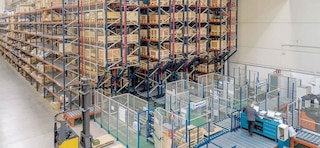
Lean logistics: leaning into efficiency
The Lean logistics methodology is a management and operations organization philosophy of Japanese origin. Applying Lean logistics to the supply chain consists of identifying and eliminating activities that don’t add value in order to increase product flow and, thus, minimize costs.
The Lean concept is all about doing more with less, specifically: less effort, less equipment, less space, less cost and less time.
This set of methods — developed by Taiichi Ohno at Toyota — was initially applied in the industrial production field; hence, it was called Lean manufacturing.
Principles of the Lean logistics methodology
The objective of Lean logistics is to reduce logistics costs, with an emphasis on identifying and trimming tasks that don’t contribute added value to the process. This, consequently, shortens the order cycle time. Ultimately, Lean logistics consists of a constant search for efficiency, which can be broken down into several phases or principles:
1. Pinpoint activities that add value for the customer
Tools such as value-stream mapping facilitate this first step, which focuses on highlighting all the tasks that make up a specific process. For example, in the warehouse, picking operations are divided into various phases, each of which can be broken down into subprocesses.
2. Identify waste and, simultaneously, opportunities for improvement
In logistics, waste is often related to lost time, as we will see below. To correctly execute this stage, it’s essential to standardize tasks and maintain cleanliness and organization throughout the installation.
3. Create a new, optimized process flow
This refers to designing a new, more effective working method in terms of time spent and service quality. To do this, you have to do away with unnecessary tasks deemed wasteful.
In addition to organizational changes, this phase can entail investments in new technology or systems that help to eliminate phases that take up extra time but fail to provide value.
4. Choose pull strategies to minimize inventory
Stock held in the warehouse determines a large part of logistics costs. As opposed to push strategies, which are based on producing according to sales forecasts, pull manufacturing methods are centered on attracting sales first and responding to them by swiftly supplying the product.
5. Standardize new processes and maintain change over time
To do this, it’s necessary to involve and motivate all workers. They have to be provided with proper training to acquire the new habits and much-needed skills that make up Talent 4.0.
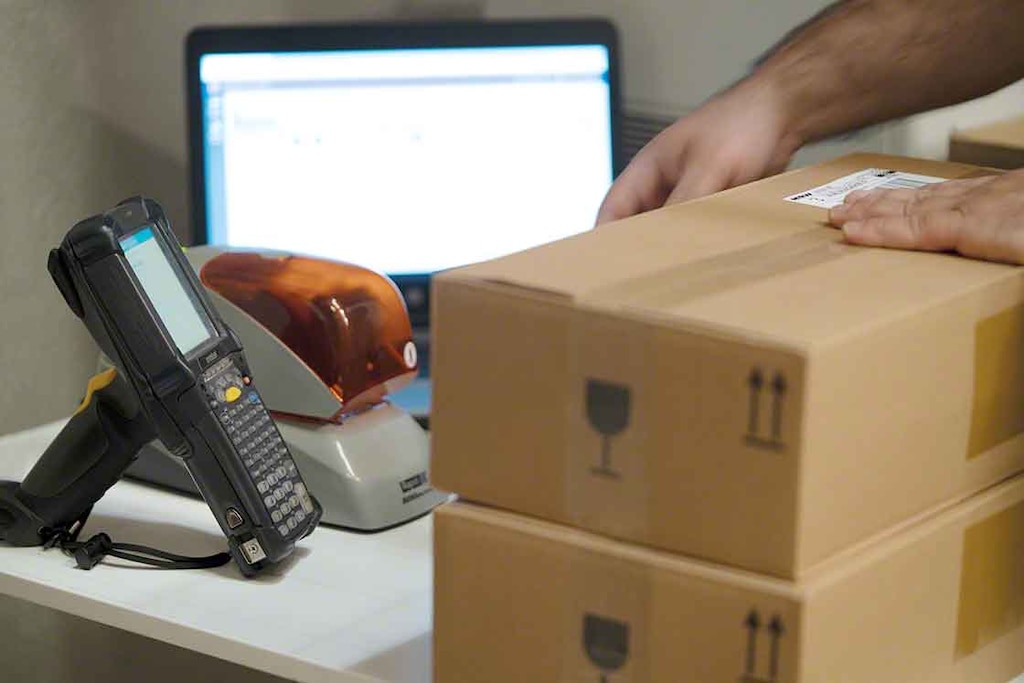
Lean logistics and the fight against waste: how to combat it
Waste can be classified into four major groups. Let’s take a close look at its characteristics and how it can be minimized:
- Excess stock stored
The causes of this undue increase in stock are usually linked to excess production in manufacturing companies, but also to inaccurate demand forecasting.
On occasion, safety stock is what swells under the pretext of “being covered.” Yet, in the end, it actually “covers up” poor supplier management and/or disorganized material flows.
This squanders warehouse space, leading to increased storage costs and low-turnover stocks that are seldom replenished.
How can you tackle this from a Lean logistics perspective?
To follow the tenets of Lean logistics in this situation, you need to work, in particular, on the factors you can control (as opposed to other more volatile ones, such as demand forecasting). Several strategies that can be implemented in the warehouse are:
- Cross-docking, which keeps stock stored to a strict minimum.
- The just-in-time system, in supplier management and warehouse organization.
- Shortened lead times, with respect to suppliers and intralogistics processes. This facilitates demand forecast calculations: the closer in time they are, the more accurate they will be. Thus, you won’t be overstocked.
- Wait times and bottlenecks
Lean logistics is based on slashing the difference between execution times (working time you pay your employees) and standard times (time you charge the customer). This operation will translate into cost savings, as inefficiencies will be exposed.
The causes can be very varied and usually relate to a badly designed work method, incidents not dealt with, or operator workload imbalances.
How can you solve this from a Lean logistics point of view?
- To organize tasks in the installation and prevent bottlenecks and downtime, there’s no better tool than a warehouse management system. This software enables the installation to process huge volumes of information and organize it by prioritizing process optimization.
- Be sure to measure and monitor each operator’s workload so as to prevent some from remaining idle while the others are overloaded. The Labor Management System module for Easy WMS addresses precisely this issue.
- To ensure that equipment failure doesn’t slow down warehouse activity, it’s advisable to have a preventive maintenance plan for the handling equipment and automated systems used throughout the installation. It’s also a good idea to have technical support so that incidents can be resolved as soon as possible.
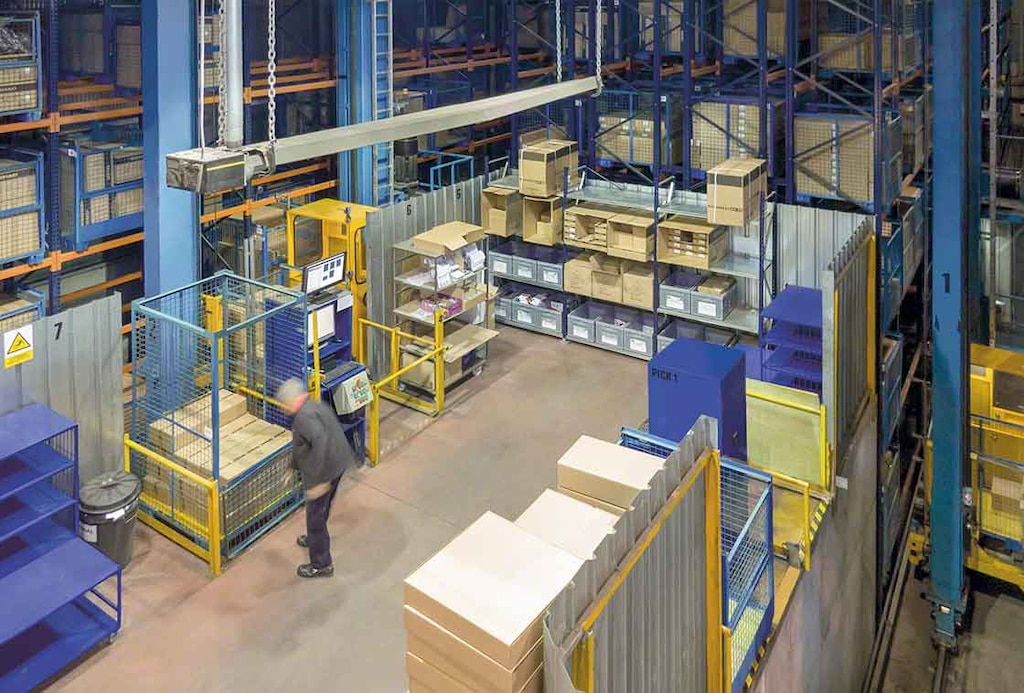
- Unnecessary travel and movements
Picking and order prep tasks are those that take up the most time in the daily activity of the warehouse. For that reason, poorly planned picking lines can be detrimental to productivity — they can result in wasted trips (for example, using unloaded equipment) or an increase in extra movements.
How can you resolve this with the Lean logistics methodology?
- Automating load handling is a great way to cut intralogistics transportation times. At the same time, it improves safety in all operations. In fact, automation achieves excellent results when it comes to processes with repetitive movements. Likewise, stacker cranes, for example, can work in combined cycles, leveraging all movements by carrying loads.
- The particular order preparation method used also affects wasted movements. In this vein, WMSs organize picking routes in the warehouse, prioritizing goods consolidation or groupage and adjusting times to dispatch schedules.
- Errors leading to returns and repeated processes
Generally speaking, higher quality levels are usually associated with greater costs, but this isn’t always the case. As a matter of fact, the top firms in the logistics sector (many of which implement Lean logistics) are known for offering excellent service at a reasonable price.
Why is this? Mainly for two reasons: they almost always get it right the first time (so they don’t have to do the work twice), and, because of this, they can charge more: they’re backed by exceptionally efficient service.
How can you remedy this from a Lean logistics standpoint?
- If returns management is complicating your warehouse operations, you should stop to analyze the causes for the returns. In the case of returns stemming from mistakes in order prep, once again, the use of a WMS as picking software enables you to reduce these errors drastically and enhance the overall service quality.
- Identifying incidents in time is a good practice that does away with the need to do the work twice or repeat tasks.
Lean logistics methodology, centered on waste reduction
The basic premise of the Lean logistics concept is that, when buying a product, the customer doesn’t pay for activities that don’t add value to the supply chain. This methodology aims to eliminate waste that hampers a company’s logistics profitability.
At Interlake Mecalux, we align ourselves with our clients and work side by side to reach their objectives through our automation and software solutions for warehouse optimization. Feel free to get in touch — one of our consultants will be happy to accompany you on the road to Lean logistics.