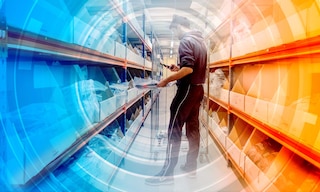
Cluster picking for speedy order fulfillment
Cluster picking is an order picking technique that cuts down on picker travel in the warehouse, thus optimizing throughput.
To apply cluster picking, it’s advisable to implement a digital program such as a warehouse management system (WMS). This software coordinates the execution of picking tasks, organizes routes, and shows pickers how many products to retrieve and which bin to place them in at every turn.
What is cluster picking?
Cluster picking is an order picking strategy whereby pickers collect products for several orders simultaneously. The operators separate the products into various containers, limiting their trips in the facility.
This picking method optimizes operators’ productivity by having them pick merchandise for different orders concurrently. Although there are other ways to perform cluster picking ― with lifts, vertical conveyors, or carousels ― the most common is to use a picking cart with multiple bins.
Cluster picking typically works like this: operators move through the picking area with a cart ― pick to cart ― containing several containers, all marked with a number. The picker collects the products and deposits them in the container indicated by the software, curbing unnecessary travel.
According to the research article Order batching optimization for warehouses with cluster-picking by authors from the University of Ohio and DHL Supply Chain, cluster picking is a method “where multiple complete orders are grouped in a batch, requiring the picker to sort the items into their designated bins on the picking cart during the picking process. Evidently, each pick cart can only hold a finite number of bins, where each bin corresponds to one customer order.”
What are the differences between cluster picking and batch picking?
Cluster picking is often confused with batch picking. With batch picking, operators place the products in the same container and later separate them into different orders. Cluster picking is a system in which operators sort the goods in separate bins, completing multiple orders on a single trip.
Whether to use batch or cluster picking will depend on your operational requirements, your level of warehouse automation, and the types of SKUs stored in your facility.
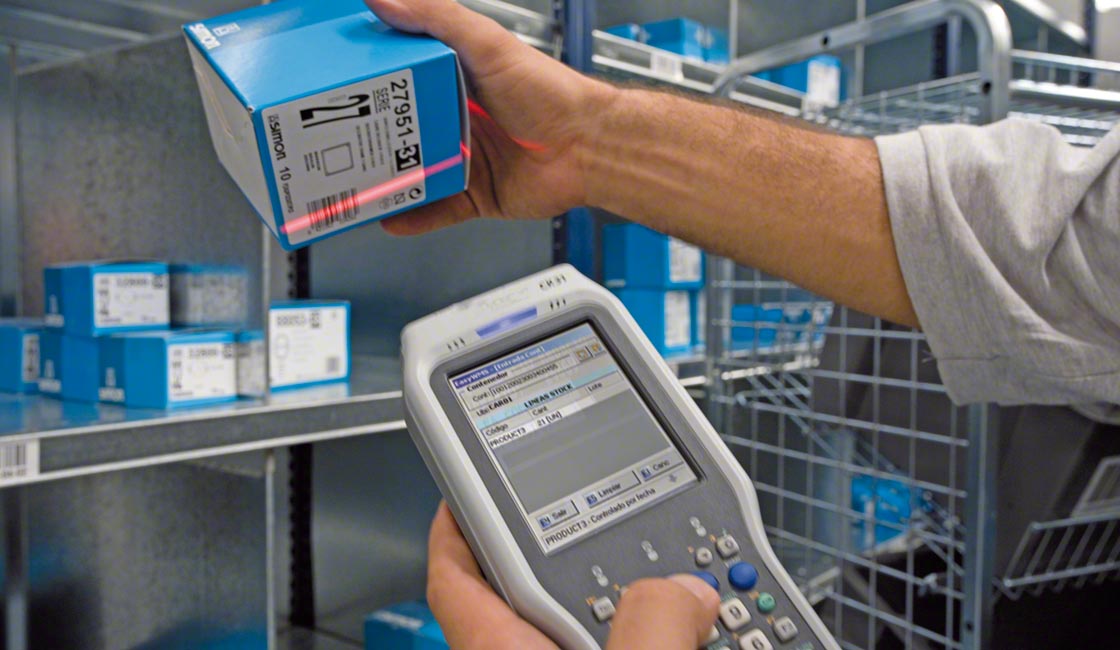
Advantages of cluster picking
Cluster picking is an order picking technique that optimizes operators’ productivity, as they can collect products for multiple orders on a single run. These are its main benefits:
- Elimination of unnecessary trips: it limits operator travel during picking, one of the least productive logistics operations.
- Increased picking throughput: operators can complete multiple orders at once, expediting picking.
- Error minimization: cluster picking can be performed in conjunction with WMS software. This guides operators, showing them which items to retrieve and which orders to fill.
Nevertheless, cluster picking makes order picking more complex, especially in facilities with a wide variety of SKUs, such as an e-commerce center. The key to boosting warehouse performance is to complement the WMS with goods-to-person systems. These automated solutions reduce operator travel by bringing products to pick stations where orders are put together.
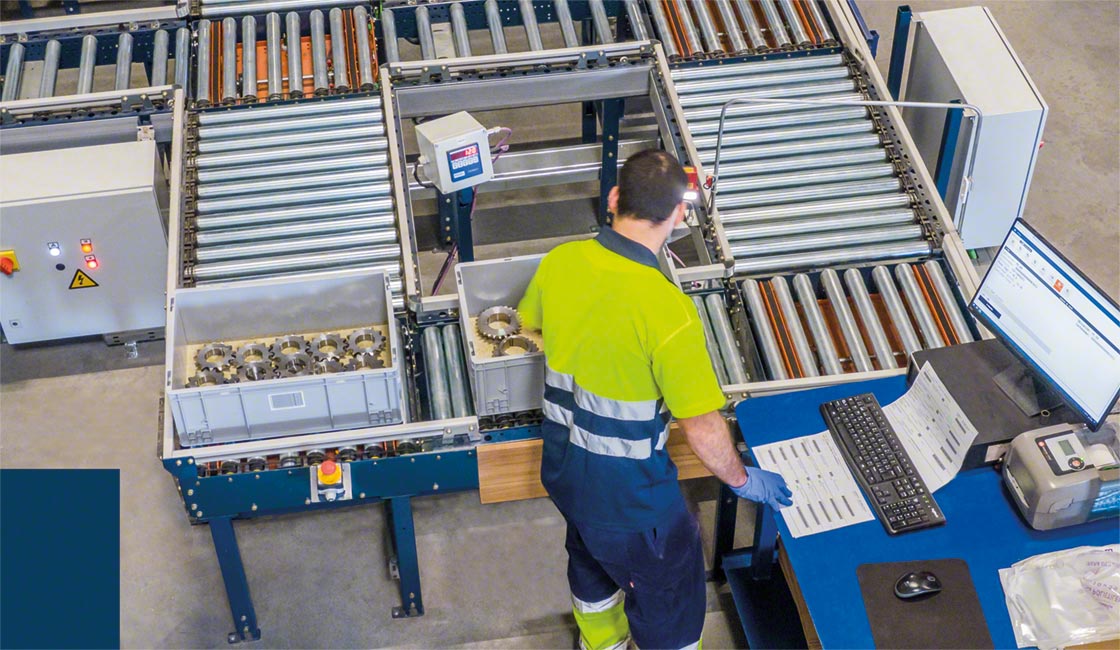
WMS: the pillar of cluster picking
Cluster picking can be performed in manual facilities without the help of a WMS. However, the complexity of this technique could increase the risk of error. To minimize mistakes, the cluster picking strategy is typically combined with the implementation of a WMS. This software directs operators as they move along their paths, continuously indicating which products and quantities to pick.
Paper-based cluster picking is less accurate: in managing many items simultaneously, pickers could pick or place the wrong item in the bin. This calls for subsequent checks to be performed, which tends to push up costs.
In cluster picking, WMS software plays a vital role: it helps pickers during the order fulfillment process. The WMS guides operators through the picking area, showing them which items to collect and which container to place them in to fill each order. On their RF scanners, the software shows the pickers which product and how many to pick. The pickers then place the items in the corresponding bin. To confirm they have carried out this action, they scan the barcode or press the illuminated button on the pick-to-light system.
Next, the WMS shows the operators where to go to pick the next SKU and to place it in the container of the order to which it belongs. This operation is repeated until all the necessary items are collected. An advanced WMS software program like Easy WMS from Interlake Mecalux automates operator tasks. Additionally, it organizes the location of the goods according to a set of rules and criteria established in advance, e.g., product turnover.
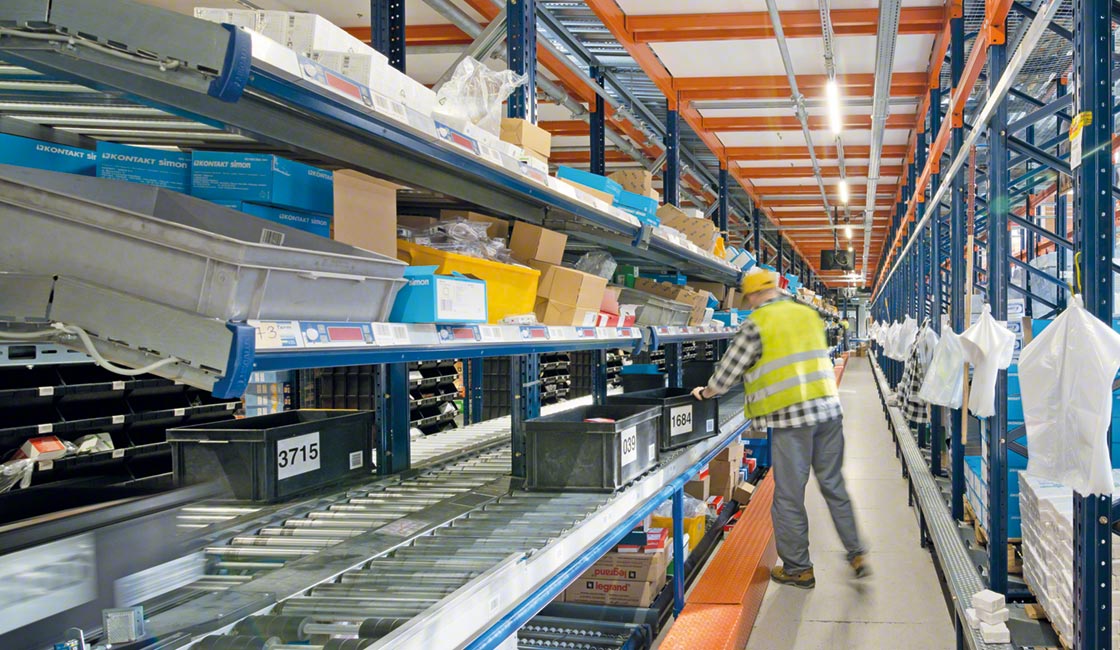
Cluster picking expedites warehouse operations
Cluster picking is a strategy that speeds up order picking in manual storage systems. However, preparing orders in this environment — without automated storage and internal transport systems — requires maximum control over inventory. After all, you don’t want to make mistakes that could prevent your products from being sold.
To eliminate the risk of error from picking, businesses implement WMSs to guide operators step by step as they perform this process. Easy WMS, Interlake Mecalux’s advanced warehouse management software, greatly increases the throughput of logistics processes. Moreover, it ensures that your facility will be productive, scalable, and efficient. Interested in boosting your logistics performance? Don’t hesitate to contact us. One of our expert consultants will offer you the best solution for your company.