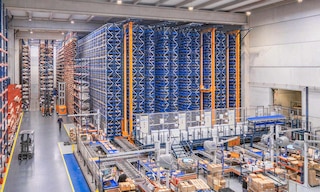
Inventory costs: Calculation and reduction strategies
Any company with logistics operations incurs inventory costs. Understanding their quantity and keeping them under control is critical for business viability.
What are inventory costs?
Inventory costs encompass all expenses associated with procuring, storing, and managing warehouse stock throughout its lifecycle. They go beyond manufacturing and purchasing tasks, covering factors such as storage space, labor, and shrinkage. Accurate inventory forecasting — in terms of total value and composition — is crucial for meeting customer demand.
Costs associated with inventory
Broadly speaking, inventory management costs fall into three main categories:
- Ordering costs. Every purchase order, no matter how small, carries a cost. This is why it’s important to track requests, invoicing, labor expenses, and transportation and processing fees.
- Carrying cost. In inventory management, carrying or holding costs refer to the expenses a company incurs to store items, whether in its own facility or a third-party warehouse.
- Stockout costs. These account for the potential losses a business faces if an item is out of stock when a customer requests it. Stockouts can lead to lost sales or drive customers to competitors. To mitigate this risk, some companies maintain safety stock to handle unexpected demand fluctuations.
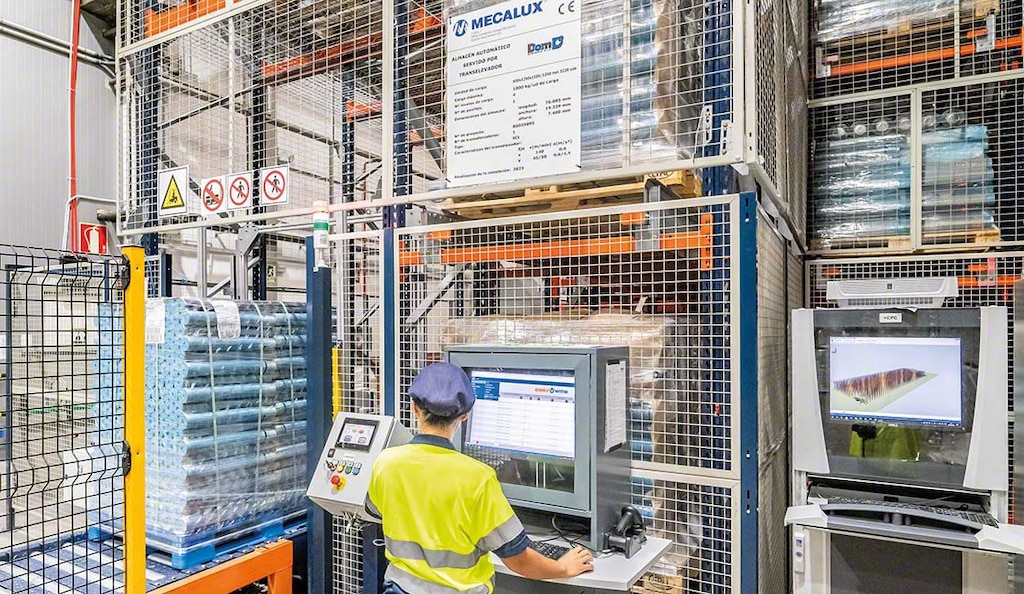
Fixed and variable inventory costs
Before calculating and considering how to optimize your inventory costs, it’s necessary to differentiate between fixed and variable costs:
- Fixed costs. These refer to expenses not directly related to the stored goods. Fixed inventory costs include personnel expenses, the value of infrastructure, and the tools and supplies required for the facility’s operations.
- Variable costs. These increase proportionally with the level of inventory. They cover expenses associated with order picking, packaging, and transportation. If your logistics operations are outsourced, variable costs might include your supplier’s per-pallet charges.
How to calculate inventory costs
To calculate your inventory cost, you need to know the cost of capital, risk costs, and maintenance costs your company has to bear.
- Cost of capital. These are the expenses a business incurs when it borrows money to purchase raw materials or products. They can fluctuate depending on interest rates.
- Inventory risk cost. Similar to inventory shrinkage, this accounts for losses due to obsolescence, fires, theft, or any kind of dead stock.
- Handling and maintenance costs. These are associated with goods handling and transportation.
Once you’ve identified these costs, you can apply the inventory cost formula:
- Inventory costs are the sum of the investment in raw materials or products, capital costs, risk costs, and handling and maintenance costs.
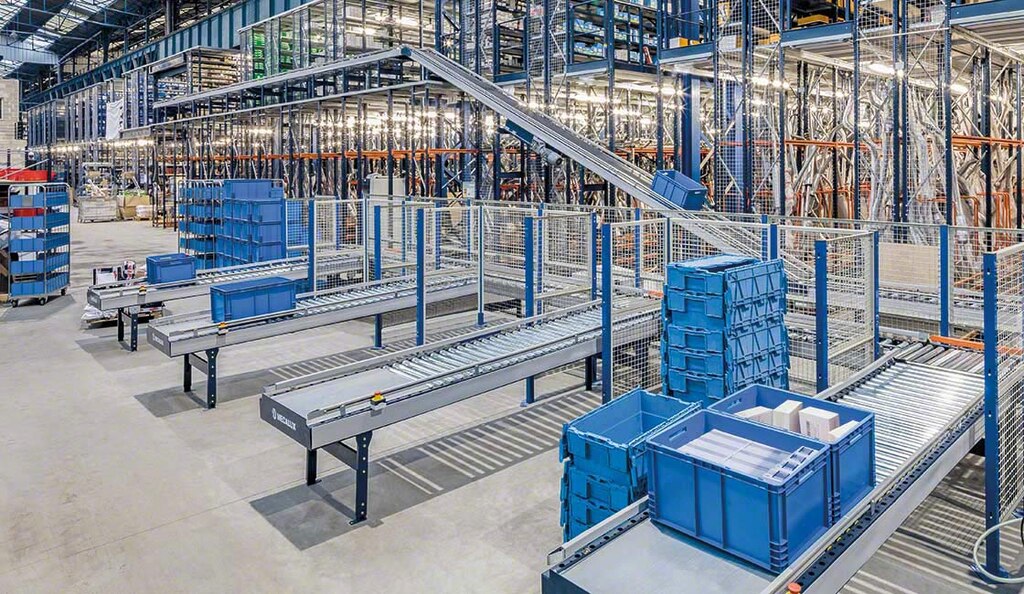
How to minimize inventory cost
Although there will always be some costs, one of the most effective ways to keep them down is to implement warehouse inventory management software to track stock. Interlake Mecalux’s Easy WMS, for instance, assigns locations intelligently, sequences tasks, and automates information flows. Additionally, it integrates with the leading ERP systems on the market and various automated and robotic intralogistics solutions. Below are some ways to reduce inventory costs.
- Improve demand forecasting. The more information you have about consumers’ purchasing intent, the easier it will be to limit overall inventory needs and provide fast, reliable service.
- Systematize data management. WMS software acts as the warehouse mastermind. It eliminates the need for manual data collection, minimizing the risk of errors.
- Automate processes. Automated solutions for product receiving, storage, and shipping make tasks more efficient, speedier, and safer.
- Adopt the just-in-time (JIT) system. This method involves storing only the essential quantity of goods or raw materials at the right time and in the right space, without excess inventory. JIT reduces the risk of obsolescence, though it requires optimal coordination to work properly.
- Hold your suppliers to high standards. Your business partners should follow your company’s best practices and deliver the required products on time, fulfilling their commitments. The ultimate goal is to provide customers with excellent service.
Control your inventory costs with Interlake Mecalux
Warehouses and distribution centers are the heart of the supply chain. Therefore, to maintain a competitive edge, it’s vital to monitor their operations to ensure they run efficiently. It can also be beneficial to automate the most frequently used spaces, such as the inbound and outbound areas.
Easy WMS currently manages logistics operations in over 1,100 warehouses across 36 countries, maximizing companies’ supply chain performance. As experts in warehouse automation and control, we also provide visibility to large distribution networks through our Easy DOM system. Contact us so we can share with you the extensive intralogistics experience our company has gained since 1966.