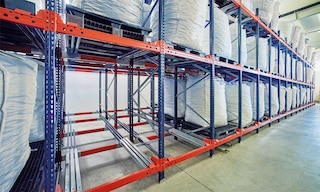
LIFO (last in, first out): uses and examples for inventory management
Companies can choose from several inventory management strategies to adapt their warehouse operations to the characteristics of their business and the products they make or sell. One such strategy is LIFO.
What is the LIFO method?
LIFO (last in, first out) is an inventory management principle where the last item stored is the first to be retrieved. With this approach, the most recently purchased or manufactured batches are prioritized over those already in a storage system. One of the main advantages of LIFO is that it shortens the distances goods have to travel since operators load and unload them from the same aisle.
The opposite of LIFO is FIFO (first in, first out), whereby the first items stored are the first to leave the facility or be used in production.
When is LIFO used?
Less common than FIFO, LIFO is typically seen in warehouses with products that are non-perishable, have long sell-by dates, and don’t lose much value over time. This is because the units stored first will remain in stock longer. In short, LIFO is suitable for scenarios where inventory turnover isn’t a critical factor and in several other cases:
- Non-perishable items. These products won’t expire soon or degrade quickly. Some examples of goods apt for LIFO criteria are bricks, cement, and bulk commodities. Other possibilities are electric components and furniture.
- Similar products. Some industrial environments house large quantities of identical materials. In these cases, where it’s not necessary to ensure fast product turnover, LIFO can come in handy.
LIFO storage systems
Due to their operation, certain racking systems are perfect for implementing LIFO inventory management:
- Drive-in racks. This is the simplest and most affordable high-density system. It consists of racks with lanes accessed by forklifts to store and retrieve pallets at several levels and depths. Pallets are loaded and unloaded from a single working aisle. Drive-in racks are a good choice for LIFO, i.e., for accommodating a small variety of SKUs and many pallets per each.
- Push-back racks. This similarly compact storage solution houses several pallets deep and a different SKU per channel. Loads are pushed along slightly sloped channels. Based on the LIFO management principle, operators access goods from the same working aisle.
- Pallet Shuttle system. This semi-automated high-density system increases storage capacity and speeds up pallet storage and retrieval. A motor-driven shuttle deposits and removes pallets from the racks. An operator manages the process, placing the shuttle in the racking with a forklift and controlling its movements via a tablet. In addition to LIFO, this option is compatible with the FIFO strategy.
When necessary, LIFO can be applied using other options such as selective pallet racks. This is one of the most versatile systems, offering direct access to each SKU stored in it. In this case, it’s important to track what was inserted last. While this can be done manually, a warehouse management system (WMS) greatly streamlines SKU tracking.
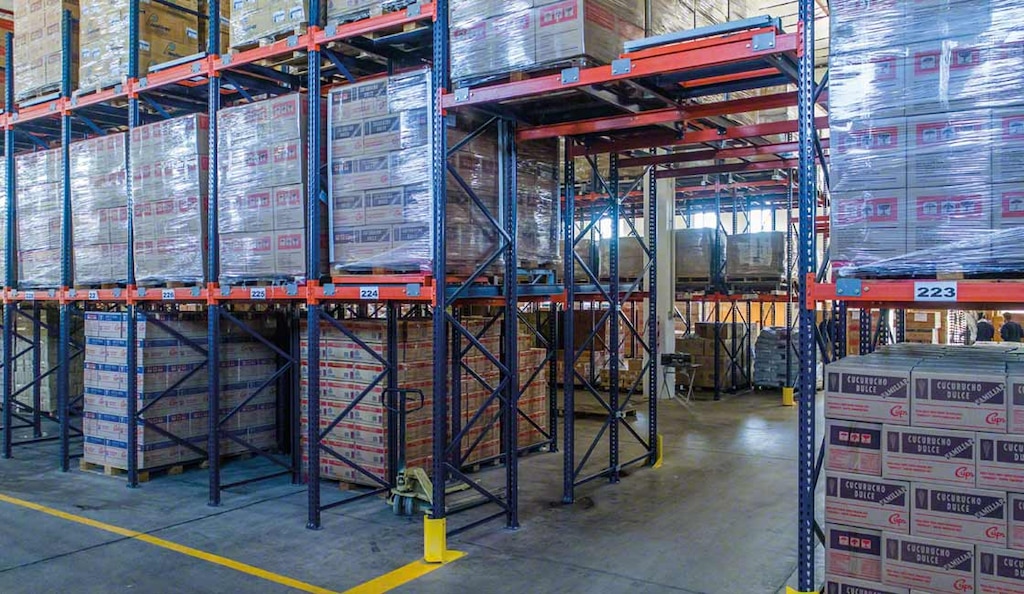
Advantages of LIFO
Using LIFO when appropriate provides multiple benefits in day-to-day intralogistics operations:
- Time savings in the receiving process by slotting goods as they arrive.
- Long-term storage of products without depreciation of their market value.
- Higher warehouse occupancy rates.
- Reduced travel distances by loading and unloading from the same aisle.
- Orderly workspaces due to fewer movements.
- Prioritized output of stock stored the longest.
- Constant inventory turnover.
- Better comparison between revenues and expenses, as the cost of goods sold aligns more closely with their acquisition cost.
Manage your LIFO stock with Interlake Mecalux
Thinking about implementing LIFO in your storage operations? At Interlake Mecalux, we can help you with the hardware as well as the software. As manufacturers of our own products since 1966, we’ve implemented thousands of automated and conventional warehouses worldwide.
In addition, our team of over 400 software engineers is dedicated to developing and enhancing applications. These include our Easy WMS warehouse management system, a valuable tool for gaining comprehensive product traceability. Be sure to contact us for advice on this and other storage solutions.