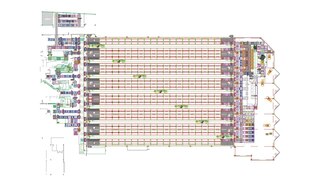
Best-in-class warehousing zones
When it comes to optimizing warehouse operations, pin pointing areas to improve is crucial for working out solutions at heights. Sometimes, a company’s circumstances will require a redesign or reorganization of the entire warehouse. However, before carrying out such a large-scale initiative, it is worth assessing whether or not you are making the most of each warehouse zone.
Tips for improving each warehousing zone
Let’s look at some best-in-class strategies for each warehouse zone:
1. Product storage area
All warehouses strive to maximize their effective capacity and prevent vacant locations from gathering dust. Three strategies stand out from the rest:
- Harnessing space at heights: when a warehouse surface is fully occupied, adding storage levels overhead is a very common solution. And, this is usually tied to automated systems, such as the installation of stacker cranes, as they are more versatile and safer than manual equipment.
- Reducing or directly eliminating space devoted to aisles: this measure will be affected by the constraints of the handling equipment used and also the type of activity done in the warehouse. For example, reducing aisles with compact storage systems or mobile shelving can double your effective capacity, but at the same time it will limit direct access to each individual unit load.
- Adapting storage systems to load types: standardizing your unit load type will pave the way for implementing this strategy. For example, if you regularly handle small products, adjust the slots in your racks to their dimensions.
2. Pick and prep zones
The more important picking and order prep operations are, the more focused your pick zone configuration must be in your warehouse. In fact, there are warehouses whose entire operation revolves around pick tasks. Such is the case of the French company Van Heck Interpieces, which can be used as a blueprint to outline some very useful improvement strategies for picking zones:
- Adjust your slotting strategy, i.e. product placement, to each product’s rotation and size, among other logistics parameters (hazard level, temperature, etc.).
- Improve the connection between zones and save on trips around your facility with automated solutions such as box conveyors.
- Optimize picking equipment: racks with direct access to goods, order picking and packaging stations.
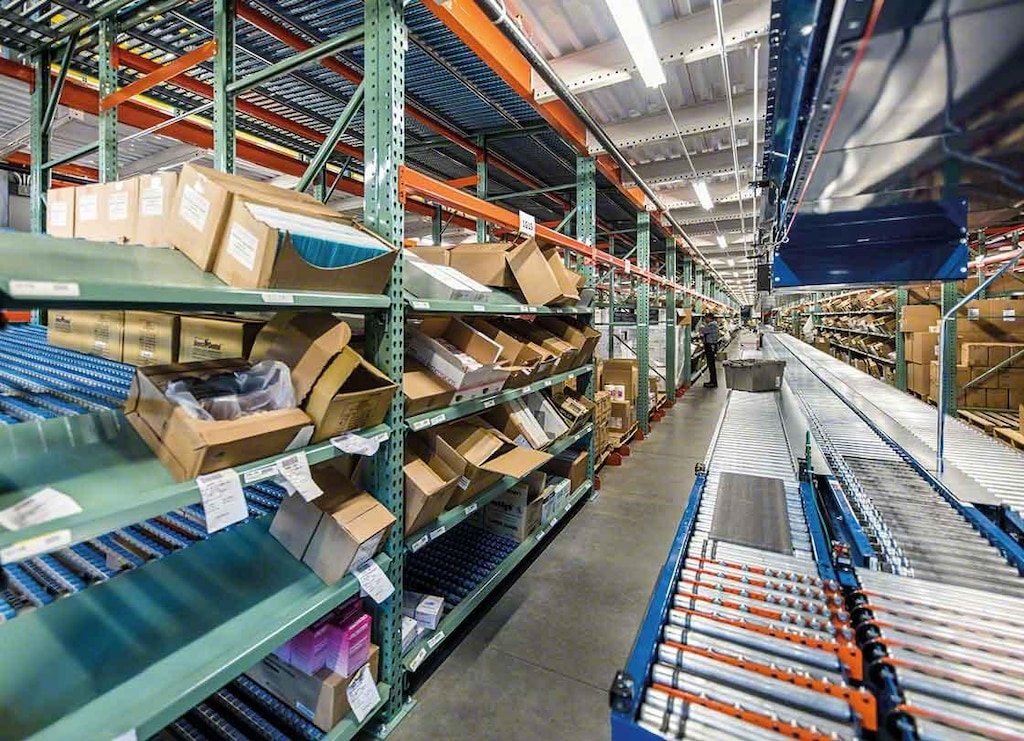
3. Zones to load, unloading, receive and dispatch
The loading/unloading zones and those engaged in the reception of goods and dispatches share a common goal of ensuring that goods flow smoothly and quickly at all warehouse access points. To make it happen:
- Control traffic at loading docks: proper planning avoids build ups or having trucks to stop and waiting. Loading and unloading automatization and a warehouse management system make this task much more straightforward.
- Designate quarantine or reserved zones: set these up near the docks for quality control of incoming and outgoing orders. But, goods on standby must not stop personnel from moving around freely.
4. Technical area for handling equipment
Technical zones are spaces allocated to charging batteries of the handling equipment and for their maintenance. These must comply with the strictest safety standards, both in location (e.g. in cold stores they must be located outside the chilled storage area) and in the appropriate environmental conditions. You can find out more about this issue in our article on handling systems batteries.
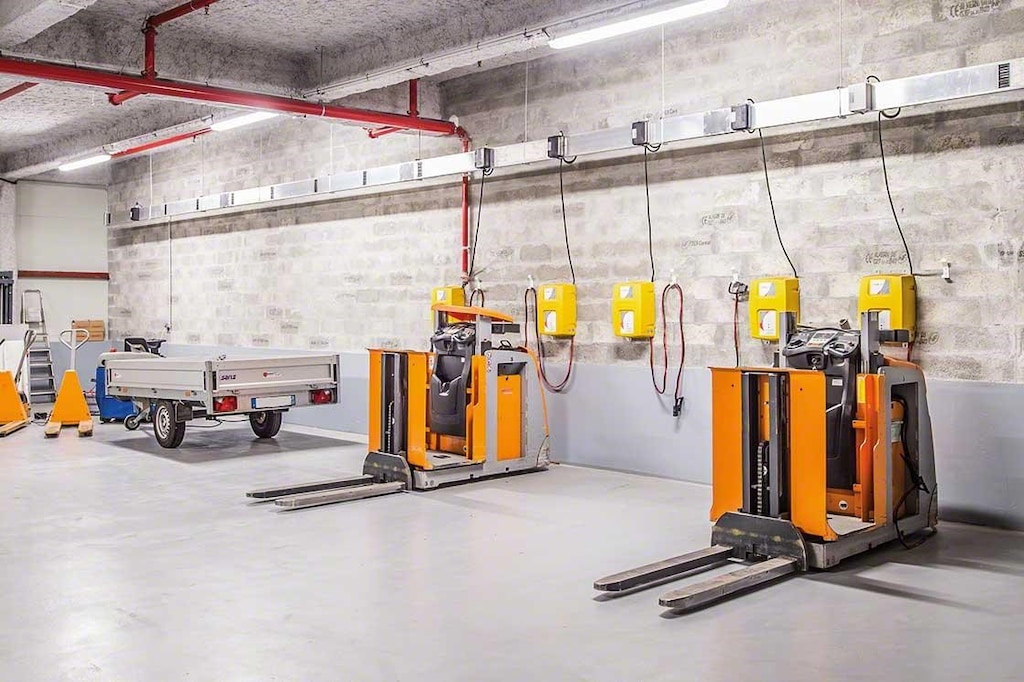
5. Admin and warehouse management zone
Every warehouse needs to have a zone reserved for admin tasks. Business offices:
- These zones must be set up in your own storage facility so that managers do not lose touch with the day-to-day running of the warehouse. They can either be at ground level or on an upper floor overlooking the storage area or loading and unloading areas.
- Admin and management areas need a powerful computer connection to the company’s server (especially if your WMS follows the on-premise deployment model), as well as the rest of the computers installed in the warehouse.
In short, a warehouse’s layout is one of the cornerstones of the entire storage installation's operations. Analyzing each warehouse zone on an individual and thorough basis helps identify room for improvement. If you want advice from one of Mecalux's experts, don’t hesitate to get in touch.