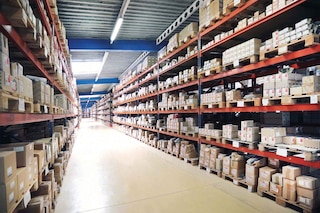
Inventory management techniques: what are my options?
Reviewing the inventory management techniques used in logistics nowadays might be necessary if you tend to find outdated perishables or other stock in your warehouse, your storage costs are through the roof, or you keep running into stockouts.
Below, you’ll find a list of different inventory management techniques to keep these situations from happening:
The FIFO method (First In, First Out)
This technique’s objective is to get rid of the oldest SKUs in stock, i.e., those at the front of your storage channels or racks.
Easy to apply, this method lets you handle, organize, and assign priority to the flow of goods and materials.
The LIFO method (Last In, First Out)
The last in, first out method means extracting your most recently stocked items, i.e., those which have arrived last.
Like the FIFO method, this contributes to better, more coherent and streamlined product flows.
Economic order quantity or the Wilson model
This model, also called the EOQ method, is particularly suited to organizations that only manage a small amount of daily orders. In other words, it’s apt for small and medium-sized businesses..
Companies order their raw materials and goods at certain times of the year.This technique is the simplest to implement, but entails making orders at regular intervals.
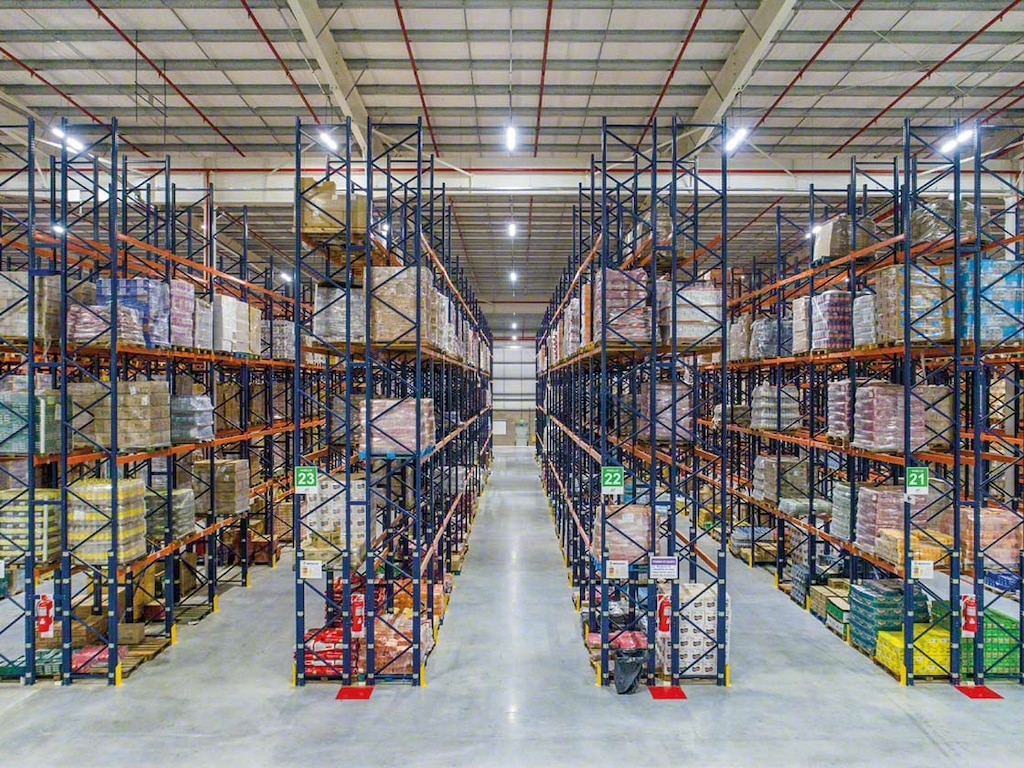
The ABC analysis
The ABC analysis, a sorting technique that prioritizes the economic contribution made by each product, is one of the most important inventory management techniques. According to this theory, goods are classified into three categories: A, B, and C.
- The most important products are in the A category and represent the highest annual consumption value. Keep in mind that these items must undergo rigorous stock control and be stored in areas with special ambient storage conditions. It’s fundamental to replenish this type of stock regularly to prevent incidents caused by a stockout.
- Products in category B are considered intermediate, i.e., they have an average consumption value. How goods are slotted between categories A and C is a crucial step to have under control so that these goods don’t get wrongly assigned to higher or lower categories.
- Products in category C are the least important, accounting for the lowest annual consumption value. For this reason, replenishment is less frequent. Generally, companies don’t store more than one item from this class and replenish it only when it’s out of stock.
Inventory management techniques for each scenario
Keep in mind that there are other inventory management techniques, such as the just-in-time system, which looks to keep inventory levels down to a minimum to cut costs. Another option is cross-docking, an order preparation method that ensures that the inventory remains in the warehouse for the shortest time possible.
However, before choosing a technique, you have to take into account a series of factors, such as order volumes, storage capacity, warehouse design, annual forecasts, and annual consumption values. The method implemented should meet the particular needs of each organization. The FIFO technique, for example, is often the perfect strategy for businesses that sell perishable products, as it guarantees the timely exit of the goods. On the other hand, companies that distribute homogenous products with a long lifespan (sand, coal, bricks) can opt for the LIFO method, as the exit date of the goods isn’t a conditioning factor.
Regardless of the technique chosen and the characteristics of each business, it’s essential to use a warehouse management system to optimize the various handling and inventory control tasks. In this vein, Easy WMS from Interlake Mecalux is the ideal tool for streamlining these operations and performing them effectively and accurately. To find out how we can help you better manage your stock, get in touch. One of our experts will contact you to offer you a solution specifically tailored to your company’s needs.