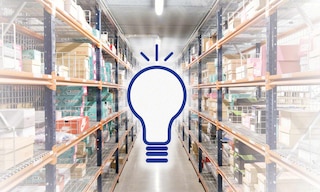
Warehouse lighting: a question of productivity, safety, and savings
Warehouse lighting is an essential issue when it comes to ensuring that operations performed in a logistics facility are carried out safely. In addition to storing goods, warehouses are responsible for order processing, inventory control, and kitting, which all require adequate lighting.
To choose the ideal industrial warehouse lighting, companies have to consider several variables: the sizes and characteristics of the logistics facility, the distribution of the storage systems, and the existence of natural light, among others. It’s also critical to bear in mind the activities done by the operators. Illuminating a facility that only receives and dispatches pallets isn’t the same as lighting one in which operators have to prepare orders containing a multitude of SKUs.
When choosing warehouse lighting, energy savings is a factor to take into account. Businesses look for solutions that, in addition to ensuring greater wellbeing and safety for operators, help to reduce the electricity bill and, as far as possible, CO2 emissions.
Advantages of proper warehouse lighting
Good warehouse lighting means that tasks will be performed safely and efficiently. Investing in a suitable lighting system also entails cost savings due to lower power consumption and fewer errors.
- Protection of operators’ health. Inadequate lighting can lead to fatigue, tiredness, headaches, and stress. Likewise, sudden changes in light temporarily blind the eye until it adapts to the new illumination. With the right warehouse lighting, operators work in a healthier environment.
- Improved safety. Aisles and work areas must be properly lit for operators to perform their tasks safely. A well-lit facility significantly helps to minimize the risk of accidents.
- Increased productivity. Both too little and too much light can cause workers discomfort. Lack of visibility is extremely frustrating when performing certain tasks. On the other hand, with appropriate lighting, operators can concentrate on their work and be more accurate.
- Energy savings. With suitable warehouse lighting, organizations can considerably reduce their electricity bills.
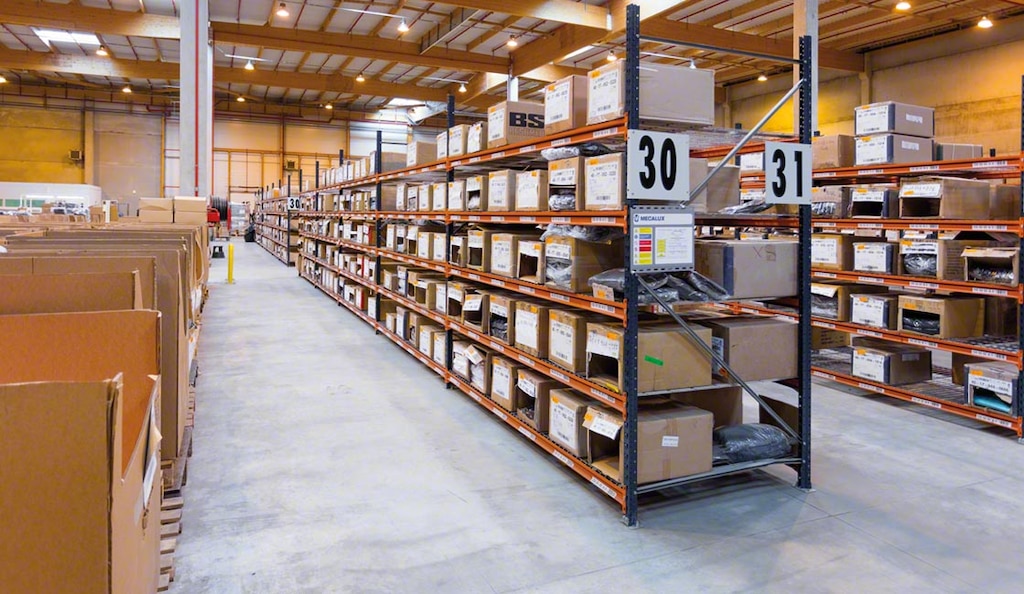
Warehouse lighting: how should it be configured?
When designing warehouse lighting, it’s necessary to carry out a prior study to decide on the ideal location for the light fixtures. As a general rule, lights are usually placed on the ceiling and in the center of the aisles to prevent the racks from creating shadows.
Before choosing the warehouse light fixtures, you have to take into account factors such as the light level — measured in lux or lx — which must be adequate to ensure operators’ visual comfort and wellbeing. Another value to consider is the Unified Glare Rating (UGR), which denotes the level of glare generated by a light source. This factor is contingent on the placement of the lighting (height, angle, location, etc.) as well as the number of lights. Lastly, you need to assess the color rendering index (Ra), which consists of the ability of a light source to reproduce the colors of the objects it illuminates.
With all these variables in mind, LED lighting is the most appropriate for a logistics facility because it lasts longer than traditional lights and saves more energy.
Companies should take into account the following requirements to make sure they have the right warehouse lighting:
- Soft lighting. The light must be projected in a diffused way so as not to dazzle the operators.
- Strobe effect. Produced by flashing lights, this should be avoided, as it makes it difficult for operators to work.
- Amount of light. The lighting should illuminate all necessary areas to ensure that operators can properly perform their tasks.
- Shadows. When installing the lights, you need to make sure that no shadows are produced because this could obstruct the operators’ vision.
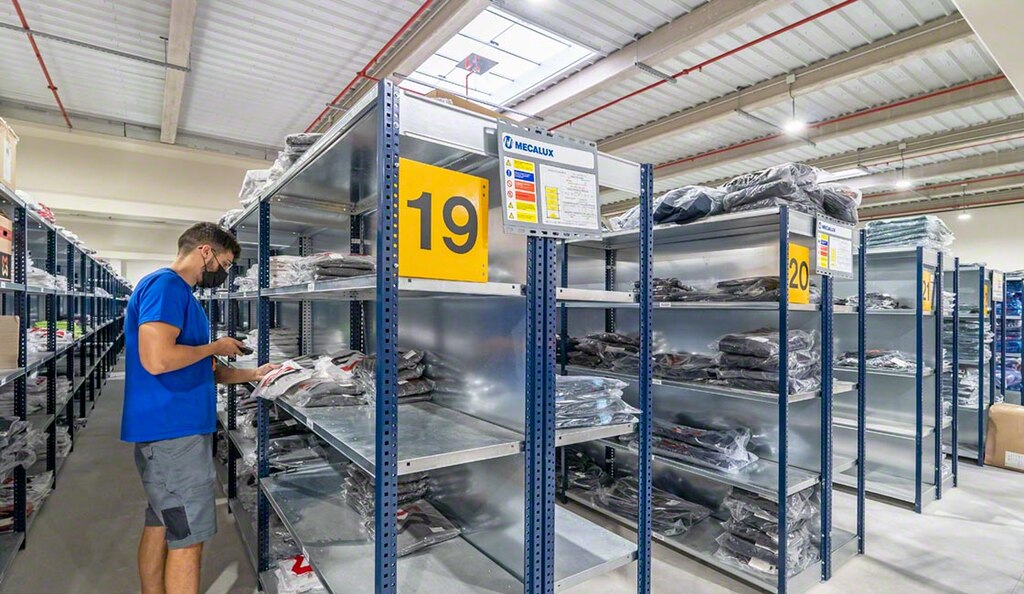
Lighting according to warehouse type
As a general rule, the main areas inside logistics facilities are outfitted with high bay luminaires and strip lights.
The warehouse docking areas must be especially well lit to prevent accidents stemming from the large number of movements made by the forklifts and products.
When it comes to order picking warehouses, good lighting in the storage aisles is vital in order for operators to find the locations in which they need to deposit the products and to identify the products to be removed from the shelves.
Another important point about warehouse lighting is that not all the lights should be on all the time. There are solutions that turn off the lights in certain areas automatically during times of inactivity. For example, Interlake Mecalux’s mobile racking systems for pallets include a lighting control system that turns on only the lights in the open working aisle. This saves energy and fosters green logistics.
Meanwhile, there are other types of warehouses in which lighting isn’t a key factor for performing operations optimally. Known as dark warehouses, these fully automated facilities require no light, since no human interaction takes place inside them.
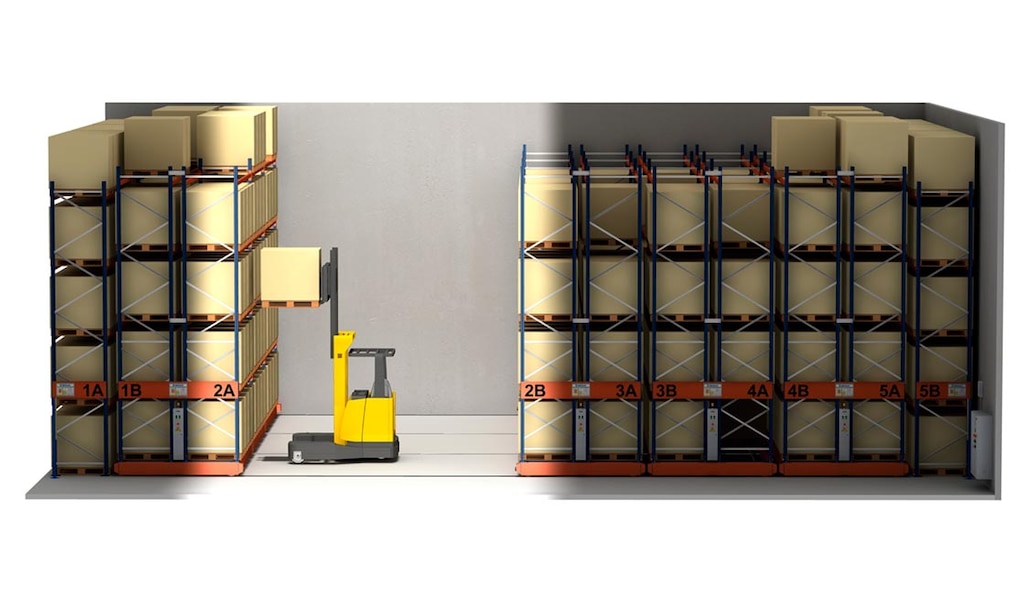
Warehouse lighting: safety and productivity
Logistics centers are spaces in which many movements and operations are executed. That’s why warehouse lighting is such a major issue: it ensures that processes will be carried out smoothly, with the utmost safety and productivity.
When choosing proper warehouse lighting, among other matters, you have to examine the design of the facility, optimizing space to achieve greater storage capacity and facilitate operator movements. At Interlake Mecalux, we have vast experience in improving warehouses of all kinds. Get in touch so we can advise you on choosing the best storage system for your business.