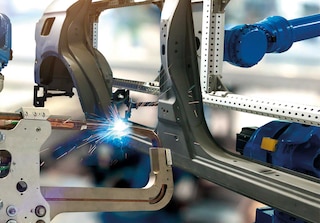
MRP: a production process milestone
Material requirements planning for manufacturing processes represents a complex challenge for any installation. How much raw material do I need? How many units have to be produced? These are just a couple of the questions that, for decades, manufacturers have found answers to with the help of an MRP (material requirements planning) system.
In this post, we’ll analyze everything involving material requirements planning: what it means, how it works, what advantages it has, and why it has been and still is so important in production processes. We’ll also explain the difference between MRP and ERP (enterprise resource planning) systems.
What’s MRP?
Material requirements planning is designed to manage production processes and coordinate in advance the manufacture, purchase, and delivery of the finished product.
MRP systems burst onto the scene in the 1970s, and their growth skyrocketed. According to the book Production Planning and Control: A Comprehensive Approach, written by D.R. Kiran in 1975, it was estimated that 700 companies used MRP systems to optimize their production processes. This figure rose by 174% annually, reaching 8,000 companies in 1981, only six years later.
Nowadays, MRP is considered the precursor to contemporary IT programs oriented towards improving industrial processes: MRP II (manufacturing resource planning), ERP (enterprise resource planning), CRM (customer relationship management), SRM (supplier relationship management), and the MES (manufacturing execution system).
MRP organizes manufacturing activities and optimizes stock management based on a business’s needs. Material requirements planning brings manufacturers closer to reaching their main goal: having on hand and at all times the exact material needed to produce the goods and deliver them to customers in the shortest time and at the lowest cost possible.
How does MRP work?
MRP systems require certain essential input data:
- Master production schedule: the MPS shows the number of items to be manufactured and the time frame for this.
- Bill of materials: the BOM specifies the raw materials, quantities, and manufacturing processes required for obtaining a final product unit.
- Inventory record file: this details stock-related information (available inventory, stock on-demand, cancelled orders, lead times, etc.). It lets you know which raw materials are available for immediate use.
With all these input data in hand, the material requirements planning system generates the following output data:
- Recommended master production schedule: the MRP system draws up a calendar with dates associated with the production process (start and end), the quantities for each step of the road map, and the bill of materials. The aim of this is to meet the demand specified in the master production schedule.
- Recommended procurement schedule: this displays the dates on which the purchased materials will arrive, as well as the dates on which new orders should be placed so as to coincide with the manufacturing schedule.
This way, the MRP system ensures that you’ll receive the right amount of materials to maintain a minimum inventory level to be able to supply production and, at the same time, efficiently plan your manufacturing, procurement, and material delivery activities.
Example of material requirements planning
After preparing the master production schedule and bill of materials, you deduce that, to manufacture the final product (product X), you need 2 units of material A and 1 unit of material B. For every unit of material A, you require 3 units of part C. And for every unit of material B, you need 2 units of part C and 4 units of part D.
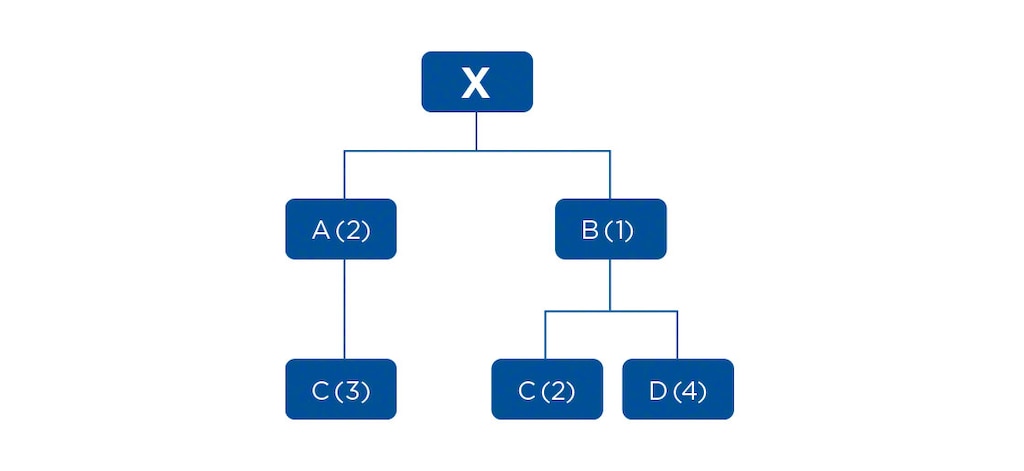
Then, you fill in the inventory record file (IRF), which reflects the available stock and the lead time for each product:
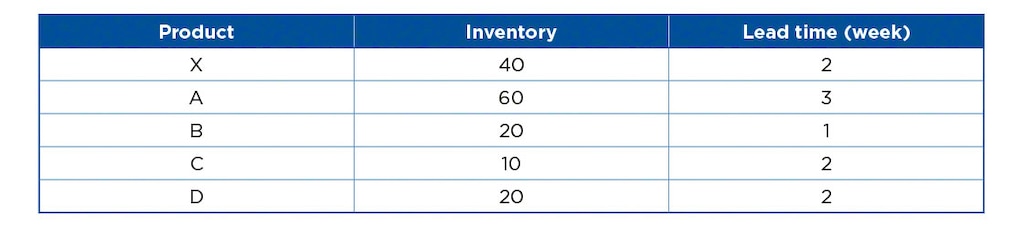
This sums up material requirements planning in the event that you have to produce 100 units of product X in 10 weeks:
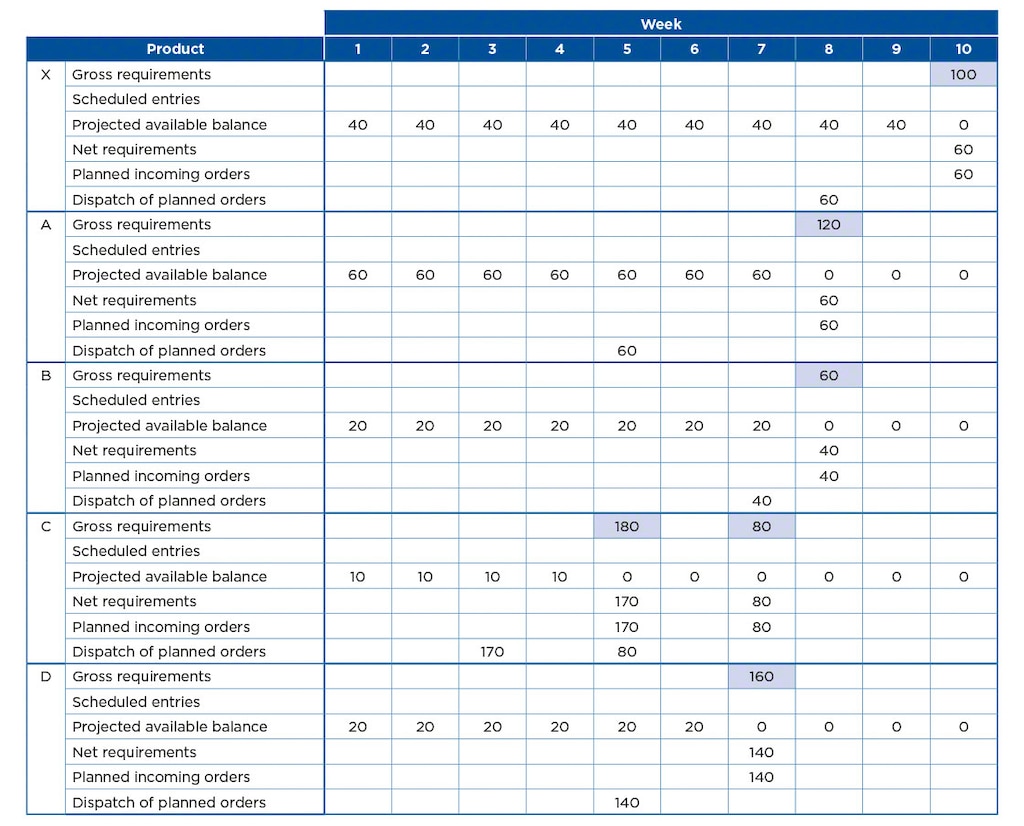
The table reflects that, to have 100 units of product X by week 10, you need 60 additional units that will be added to the 40 units already available in your inventory. Given that we’ve defined the lead time for product X as 2 weeks in the inventory record file, the order must be placed by week 8.
If 2 units of product A are required for every unit of product X, by week 8, you’ll need 120 units of product A. Since you already have 60 units of it in your inventory, the net requirement for product A will also be 60 units. Taking into account the lead time, these units will have to be requested three weeks in advance.
Following the same procedure, we can establish the net requirements for products B, C, and D, as well as the week they need to be ordered.
MRP functions and advantages
In production processes, material requirements planning is responsible for calculating the necessary raw material and components and the amount of finished product to manufacture.
Material requirements planning provides the following benefits:
- Total availability of raw material for production.
- Fulfillment of delivery deadlines.
- Maintenance of low inventory levels, of both raw material and finished product.
- Planning of manufacturing, delivery, and procurement activities.
- Cost reductions.
The MRP system solves many of the problems manufacturers face on a daily basis, especially involving the procurement of raw materials. An incorrect or insufficient purchase could delay delivery times and, in the case of buying more material than necessary, result in extra storage costs.
Differences between MRP and MRP II
At the beginning of the 1980s, MRP (material requirements planning) evolved into MRP2 (manufacturing resource planning), a more advanced system with a broader scope. Generally speaking, the main differences between the two systems are as follows:
- In addition to planning the management of the materials needed for production, MRP II integrates other departments within the company, such as sales, accounting, etc.
- While MRP works according to the master production schedule, MRP II is based on market and demand forecasts.
- MRP II analyzes the behavior of the business to execute efficient planning, while MRP does this on the basis of the company’s practices and previous experience.
- MRP is an open system as opposed to MRP II, which is closed. This means that the reports generated by MRP II can be fed back into the system, making it possible to adjust planning so that it’s more accurate.
MRP II is the modern version of MRP. Besides responding to the question of how many and when to manufacture, it also defines the resources, their quantity, and the time at which this production should be carried out.
Differences between MRP and ERP
ERP (enterprise resource planning) systems were first used in the 1990s, and they’re even more complete and versatile than MRP, their predecessor. What sets ERP apart is its ability to consolidate all the areas of a company into one system.
In other words, MRP is software that works alone, while ERP systems integrate with and combine the IT systems used by each department in order to create a centralized database. This way, any of the firm’s areas can access information in real time, control workflows, minimize errors, and communicate with other departments.
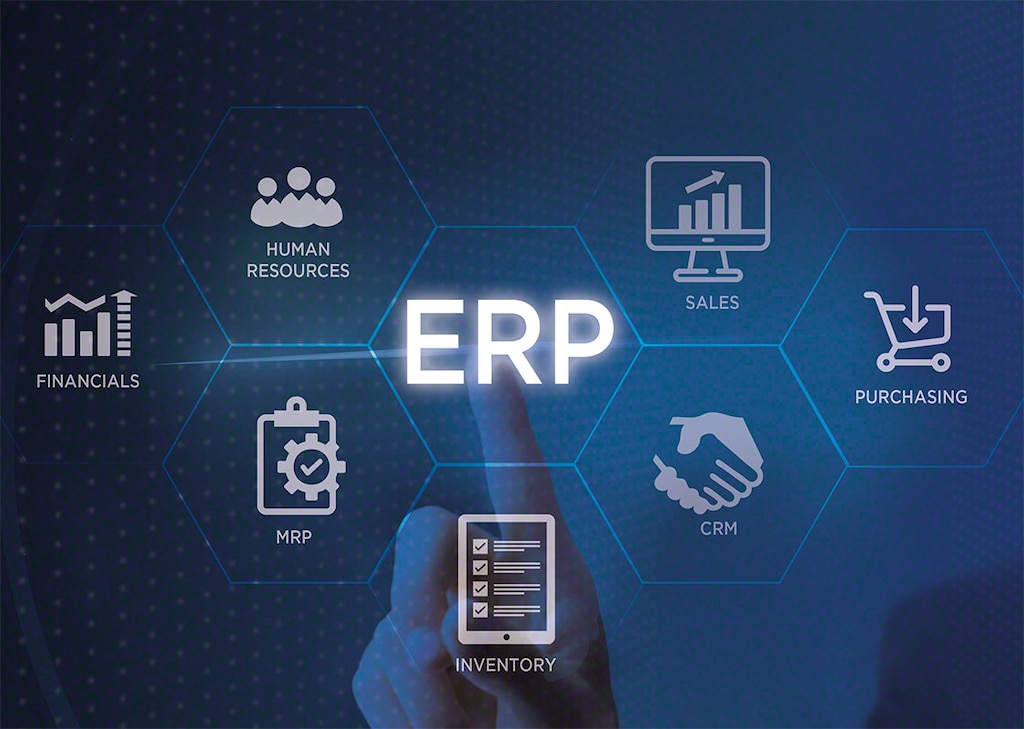
MRP: in the wake of technology advances
After being employed in industry for the past fifty years, we can affirm that material requirements planning has marked a before and after in production processes. Charged with anticipating companies’ needs to be able to plan for them, its function has been adapted to new technologies with a view to boosting supply chain profitability.
At Interlake Mecalux, we’re committed to providing the most cutting-edge technology solutions on the market for both storage and logistics management, such as Easy WMS. It can be integrated with any ERP software to ensure that both systems transfer data and information aimed at increasing warehouse productivity.
Be sure to get in touch. Our team of specialists will help you get the most out of your supply chain.