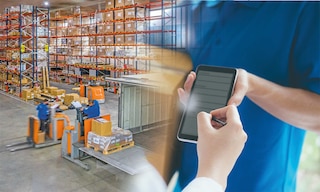
Fill rate: KPI for measuring delivery efficiency
When it comes to achieving customer satisfaction, ensuring efficient order deliveries is a must. The fill rate enables you to measure your shipping performance and make decisions for improvement.
The ability of your warehouse to distribute orders on time and without errors has a direct impact on your business’s reputation. Why? Companies that deliver goods by the agreed deadlines and without issues gain prestige and, consequently, attract new customers.
What is fill rate and how do you calculate it?
The fill rate is a key performance indicator (KPI) used in logistics to evaluate the efficiency of order deliveries. It measures the rate of orders you delivered successfully within the committed time frame compared to the total quantity of orders customers have placed.
To calculate this metric, you first divide the number of orders or products you delivered by the total number of customer orders you received. Then, multiply the result by 100.
Fill rate formula = (No. of orders delivered / No. of orders received) x 100
If you obtain a fill rate of 100%, it means you’ve delivered all the products your customers have ordered without incident. If the percentage is lower than 100%, it means some orders couldn’t be distributed, for example, because of a lack of stock in the warehouse for that SKU.
Although it’s always best to have a high fill rate — the ideal being as close to 100% as possible — reaching that figure can be challenging. Realistically, the percentage should fall somewhere between 85% and 95%.
The fill rate KPI allows you to assess your company’s ability to meet customer needs and expectations. A high fill rate denotes an efficient supply chain with excellent product availability and streamlined warehouse operations. A low fill rate, on the other hand, can indicate inventory management problems, insufficient demand planning, and a lack of coordination with suppliers.
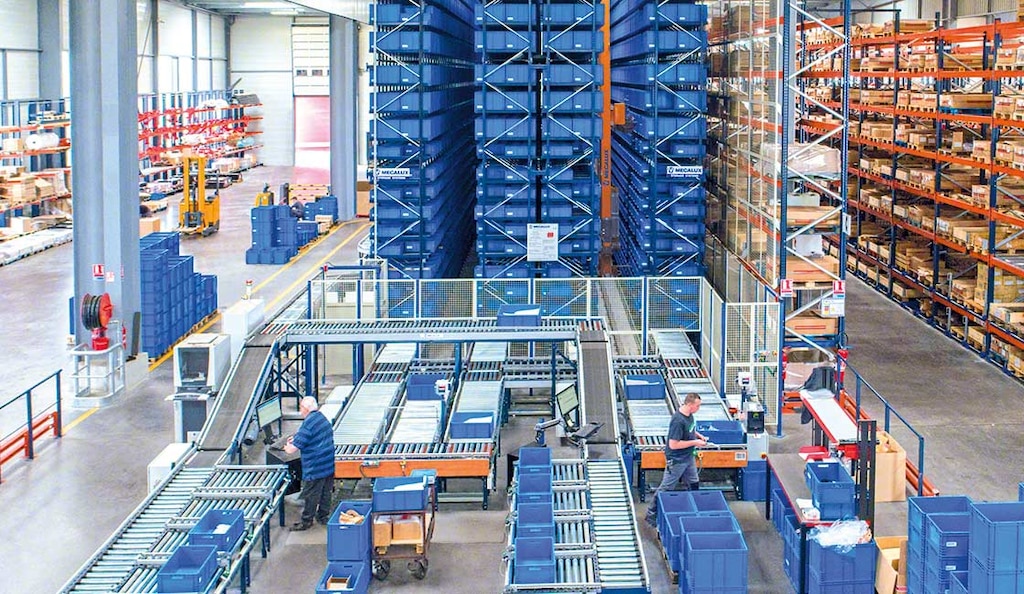
Importance of the fill rate
The priority of any business is to provide good customer service. The fill rate lets you measure the performance of a key supply chain process: order delivery. This KPI is vital for companies in all industries because it enables control over whether customers have received the purchases they’ve made within the stipulated time.
Delivery delays can happen for several reasons, all of which bring the fill rate down. The most common include production planning and scheduling issues, late supply deliveries, poor inventory control, and a lack of coordination between the various supply chain stakeholders. To implement corrective actions, you need to identify the specific causes of the low fill rate.
If your fill rate is high, it means your company is effectively and consistently meeting customer expectations, resulting in loyalty and repeat purchases. Businesses that strive to deliver orders in the shortest possible time enhance their level of service.
Good supply chain management contributes to optimal fill rates. With efficient warehouse operations and smooth communication between your different departments and suppliers, your productivity will go up. Additionally, successfully delivering orders to customers reduces associated return costs, minimizes reshipments, and prevents missed sales opportunities.
How do you measure the fill rate?
Customer satisfaction is a core variable in supply chain management. Overseeing your warehouse operations is critical for quantifying performance and making improvement decisions.
To measure your fill rate, you need to know the exact number of orders customers have placed and that your facility has shipped. But how can you obtain this information accurately? Through digitalization.
Digital solutions such as a warehouse management system (WMS) help you control all processes in your facility. The program identifies products from the minute they arrive until they’re shipped. Therefore, it knows exactly how many orders have been distributed.
Through its integration with the ERP system, the logistics software is also informed of customer orders received. Once the ERP program communicates the products required, the WMS software organizes order fulfillment. It sends operators instructions so that they can locate and ship the products as quickly as possible.
The WMS should be equipped with advanced functionality to strictly control all processes taking place in your facility. For instance, Interlake Mecalux’s Easy WMS features Supply Chain Analytics Software, a digital solution with dashboards that monitor the vast majority of operations relevant to a warehouse.
One Supply Chain Analytics Software KPI that provides data for analyzing the fill rate is accuracy, which presents detailed information on distributed orders. This KPI calculates the percentage of stock units shipped compared to those ordered (a significant data point for spotting potential stockouts). It also shows the percentage of orders filled with all the necessary product quantities and without picking errors.
Another useful dashboard to help raise your fill rate is shipments. The system calculates, among other parameters, the orders shipped per hour, line fill rate, and on-time ready-to-ship. With these KPIs, logistics managers can track their shipment productivity.
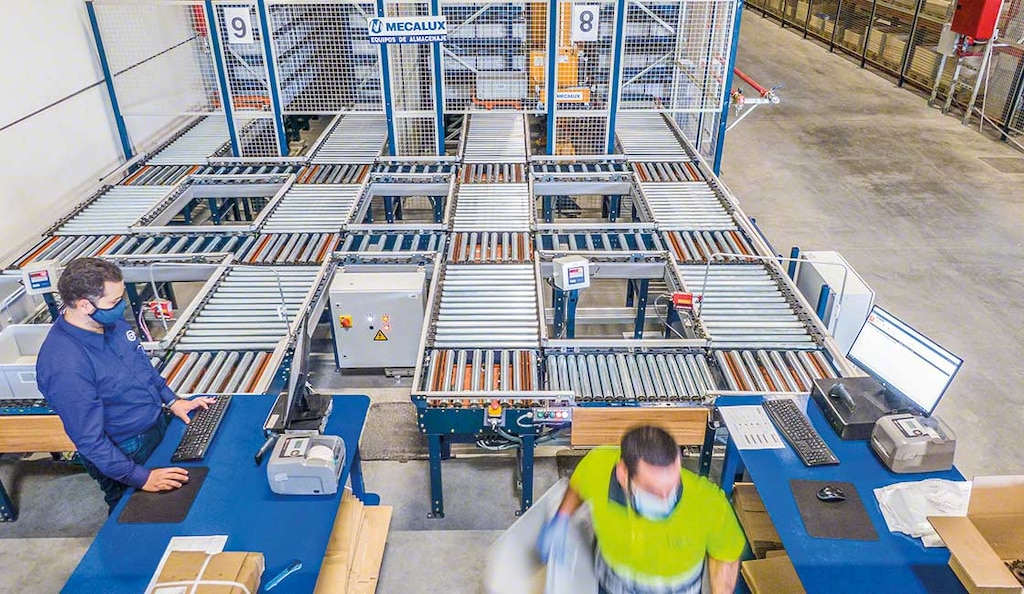
Fill rate: digitalization to boost logistics
Given the link between the fill rate and customer satisfaction, it’s in every company’s best interests to apply strategies that improve supply chain processes and streamline order delivery. To scale up your level of service, it’s crucial to implement systems and technologies to increase the visibility of your processes.
Digital solutions such as a WMS allow you to closely monitor your different logistics operations and foster cooperation between all supply chain players. At Interlake Mecalux, we have extensive experience in developing logistics software that effectively manages inventory and optimizes order fulfillment. Be sure to get in touch. We’ll show you how our solutions can empower you to deliver the service your customers expect.