious consequences for the warehouse
How to determine optimal stock levels
Which factors should the logistics manager consider to determine the optimal stock level? Although this depends on each firm’s particular strategy, these are the four main elements to bear in mind:
- Customer demand. The logistics manager, together with the accounting department and management, should analyze demand trends over the years, the demand forecast for each SKU, seasonal demand for each product, etc.
- Stock turnover. The manager needs to know the turnover for each SKU to properly manage goods slotting. The ABC analysis is a common method for organizing SKUs according to their demand.
- Product type. The characteristics of each product, as well as the company's business sector, will be fundamental when it comes to assessing optimal stock levels based on the storage systems installed. For example, food logistics, which calls for cold storage lest the goods expire, differs greatly from the warehousing of cables and pipes, whose products require specific storage systems that adapt to their characteristics.
- Maximum, minimum, and safety stock levels. With these three numeric values, you can calculate the optimal stock level for each SKU. Thus, the space, methodology, storage systems, and handling equipment will determine the maximum stock level, while the demand and capacity to manage each order will establish the minimum level. For its part, the nature of the business will designate the necessary safety stock in each facility.
- Lead time. The warehouse manager also has to know the lead time for each supplier. That is, the time elapsed from the moment a stock entry order is generated in the warehouse until the supplier delivers the product.
Against a logistics backdrop in which efficiency and the reduction of storage costs are increasingly important, ignoring optimal stock levels could result in major repercussions for the company. These might include inefficient storage processes, expensive overstock, and, above all, spoilage of warehouse stock, especially if this includes perishable goods.
Stock types: optimal, minimal, and safety
It’s impossible to understand optimal stock without first running through other concepts, such as working stock, safety stock, and the reorder point. Let’s examine the different types of stock according to logistics strategy:
- Available stock: this refers to the amount of stock in the warehouse that’s ready to be included in any order. All logistics processes are carried out on the basis of available stock, also known as working stock.
- Minimum stock: this is the minimum amount of each product the warehouse must have to respond to demand.
- Safety stock: every facility should have safety stock (sometimes called buffer stock) in order to prevent stockouts in the event of an unexpected rise in demand.
- Order point: numeric value established in the logistics strategy that determines when an order should be placed with a supplier. It lies between the minimum and optimal stock levels.
- Maximum stock: this concerns the amount of stock that must not be exceeded in order to keep warehouse operations running smoothly. It’s related to the facility's storage capacity and the business’s workforce.
Now that we’re clear on these concepts, we can calculate the optimal stock level. As mentioned earlier, this refers to the amount of inventory to maintain to ensure that the company obtains maximum profitability and can respond to both existing demand and any fluctuations that may occur.
Optimal stock level formula
Once the logistics manager has taken into account the considerations set out in the point above, he/she should use the optimal stock level calculation to know exactly how much of each item to store in the warehouse. To obtain this datum, we take the optimal order quantity and add to it the minimum stock and safety stock that should be on hand in the facility. This is how we get these variables:
The optimal order quantity is related to the EOQ formula (or Wilson model), which uses the amount and frequency with which orders are placed with suppliers to achieve optimal management of inventory and of raw material procurement. This numeric value is calculated using the formula below:

The optimal stock level formula is based on the EOQ formula
Where Q is the optimal order quantity, D is the annual demand for raw material, K is the cost of each order, and G is the cost of storing a product for a specific amount of time. As a result, thanks to the EOQ formula, the warehouse manager will know when an order should be placed.
Besides the optimal order quantity, we need to obtain the facility's minimum and safety stock levels. This formula determines a warehouse’s minimum stock level:

Minimum stock level formula
To this calculation, we need to add the safety stock calculation, which is determined using the following variables:
- Supplier lead time under normal circumstances (SLT).
- Maximum procurement lead time in the event of an incident (MPLT).
- Average product demand (APD).

Safety stock formula
Finally, the optimal stock level formula would be worked out as follows:
Optimal stock level = optimal order quantity + minimum stock level + safety stock level
Example of how to calculate optimal inventory level
Let’s illustrate the formulas above with a specific example. A steel company has a raw materials warehouse that supplies its production center with bolts. The company requires 80,000 bolts a year to manufacture the metal sheeting it sells.
Each order the firm places with its bolt supplier costs $100, while the cost of storing a bolt is about $0.05 annually. So what’s the optimal stock level of bolts the company should have in its facilities?
As seen above, the first step is to calculate the optimal order quantity. Using the formula, where K (the cost of the order) is $100, D (the annual demand) is 80,000 bolts, and G (the unit cost of storing a bolt) is $0.05, we obtain a Q of 17,888 bolts.
Q or optimal order quantity = √((2 × 100 × 80,000) / 0.05) = 17,888 bolts
Subsequently, to calculate the optimal stock level, we have to determine the minimum amount of stock there should be in the warehouse. To do this, it’s necessary to figure out how many bolts the company requires per unit of time (per day). If the company operates 250 days a year, it will need 320 daily units. Consequently, if the supplier’s lead time is just a week, the minimum stock needed will be 2,240 units.
Minimum stock = (80,000/250) × 7 = 320 × 7 = 2,240 bolts
To finish up, we’ll calculate the amount of safety stock the warehouse should have. If the supplier’s maximum lead time under abnormal conditions is 21 days, the conclusion is that the safety stock should be 4,480 units.
Safety stock = (21 − 7) × 320 = 4,480 bolts
Therefore, the optimal stock calculation is 24,608 bolts: the result of adding the optimal order quantity (17,888), the minimum stock (2,240), and the safety stock (4,480).
Optimal stock level = 17,888 + 2,240 + 4,480 = 24,608 bolts
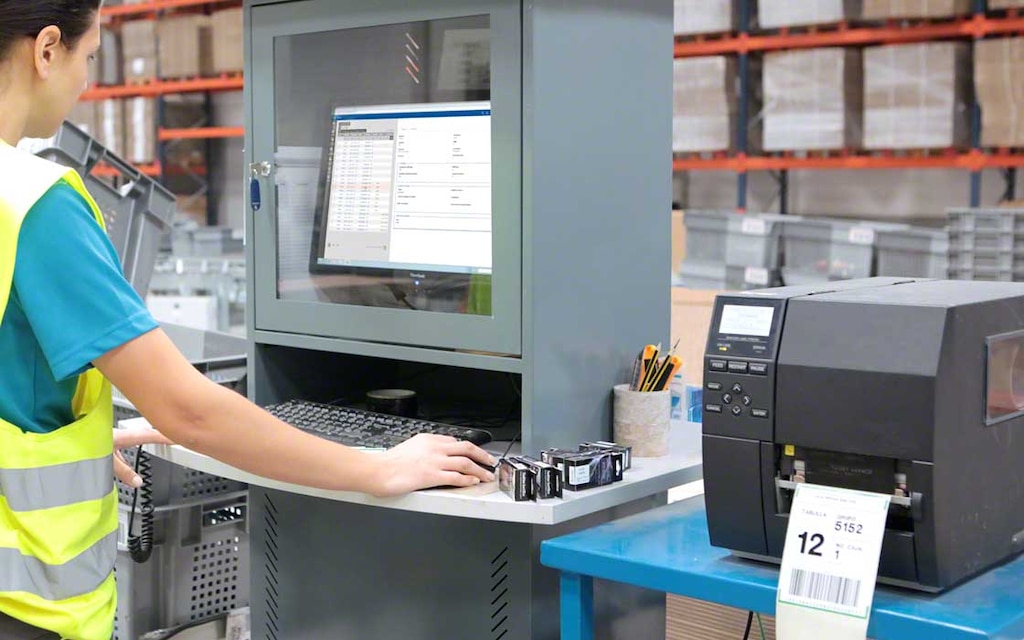
WMSs automatically organize tasks such as picking and stock replenishment
Digitization of optimal stock levels
The digitization of logistics processes has made it possible to automate multiple tasks that used to lead to mistakes and cause operators to lose valuable time. The implementation of an ERP (enterprise resource planning) system is key for integrating order management in the warehouse and knowing the demand for each product and the lead time of each provider, among other data. In the end, it helps the logistics manager to calculate optimal stock levels and the optimal order volume for each supplier.
Once you’ve determined the optimal stock levels for each SKU, a warehouse management system (WMS) can automatically prioritize processes such as replenishment at the pick stations, the receipt of inbound orders, and even management of the production lines at the facility.
Moreover, these applications calculate the optimal stock levels for each SKU, which will automatically generate replenishment tasks for products below the preset limit. As for warehouse slotting, a WMS automatically assigns each product a location based on its attributes (turnover, batch, and expiration date), minimizing errors and boosting productivity in the facility.
Accuracy and flexibility: the crux of Logistics 4.0
With logistics and industry becoming more and more demanding, logistics managers are forced to cut costs in storage and order prep processes to be more competitive. For this reason, using tools such as optimal stock levels eliminates errors and overcosts, guaranteeing enough inventory to satisfy the demand for each SKU without incurring unnecessary costs.
All the same, a growing number of logistics managers are implementing solutions to automate stock flows. Once you’ve calculated the optimal stock level, a WMS, together with an ERP system, enables you to schedule orders to suppliers and sequence replenishment tasks, in addition to a host of other advanced features.
At Interlake Mecalux, we offer Easy WMS, a WMS with multiple applications in the logistics sector. If you’re interested in ramping up the efficiency of your business’s processes and optimally monitoring stock, be sure to get in touch. One of our expert consultants will advise you on the best digital solution for your company.