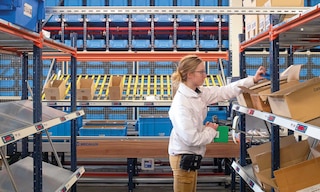
WMS hardware: Devices for warehouse optimization
Complementing a warehouse management system (WMS) with hardware expands the capabilities of these software solutions, which are designed to enhance productivity and efficiency in logistics facilities.
What is warehouse equipment for WMSs?
WMS hardware refers to external or internal devices and equipment that enable the input or retrieval of data for storage, communication, or processing beyond what WMS software handles. When a WMS and hardware work together, warehouse associates can receive instructions for tasks such as slot assignment or task sequencing through headsets, RF scanners, or other devices.
Therefore, WMS hardware is an asset for receiving goods, locating them in the warehouse, and fulfilling orders for shipment. Leading solutions, such as Interlake Mecalux’s Easy WMS, integrate seamlessly with major hardware and ERP systems. This makes it much easier to manage large inventory volumes and helps businesses adapt their logistics operations to the demands of omnichannel strategies.
What hardware do I need for a WMS deployment?
WMS software oversees a company’s logistics processes, intervening in all operations. To provide a real-time, comprehensive, and transparent view of every link in the supply chain, a WMS deployment requires certain essential components.
Type of hardware | Description |
---|---|
Internet connection | These web-based applications require an internet connection. RF scanners can run via Wi-Fi or 4G. |
RF scanners | A WMS like Easy WMS sends tasks directly to associates’ mobile RF scanners, eliminating the need for verbal instructions or paper documents. |
Label printer | This device produces labels that RF scanners can read. |
Document printer | This equipment generates delivery notes or packing lists from Easy WMS. |
Computer or tablet | While not indispensable, these are useful for fine-tuning operations. They’re recommended for logistics managers and chief supply chain officers to monitor inventory flow and plan strategies. |
Server (internal or external) | Businesses must choose between software-as-a-service (SaaS) or on-premise deployment. The SaaS model runs in the cloud, while the on-premise option is installed on a server within the company’s facilities. |
WMS hardware to optimize warehouse operations
As goods arrive at a facility and are unloaded, associates verify each delivery’s contents to ensure that quantities and SKU codes are correct. However, manual inventory counting and inspections can be time-consuming. This is where RFID technology can come in handy.
Glove barcode scanners can also streamline the goods-receiving process when used alongside a WMS. These wearables eliminate the need to hold an RF scanner, enabling associates to identify products more quickly.
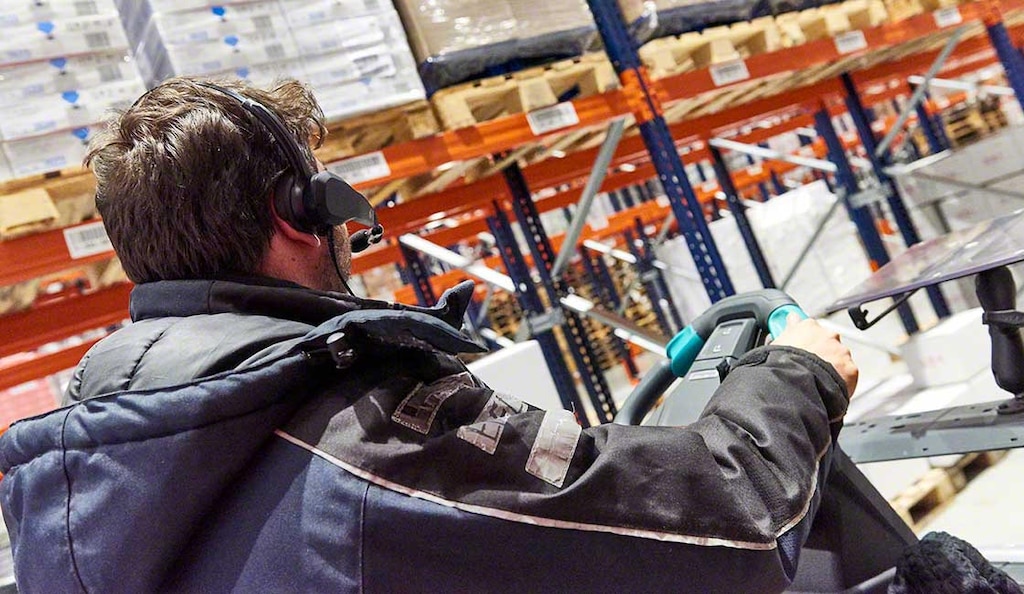
What equipment is crucial to realize the full potential of a WMS?
Although not essential for the basic operation of a WMS, the devices listed below enhance operational efficiency in distribution centers and greatly speed up workflows:
- Pick by voice. Voice-directed warehousing systems guide associates through order picking using audible instructions, allowing them to work hands-free. Synced with a WMS, this technology is commonly used for receiving, picking, storage, sorting, replenishment, cycle counting, returns, and even audits.
- Pick-to-light systems. Some carton flow racking systems feature numeric displays with buttons controlled by a WMS. When the light is on, it means the associate should retrieve goods from that channel, while the display indicates the exact quantity to pick. This technology is particularly helpful for batch picking.
- Put-to-light. Assisted picking with a put-to-light system uses LED indicators to show associates where to place products and how many units to include per package or tote.
- RFID devices. This system relies on smart tags that function as radio transponders, receiving and responding to signals. The tags contain product information that can be read across the supply chain.
- Glove scanners. These smart wearables automatically capture barcodes during the picking process. They do away with the need for associates to locate barcodes manually, allowing them to work with both hands.
Other optional tools can also be advantageous in certain industries. For example, scales and measuring instruments integrated with WMS software can give businesses a competitive edge.
Make the most of your hardware with Interlake Mecalux’s WMS
Our company created Easy WMS to boost throughput in both manual and automated warehouses. Hundreds of clients leverage its capabilities daily to run their operations, which is why a team of over 400 engineers dedicated to software development ensures it is constantly updated. Be sure to contact us for expert advice on this and other storage solutions.