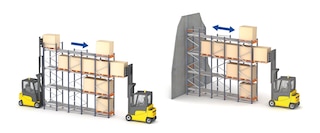
What are FIFO & LIFO Inventory Management Systems?
Whether you are running a small industrial warehouse facility or a large international distribution center, the majority of logistics managers are familiar to some degree with FIFO and LIFO inventory systems. It comes as no surprise that one of the best ways to ensure smooth and seamless operations is by maintaining an extremely organized inventory record at all times. But, how can you be sure that your products are all in the right place at the right time and being picked in the proper order?
FIFO and LIFO: What information should you first take into consideration?
- Product characteristics (For example, are they perishable or do they risk going out of style?).
- Inventory turnover and required safety stock.
- Value of current inventory and if the current cost of goods sold (COGS) is increasing or decreasing, or if it regularly fluctuates.
- What the forecasts are for future demands of different inventory types and the estimated reordering points.
- Inventory holding costs.
- Profit margin objectives.
FIFO: First in, First out
How does it work?
As the name implies, this method refers to a process in which the first stock units produced and stored are the first ones to be sold. In this case, the newest materials received are the last ones sold and the older materials take priority in order picking.
What should I keep in mind?
- Generally speaking, this is one of the more popular and recommended inventory control options.
- Ideal method if your products are perishable, have a limited shelf life or if their popularity is related to popular trends.
- If your goal is to maintain your profit margin, but the cost of goods is increasing, this would result in the need for an increase in product retail prices.
- Examples of FIFO shelving: pallet flow racks and carton flow racks.
LIFO: Last in, First out
How does it work?
Conversely, this method assumes that the last stock unit placed into inventory is the first to be picked and sent to clients or directly to customers. In other words, the newest materials received are the first ones sold and thereby take priority over any older materials.
What should I keep in mind?
- Not all regions in the U.S. permit LIFO to be used as an official method of calculating the cost of goods.
- You are better able to match your most recent costs against your revenue, especially if your products are goods you manufacture.
- This method can be beneficial for companies in industries where production costs are continuously increasing.
- This system is most often used for homogenous goods, such as stone, brick, sand and coal.
- Example of LIFO shelving: push-back racks.
Inventory management is often ranked as the number one challenge for warehouse managers and the type of system used will ultimately have an impact on your consumers. In addition, how you choose to handle and store your inventory will directly affect how much the remaining stock will cost your company and the profit margins obtained.
Here we have seen how the main difference in classification between LIFO and FIFO systems is in terms of the arrival of stock and when it is actually sold. Now it is up to you to determine which option is most appropriate for your inventory needs in order to get the most out of these unique storage criteria.