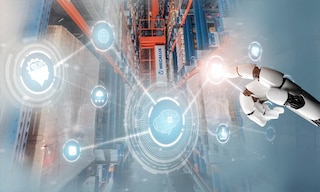
Logistics robots: the rise of automation in warehousing
Logistics robots are a growing trend that has really taken off in recent years. The progressive complexity of warehousing and the demand for agile and efficient operations have caused companies to invest in automating movements as well as the different areas in the facility with automated storage and retrieval systems (AS/RS).
The boom in logistics robots responds to the need to reduce costs and optimize processes to improve competitiveness. As opposed to conventional equipment, logistics robots ensure maximum throughput 24/7 if required, in addition to the safety of the goods, the operators, and all other elements involved in the warehouse.
What are logistics robots?
Logistics robots encompass any autonomous system or machine used to automate product flows, maximize safety, and boost productivity in warehouse operations.
The implementation of new technologies in any warehouse process — e.g., goods receipt, storage, stock management, order processing, and shipping — has led to these robots becoming more prominent. These solutions work with full autonomy to perform functions such as transferring products between two points, preparing orders, and storing products on racks.
More and more businesses are considering the introduction of robots in their logistics tasks to eliminate the risk of mistakes and ramp up productivity. This is reflected in the recent McKinsey study Automation has reached its tipping point for omnichannel warehouses, which puts the annual growth rate for the warehouse automation market at 23%, reaching $51 billion by 2030.
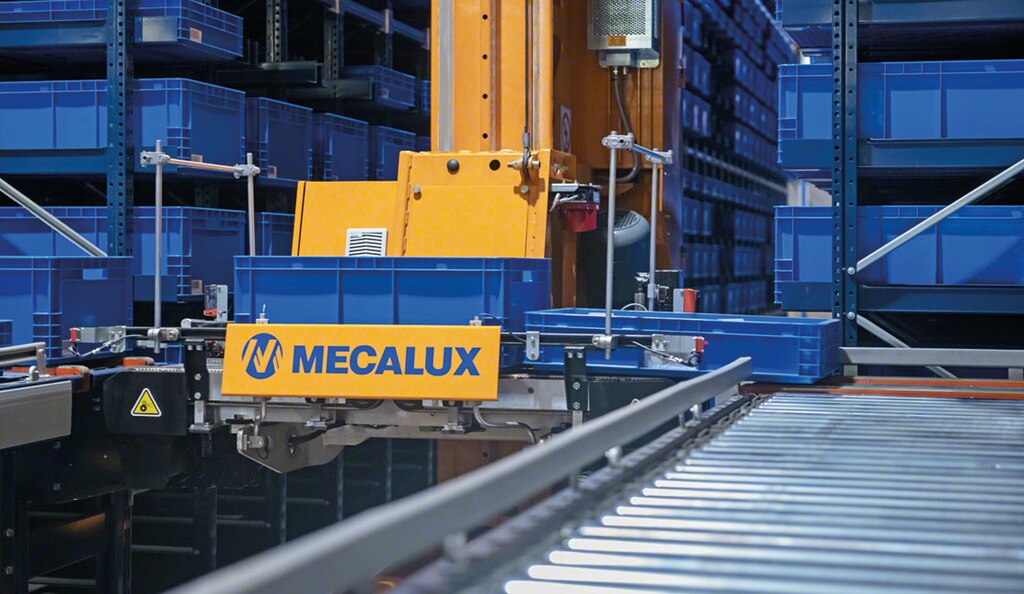
Which robots can be used for logistics?
In logistics automation, different machines and robots are employed to streamline processes, reduce logistics costs, and minimize the risk of accidents. Depending on the operations performed, the following robots can be used:
- Goods receipt and dispatch. Product receipt and dispatch tasks can be carried out with logistics robots such as automatic truck loading and unloading systems, which make it possible to insert and remove pallets from trucks autonomously and with minimal operator intervention. Automatic conveyors for boxes and pallets can also be used to speed up goods receipt and dispatch, two key warehouse processes with the highest number of daily movements.
- Storage robots. This category features stacker cranes — for both boxes (miniload) and pallets — which stand out for their capacity and agility when storing and retrieving items from the racks. There are several types of stacker cranes, including single-mast, twin-mast, and AS/RS trilateral stacker cranes. These logistics robots move horizontally and vertically in the storage aisles, inserting and removing pallets from the racks automatically. Businesses with a high volume of goods inflows and outflows can also opt for another very common automated solution: the automated Pallet Shuttle. With this compact storage system, an electric shuttle glides inside the storage channels, expediting pallet loading and unloading.
- Order picking. AS/RS for boxes exemplify the concept of logistics robots in order preparation. A single storage solution can include both a stacker crane for boxes and a conveyor for boxes; with this configuration, the operators remain at their pick stations, preparing orders according to the goods-to-person method. Another option to facilitate picking are industrial robotic arms, tasked with performing pick and place, i.e., removing products from one location to place and organize them in another.
- Internal goods movements. Logistics robots such as box and pallet conveyor systems are one of the most effective solutions for facilitating movements of goods in the warehouse because they make it possible to build very varied configurations to connect the various zones in the facility. Another conveying system used to link different areas in the warehouse are electrified monorails. Driven by an electric motor, these automatic trolleys move along an electrified rail suspended from the ceiling or fixed to the floor of the warehouse. Lastly, companies also turn to automatic guided vehicles (AGVs) or autonomous mobile robots (AMRs) to transport goods between the various working areas.
- Transportation. Drones have recently touched down in the logistics sector. Their technology enables them to transport and deliver customer orders by air. Although still being tested, this solution would bring advantages such as lower costs, faster order deliveries (compared to conventional distribution by truck), less highway traffic, and as a result, a significant reduction in pollution. This type of delivery would be especially useful in urban areas. But also has great potential in remote and isolated rural areas.
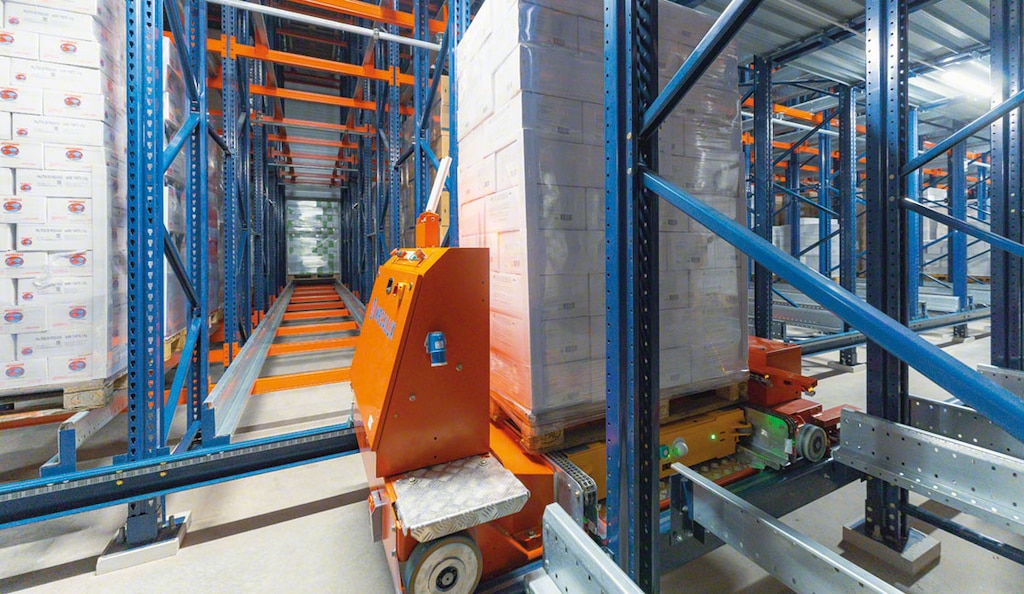
What’s the current situation with robots in logistics?
Logistics robots are poised to exceed their growth expectations. The Boston Consulting Group study Robotics Outlook 2030: How Intelligence and Mobility Will Shape the Future goes above the McKinsey forecasts, setting logistics robot sales at $80 billion by 2030.
The situation of robots in logistics is very favorable, as the symbiosis between these machines and humans greatly raises productivity. In automated warehouses, industrial robots complement operators in performing the more cumbersome and repetitive operations; thus, these employees can concentrate on higher-value tasks. According to McKinsey in its analysis Industry 4.0: Reimagining manufacturing operations after COVID-19, “process automation and physical automation or robotics can supplement labor capacity.”
But robots are not only responsible for carrying out the more burdensome tasks such as the movement, storage, and retrieval of goods. They also play a part in more complex logistics phases, e.g., dispatch and the shipment of orders during the last mile. In the research article The adoption of self-driving delivery robots in last mile logistics, prepared jointly by Nanjing Forestry University (China) and Cardiff Business School (UK), the authors say: “The demand for contactless delivery has expanded dramatically in 2020. Several technology companies are testing their autonomous robots to do last mile operations. While a parcel delivery by drones still has a few challenges to overcome, the other alternative of contactless delivery technology is becoming popular.”
The aim of automation is to drive efficiency in logistics and industrial operations. In his study Automated and Robotic Warehouses: Developments and Research Opportunities, Prof. René De Koster of Erasmus University Rotterdam (Netherlands) says: “The main advantages of automation are the saving of space (an automated warehouse can be built on a smaller area), savings in labor costs (a 24/7 operation can be achieved relatively easily and inexpensively), availability (it is not always easy to find unskilled personnel willing to do warehouse work), and savings on other operational costs such as heating and lighting.”
Logistics robots: welcome to the warehouse of the future
Logistics robots have arrived in warehouses and production centers to complement the tasks of operators and achieve maximum efficiency and productivity in complex operations such as order processing, the storage and removal of heavy loads, and the movement of goods around the facility.
These automated solutions are steadily gaining ground thanks to the emergence of technologies such as machine learning, the Industrial Internet of Things (IIoT), and big data, which boost the throughput of warehouse logistics robots and eliminate the risk of error due to manual management. Want to know how you could benefit from automating all or part of your facility with robots? Don’t hesitate to contact us. An expert consultant will offer you the best solution for your warehouse.