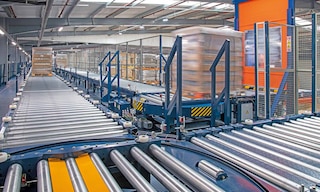
Conveyor rollers and how they work
Conveyor rollers are cylindrical parts incorporated in the upper part of a conveyor frame to facilitate the movement of goods. The purpose of roller conveyors is to speed up the transport of products between two or more areas of a warehouse or production center.
A roller conveyor is an automatic internal transport element dedicated to the movement, accumulation, and distribution of goods to specific locations. These static systems can be made up of a set of rollers, chains, or both.
Conveyor roller applications
Conveyor rollers are galvanized steel components with precision bearings that serve to move loads. With a standard spacing of about 6" between each roller, conveyors ensure continuous, safe flows of goods between different areas of a warehouse or between production and storage zones.
This is the case of multinational packaging solutions company ALPLA. The business’s logistics complex in Golborne, England, consists of two buildings — one dedicated to manufacturing and the other to storage. These two structures, however, are separated by a public road. ALPLA turned to conveyors to gain efficiency in transferring pallets between the two areas. “We needed a system that would connect both buildings and automatically move the goods from the production plant to the warehouse. We wanted to do away with manual handling and the use of heavy vehicles,” says Liam Grimwood, UK Plant Engineering Manager at ALPLA. The double roller conveyor line installed by the Mecalux Group works 24/7, ensuring daily transfers of around 2,500 pallets.
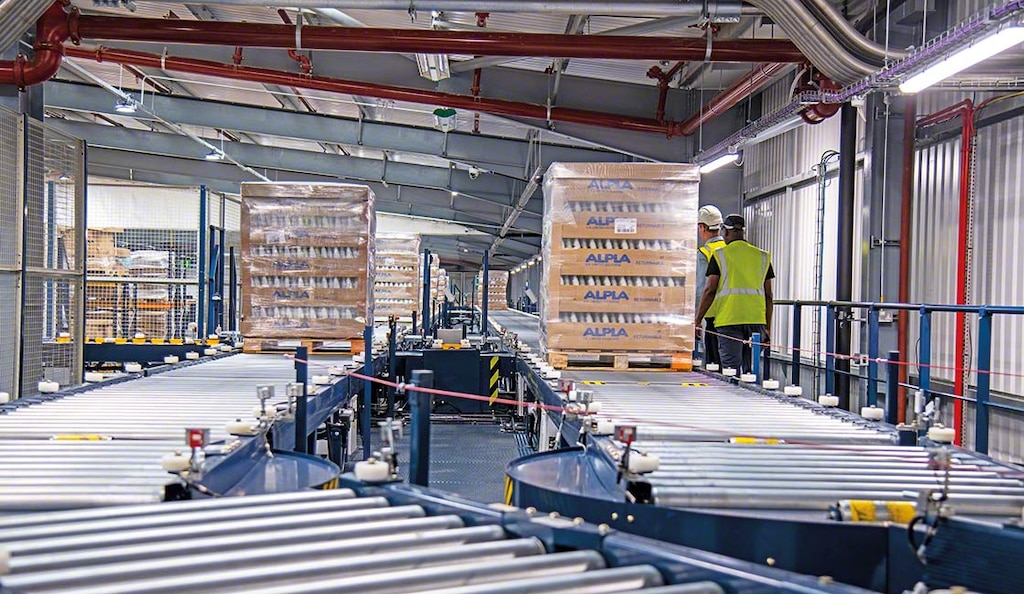
The diameter and length of the conveyor rollers can vary depending on the unit load to be handled: pallets, boxes, or containers. To move Euro pallets, for example, each roller should measure 3" in diameter.
The characteristics of conveyor rollers make this type of solution suitable for facilities run at ambient, refrigerated, and frozen temps. Thus, the logistics center of Congelados de Navarra in Fustiñana, Spain, uses roller conveyors to move goods among different areas, e.g., to the entry to the freezer warehouse and under the sorting lines.
How do roller conveyors work?
The versatility of this logistics solution means it’s possible to create configurations adapted to the needs of each customer, the warehouse layout design, the type of unit load handled, and the logistics processes in place.
Conveyor lines can also integrate other logistics solutions, such as full pallet stackers (to change the pallet type or stabilize the base of defective pallets) or lifts (to move goods vertically and overcome height distances).
Most conveyors incorporate a control system that guides the movement of goods. (The exceptions are plug & play conveyors, which don’t require any programming). In automated logistics facilities, a warehouse management system (WMS) coordinates the execution of the conveyor movement together with the rest of the automatic elements operating in the center.
Different types of roller conveyors
Conveyors incorporate multiple elements that can be coupled and combined according to route or unit load. These are the three kinds of roller conveyors most typically found in warehouses and production centers:
- Powered roller conveyor: static internal transport element with a battery of rollers that move goods in a straight line. This automatic conveying system is used to cover long distances. It’s outfitted with electric motors that propel the pallets or boxes, supplying the different areas of a facility nonstop.
- Turntable conveyor: roller system that lets you change the direction of the goods flow. This solution is used to adapt the conveyor line to the layout of the warehouse or the route to be designed.
- Cross transfer conveyor (with rollers and chains): module combining rollers and chains, mainly used to change the direction and orientation of pallets. For this system to work properly, the chain segment of the conveyor must be 2" higher than the roller segment.
Although these are the most common conveyor solutions, they can also be combined with other elements, e.g., incline conveyors, hydraulic tables, and lifts to connect different levels
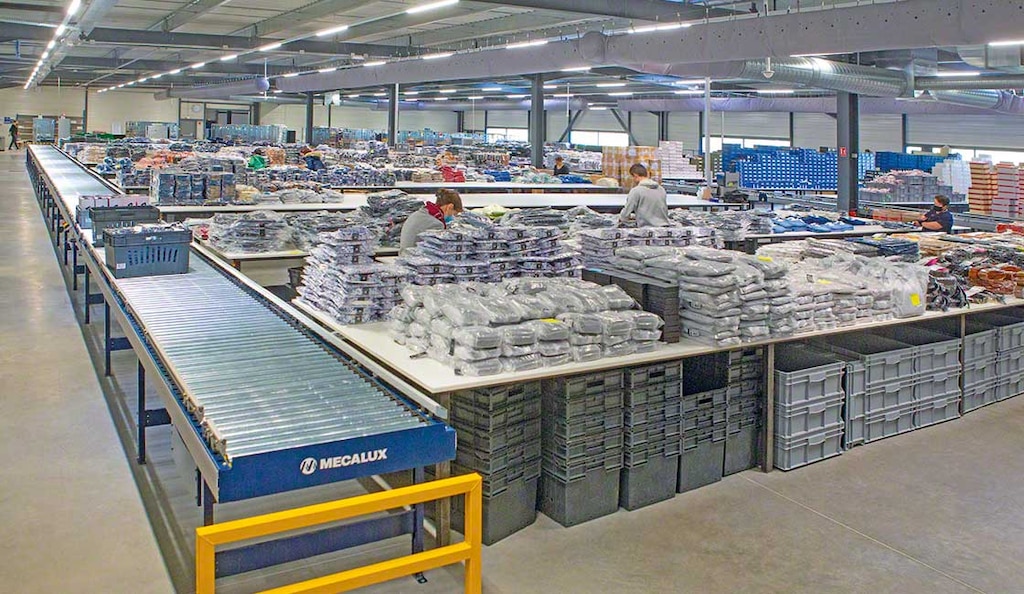
Examples of roller conveyors
The Mecalux Group has designed and implemented roller conveyors in numerous facilities. Let’s check out three examples:
- CCV (France). Mecalux equipped the logistics center of this multi-brand fashion retailer with a roller conveyor for boxes to streamline the movement of over 20,000 products a day. “Our priority was to shorten the distances that operators traveled because, with the time gained, they could concentrate on other tasks that would have an effect on the productivity of the entire facility,” says Michel Gladstein, CEO of CCV. The conveyors automatically link the picking and consolidation areas to improve the warehouse’s throughput. “By using conveyors, we’ve ramped up our productivity: our processes are much quicker and more reliable,” says Gladstein.
- EcoWipes (Poland). The roller conveyors bidirectionally connect the logistics facility with the production center to ensure a constant flow of goods to the production lines: “The conveyors have significantly reduced the time used to carry out logistics operations, such as the supply of the manufacturing area and the receipt of products from the production lines,” says Michał Kulczyński, Supply Chain Director at EcoWipes. In designing this project, the Mecalux technical team had to build a raised, covered bridge to be able to send materials across a busy street.
- Finieco (Portugal). Mecalux built a technological solution to efficiently cope with demand peaks in the automated warehouse of Finieco, one of Europe’s largest paper bag manufacturers. A conveyor connects production with the storage area, speeding up daily transfers of 240 pallets arriving from the manufacturing plant. Joining these two zones by conveyor has enabled Finieco to cut costs and ensure continuous product flows.
Conveyor rollers: structural elements for moving goods
Conveyor rollers are a key element in transferring materials between two or more areas of a warehouse: they guarantee the proper functioning of conveyors. This automatic internal transport solution is extremely versatile, as the diameter of the rollers and the configuration of the conveyor line can be customized to match your particular needs.
At Interlake Mecalux, we have extensive experience designing and installing conveyors for all kinds of customers. Our solutions have boosted the productivity of multiple warehouses around the world. Interested in improving your throughput when it comes to product movements? Don’t hesitate to contact us. One of our expert consultants will advise you on the best solution for your company.