
The Importance of Effective Warehouse Slotting
One of the cornerstones of any successful distribution center is a well-studied and fully optimized warehouse slotting strategy. Efficiency in warehouse design and order fulfillment is directly tied to customer satisfaction, which when done correctly, ultimately leads to increased sales and profitability.
It is a common misconception that the only way to increase throughput is with the total integration of automated systems or through an expensive building expansion. Although these options may be effective in improving your throughput, it is highly recommended to first take a look at your current warehouse slotting arrangement and identify overlooked opportunities for optimization.
What does warehouse slotting refer to and why is it important?
When trying to understand the concept of warehouse slotting, it can help to make an analogy with many of your own personal habits. For example, the organization of your pantry and kitchen drawers. Surely the products used more often are in more accessible locations, in addition, items which you tend to use at the same time or for similar purposes are located next to each other. In summary, warehouse slotting is the process of identifying the most appropriate storage location for each product of your inventory.
You may be asking yourself, “Does it really matter if my warehouse slotting is random, fixed or dynamic?” The truth is that it has more of an impact than many logistics managers may realize. Here are some of the major benefits:
- Better control of inventory
- Improved workload distribution among staff
- Greater picking accuracy and productivity
- Lower product handling and manpower costs
- Elimination of bottlenecks and aisle congestion
- Reduction in order fulfillment errors
- Increased customer loyalty due to improved quality of customer service
So how do I know where to put what?
Warehouse slotting depends on product features, functions and demand
When it comes down to it, it’s all about having your inventory in the right place at the right time. Before deciding on your warehouse slotting organization, take a step back to evaluate the following:
- Be sure to have accurate analysis of all SKU and order transaction data.
- Know the durability and intrinsic stability of each type of stored unit.
- Is there a correlation between the demand of various inventory types? In other words, identify which product groups exist that are typically ordered together.
- Classify the seasonal demands of different goods.
- Don’t forget to take into consideration the ergonomic placement of goods based on their physical characteristics and order frequency.
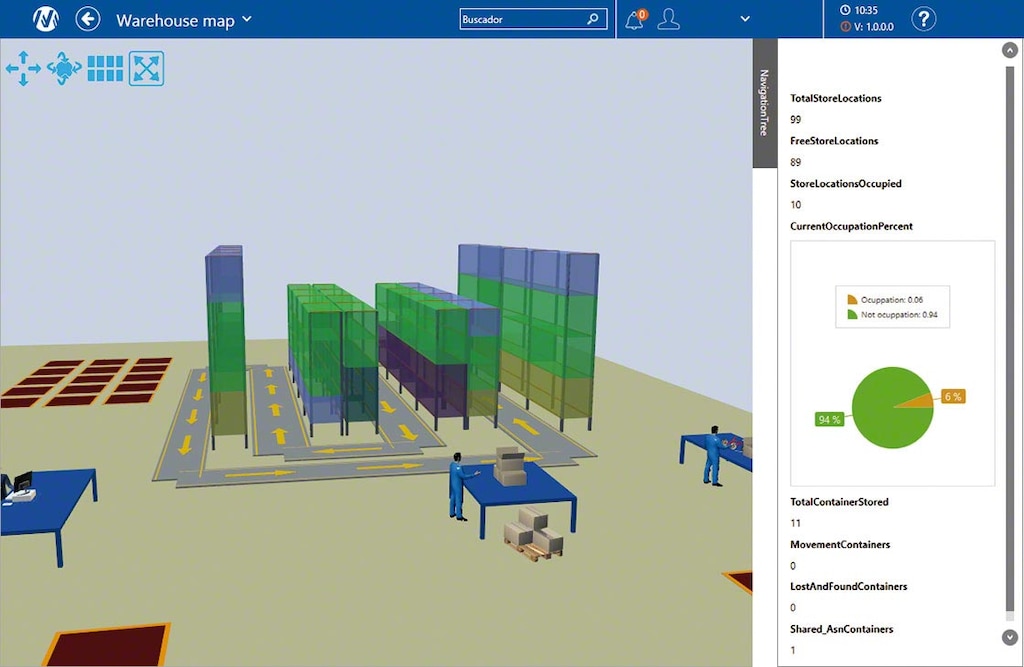
Here are some classic recommendations for optimal slotting:
- High demand pallet items should be placed closer to shipping docks and on lower more accessible racking levels, while low demand goods should be further away from docks and on higher levels.
- Keep in mind basic product characteristics and the resources required to transport them.
- Develop a system for calculating the relative value for each product placement, then compare various configuration strategies and run simulations to determine the optimal slotting arrangement.
- Don’t forget to periodically re-analyze picking locations based on the arrival of new products and changes in consumer demands.
- Take a look at our logistics article, The well-slotted warehouse, to get even more professional advice from our experts.
As your parents probably told you often as a child, “There’s a place for everything, and everything should be in its place.” This could possibly be the perfect theme song for a warehouse slotting design team. So before making the decision to invest in new racking units or a possible building expansion, put your warehouse slotting design under the microscope and discover how even the slightest changes in organization can result in exponential rewards.