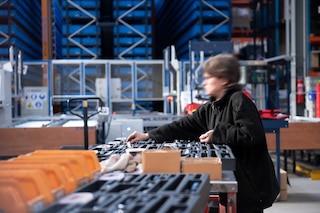
Kitting: optimizing assembly in the warehouse
Kitting is a logistics strategy that consists of gathering the individual parts that make up a product and combining them to create a package or kit. This kit is then brought to other operators in the installation who will put together the final product.
Assembly-line workers themselves could go and get the components that make up the product. However, implementing a kitting strategy, with employees specialized in kit preparation, increases speed and reduces errors in the manufacture of the goods. For this method to be successful, a number of challenges need to be met. We’ll analyze them in this article.
What’s kitting?
Let’s begin with a more detailed definition: kitting refers to the process of collecting all the materials that make up a product and grouping them into a kit, which is subsequently delivered to the assembly lines to be put together. This operation is carried out in advance to guarantee the uninterrupted supply of goods to the assembly lines.
Assembly lines are commonly found in the manufacture of automobiles, furniture, and appliances, among other commodities. The various components of each product are joined together in a sequenced way as they go from one workstation to another.
One very simple example would be a pen company. In the warehouse, operators pick five SKUs:
- SKU01: cap
- SKU02: barrel
- SKU03: plug
- SKU04: ink
- SKU05: tip
None of these items can be marketed separately; instead, once gathered together, they have to be sent to the assembly lines for the new SKU to be manufactured (SKU06, the pen). Accounting for these SKUs separately (both the pen and its parts) helps the company to monitor its stock more accurately.
Kitting: neither VAS nor production supply
We shouldn’t confuse the concept of kitting with the process of supplying the production lines or with value-added service (VAS). Let’s take a look at what they consist of:
- Production supply. Some warehouses supply the production lines with the raw materials necessary to manufacture the products. For example, flour, salt, and yeast are compiled in a warehouse. Then, water is added, transforming them and creating a new SKU: the bread. Among Interlake Mecalux’s software solutions, the module that performs this function is WMS for Manufacturing.
- VAS or value-added services. In logistics, VAS relates to the transformation of a product to fulfill specific customer requests (for example, the screen-printing of a T-shirt with a personalized message). In the warehouse, operators locate the items and bring them to the corresponding workstations to be modified. Once this process is finished, the products are dispatched to be delivered directly to the customers.
In other words, kitting is a strategy with the aim of assembling the final product. Production supply, in contrast, deals simply with the supply of raw materials in manufacturing processes. And VAS consists of personalizing an item for an individual client. Although these three concepts might coincide on occasion, it’s necessary to understand the differences between them, since they are implemented and developed in different ways.
Advantages of kitting
Kitting is a challenge for businesses: it forces them to allocate time and resources in the warehouse to a need that’s not always evident. Nevertheless, it’s a working method that, when applied efficiently, has great value for the entire company, offering numerous advantages. On the assembly lines, operators have within their reach all the essential materials to do their job, resulting in greater speed and cost savings.
- Optimization of work time, and reduced movements. By leaving the items prepared, assembly line employees don’t have to look for the materials they require, as they’re all on hand.
- More streamlined supply chain. The warehouse and assembly lines are perfectly connected and coordinated to maximize the manufacture of the goods. This leads to improved service and agility in this operation.
- Error reduction. Workers who prepare kits specialize in this task and, with the help of the warehouse management system and computerized picking systems such as put-to-light, can group all the items together without making mistakes.
- Boosted productivity. Preparing all the materials in advance allows you to control your inventory more strictly and ensure continuous, uninterrupted goods assembly.
- Space maximization. Operators on the assembly lines are provided only with the products and tools they require to do their job. Therefore, only the space strictly necessary for storing the products is occupied.
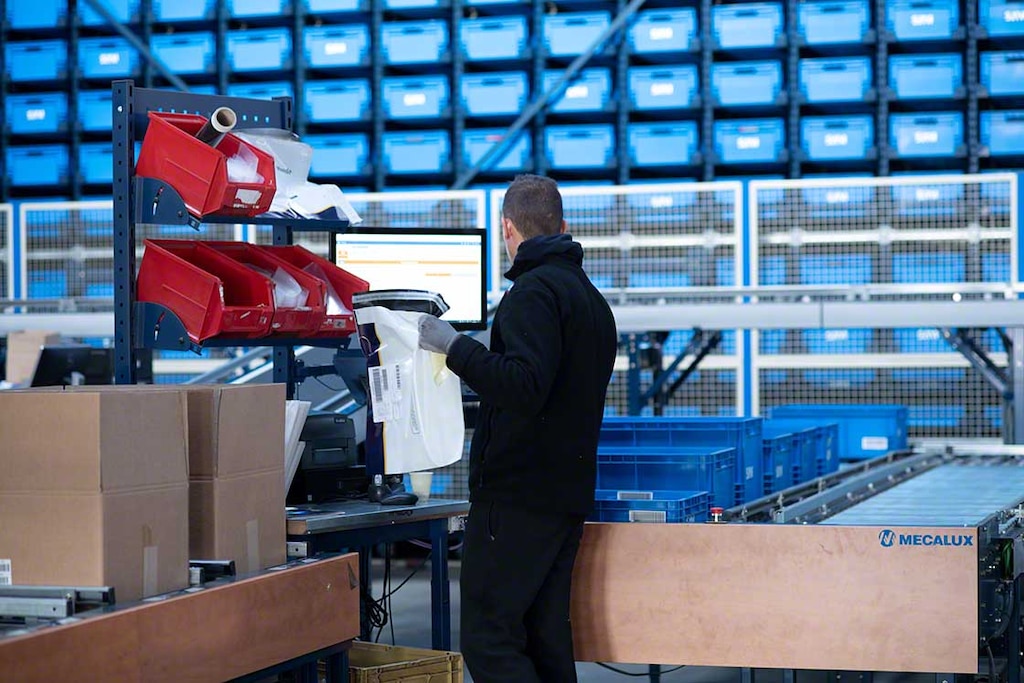
Storage systems for kit preparation
To put kits together effectively, the installation needs to be equipped with the appropriate storage systems and handling equipment for carrying out this process. They should have the following characteristics:
- Easy access to stock. Direct access speeds up goods management and inventory control.
- Versatility for products with different attributes. The locations need to accommodate all kinds of products of varying sizes and turnovers, including both the components that make up the kits and the kits themselves.
- Organization of goods in the warehouse. Optimal distribution of the products lets you locate SKUs more easily while streamlining operator movements. Thus, for example, it’s better to store the parts that usually go into making the kit very close by to avoid excess travel.
When the kits comprise small components, these can be stored on picking shelves, since they provide good access to the merchandise. In particular, carton flow racks are the most useful for handling large amounts of product.
These gravity flow racks can house more goods than static shelving, cutting down on replenishment. Plus, with these racks, stock replenishment and kit preparation are carried out in different aisles, eliminating interference between these tasks. The incorporation of pick-to-light devices also speeds up operators’ work.
On the other hand, when the kits include big items, these are usually stored on pallet racks, an ideal solution with direct access for storing a significant number of SKUs and leveraging the available space. The employees pick the SKUs they need to form a kit directly from the pallet located at floor level. And replenishment is done with the pallets positioned on the levels immediately above this.
The automation of kitting
If you want to achieve greater throughput in kitting, the potential of automation is worth noting. Automated warehouses for both pallets and boxes not only optimize space, but also contribute towards completing kits more quickly, securely, and accurately.
The product-to-person method helps to shorten kit preparation times. This is because operators remain at their assembly stations awaiting the goods, which will be brought to them automatically (thus, doing away with the need for them to travel). In addition, kits are prepared in a sequenced, organized way, taking into account the company’s requirements.
Automating kitting has four clear-cut advantages:
- Quicker and more efficient goods storage.
- Reduced worker movements (hence, time saved).
- Security of the products, as access to them is restricted.
- Just-in-time parts delivery, as the kit components are sent to the production lines at just the right time.
WMS, an essential kitting tool
Warehouse management systems (WMSs), such as Interlake Mecalux’s Easy WMS, are a fundamental tool for enhancing all operations in the installation, including kitting. Two of its basic functions are to manage the movements of the handling equipment (stacker cranes and conveyors) and to supply the kit preparation stations with the necessary goods.
Furthermore, for kitting to be truly effective, the WMS continuously monitors the stock. Stockouts could lead to delays in kit preparation and, consequently, interruptions in product manufacturing.
In this process, particularly, perfect integration between the ERP and the WMS are of paramount importance. Kit assembly takes place after an order is sent by the ERP, and tasks are performed by following instructions from the WMS.
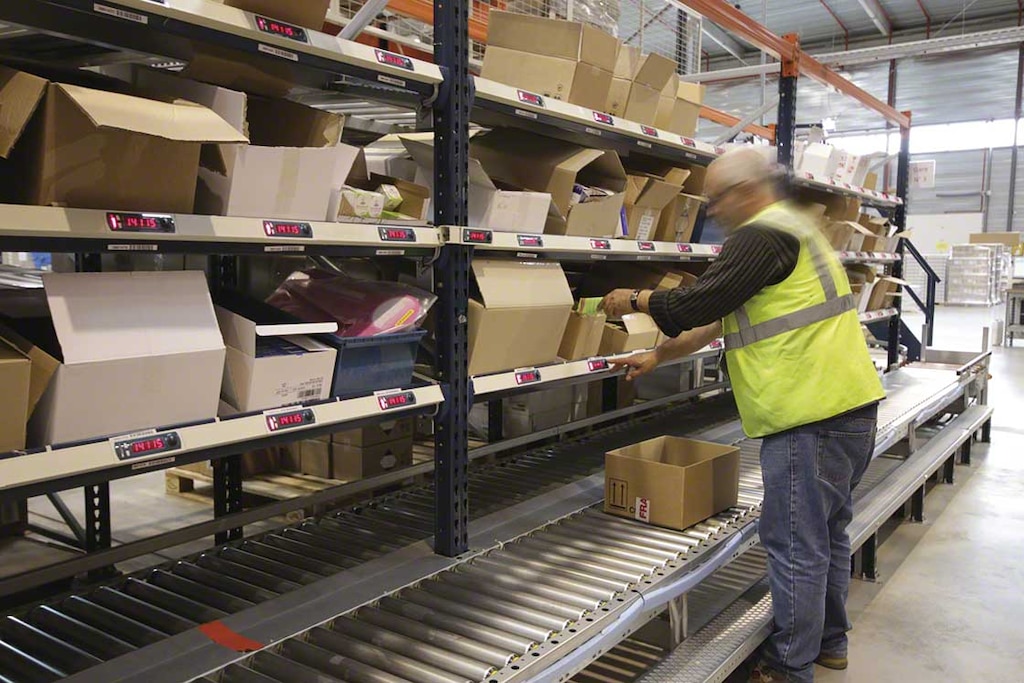
For kitting, the flow between the WMS and ERP would be as follows:
The ERP generates a bill of materials, a list specifying the components required at each assembly station to manufacture the products.
Immediately afterwards, the WMS not only organizes the kits (to ensure that priority orders are prepared first), but also plans and assigns tasks. This system guides the operators, sending them clear orders so that they gather all the materials needed without fail.
Once the kits are finished, the WMS notifies the ERP and arranges for them to be sent to the assembly lines at the appropriate time.
Logistics at the service of the assembly lines
The main goal of kitting is to optimize time and work on the assembly lines. Warehouse employees compile and group the necessary items ahead of time and send them to production at just the right time to prevent delays and interruptions to service.
To supply the assembly lines more promptly and efficiently, the installation needs to be equipped with storage systems that facilitate the location and preparation of the SKUs comprising the kits. Likewise, it’s essential to have a WMS to coordinate operators’ tasks and strictly monitor stock.
There’s no doubt that automation provides greater throughput. Interlake Mecalux has extensive experience in deploying automated warehouses. A good example of this is the project our company carried out for French tool manufacturer SAM Outillage. At its facility, Mecalux installed kitting stations wide enough for workers to be able to sort the tools and quickly place them in cases. Kitting fulfills the product-to-person principle, that is, stacker cranes and conveyors automatically bring the goods to the operators.
Don’t hesitate to contact Interlake Mecalux to set up your storage project and make the most of kitting in the warehouse.