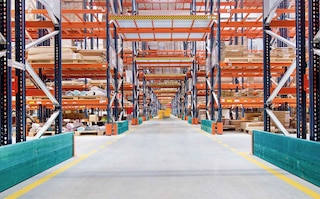
Safety stock: what is it and how can I optimize it?
Safety stock is additional inventory stored in the warehouse in order to deal with contingencies related to changes in demand or supplier delays. The objective of safety stock is to prevent stockouts.
All depictions of stored stock show peaks (when new goods are received) and valleys (when products are dispatched). This is illustrated below:
Graphic representation of stock levels
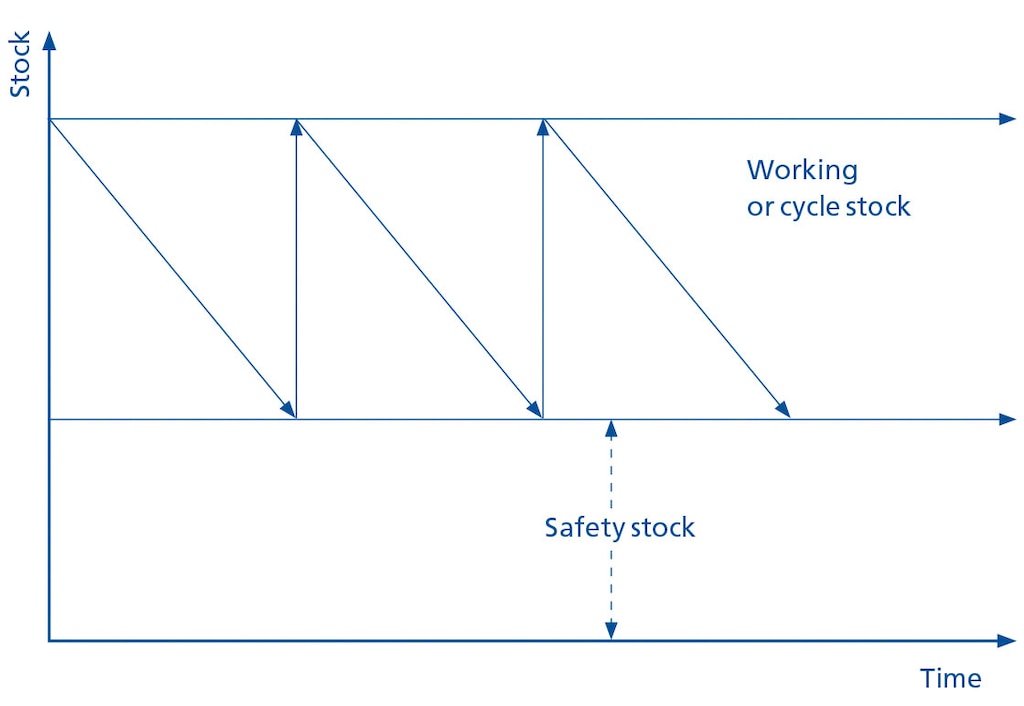
To control the variations that demand imposes on available stock, two key concepts are used: safety stock (defined above) and minimum operating stock.
Operating, working or cycle stock refers to the amount of inventory used to cover demand during a given period. It remains above the safety stock level.
When your inventory dips down towards the safety stock level, you know it’s time to place a new order with the supplier (this is known as the reorder point).
How do you calculate safety stock?
Safety stock is calculated according to mathematical formulas that combine the different variables affecting this value. In any case, this process has become increasingly automated through the implementation of software with stock management functionalities, such as warehouse management systems.
The standard method, nevertheless, is to consider safety stock as a percentage of working stock. This percentage is determined based on sales figures and sales forecasting (demand forecast calculations).
To grasp the definition of safety stock in full, it helps to examine the factors impacting it:
- Demand fluctuations:
Although your company has an optimized demand forecasting strategy, consumption can sometimes be erratic and difficult to control. Nowadays, demand volatility is greatly exacerbated by market ups and downs, the emergence of new products and the actions of competitors, among other elements.
And then there’s product seasonality, which also has a direct effect on stock levels. Demand variation, then, is calculated by finding the difference between maximum and average sales figures in a given period (thus, sidestepping seasonal fluctuations).
- Supplier lead times:
In logistics, lead time refers to the estimated time it takes for a provider to supply the goods ordered by the warehouse. Normally, the company will have scheduled a specific delivery time with the supplier. Nevertheless, you have to add on possible delay time, which is when safety stock comes into play.
For example, a supplier has an average lead time of 10 days; however, weather conditions have cut off roads, and the products are 3 days late. While this incident is being dealt with, it’s the safety stock that will be able to satisfy demand up to the time the goods arrive at the warehouse and inventory can be replenished.
- Company service level
Level of service relates to meeting demands and is characterized by what the customer expects from the business. Having a good level of service means that the installation can deliver the product requested by customers the moment they need it. This is the inverse of the stockout indicator.
The decision regarding what level of service to provide depends on the company’s business policy, the type of product, and the sector in which the firm operates. For instance, in e-commerce logistics, the different lead times are very tight. This is because the market pressures companies to have an exceptional level of quality service.
The risk and the importance of safety stock
Storing safety stock is a strategy that’s become vastly popular in the logistics sector. After all, no one wants to operate in an uncertain situation, and this extra stock extra prepares the company in the event of unforeseen incidents.
Be that as it may, traditional mathematical approaches for calculating inventory levels have used formulas with very limited and somewhat rigid variables, while the logistics environment has only become more complex.
In this context, companies cover risks by increasing their safety stock in a uniform way, which easily leads to overstocking. The effects of this excess inventory have a direct impact on logistics storage costs and the firm’s financial situation.
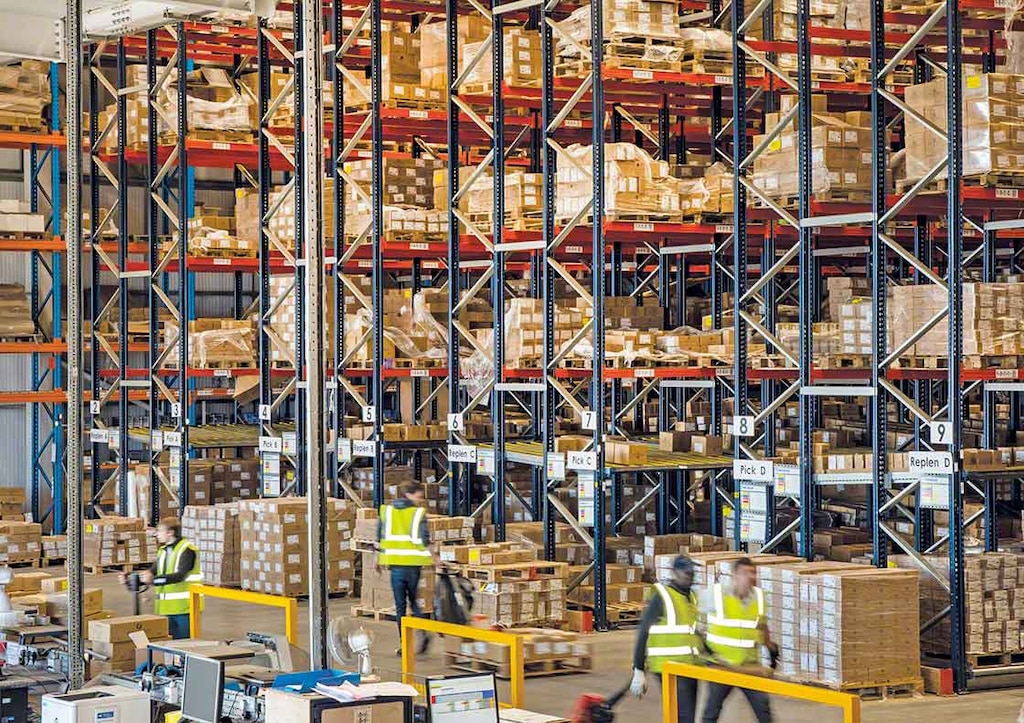
How to avoid having too much safety stock
Let’s take a look at some strategies for keeping safety stock levels under control:
1. Don’t adjust your safety stock uniformly
As market volatility has created much more complex scenarios, these somewhat rigid methods have proved imprecise — they’re incapable of adjusting the safety stock to a demand that’s different and extremely variable for each SKU in the installation.
In this situation, the goal is to come up with a combined formula that takes into account all the variables. When you have thousands of SKUs in your installation, as is becoming the trend, you may ask yourself: how can I adjust my safety stock levels to cover risks without going overboard? The solution lies in new technologies related to big data in logistics.
On the market, you’ll find software programs that enable you to process an enormous amount of logistics data and parameters and leverage them in a way that’s relevant to decision making.
In fact, this is one of the most significant AI applications in logistics; through machine learning and data mining, these programs can provide the key to calculating the right amount of safety stocks and prioritizing SKUs that are particularly important for the welfare of the business.
2. Improve processes and elements that you can control
Every supply chain faces continual uncertainty and unexpected circumstances on multiple levels: procurement strategies, sales forecasts, planning in conjunction with suppliers, etc. It’s understandable to want high levels of safety stock. After all, this bolsters the operation of the company in the face of unpredictability.
However, many logistics managers fall into the trap of centering their efforts on getting their demand forecast calculations right while continuing to operate with high levels of safety stock “just in case.” In this vein, it’s much more effective to focus your attention on variables that can be controlled from within.
For example, cutting internal lead times helps reduce cycles, limit wasted time and eliminate duplicate tasks. The warehouse is a natural source of optimization, as materials handling usually takes up a lot of time, and organization might not be up to snuff.
To mitigate these inefficient hot spots, many firms have decided to automate processes in the installation or implement warehouse management software to eradicate errors and streamline operations.
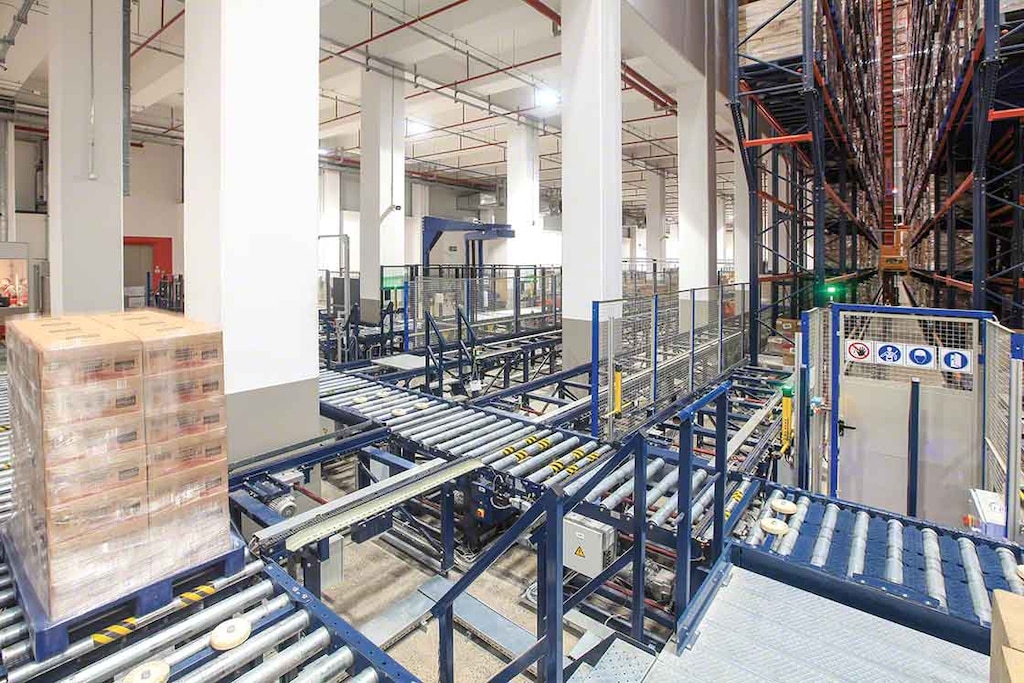
3. Control your stock levels with warehouse management software
On occasion, stockouts occur because the management of information regarding the company’s stock is flawed. For example, imbalances between the data in the records versus what’s actually stored in the installation are a major source of headaches for logistics managers.
Therefore, the role of warehouse management systems is fundamental for precise stock control and to ensure appropriate levels of safety stock: neither too high nor too low.
Mecalux’s Easy WMS software lets you:
- Limit human error and achieve fully accurate information on registered stock data and the location of products in your installation.
- Have a historical record that facilitates the calculation of estimates as well as learning for the future.
- Carry out an exhaustive inventory control showing the amount of safety stock actually needed thanks to its classification, based on logistics parameters.
- Detect incidents in time and schedule notifications to place new orders.
Traditional inventory policies started from a rather rigid premise in which stock calculations were done using limited variables. Flexibility in warehouse organization and stock management are trump cards in today’s logistics scenario. Do you think you have too much safety stock? Get in touch — together, we’ll come up with a solution tailored to your needs.