
Warehouse slotting: how to hit the jackpot
The objective of warehouse slotting is to put the appropriate product in the right place so that it can be efficiently picked at the right time.
In doing this, warehouse slotting criteria determine the way products are organized in each location. Which ones are most commonly used? What factors should you consider when choosing one or the other? Let's take a look at this in more detail.
Most common slotting strategies
There are two major types of rules:
- Fixed or static slotting: each SKU stored is assigned a specific position beforehand. This facilitates the location of products without the need for an IT system to record this information.
- Chaotic or random slotting: goods are placed in available spaces as they are received at the installation. To carry this out successfully, it’s essential to use a warehouse management system.
It should be mentioned that many storage installations apply mixed slotting criteria that combine both product organization methods.
Which slotting system should I use?
Employing one slotting approach versus another will depend mainly on three major points:
1. Study the characteristics of the SKUs stored:
- Physical product attributes: the volume that the goods occupy (height, width, and length measurements) and their weight are vital for determining the space needed to maneuver and, thus, deducing the most appropriate storage systems. For example, heavier products will be placed on the lower level of the racks whenever possible. A uniform method — preferably automated — should be used to measure each product, thereby preventing possible deviations. In this vein, it’s customary to designate several standard box sizes in which any SKU can fit in order to simplify the packaging process.
- Other characteristics affecting merchandise storage and slotting: these include, among others, compatibility with other goods (the storage of chemicals is regulated by law), weather resistance (storing products in outdoor warehouses can bring down costs), and expiration dates of perishable products (they have to be arranged by date, in specific temperature and humidity conditions, and their batches must be traceable).
2. Analyze available storage systems and the warehouse layout
- Establish a naming system to identify all the locations: the more detailed, the more complex, but also the more precise. At the very least, this classification should identify the channels or shelves of each height level and each space with numbers or letters. Of course, other elements can be added, such as installation, aisle, container, and/or area.
- Calculate the warehouse storage capacity and occupancy: if it exceeds 90%-95%, it would be advisable to review your slotting criteria to see whether space is being leveraged effectively. You also have to take into account the specific kind of industrial racks used, particularly when it comes to high-density or direct-access systems. Generally, the former are better suited for inventories with many pallets per SKU, while the latter are more versatile when managing few pallets per SKU.
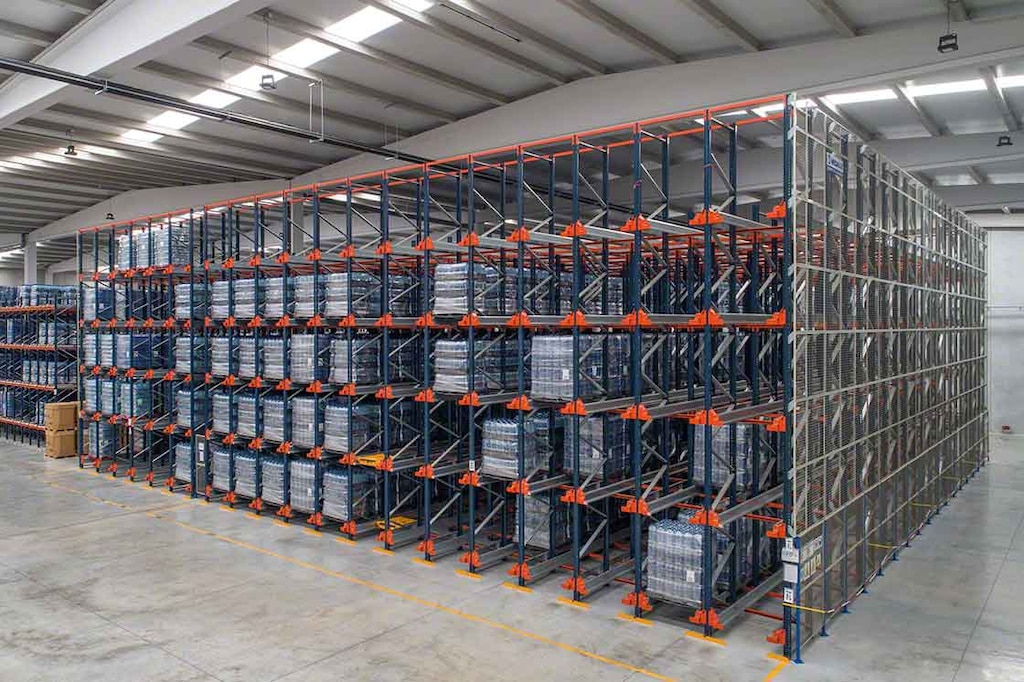
3. Examine goods and operator movements in the warehouse
- Goods movements:
1. Stock turnover: this allows you to arrange products by the frequency with which they’re removed from the installation. It’s directly related to demand over the course of the year. Following the ABC method, the general warehouse slotting rule consists of positioning higher-turnover goods closer to the receiving/shipping docks and placing goods in further away locations as SKU turnover decreases.
2. FIFO or LIFO methods: these refer to the order of the goods flow. With FIFO (first in, first out), products that arrive most recently are the first to be shipped out. On the other hand, LIFO (last in, first out) flows mean that the goods received most recently are the first to be dispatched.
- Operator movements:
The distance traveled by each operator depends primarily on the picking method employed, the accessibility of products on the racks and the handling equipment and automated systems used. For example, conveyors and stacker cranes reduce the manual maneuvers operators have to make and the routes they need to take.
The aim of warehouse slotting management is to maximize storage capacity, minimize movements, and adapt each location to product characteristics.
Thanks to our Easy WMS software, we can perform an in-depth analysis of the location rules in your warehouse and, thus, optimize your inventory. Get in touch! We’ll help you to define the slotting criteria that best suit your installation.