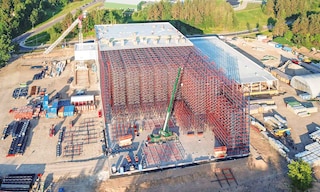
High-bay warehouse: what is it?
A high-bay warehouse is a facility with tall racking units that leverage the height of the building to maximize storage capacity.
To be efficient, these warehouses require solutions that streamline movements of goods. For this reason, it’s standard practice to replace manual handling equipment with automated storage systems. In these facilities, robots such as stacker cranes streamline loading and unloading operations at heights of more than 130'.
What is considered a high-bay warehouse?
A high-bay warehouse is a logistics facility where the storage systems reach a minimum height of approximately 40' and a maximum of 165'. The height of the racks allows you to leverage all available warehouse space from the bottom to the top.
High-bay warehouses are ideal for optimizing storage space. The first high-bay warehouses were built in the 1960s, as Professor René de Koster of Erasmus University’s Rotterdam School of Management points out in his publication Automated and Robotic Warehouses: Developments and Research Opportunities: “The first automated, high-bay warehouses were introduced some 50 years ago. Since then, developments have continued at a rapid pace. Initially, automation was mainly focused on pallet warehouses with bulk storage facilities. A major reason was to increase the storage density, which could be achieved by making the warehouses higher.”
A high-bay logistics facility can be outfitted with conventional storage systems, automated solutions, or a combination of both. But it’s standard practice to implement automated systems. Why? As opposed to manual handling equipment, automated solutions such as stacker cranes can reach over 130' tall and operate more safely and with greater agility at these heights.
Automated high-bay warehouses speed up storage and retrieval operations. In addition, they ensure uninterrupted goods-in/goods-out movements, boosting efficiency in the facility. These warehouses can also be rack-supported buildings, which stand without columns or beams; instead, the racks themselves support the construction elements and are designed to withstand external agents such as wind and seismic activity.
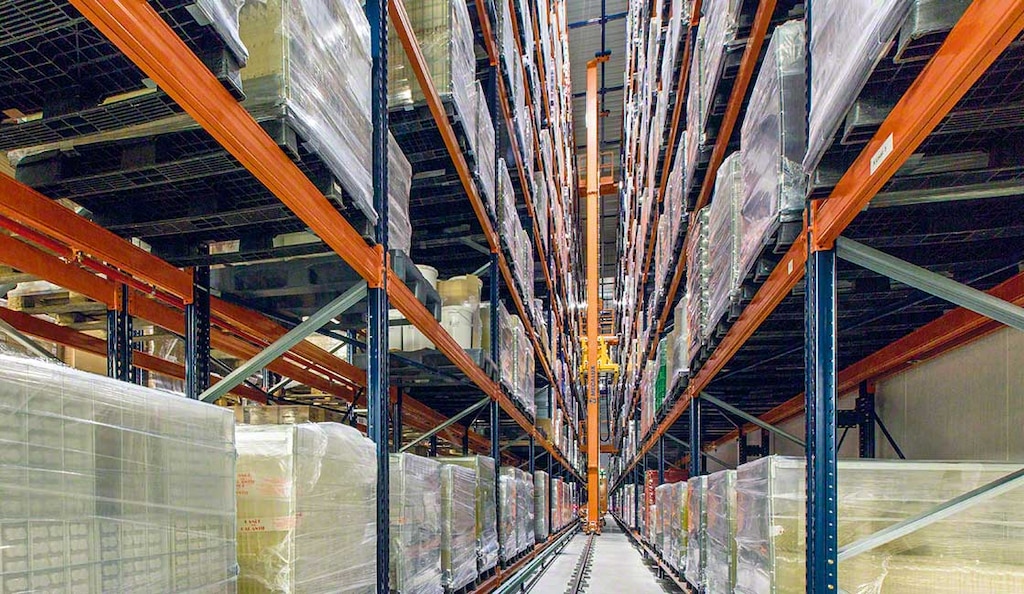
Advantages of high-bay warehouses
When you need a high storage capacity, a high-bay warehouse is an excellent choice. These are the main benefits of installing a high-bay warehouse:
- Maximum space utilization by gaining cubic feet vertically.
- Configuration adaptable to different types of loads and weights.
- More throughput in warehouse operations, e.g., goods storage and removal.
- Flexibility in installing manual storage systems and/or different degrees of automation.
- Improved safety in the facility through the use of automatic handling equipment.
Nevertheless, high-bay warehouses have limited scalability: even though you’re allocating space at height to storage, the facility can stand no taller than the maximum number of feet established for safety reasons.
How does a high-bay warehouse work?
High-bay warehouses make manual handling of products complicated. Automatic solutions — i.e., stacker cranes for pallets or boxes — facilitate this operation, enhancing efficiency and safety in goods loading and unloading processes.
In an automated high-bay warehouse, all operations are controlled by a warehouse management system (WMS). This software coordinates the movements of the unit loads and the automatic equipment. A parameterizable, scalable program such as Easy WMS from Interlake Mecalux provides real-time inventory control and automates product flows in the facility.
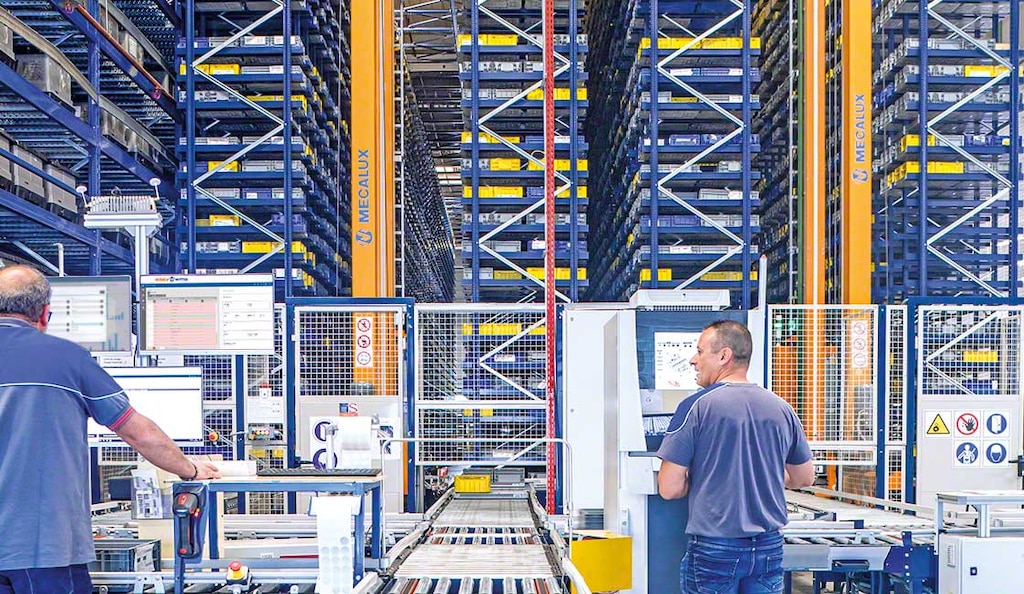
These facilities can also incorporate internal transport solutions to move goods between the different areas of the premises. To speed up product flows and ensure continuous movement, forklifts and other handling equipment are normally replaced with internal transport solutions such as automatic conveyors, autonomous mobile robots, and automated guided vehicles.
In their publication Flow of Goods in the Warehouse Management Systems – Problem Analysis, researchers from Poland’s Gdynia Maritime University explain that in automated high-bay facilities, “the role of forklift operators is taken over by warehouse stackers handling pallets on racks up to 40 meters [131'] high. When the goods are released into the automated part of the warehouse, they are [fed into] the conveyor system. … After selecting the [aisle], the system allocates a storage place where the goods will be located, while generating for the stacker the task of transporting the pallet to the previously reserved storage place. The location of loads is also managed in this case by the IT system.”
The authors of the analysis highlight the role of software in high-bay warehouses: “It tracks all warehouse transfers and generates them itself, so if the pallet does not reach its place, the system will signal this fact to the employee.” The authors go on to say that the software comprehensively manages all data entered (e.g., raw material and product expiration dates, production order deadlines, and customer orders), generates transportation orders, and coordinates the preparation of all order items.
High-bay warehouse to optimize storage capacity
The increasing price of logistics square footage has driven companies to reverse the trend of acquiring more surface area horizontally, growing vertically instead. A high-bay warehouse with high-bay racks lets you make the most of your facility’s capacity and reduce your logistics costs.
Our company has extensive experience in installing these types of warehouses all around the world. Examples include Hayat Kimya (Turkey), Intersurgical (Lithuania), and CEPSA (Spain), among many others. Interested in boosting your company’s throughput? Don’t hesitate to contact us. One of our expert consultants will work with you to come up with the best solution for your facility.