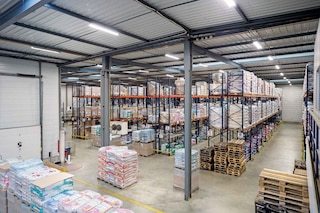
8 warehouse organization ideas to increase efficiency
Are you one of those managers who needs warehouse organization ideas in order to achieve better productivity, fewer accidents, more stock control, and maximize storage space? An unbeatable way of achieving this is to follow our eight tips below, which will help you to improve your warehouse organization properly and stop wasting time and money.
1) Revise your warehouse’s design
The first key element and often the motive behind a poorly organized installation is the warehouse’s design. If it isn’t consistently organized, your facility will not reach its full potential.
When it comes to your space, keep the three following issues in mind, among others:
- Your workflows: Be sure to have a clearly defined space needed for production zones and workflow areas.
- Access to goods: Do your operators need access to the goods? Some types of racks offer direct access to pallets and others don’t. So, have you opted for the right solution?
- Your storage capacity: If there are gaps in storage space purposing, this means that you are losing out on the opportunity to store more goods.
2) Label your goods properly
Imagine you are in the middle of high season and have to process more orders than usual; and, to deal with this increased activity you hire non-permanent staff. Keep in mind that work done by new operators is a non-money maker if your goods have not been labelled meticulously. In fact, these last issues waste time during the order picking process, as well as your organization’s money.
Labels often include GS1-128 barcodes. These codes have numeric and alphanumeric characters that detail a product’s characteristics, such as its batch number, manufacturing date, and expiration date. Mislabeled goods could be missing this important information.
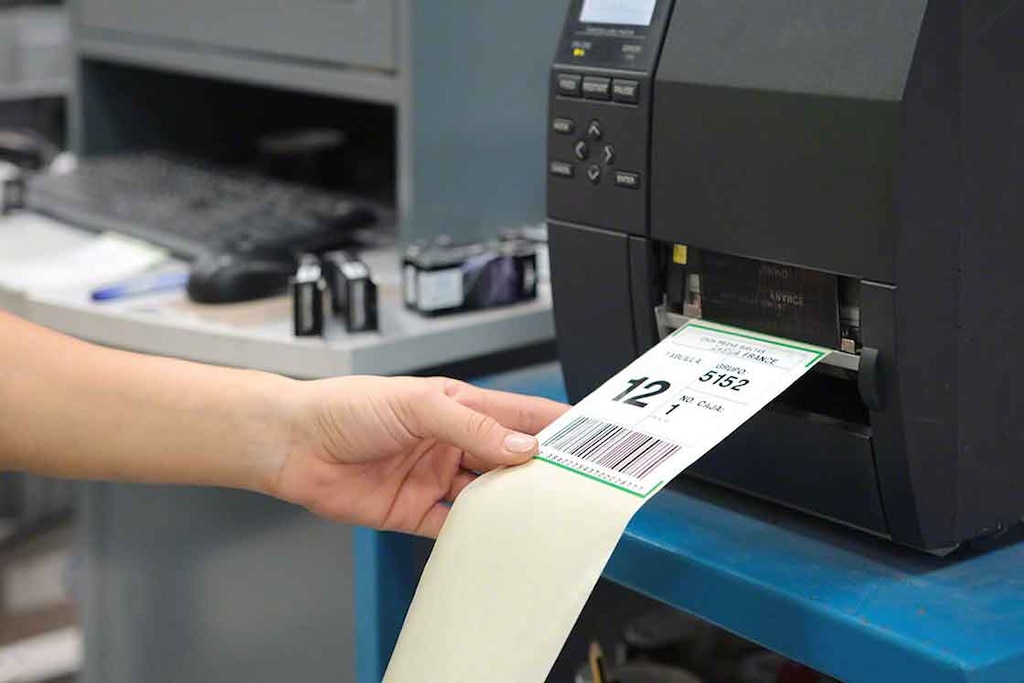
3) Select the best storage system
This is one of the more important warehouse organization ideas. Do you only use a fraction of the storage capacity available in your logistics center? If the answer is ‘yes’; rethink the storage solutions that you are using. Selective pallet racks, for example, have the ability to adapt to any unit load, weight, and volume. These types of racks are good for warehouses that need to store very diverse products and pallets of different sizes and characteristics. Meanwhile, high-density racks, such as drive-in drive-thru pallet racks, pallet flow racks and push-back racking systems, make the most of the surface area and provide a higher storage capacity.
Automated storage systems are also an option for warehouses with high goods flows. This type of solution better leverages available space, offers more control of the goods, ensures agile operations, and greatly reduces errors that would otherwise occur with manual product management. Examples of automated storage solutions include stacker cranes (AS/RS for pallets), miniload systems (AS/RS for boxes), and pallet conveyor systems.
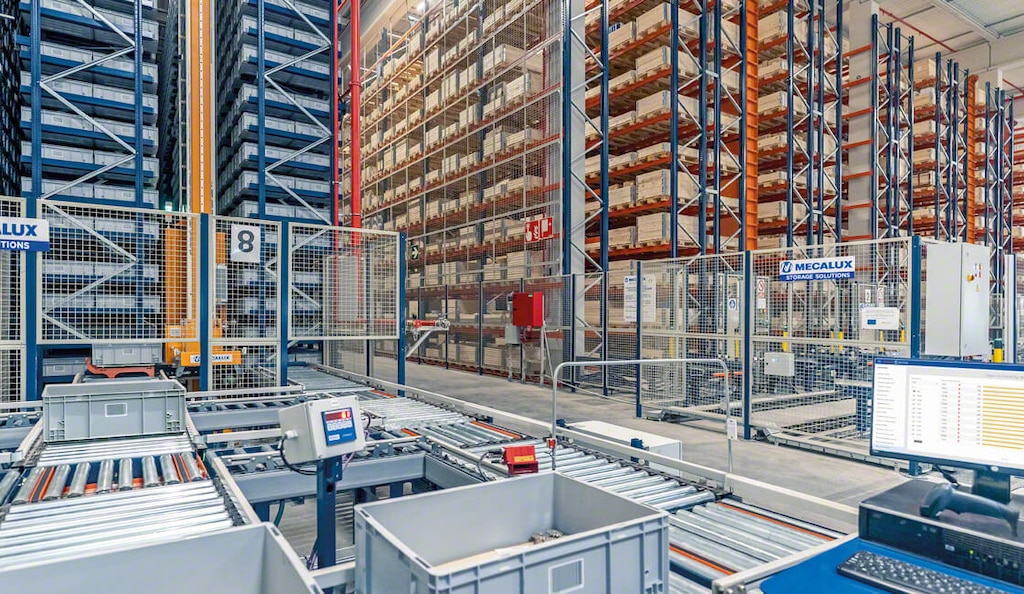
4) Call a consultant
Logistics consulting businesses offer services for logistics professionals to help them smooth out their entire supply chain.
To renovate your warehouse or purchase a new storage solution, whether automated or not, these business professionals will help take an in-depth look at your needs and detect flaws in your current logistics management; in this case, rethinking your warehouse’s organization.
Given that these organizations assess companies on a daily basis, they will also have a better understanding of the situations you could run into.
5) Improve inventory organization
Warehouse organization is important for avoiding stockouts, reducing storage costs, and managing perishable products, to name a few aspects. It’s crucial to analyze products in the warehouse according to the ABC analysis. “A” products are considered to be of the highest turnover and are consumed the most. “B” products are of average turnover, and “C” products are the ones that are consumed the least. Category A products should be stored closest to the loading docks, while category C products need to be located further away.
It’s also necessary to determine whether inventory should be managed according to the FIFO (first in, first out) method, in which the first SKU slotted is the first to leave the warehouse, or the LIFO (last in, first out) method, whereby the last product stored is the first to exit. This leads to better and more streamlined product flows.
6) Optimize picking processes
One of the best ways to improve picking processes is to minimize as much as possible the distances operators need to travel to retrieve the goods needed to complete orders. This can be done by deploying a warehouse management system (WMS). This software tells operators the exact number of items that must be retrieved and the routes that must be followed so they travel the shortest possible distance in the warehouse. This way, they can prepare a greater number of orders more efficiently.
It’s also a good idea to choose the appropriate picking methods. Among them, three main types are most commonly used. With piece picking, operators complete orders one at a time, in sequence. In contrast, wave picking involves the preparation of different orders all at once. Zone picking is the third most commonly used method, whereby operators collect different orders at the same time in the same warehouse area.
To optimize picking even more, it may be necessary to utilize automated solutions, such as automated storage and retrieval systems (AS/RS) for boxes. These systems apply the “goods-to-person” picking method in which the products needed to complete orders are brought directly to an operator at a pick station. This prevents the need for operators to travel the warehouse, thereby saving time.
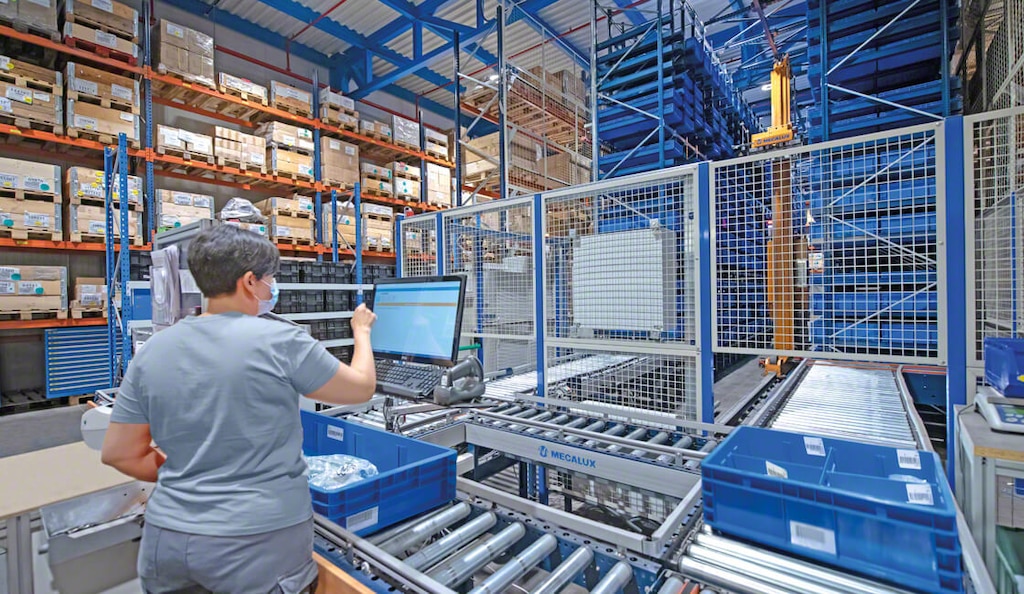
7) Enhance goods receipt processes
Correctly organizing goods receipt processes is vital to having an efficient warehouse and managing operational expenses. In this vein, it’s important to determine how the loading docks are organized when reviewing a warehouse’s layout and to assess how many access points are necessary based on the loading docks’ characteristics.
Here again is where a WMS may also play a role in optimizing goods receipts, as it can help you to prepare for incoming stock. The software will register the goods in the system and prepare a label to properly identify the inbound items. Then, it can assign the proper storage location to the goods in order to maximize space in the warehouse.
Another good warehouse organization idea when it comes to goods receipt is to automate some of these processes. For example, it may be helpful to incorporate conveyor lines next to the loading and unloading docks to prevent operators from having to make long trips in the warehouse.
8) Implement a WMS
We’ve already mentioned how a warehouse management system can improve picking and goods receipt processes, but a WMS is a good warehouse organization idea for many other requirements as well. For one thing, a WMS, such as Interlake Mecalux’s Easy WMS, greatly reduces errors in inventory management and other warehouse processes, which reduces costs and improves a company’s image.
Deploying a WMS can also result in greater storage capacity, enabling facilities to quickly dispatch orders. The software determines the best location for products (warehouse slotting), which maximizes space utilization. And Easy WMS, in particular, features modules and functionalities that tailor the software to a company’s specific needs. For these and many other reasons, a WMS is a good idea to give your warehouse organization a boost.
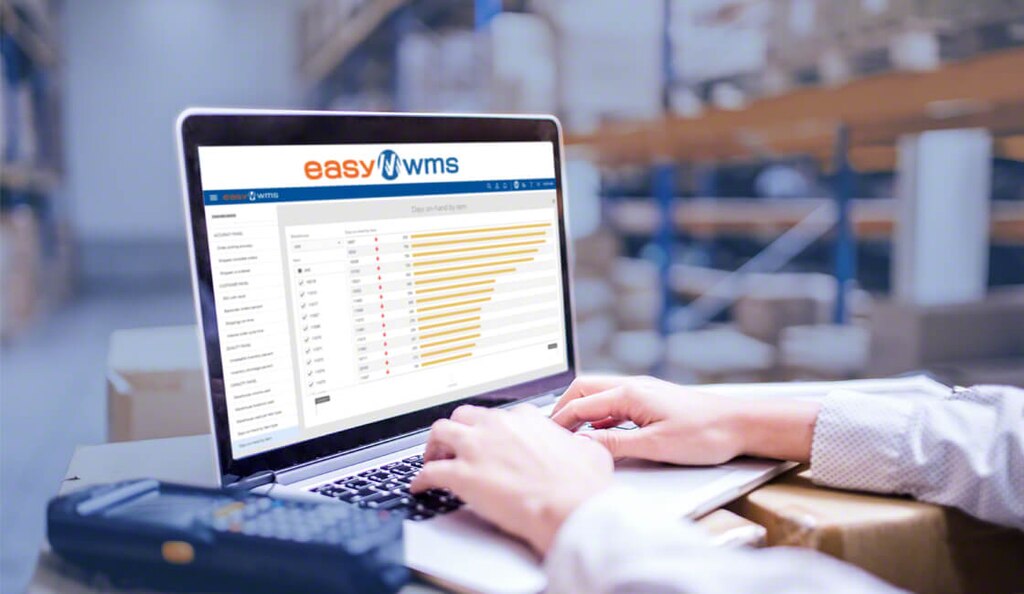
Ideas for a better organized warehouse
By applying these eight warehouse organization ideas in your facility, you’ll greatly improve your warehouse management. These tips are vital for improving order preparation, streamlining inventory management, and maximizing storage space, to name a few.
Keep in mind that using warehouse management system goes a long way towards improving your warehouse’s organization. Deploying a WMS will help you to better arrange your facility by giving a boost to your goods receipt, stock management, and order dispatch processes, among others.
So, if you’re looking for more ideas to enhance your warehouse organization, don’t hesitate to contact us. Our team of expert consultants can help you analyze your facility and show you how our solutions can aid in optimizing your warehouse processes.