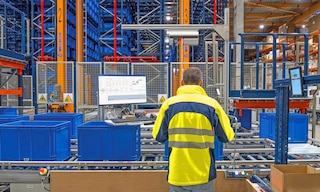
How to measure productivity: Techniques, uses, and recommended technologies
Productivity is a metric that evaluates how efficiently resources are utilized to achieve results. Analyzing it not only optimizes resources but also improves customer service and cost-effectiveness. Below, we explore the advantages of measuring productivity, how to calculate it, and the technological tools that facilitate the process.
Why is measuring warehouse productivity important?
Measuring warehouse productivity is essential for guaranteeing that operations run efficiently and meet business objectives. These are some key benefits logistics managers can obtain when they know how to improve warehouse productivity.
- Resource optimization. The process identifies areas where labor, space, and equipment are underutilized, helping reduce costs and improve performance.
- Informed decision-making. Productivity data provides a basis for strategic decisions, such as expanding the warehouse, reorganizing zones, or investing in technology.
- Bottleneck identification. Assessing this metric helps pinpoint processes or areas slowing down operations and implement targeted improvements.
- Service level compliance. Accurate measurement ensures that orders are processed and delivered on time.
- Performance tracking. Evaluating the efficiency of associates, equipment, and processes enables managers to establish clear metrics and compare progress against set goals.
- Operational cost reduction. Measuring productivity identifies opportunities to cut down on waste, optimize pick paths, and minimize inventory handling errors.
- Adaptability and continuous improvement. Metrics enable businesses to pivot to demand fluctuations, detect trends, and constantly enhance operations.
- Market competitiveness. A productive warehouse can handle higher volumes and respond better to customer demands, strengthening the company’s position against competitors.
How to measure warehouse productivity?
An organization can measure its warehouse productivity through metrics that correlate performance with the resources used. To apply them, managers need to define supply chain KPIs tailored to warehouse needs and monitor them continuously. Some of the most common ones include:
Orders picked per hour
This productivity rate indicates how many orders are completed within an hour, reflecting the performance of teams, systems, and processes. It’s useful for assessing operational capacity during peak periods, identifying bottlenecks, and comparing the throughput of different shifts, lines, or warehouses.
To calculate the number of orders picked per hour, divide the total number of orders filled by the number of hours worked.
Orders picked per hour = Hours worked / Total orders picked |
---|
Lines picked per associate
This KPI indicates the number of order lines — different products within an order — that each associate picks during a specific period. It’s crucial for assessing efficiency and allocating resources in order fulfillment operations, including picking and packing. Additionally, it helps identify areas for improvement, measure the effectiveness of different teams, and analyze the impact of technology or workflow changes.
To determine the average number of order lines picked per associate, divide the total number of lines picked during a specific period by the number of employees involved in that task.
Lines picked per associate = Total lines picked / Number of associates |
---|
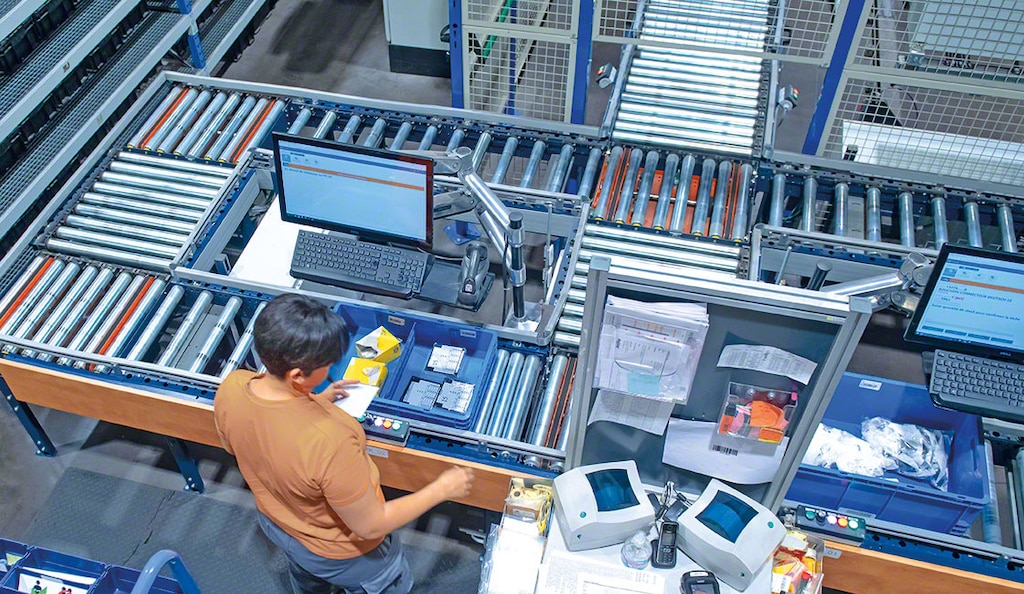
Inventory turnover rate
This critical metric in logistics and inventory management measures how often stock is replenished over a given period, typically a year. It indicates how many times stored products are sold or consumed, revealing inventory management efficiency and alignment with demand. This KPI helps determine whether stock levels are appropriate, minimize storage costs, and tailor purchasing and production to market needs.
To calculate the inventory turnover rate, divide the cost of goods sold by the average inventory value.
Inventory turnover rate = Cost of goods sold / Average inventory value |
---|
Order picking accuracy
This metric evaluates order processing efficiency during picking. It measures the number of correctly selected items according to order specifications in relation to the total lines or items processed. A high accuracy rate ensures excellent order fulfillment, improving customer satisfaction. This KPI identifies inefficiencies in the picking process, reducing returns and extra costs.
Order picking accuracy = [(Total orders - Incorrect item returns) / Total orders] x 100 |
---|
Cost per unit handled
This KPI calculates the total cost of managing an individual product unit in a logistics operation. It’s fundamental for assessing operational efficiency and controlling receiving, storage, picking, packing, and shipping expenses.
To determine the cost per unit handled, divide total logistics operation costs by the number of units processed.
Cost per unit handled = Total logistics operations cost / Total units handled |
---|
How to improve productivity through technology
Technology plays a vital role in tracking, analyzing, and improving warehouse productivity.
A warehouse management system like Interlake Mecalux’s Easy WMS enables companies to supervise and optimize every stage of logistics operations. It features the Labor Management System (LMS) module, which measures productivity. Würth Modyf, a business specializing in workwear, uses LMS to assess logistics task performance. This enables it to make data-driven decisions to increase warehouse productivity at its headquarters in Polinyà (Spain). “With Labor Management System, we can monitor the workflow in our facility to boost productivity,” says Juan Martínez, Operations Manager.
To collect real-time data and generate detailed reports on warehouse activity, technologies like barcodes, RFID tags, and handheld scanners are a must. Advanced analytics tools (e.g., data analysis software and artificial intelligence) further help identify patterns, forecast demand, and optimize operational planning.
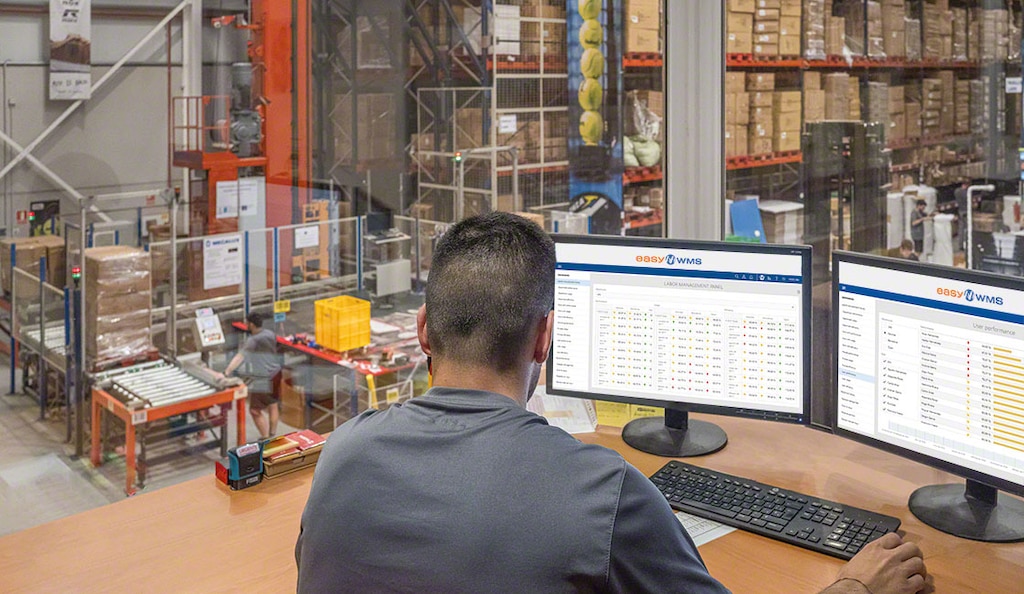
Measuring warehouse productivity: Central to logistics success
Measuring productivity not only ensures more efficient operations — it boosts companies’ logistics competitiveness. Technologies like WMSs, automation, and analytics tools provide accurate data to maximize available resources.
In today’s dynamic, competitive logistics environment, measurement and continuous improvement are imperative for meeting market demands and satisfying customers. If you’re looking to measure your warehouse productivity, be sure to contact us. We’ll provide guidance and support you in implementing the solution that best suits your company’s needs.