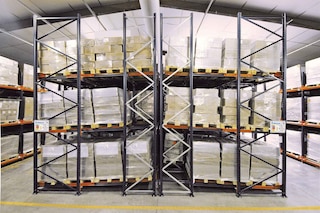
Flow Racking Systems: Increase turnover & keep things moving
Whether you are handling goods with a very limited shelf life or searching for high density storage solutions, flow racking systems can make a huge impact in your day to day logistics operations. These unique shelving units provide operators with unparalleled versatility and the first step to taking advantage of them is identifying which system is most advantageous for your facility and its objectives.
Flow racking systems for different inventory methods
Which strategy is best for FIFO and why?
Pallet and carton flow racking systems are ideal solutions for storing first in, first out inventory. The designs of these systems include multi-level platforms with lanes of wheel platforms which are positioned at an angle. With this structure, goods may be introduced on one side of the unit and then gravity moves them along the wheels until they reach the other side. These systems both have the advantage of providing operators with in-stock visibility so that picking aisles can remain full, while at the same time restocking can occur.
Which strategy is best for LIFO and why?
Push-back racking systems save space, increase storage density and are the best shelving units for inventory requiring last in, first out order fulfillment. This design is similar to that of pallet and carton flow racks in that it is made up of multiple angled platforms, however in this case they employ carts to facilitate the movement of goods. In addition, instead of goods being loaded from one end of the unit and picked from the other, products are stored and extracted from the same side and move between the front and back of the racking unit. In other words, the initial pallet is placed in the first position of a platform lane (the one closest to the aisle) and then the next pallet is used to push the first back. This process continues until each lane is full.
Unique characteristics of each flow racking system
Pallet Flow Racks
- Ideal for high rotation perishable goods which require continuous flow with constant entry and exit operations.
- High quality pallets in good condition and of compatible size and weight can be stored in lanes more than 65 feet deep.
- Increased storage space height may have to be considered due to pallets being positioned on a slant. That is to say, if extreme depth is desired, greater height will be required.
- Excellent solution for warehouses dealing with replenishment difficulties and are running out of storage space.
Carton Flow Racks
- Composed of durable, damage-resistant materials which can be quickly assembled and reconfigured thanks to their clipless track and guide system.
- Can result in a savings of up to 75 percent of labor costs compared to static storage units.
- Ideal for a wide variety of sectors and are designed to minimize product shelf time and maintain a fresh inventory.
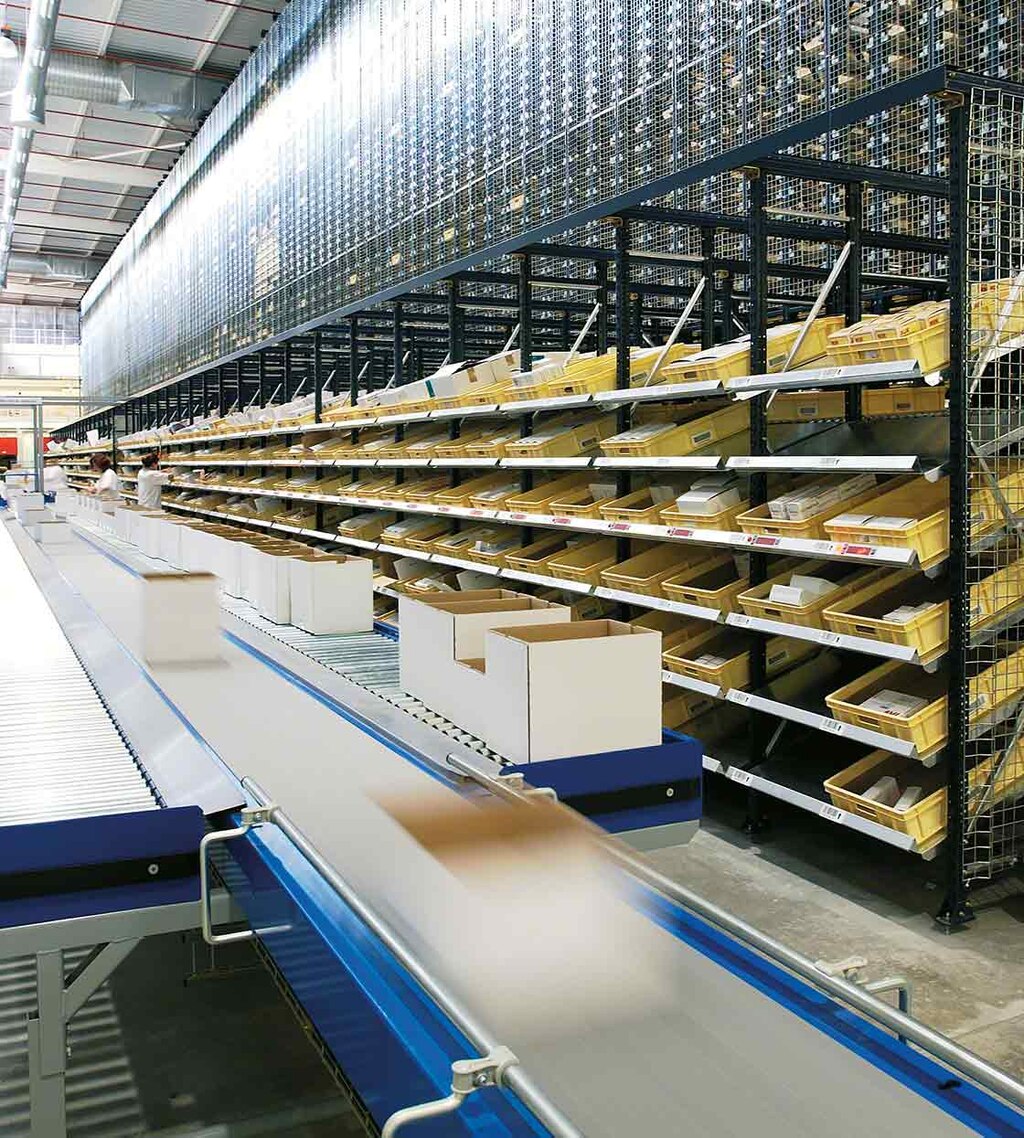
Push-Back Racks
- Safety and handling times can be greatly improved in comparison to other shelving types, such as drive-in racking, due to the fact that forklifts do not have to actually enter storage lanes.
- Ideal for high-density, multiple product storage of average to high consumption goods with a low volume of different SKUs.
- Telescopic carts are installed for levels up to five pallets deep.
- Learn more about the advantages and versatility of this system in our post dedicated exclusively to push-back racks.
Clearly the requirements for product rotation and order fulfillment must be taken into account when deciding which flow racking systems to install, along with other factors such as product shelf life and current costs of goods. Regardless of whether you rely on FIFO or LIFO , the implementation of flow racks in your facility will ultimately have a positive impact on your warehouse product distribution operations.