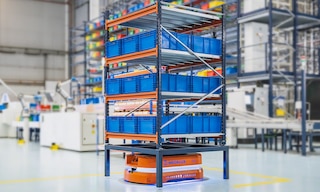
Shelf-to-person: an innovative order picking solution
Shelf-to-person is an order picking method that came about through technological advancements in intralogistics, coupled with the growing demand for faster picking operations.
What is the shelf-to-person system?
Shelf-to-person is an order picking method involving autonomous mobile robots (AMRs). These automated vehicles move picking shelves to operators, who then retrieve the products they need to put together each order.
The shelf-to-person system represents a major development compared to traditional picking techniques. That is, operators no longer have to travel around a facility to locate the items required to fulfill orders. Instead, merchandise is brought to them autonomously.
This method can also be considered a variation of goods-to-person systems, in which automatic equipment such as stacker cranes or conveyors deliver materials to operators’ pick stations. In the case of shelf-to-person, AMRs move the picking shelves to the operators, fostering efficient order fulfillment.
What type of software controls the shelf-to-person system?
Shelf-to-person eliminates the need for operators to walk around the warehouse looking for products. With this solution, they remain at their workstations as the AMRs deliver goods to be sorted and included in orders for shipment. Shelf-to-person order picking calls for AMRs capable of carrying shelving units to pick stations.
Interlake Mecalux’s AMRs move safely and effectively through the coordination of three specific software solutions:
- Warehouse management system (WMS). Programs like Interlake Mecalux’s Easy WMS organize logistics processes such as order fulfillment. This solution distributes work among operators, sending them instructions to ensure error-free task completion.
- Fleet management software. This system oversees robot traffic and allocates tasks among the available AMRs in the facility. It tells each AMR which shelving units to locate and transport to operators for order picking.
- Navigation software. Integrated into each robot in the fleet, this program calculates the most efficient route to carry the goods through the warehouse. It also detects obstacles, adjusting the vehicle’s trajectory in real time.
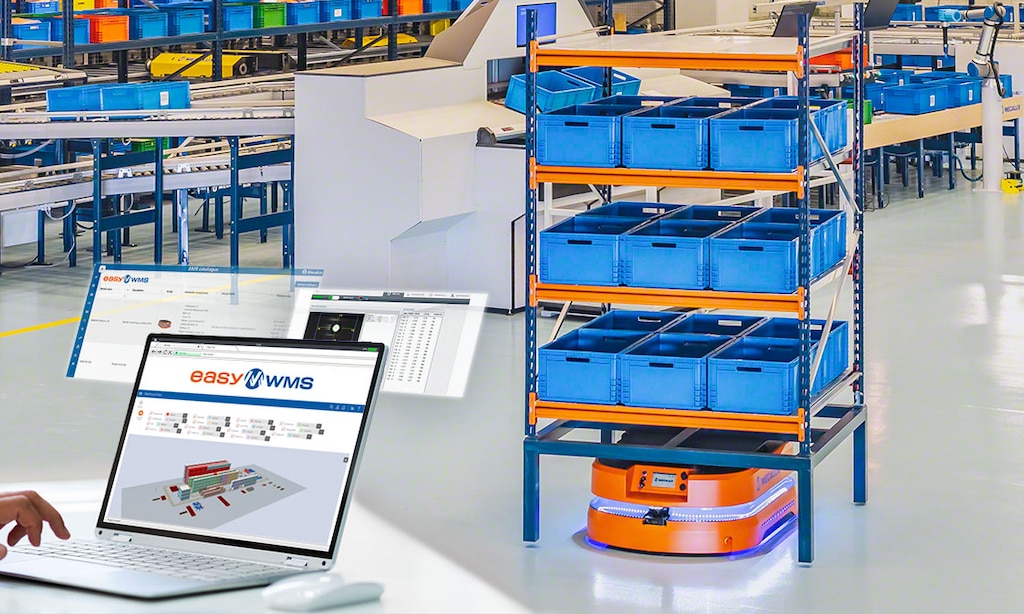
How does the shelf-to-person system work?
Shelf-to-person picking with AMRs typically works like this:
- Order receipt. When the logistics center receives an order, the WMS records the information, determines which products to pick, and distributes the work among operators.
- Dispatch of robots to shelves. The WMS software informs the fleet manager of the orders to be fulfilled. The fleet manager then commands the robots to move to the corresponding shelves.
- Transport of shelving units. Aided by the navigation software, the AMRs travel to the shelving units containing the merchandise needed to fill orders. The AMRs then transport those shelves to the operators at their pick stations.
- Selection of goods. As directed by the WMS, the operators retrieve products from the shelf and sort them into boxes, totes, or other shipping units in which items for the same order are gathered.
- Continuation of picking. The robots bring the operators as many shelves as they need to fill orders until all the required goods are collected.
Once picking has finished, the orders are packed and distributed to customers. Moving products to operators automatically streamlines order fulfillment and shipping. Additionally, it reduces fatigue and the risk of injury.
What are the advantages of the shelf-to-person system?
Shelf-to-person picking offers a series of benefits, making it an attractive solution for warehouses with large order volumes:
- Increased efficiency. AMRs transport loaded shelving units swiftly. This allows operators to prepare more orders in less time, enhancing company responsiveness.
- Flexibility. Shelf-to-person picking adapts easily to different product types and changes in a facility. This system can be used in warehouses that handle a broad range of materials, from small items to bulky goods.
- Optimal working conditions. To perform picking, operators don’t have to travel vast distances or lift heavy loads. This lowers the risk of injury and improves occupational safety and health.
- Error reduction. Minimizing operator travel in the facility reduces the possibility of errors when selecting products. Bringing merchandise directly to operators streamlines the process.
- Space optimization. Shelf-to-person picking helps optimize the storage space by positioning products more compactly.
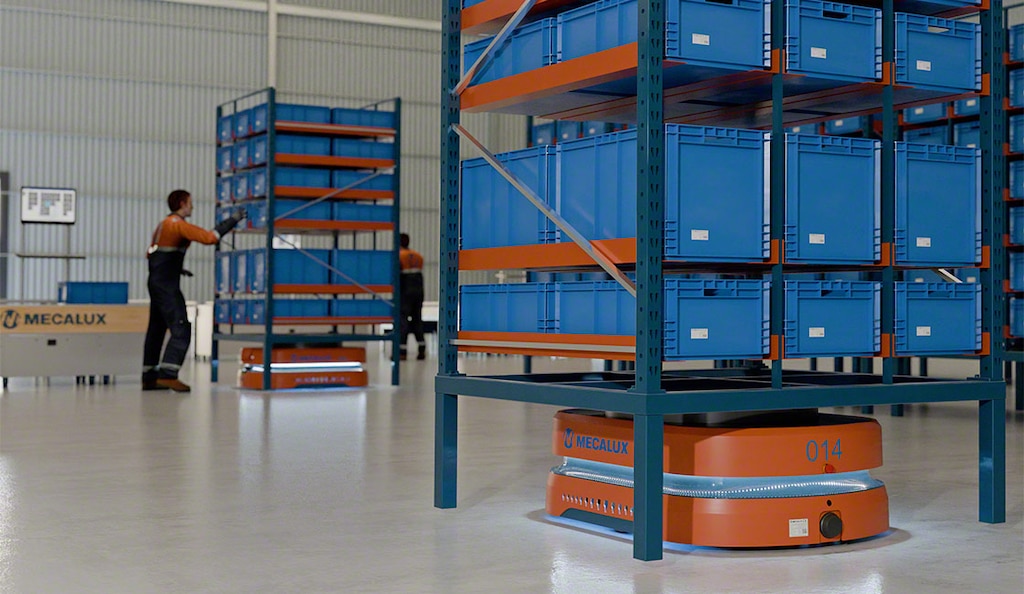
Innovative picking with the shelf-to-person system
Shelf-to-person is a revolutionary solution for raising efficiency and productivity in order processing operations. This picking method makes the most of technological advances in intralogistics to meet current market needs expeditiously and effectively.
The automated solution — facilitated by AMRs — expedites the order fulfillment process. Interlake Mecalux’s line of AMRs transports a wide variety of loads, from boxes, totes, bins, and trays to pallets and shelving. Be sure to contact us if you’re planning on implementing the shelf-to-person system in your warehouse.